Introduction: 3D Printing: Make Water Tight and Air Tight Containers
Air tight and water tight containers such as cups, canisters, or tanks can now be 3D printed using standard filament 3D printers. This makes it possible to make 3D prints that hold water or float. Air pressure tanks, boats, submersibles, pontoons, and food safe containers can be made. lab-ware such as tubing, pipettes, measuring spoons and cups and beakers and flasks can also be made.
Intro pic shows a 3D printed martini glass and beaker holding colored water.
Step 1: How It Works
After more than a year of experimenting with various slicer programs and slicer settings, a way was found to print objects with a standard filament printer that will hold water or air under pressure.
Normal slicer program settings will produce a clean fast print that is fairly porous. Microscopic gaps are formed between side by side layers and where the extruder reverses direction.
Pic 1 shows a typical print using normal settings and pic 2 shows a print with fused layers.
Minimum Wall Thickness
The minimum thickness that containers should be designed with is .068 inches. This will result in at least 3 extrusions side by side in a vertical wall. This gives a double seal.
Step 2: Tools and Materials
Access to a filament 3D printer.
PLA filament. Food safe filament is advised if used for food contact.
Mattercontrol slicer-FREE- can be downloaded here: https://www.matterhackers.com/store/l/mattercontro...
Glue stick- Good for prints having trouble sticking or for making it easy to release prints that are sticking too much. Yes, it works for both.
Step 3: Programming the Slicer
A slicer is the program that is used to tell a 3D printer how to print an STL file. I have had very good results using the free Mattercontrol slicer to slice prints for a Makerbot Replicator 2. You may have to make some adjustments of the settings for other 3D printers.
Other slicer programs can be used, but the settings will have to transferred over, which can be difficult as different programs use slightly different terminology for the settings.
In order to get prints that are waterproof and airtight, the slicer settings have to be adjusted to over-extrude the filament. Most extruders are designed to do a clean print as fast as possible. In order to over-extrude, the print speed has to be slowed down and the extrusion multiplier increased. This allows for the extrusion to be wider and overlap side by side layers. twice as fast extrusion speeds as detailed here can be used, and they will seal, but they tend to result in less smooth prints.
Here are the essential settings used, all other settings are left at default:
GENERAL
layers/surface
Layer height- .2mm
First layer height- .25mm
Perimeters- 2
Avoid crossing perimeters X
Eternal Perimeters first X
Start end overlap- 140%
Merge overlapping lines X
Expand thin walls X
Top solid layers- 9
Bottom solid layers- 9
Infill Fill density- 100%
Infill type- lines
starting angle- 0
Infill overlap- .9mm
Fill thin gaps X
Speed infill- 20mm/s
Top solid infill- 20mm/s
raft- 100%
inside perimeters- 20mm/s
outside perimeters- 20mm/s
support material- 20mm/s
bridges- 25mm/s
Travel- 130mm/s
First layer speed- 20mm/s
FILAMENT
Material Diameter- 1.75mm
Temperatures
Extruder temperature- 233 Deg C
Extruder wipe temp- 0 Deg C
Retraction
speed- 70mm/s
Extrusion
Extrusion multiplier- 1.5
First layer- 160%
Outside perimeters- 160%
PRINTER
Set for your particular printer
Step 4: Making Food Safe Containers
Bacteria
Normal 3D prints are fairly porous leaving lots of micro spaces for food and bacteria to accumulate. Printing as described here will result in solid prints which are easier to clean and less friendly to bacteria.
Food Safe Filaments
For storage or measurement of dry foods, most PLA printing filaments can probably be used without problems. For holding liquids, more should be done. Many filaments have proprietary chemical additives to make them more flexible or give better extrusion characteristics. They could be somewhat toxic. Some of the additives used to create colors can also be somewhat toxic. To be completely safe, filaments rated food safe should be used.
Clean Extruders
Most filaments leave residues in the extruder as can be seen in prints after changing to a different filament. Residues from previous filaments can end up being extruded even with fresh filaments. To be completely food safe, new extruders should probably be used that have only run food safe filaments.
The Best Nozzle
Many Brass nozzles are alloys that can include lead which could leach out and should be avoided when making objects that will be in contact with food--especially liquids. Instead, to be on the safe side, stainless steel or other lead free nozzles should be used.
Step 5: Other Possibilities
Pressure Tanks
Step 5 pic1 shows a small air pressure tank that was printed using the above settings and held air at 40 PSI.
Artificial Muscles
Pneumatic artificial muscles that hold 30 PSI air pressure can also be printed. The slicer settings are somewhat different. Pic 2 shows an experimental ant robot that uses ninja-flex filament. The legs have two muscles each and were printed in one piece with two control tubes..
This may be the subject of a future instructable.
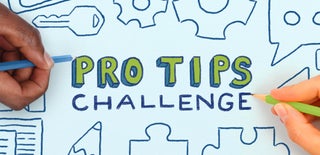
Participated in the
Pro Tips Challenge
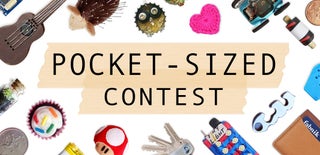
Participated in the
Pocket-Sized Contest