Introduction: 3D Printer Enclosure From Old Network Server
One of my friends kept this steel network server box for me, as his workplace were throwing it out...I didn't know what I was going to use it for at the time, but it turned out my 3D printer fits perfectly inside, so reusing the server as an enclosure seems right.
Tools used:
Electric drill
8mm steel drill bit
Jigsaw – steel cutting blade
Allen keys
Screwdriver
Masking tape
Permanent marker
Cost of project:
Server box: Free
Spray paint: €15
5050 RGB LED’s: €17, https://www.amazon.co.uk/Waterproof-Colour-Changin...
LED Connector: €7 https://www.amazon.co.uk/gp/product/B01EJ32EXO/ref...
Plastic sheeting: €5 (left over from previous project)
MDF sheet: €5 (left over from previous project)
Total: €49
Step 1: Drill Holes and Prep.
I decided I wanted the LCD screen and functional buttons of the printer outside the enclosure, I used masking tape and a permanent marker to trace the location of the screen and the buttons. I placed the tape on the side of the server and used it as a template to drill and cut the holes.
Step 2: Painting
I removed the glass door and used masking tape and cardboard in places to prevent and spray paint getting into the inside of the box. I decided on black spray paint on the outside and wanted to keep the inside as it is.
Step 3: Install LED Lights
I quickly realized I could not bend the LED strip to create rows of the LED's without cutting the strip. I cut the LED strip into 16" length's. I decided to use these LED connector's I found on Amazon, way easier than soldering I thought. The connector's are flexible and once I hot glued the LED strips down, I made the connections using the strip's. As I way using the water resistant LED strips I had to peel off the end of the insulation. When I glued the strips down to the board, I turned each other strip upside down, to allow the for the connections to be inline.
Step 4: Final Assembly
I installed a section of clear plastic on the side wall and spray painted a square sheet of wood for a back panel. I cut out the LCD display section using a steel blade and a jigsaw.
Step 5: Complete Enclosure With Printer Installed
I installed the LCD display form the 3D printer in the slot I created in the side wall, I then installed the printer, which just fits...
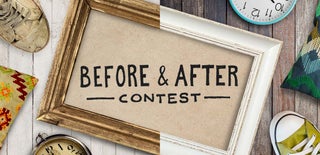
Participated in the
Before and After Contest 2017
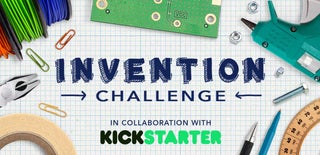
Participated in the
Invention Challenge 2017
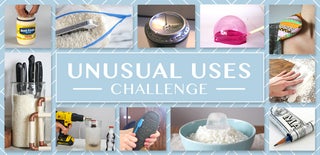
Participated in the
Unusual Uses Challenge 2017