Introduction: Tooled Leather Hat
Learn How to make an awesome leather hat with tooling on both sides of the brim!
What you'll need:
- Measuring Tape
- Paper or cardstock
- packing tape
- Wing Dividers
- 1/2 a side of 2-3oz Veg tan leather
- Exacto Knife or similar cutting implement
- Cutting Surface
- 4mm Diamond Chisels
- Nylon/wood mallet
- Plastic Cutting board or similar surface for punching holes
- Masking Tape
- Swivel Knife
- Beveler Leather Stamps
- Pear Shader Leather stamps
- Backgrounder Leather Stamps
- Other Leather stampes(Flower center, seeder, Veiner, mules foot, basketweave, etc)
- Leather Dye
- Neetsfoot Oil
- Contact Cement(Barge, Weldwood, Renia aquilis 315, etc)
- Saddlers Needles
- Ritza Tiger Thread .8mm or similar
- Snoseal or similar Beeswax based finishing coat
- regular Needle & Thread
- Old Tshirt rags
- Canvas or denim cloth
- Edge beveler
- Sand paper- 200, 400, 600 grit
- Optional- Granite slab
- Optional- Hair dryer or Heat Gun
- Optional- Sewing Machine
Step 1: Creating a Template
This is probably the hardest step in making the hat. The first thing we need to do is measure the head of the person we want the hat to fit. Use your sewing measuring tape to measure the circumference of the head as well as the width and length. Using the width and length we can use a Ellipse Circumference calculator to get the circumference, tweak the numbers as necessary to get the desired circumference. This one is 8.5" long by 7" wide giving us 24.4" around, keep in mind that leather stretches so a little under is better than over.
Once we have those measurements we can create the template, this can be done by hand but using a program like Adobe Illustrator or similar makes things much more precise and saves on paper! Keep in mind that you will want excess material on the outside of your stitch line, 1/4" at a minimum. You'll probably also need to tape several pieces of paper together since these will be large templates.
For the brim you take your center(head) Ellipse and add the desired brim length to each side and create a bigger ellipse. Easy! Try different lengths to achieve your desired look.
For the crown top you have a few options. What shape do you want oval or egg? How small do you want the top to be, smaller means the crown sides will slope in more. Generally you want it smaller than the center ellipse but prototype and decide what you like!
For the Crown side things get far more complicated! You'll need to decide how tall you want the crown to be, the one pictured is 5.5". Using two pieces of thread or string make them match the circumference of the center ellipse and crown top. Lay the two pieces of thread out on paper in a gentle curve using wing dividers set at 5.5" to keep them exactly that far apart. The tighter the curve the more sloped the crown sides will be. The straighter it is the less sloped it will be. If you cut this in half both sides should be the same. Getting this right is by far the most difficult part of the hat. There is a mathematical way to determine the exact curve needed but that's so complicated it needs it's own instructable!
Once you have the template drawn, use your diamond chisel and measure how many stitching holes go around your center ellipse and your crown top ellipse/egg and make sure that you have the same number of holes on the top and bottom of your crown side.
If you're using Adobe illustrator you can use the document info and turn on objects, this will give you the path length of the selected object. Make the crown top length and center ellipse length match. Then using stroke you can add the excess material to the outside of your stitch line.
Step 2: Cutting Out Your Templates
With templates in hand it's time to cut them out.
What you'll be cutting:
2x Brims
1x Crown Side
1x Crown top
1x Leather strip 1 3/8" wide and 1-2 inches longer than your center ellipse circumference.
