Introduction: 3D Printing Obsolete Vehicle Electrical Connectors
Every now and then I am called upon to conduct some automotive necromancy.
All too often, things are thrown away because of a small, but critical, part that has broken and cannot be replaced.
In many cases on old Volkswagens, replacement connectors just aren't available and so all sorts of bodges are made to work around it. But there's no reason these cannot be recreated with some careful measurements.
This Instructable is about exactly that sort of thing! Electrical connectors in vehicles!
Supplies
Some vernier calipers for measuring
A 3D printer
Some soft of software for drawing stuff to print
Step 1: Measure and Draw!
With simple verniers, you can get pretty accurate measurements and infer other unknown dimensions and radii from them.
In this case, you can see that the angles and curves don't seem to follow a regular shape. But, if you carefully measure and draw as you go, the object almost draws its self.
Start by selecting a "Datum" (this is a baseline to measure everything to). It doesn't matter which point you select, but it is sensible to select the longest flat edge.
Measure the maximum outer dimensions of the piece, and draw it as a cuboid. You are going to "sculpt" it as you go.
Measure the distance from the datum to each angle, like in picture 1. measure the length of all the flat edges too.
Mark this on your cuboid, picture 2.
Because of the way geometry works, the length of each flat side will only go in once place. Provided your overall dimensions are accurate, you don't have to worry about the angles, they sort themselves out!
Once you've marked and checked, you can remove the bits of the model you don't want.
After this, I drew the shapes of the connector holes in the face, carefully measuring where the extremities were relative to my datum and the opposite straight edge, and extruded these through the model.
You will need to add a little retainer block inside the extruded holes for the spade connector to clip into so they are retained. If you look at the spade connector, they will have a little tag that sticks up to latch into the connector, as in picture 3. If you are making a whole new termination and replacing the terminals, MAKE SURE YOU USE THIS TYPE!
The terminal you use must be able to pass through the back, but the hole at the face of the connector must be smaller than the terminal so that it doesn't drop out the front, and the block you put inside the hole to catch the little tag in the right place so it sits butted up against the end of the plug. It's harder to explain than show, but I hope you understand what I am on about? Anyway, this might be a bit of trial and error. On my first run, I had to replace the terminals when I fitted the plug as they were shot, and the replacements had the tag in a different place so a small adjustment was needed.
Also, for a bit of flare, I added my friend's company logo to the pieces so that once they are plugged in, you see it on the back.
Easy peasy! Just take your time, and measure lots of times before committing. The more measurements you take between known, correct points, the more accurate the pieces you add or take away will be.
Radii are a little trickier, but all I did was measure from a straight edge to the curve at several points, and made a "line of best fit" through the points.
Remember! The plugs can always be tweaked, sanded and adjusted post-print if needed! Also, a 3D printer is squirting molten plastic through a little hole and sticking all that together. It's accurate, for a given value of "Accuracy", so don't worry too much if you are a tenth of a mm out here and there, your printer probably can't even print to that degree of accuracy anyway.
Before you know it, you're done! Time to fire up the printer...
Step 2: Away She Goes Printing!
I printed off various plugs, in various materials, trying PETG, PLA and HIPS.
I did have some issues with wall thicknesses, but playing around with print settings eventually got a nice result that fitted well and accepted the connectors.
Step 3: Lots Is Possible!
I've made lots of different connectors now and brought lots of things back to life saving it from the scrapheap.
Alternator plugs, indicator stalk connectors, starter motor collector blocks... Often, it requires the replacement of the terminals inside the plug too, and quite often replacement of the whole cable, whatever the other end of the cable attaches to, and with alarming regularity half of the car to which it belongs (see my other Instructables and you will see what I mean, hahahaha!).
One major thing you have to consider is the current going through the connector, higher current means more heat and so you need a higher temperature filament. So far, PETG has worked well for me.
So, a 3D printer can be used to keep old things alive! This makes me happy...
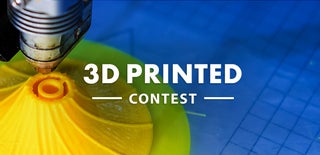
Participated in the
3D Printed Contest