Introduction: 3d Printed Ultrasonic Record Cleaner Attachment
First, I just have to say "thanks" to Instructables for getting me to finish this project. I've had the ultrasonic cleaner for a year before actually starting the design, but with the 3d printing contest and "finally finished contest" that provided the extra shove I need to get off my butt and start doing some design in Fusion360 :)
Now, a bit of introduction...
“Cleanliness is next to Godliness,” goes the adage. Nowhere is that more true than in the wide world of vinyl playback. Vinyl, being a physical medium, can be exposed to all manner of dirt, debris, or gunk. This is unfortunate, as the playback of records is one of the great pleasures of music listening. The tools and techniques shown here are a method to get the most out of your vinyl playback without spending a mint.
Background Why is cleaning so important? Vinyl records make music by dragging a small diamond through a groove with an analog of the original soundwave produced by musicians etched into the groove. This vibrates the stylus, in turn the cantilever, and in turn, a magnet or coil of wire (or iron). This vibration induces a current in a coil of wire, creating an electrical signal analogous to the vibrations in the groove. Given the size of the groove, only about 40 micrometers across (see figure 1), it’s easy to see that any dirt will upset the smooth flow of the stylus riding the oscillations of the groove, thereby adding noise.
Figure 1: Electron Scanning Microscope photograph of vinyl record groove. Taken from http://www2.optics.rochester.edu/workgroups/cml/o... without any rights secured.
Vinyl records appeared around 1930, gaining in popularity after the introduction of the Long Playing (LP) record in 1948 by Columbia. In the intervening almost 100 years, there have been many methods introduced for cleaning and caring for vinyl records. One of the most interesting developments in LP cleaning has been the introduction of ultrasonic cleaners. Ultrasonic cleaning works by vibrating a bath of a solvent (usually distilled water) at ultrasonic frequencies to create small bubbles or cavitations. These bubbles collapse, with great force, loosening any dirt or debris on the surface of the object being cleaned. This method of cleaning has been used for years for jewelry and in laboratory settings. The breakthrough in ultrasonic record cleaning came with the introduction of the Audio Desk Systeme Premium Vinyl Cleaner in 2009. However, as with many innovations, there are DIY designs going back years prior. This design has more in common with those older DIY methods, bringing in the new(ish) technology of 3d printing to make some of the components more accessible and less expensive than many commercially available products.
My design has the ability to raise/lower records for conveniently adding/removing them from the bath and (if needed) drying. I originally designed the mechanism to raise and lower from the front of the machine, but that made it difficult to reach around back to add the records. Now I turn the machine sideways and I can easily raise/lower the mechanism and still access the ultrasonic control panel.
1.https://thevinylrevivers.com/a-brief-history-of-vi...
2.https://en.wikipedia.org/wiki/Phonograph_record
3.https://en.wikipedia.org/wiki/Ultrasonic_cleaning
4.https://thevinylpress.com/the-curious-case-of-reco...
Supplies
- 6L Ultrasonic Cleaner
- 3D Printer and PLA filament
- 3D Model https://www.thingiverse.com/thing:4386819
- 2x M2 bolts
- 2x M2 nuts
- 2x larger bolt, m5 or m6 works well, but 1/4" also works.
- 1x M5x45mm Carriage bolt (doesn’t have to be m5, just whatever will fit)
- 1x M5 wing nut (fits to carriage bolt above, so ensure you have the matching size, thread)
- 1x 3/16” threaded rod, 3-4” long
- 1x 3/16” nut
- Several random nuts to act as spacers. ½” works as they slide over the 3/16” rod without engaging the thread. You can also 3d print some from the thingiverse model
- 1x Motor Shaft coupler. Rigid is better, Motor coupling but flexible is all I had like this flexible shaft coupling
- 1x Small gear motor
- 1x Adjustable output voltage AC adapter
- 2 gallons distilled water
- A few drops of dish soap
Step 1: Acquire Materials
This system is built around a common 6 liter ultrasonic cleaner that is commonly available on sites like eBay or Amazon. These models typically cost around $120 US, though you may be able to find them cheaper. These models are 40khz models that may be inferior to 60khz models. I have no means of verifying those claims, and I’ve found 40khz cleaners to work well enough in my experience.
Once you have acquired an ultrasonic cleaner, you will also need access to a 3d printer. Mine is an Anet A8, which costs about $180 US (though they can be found cheaper). If you can afford it, go for a nicer model like a Creality Cr10 (~$500) or a Prusa i3 Mk3 ($750). However, if you are new to 3d printing and you don’t have a friend with a printer that you can get to make the parts, then the Anet A8 is a good place to start. Fair warning, 3d Printing, as a hobby is almost as time and money consuming as DIY audio!
Now that you’ve got your printer, you’ll need some material to print. The standard material is PLA (poly lactic acid) which is cheap, light, stiff, and widely available. A kilogram of PLA is usually $20-30 US.
Once you have your printer set up and your consumables ready to go, it’s time to print. The model and 3d print files for my cleaner are available on Thingiverse. Download the STL files and set up your printer to print them. After printing the files, we can now assemble the pieces.
Step 2: Print the Parts!