Using Masking tape, tape them to the leather making sure you avoid any bad blemishes or grain issues in the leather. Once taped down, use your Xacto knife to cut around the templates, it's okay to take multiple passes on a cut as long as you've got the shape right. Do not cut out the center ellipse! It helps the leather keep it shape when tooling and will be cut out later. Since this brim will be double sided you will need 2 brims, BUT cut the second brim slightly bigger than needed! This way when they are glued together and stitched the 2nd brim will be trimmed down the perfect size. If you cut them the same size one might stretch or shrink when tooling and cause shape issues. Once they are cut out peel off the masking tape. The long strip will be used as your Sweat Band, the reason it's longer is in case it stretches or shrinks
Step 3: Tooling Design
This is where your artistic flair comes in handy! It's time to create a design for your hat. There are tons of references out there to give you ideas but ultimately it can be whatever you want. Floral design, basketweave, animals, whatever you desire! Use your templates to make more templates and draw on those. If you used cardstock, switch to normal paper here. Once you have your final design on a template use packing tape on the backside making sure there is no exposed paper as it's about to come in contact with wet leather and you don't want it soggy.
Step 4: Transfering Your Template and Cutting in the Design
First thing you want to do is put masking tape on the fuzzy backside(flesh side) of your leather. This helps prevent stretching when you're tooling. Once you're all taped up you'll need to dampen your leather, you can use a spritzer bottle, sponge, cloth whatever tickles your fancy! Once it's damp you tape your design template on. Then using a ballpoint pen or stylus you trace the outline of your design. You don't need to press super hard, you'll feel it leaving an indent in the leather. Peel back the template occasionally to make sure you didn't miss any lines.
Once you're finished take off the template and it's time to cut the design into the leather. This is done so that when a stamp is used it will only push one side of the leather down allowing for your design to pop out at you. You will want your leather "cased", which is a state of being dry on the surface but damp underneath. With thin leather though your window for properly cased isn't very long! So if it looks dry on the surface after taking off the template you will want to dampen the leather again. Once that's done it's time to put blade to leather, your swivel knife should feel like it's gliding through the leather, if it feels like it's dragging you might need to dampen the leather again. Also since this is thin leather you need to watch the depth of your cuts! It's probably worth it to practice on some scrap pieces just to make sure you know whats too deep and what's not.
Step 5: Tooling
Time to break out the stamps and granite slab if you have one!
Stamp texture is going to be purely based on personal preference so use what you think looks good!
Remember you don't have to always hold the stamp flat. You can angle it to achieve fading effects and to keep it from marking spots you don't want marked.
First off we case the leather agan! This is an important step when doing the tooling. Too wet and it will take stamps way too easy, not burnish and smush the leather. Burnishing is the key here since you want that extra color to add contrast and depth to your design. Too dry and it won't take stamps well at all. You will have to re-case your leather several times when working on it. If you're not dyeing a dark color you will want to make sure to case the entire piece each time to keep any watermarks even.
Beveling is usually done first. The beveler is what creates the effect of what's in front or behind of other things in the design as well as making it pop out from the rest of the leather. It's important to know what objects are in front or behind, but since you designed your pattern that should be easy to tell. Bevel all your lines!
Once your beveling is done we move on to pear shading! Pear shaders add that extra bit of depth in this design it's used for the divets in leaves, flowers, and vines.
Then it's Backgrounder time. Background is generally considered anything inside your design that would be behind it or black space. You can also use certain background tools around the outside of the design, but it should be used sparingly and quickly faded out.
Finally it's the accents! Veiners, camoflauge, and mule foot stamps are used to accent certain parts of the design. Veiner does leaf veins or curves on a vine among other things. Border stamps are used for borders. Decorative cuts are using your swivel knife to make accent cuts that just set the whole piece off. At this stage your design should be complete!
Wet the leather down and find a nice smooth flat surface. Find something smooth and flat to place on top of it, like a piece of board/plywood. This is so when the leather dries it will be flat, it's not fun trying to glue two brims together if they aren't flat!
Step 6: Conditioning, Dyeing, Buffing
When your leather finally dries it's time to condition it. You just pounded on it and soaked it in water, both things it doesn't like! Since we don't want cracking leather we need to add some oil back to the leather. If you're using water based dye or did not case/tool a piece you can skip this first oiling. Take a rag, paper towel, dauber, etc and soak it in neatsfoot oil and put a very light coat of oil on your leather pieces. As soon as your done wiping the oil on get another rag/towel and start wiping it off. It will absorb the oil it needs quickly and anything sitting on the surface is excess. Only do 1 very light coat, too much oil is bad and will result in your dye almost never drying as well as your leather being floppy. Let your oiled pieces sit overnight, they will go from splotchy brown to a nice uniform color as the oil spreads. This oil will darken the leather a little bit so keep that in mind when thinking of colors.
