Introduction: 3D Printed Leather Hat Stamps Using Fusion 360
The problem with making a tooled leather hat is that the tooling takes a very large amount of time. This project allows you to 3d print large stamps that allow you to save dozens of hours by cutting out most of the tooling.
Supplies
- 3d printer with a print bed at least 280mm in either the X or Y axis
- Fusion 360
- Slicer of choice
- PLA+ Filament(PETG, ABS, or Nylon could potentially be used but have not been tested)
- Leather hat pieces ready for stamping
- Shop press or lots of clamps
- Plywood
- Suede or leather for backing/protecting
- Steel plate & Channel
Step 1: Structure, Design, & Files
Several things need to be considered when determining the structure of the stamp. Several iterations were done to improve stamp performance to get as many presses out of it as possible, but different leather, leather thickness, and pressing technique might require experimentation in order to get the best stamp.
Wall Width- The goal here was at least 3 layers thick. Using a .4mm nozzle this means 1.2mm or .048". Some places it gets thinner due to the line offsets being done in Adobe Illustrator.
Wall Height- Having tall walls meant they were prone to buckling to one side or the other due to uneven pressure or just an uneven surface. If the walls were too short then you don't get a deep impression and the leather hits the top of the stamp picking up unwanted impressions/texture.
Base Thickness- The thickness of the stamp base is also important, too thick and infilled it will buckle, too thick and 100% filled then it takes longer to print and you're wasting a lot of material. Too thin and you risk your presser material(wood, metal) imprinting into the leather.
Ultimately a thin base was used and medium height walls. The thin base allows the stamp to flex in when used with uneven pressure/surfaces. The walls are about 2-3x the thickness of the leather used, 2-3oz leather is 1-1.2mm thick and the walls are 3mm.
Design- The actual pattern for the print is based on Hector Escaton's hat in Westworld. It was designed in Adobe Illustrator, saved as an SVG file, and then inserted into Fusion 360. This is probably not the optimal way to do this, but it worked more or less. Fusion 360 does it's best with all the points but it does slow down when editing them. The better way would have been to cut it into smaller components and then combine them all at the end.
Step 2: Stamping Tips
First you're going to need a lot of pressure, hundreds of pounds. The best option is a multi-ton press, Harbor Freight has a 20 ton for ~$160 on sale. Don't want to buy a press or don't have the space? Clamps, lots of clamps! A vice can work with smaller stamps but with larger ones it becomes much harder to use without unwanted marks or uneven pressure.
Wet your leather- The more wet the leather the easier it will take a stamp. If you want to attempt to get the burnishing effect though you'll need to case your leather and use more pressure.
Backing Material- You want a backing material that has some give to it. This enables the stamp to push in and gives a much deeper impression. The softer it is the more detailed the stamp, but it stretches the leather. So you want something that has a little bit of give but not too much. Suede or leather is a great backing material, but rubber mats with no texture, closed cell foam, or even a soft wood can be used.
Spread out the pressure- Thick flat steel plates work the best, but wood can also work. You want as many layers of this as you can as every layer helps spread the pressure more and more. Channel steel can spread the force from one point to all along the edges, which helps when doing a long item. The stamps will take A LOT of pressure before breaking if printed correctly. In fact during this project the channel steel bent but the stamps were absolutely fine. This is partly because the pressure is spread out over a larger area of the stamp but also because the force is in one spot on the steel channel. Still very impressive how well the stamps hold up.
Protect your project- Since you'll be using metal or wood to press on the stamp you want to protect the project from touching that. A large piece of leather or even suede helps here. Be careful with consequent presses, the imprint from the previous stamp can actually imprint in the project if the leather gets moved around or a different stamp is used.
Keep the item pressed for at least 30 minutes- This helps insure you get a good impression. Think of it like when you lay your arm on something, a few seconds and you wont have any impression but lay on it for a half hour you do.
Don't be afraid to press again- If you're not happy with the impression you've got you can always stamp again. Matching up the stamp to the impression is very easy. So if you're afraid of applying too much pressure you can always start lower and work your way up.
Experiment first- While this guide serves as a starting point, experiment! Find out what works best for you! Things like filament type, leather thickness, leather type, and how pressure is applied can all impact the results.
The press setup used for this project from bottom layer to top was 3/4" plywood base, Suede backing layer, Leather to be stamped, stamp, leather to protect, 1/4" steel plate, Steel Channel, press.
Step 3: Results
These are the results. The stamped version doesn't have the detail, depth, and subtle-ness of the tooled version but it is more bold. A far more experienced 3d modeler can probably do much better at putting in details and texture, hopefully one day we will see!
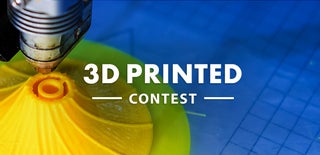
Participated in the
3D Printed Contest