Take the models from Thingiverse and print them on your 3d Printer.
I printed mine with 0.8mm nozzle, .2mm layer heights and 50% infill. Use whatever works for you. If you print with supports, you may need to post-process a bit. I used some 150 grit sandpaper to smooth the 'tracks' for the motor carriage.
Step 3: Assemble the Motor Carriage
First, insert the carriage bolt through the top hole
Second, insert the motor so the back is facing you and the shaft goes through the carriage
Third, screw down the motor to the carriage with the m2 screws and nuts
Fourth, attach the shaft coupling to the motor shaft. Make sure one of the set screws hits the flat part of the motor shaft.
Fifth, insert the threaded rod or bolt into the coupling. I had to make do with a flexible coupling. Rigid would be better. A 7mm threaded rod would be ideal. I didn't have that, so I'm using a 3/16 or 1/4" bolt that I cut the head off. Whatever you've got should work, as long as it's small enough to go through the 0.286" + 0.001 - 0.002" hole in a record, but big enough to be held securely by the shaft coupler.
Step 4: Assemble the Main Bracket
Put a screw or two in one of the holes at the bottom of the bracket. I had this nice 5mm plastic covered one, it fits perfectly. Use what you have. A regular bolt will do just fine. There are a few holes at the bottom of the bracket for 3mm, 5mm, or 8mm screws. Just thread into the plastic for now, don't tighten it.
Now take the motor carriage and insert it at an angle so the carriage bolt goes through one slot and the motor carriage goes through the other. When looking at the main bracket, the carriage bolt goes to the right.
Next take the wingnut and washers and put them onto the carriage bolt, tighten them down to hold the carriage in place. I used two washers and a lock washer to give some spacing. Tighten down the wingnut.
Now place the main bracket/motor carriage assembly onto the side of the cleaner. You might have to lever it on.
Finally, finger tighten the screw(s) on the bottom of the main bracket to hold it in place. Don't torque them down yet!
Step 5: Wiring the Motor
This may be a little idiosyncratic to the hardware you have on hand.
I took the ends off of my AC/DC wall wart's leads. This may be dangerous. Don't do it if you don't know what you are doing! The AC/DC adapter I linked from Amazon has a terminal block output, so you can cut the leads off of the motor and screw the bare wires into that terminal block. Use your best judgement.
One thing you will want to do is make sure the motor turns counter-clockwise. You want the nut securing your records to be screwing ON, not OFF. Ask me how I know
With everything wired up, you should be able to control the speed of the motor with the voltage control on the ac adapter.
Step 6: Cleaning a Record
Now comes the fun bit!
Raise the motor all the way up. Put a spacer onto the shaft, put on a record, another spacer, and finally a nut to hold it all in place.
Lower the motor carriage.
Center the main bracket by loosening the screws at the bottom, then slide it back and forth to get the record centered in the bath. Now tighten the screw down. Just get it snug. Don't go hulk on it, or you'll strip the plastic out and have to get another larger screw.
Now you can add some cleaning fluid. You'll need 6 or so liters of DISTILLED water. Add a couple drops of Tergicleen or (if you're cheap) Dawn dish soap.
The level of your water should be up to the level of the runout groove on your record. Don't submerge the label! The spacers don't keep water off the label!!
Turn on the motor and set the voltage so you get about 1-2 RPM.
Now it's time to turn on the ultrasonic cleaner. Flip it on, and set the timer to 5-15 minutes. Dirtier records get longer. I wouldn't go over 15 minutes, personally.
Once the cleaning cycle is done, you can raise the motor carriage, speed up the motor by increasing voltage, this will help the record air dry.
Of course, air drying is less that ideal (lots of dust in air), so if you can, vacuum the record dry with a record vac.
Once the record is dry, turn off the motor, the cleaner, remove the record, and go listen. See if you haven't removed a lot of those nasty clicks and pops!
Step 7: Conclusion
So, how does my homebrew record cleaner stack up to more expensive hi-fi models? I have no idea. If someone wants to send me one, I’ll be glad to A/B them :)
However, I can compare this to my beloved old Nitty Gritty vac. The Nitty Gritty is more convenient, providing a record cleaning and drying station all in one. It’s also quiet enough and fast enough to keep in my listening room. The ultrasonic cleaner is much louder for much longer (typically 10-15 minutes to clean a record). Where the ultrasonic shines is getting a lot of fine dirt and gunk out of the grooves of a record. It takes longer, but for occasionally cleaning a small batch of records (3-4 at a time) it works very well.
I think the ultrasonic cleaner is much better than hand washing methods, though again, it’s not so fast or convenient.
The best method might be some combination of the 3: hand cleaning to get the big gunk loose, ultrasonic for getting out the fine particles, and vacuuming the record dry to remove any cleaning residue. Experiments continue!
Keep your eyes on my thingiverse page, as I’ll probably be making updates to the design for things like improved ease-of-use and better drying.
:)
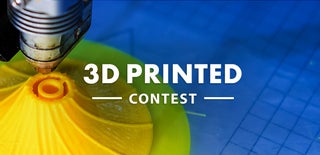
Participated in the
3D Printed Contest