Now that we've conditioned the leather it's on to dye. The oil we just used will help the dye spread evenly throughout the piece. Using a dauber just dip into the dye and spread in a circular pattern until completely covered. Let dry for several hours and determine if you need a 2nd coat or not. If you do just repeat this process. Let it dry overnight to make sure the dye has set. If you're using Water based dye you may want to dampen the leather first to help it spread more evenly.
With the dye dry we repeat the oil process since the dye is harsh on the leather. Just a super quick and light coat of oil. Let it sit for another few hours if possible. Then it's time to bust out the buffing cloth(aka old tshirt!). Just buff the leather until it starts to have a nice smooth finish and light shine. This helps remove any excess dye and starts to add that nice finished look to the leather.
Step 7: Gluing and Trimming Your Brim
Two pieces become one!
This is a difficult step but relatively quick. First remove any masking tape that is still on the back of the brim and crown while you're at it. Using masking tape put markers on your brim so you know what's front, back, and sides making sure it matches with your other side. Since the bottom is slightly bigger put the top piece on and drawn around the outside, again marking front back and sides. If your designs on top and bottom are matching you should be able to feel them match up from the tooling bumps and ridges.
Now that you have them lined up they way you want them glued, apply contact cement to both sides watching the edges to make sure they are glued but don't have tons of excess to squeeze out and ooze everywhere! Wait the requisite amount of time for the cement to become tacky and then slowly put the pieces together making sure to match up the lines and front/back/side markers. Once together press firmly. Using your flat surfaces from earlier press the two pieces together to insure equal pressure. You can also use foam padding and weights to help put more pressure without ruining the tooling design. Leave this to dry for several hours to a day, any sooner and it might curl from the glues moisture.
Since the brims are now glue together you can trim the excess from the 2nd brim with an xacto knife. Just be careful not to trim into the 1st brim, a sharp knife and going slow helps this process.
Step 8: Wetmolding Your Sweat Band
Take your strip of leather and run it quickly under the sink with tepid water. Once it's wet you want to fold over one edge so you have 3/4" on one side. Once you have a decent fold go over it again put some real pressure on and get a good tight fold. Now take out your wing divider and set to ~1/4" and make the back side of the fold for a stitch line. Eventually your hat liner will be sewn into this fold
Step 9: Punching Sewing Holes & Stitching the Brim
It's arguable when the best time to punch the sewing holes is, but at
this point is a good one. The dye is done(mostly), the glue is done. Dye can distort leather with shrinking and buffing with oil can stretch, which can make your holes distort in length and not line up. Glue in your holes is just an awful experience and makes sewing that much harder. This lesson was learned the hard way, you can see the stitching holes pre-tooling in some pictures, it was not fun.
Using your template, tape it back on the leather and you can punch right through the template using your diamond chisels. It's as simple as that! Well there is one change, the crown top needs it's sewing holes punched from the backside, so when the crown side and top are sewn together the direction of the holes line up. Other than that double and triple check your stitch counts to make sure your brim center stitch count and base crown match as well as the top crown and crown top. Once you're 100% sure on the stitch count of the inside brim you can now punch that many stitches into the sweat band and trim. Make sure you're punching from the backside on the fold over! Again this makes sure the stitch holes all going in the same direction. if you're feeling fancy you can put some holes on each end of the sweat band above the fold and do a cross stitch to hold it together in a loop.
Of course there is one other stitch line that you wont have on your template and that is around the outside of the brim. Just get your handy wing dividers and set them to ~1/4" and mark a stitch line, then it's just hammering diamond chisels along the line and saddle stitching. Since the circumference around the brim is quite long it's advisable to break it into sections to keep thread length manageable. If you have a sewing machine that can handle leather, now is the perfect time to use it. You'll save yourself hours of stitching.
Step 10: Sewing Your Crown
Your crown will be sewn inside out since turned seams look nicer. First thing you want to do is trim your excess material down to about 1/4" from your stitching. This will help greatly in getting the leather to curve while your stitching. If you leave too much it will add extra pressure to the stitches, make it hard to find the right stitch holes, and potentially bust stitches.
Take your crown side and with the tooled side in bend together the ends. Match up the stitching holes and saddle stitch them together. Once that is done you do the same with the crown top, line up the back of the crown top with the seam of the side and start stitching. Do not pull super tight or you will bust stitches in the leather. Just take your time and make sure your not skipping any stitches. About half way you'll be praying you counted stitches right! If you did you'll have no problems! If you didn't you'll have to be creative in getting things line up again like double stitching through one hole and not another. If you need to trim any excess material on any of the seams now is the time.
If everything matched up, now you have an inside out crown! Run the crown under a sink with tepid water, gently turn the crown inside out. Then push the seams a bit from the inside to make sure they expand evenly. Do any final shaping and let dry overnight.
Step 11: Making a Hat Liner
Exactly like the leather crown! Take your templates you made for cutting out the leather crown and do the same with your fabric. Except! Leave an extra 2" of material on the long side(base) of the crown siding. This material is left so we can do a hem, sewing through 2 layers is much stronger than trying to sew right at the edge of fabric.You'll also want to add about a 1/2" to the ends of the crown side so you have room to make sure it fits the crown and it's not too short!
Once you have your pieces cut you have 3 ways of sewing them together. Sewing machine, hand sewing, or saddle stitching. Sewing machine is the fastest, but certain materials like satin can be extremely tricky due to bunching. Hand sewing is slow and your stitch might be uneven, the liner will have turned edges so it won't be very noticeable. Saddlestitching is super slow, but its even and the material will probably rip before the stitching comes undone! Just use your diamond chisels to mark the spacing and saddle stitch like normal.
First step here is to sew the crown side together. Wrap the fabric around the outside of the inside out leather crown, making sure the good(shiny) side is towards the crown. Mark where the ends meet and sew them together. Once you have the band you can sew the top on it, again shiny side inside, line up the back and front and start where the band's seam is. Don't pull super tight or it will bunch and be smaller than you need! Once you're finished sewing you can turn the hat liner inside out and inspect to make sure everything looks good. If everything checks out, turn it inside out again. Now you have a fancy hat liner!
Step 12: Glueing Your Hat Liner to Your Sweat Band
Hat liner meet sweat band! We have to keep the hat liner in the hat somehow but we also want to hide the edge of it. Since we have to sew the sweat band as well it makes for a good team. Put the hat liner over the completed crown with the good side in. This is where we take care of that excess material. Using the stitch line on the crown we can fold the excess material over to form a hem, just make sure the fold is slightly passed the stitch line. Now use clamps, paperclips, pins, or even a basting stitch to hold that hem in place.
On the sweat band put glue above the stitch line on the inside of the fold. While the glue is still wet put the hem inside the fold and apply lots of pressure to the fold. Use clamps to apply pressure until the glue is dried. The idea is to glue the hat liner to the sweat band but not fill the stitching holes with glue. The stitches will eventually hold the liner and the sweatband together, the glue just needs to hold long enough to get it stitched together.
Step 13: Cutting Out the Center and Wet Molding the Brim
Now it's time to cut out the center of the brim. You have 3 options to do this. First you can trust your template and cut out the center from that. If anything stretched or shrunk the template might not fit right and the center might be off. The next option is to use wing dividers and from the outside edge of the brim you mark ~1/4" pass the stitch line around where the hole will be. Again the outside of the brim might be less than perfectly round and that will create a less than round hole. The last option is to use your wing dividers and make ~1/4" from the stitch line. Any of these will work, what you pick will depend on how things fit or look. Then it's just cut and viola, hole in a brim.
Then we can wet mold the inside edge. Just run the inside stitch line of the brim under a sink with tepid water. Then gently mold the leather up. Once it's up you can then use a nice flat sided round object, like a roll of tape, to just help coax it up by just rolling it around the edge. Once done, leave to dry overnight.
Step 14: Finishing Your Edges!
Any edge that will be visible should be finished in some manner!
Edge beveling- If you have one now is the time to bevel those edges! These help round the edges, if you don't want round edges you don't need to bevel, but it does help with mushrooming.
We then need sand our edges. 200 grit sand paper makes sure edges are flush, 400 grit to further refine, and 600 grit to make sure they are smooth.
Dye touchups! since we are removing material we might expose some undyed leather. Use daubers and q tips to touch up the edges. Let dry for about 30 mins, depending on the dye, before continuing.
Finally, burnishing, some use gum trag or other products to burnish an edge. All you really need though is some water, a cloth(preferably canvas or denim), and time. Dampen the edge of the leather and rub with the canvas. Repeat this and eventually you'll have nice shiny burnished edges.
Step 15: Sewing It All Together
it's finally the crowning moment! Sewing everything together, yes everything! You'll be running a stitch through the brim, into the crown, and into the sweat band/hatliner. Its a big stitch so make sure you have plenty of thread. This is a difficult step since you need so many things to line up at once, but so worth it when its done. No real tricks here, make sure the front back and sides are lined up and start stitching from the back seam. Pay very very close attention to getting the right stitch holes. Again the stitches just need to be snug, you don't want to break any stitches here.
Now you officially have a hat! But we aren't done yet!
Step 16: Trimming the Crown
Now we take care of the excess material of the crown. Very carfully you trim it flush with the hat band with an xacto knife. Hold it so the base of the knife is on the brim and the point is toward the center of the hat. This way if you slip its not a knife point right into the brim.
Once trimming is done we do dye touchups again and burnish but without the sanding.
Only 2 more steps to go before we are finished!
Step 17: Wet Molding the Hat!
Want a certain brim curl? Hat a little to snug? Well now is the time to fix it! Run the whole hat under the sink in tepid water. Then you just carefully curl the brim to the desired shape and find a creative way to hold it while it dries. If it's too snug then you can also stretch it a little bit by pulling in opposite directions around the center hole. Don't pull too hard as wet leather is not the strongest. you can buy a hat stretcher as well that will help with this. This is also the time to shape the crown one last time so it has the shape that you want.
Let dry overnight
Step 18: Finishing
Time to apply that last little touch before it's ready for a night on the town. Depending on what you prefer you can use many different finishes. Some prefer Resolene, but that can be difficult to apply evenly and gets very shiny with multiple coats. This project uses Snoseal, which is a beeswax based product that helps waterproof the hat as well as conditions it. It also gives a nice natural shine.
Apply wax to a rag and rub onto the hat in a nice thin layer. If you have a hair dryer or heat gun, put them on the lowest setting, hold it well away from the hat and heat until you just see the wax start to melt. If you overheat and cook the leather it will crack and the hat will be ruined. Low and slow! Then get a new rag and buff buff buff. You can do a 2nd coat if desired. Just make sure you don't coat the sweat band...cause that would defeat it's purpose.
If you don't have a heat gun, hair dryer, or are just scared of overheating then you'll just multiple coats and a lot of buffing. Put a thin coat on with 1 rag and buff off with another. You want to create enough friction to melt that wax into the leather with just the buffing. Repeat until the surface feels waxy and has a nice shine. Swap out buffing rags if it gets too much wax in it.
Finally find a model that can sit still long enough for you to take pictures of your awesome hat.
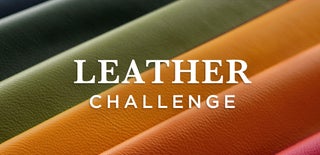
Runner Up in the
Leather Challenge