Introduction: '3rd Hand' Leather Stitching Clamp
When I teach leathercraft, I tend to focus heavily on stitching. You can have the most perfectly formed and cut piece, with amazing tooling, but if your stitches are crooked or uneven, you simply aren't doing justice to your own work. When you're freehand stitching a project, it can be a bit unwieldy to hold your pieces together, as you work with your awl, especially if you're like me and don't like to use glue. The '3rd hand' is a great addition to any leathercrafter's toolbox as it frees up your hands so that you can concentrate on making your stitches as perfect as possible. Best of all, I've designed it to be easily dismantled so that it'll fit in your leather working case, or be stored in a drawer for later use.
This is an old, traditional design that's been around since leathercraft first became leathercraft, so I didn't create it. This is simply my own design, based on my dissatisfaction with store bought versions, (which can be very expensive as well), and the design changes I wanted to see in them.
Step 1: Tools and Supplies
Tools;
- Saw - circular, hand, table
- Drill with bits
- belt sander - though much of the belt sanding can be done by hand if you don't own one. It just takes a bit longer
- combination square
Supplies;
- 1"x3"x40" wooden board - pine, cedar, oak all work
- 2"x3"x2" block of wood - or you can cut two 2" pieces of the 1"x3" and glue them together
- sandpaper- 100, 150 grit
- wood glue
- 4" 1/4" carriage bolt with wing nut and washer
- 5" 1/4" carriage bolt with wing nut and washer
- piano hinge - I choose piano hinge because of it's thin profile, but if you want to use a regular hinge that would work fine. You will only need 3" worth.
- 1/4" tapered hinge screws
- 1" tapered hinge screws
Step 2: Cutting and Sanding
First you need to cut two 2" pieces off of the 1"x3" board. These will go at the clamping end of the third hand. Next cut a 16" piece, from the same board for the base. The 2"x3"x2" block is for the hinge end of the 3rd hand. If you don't have a suitable piece, you can simply cut two more 2" pieces from the 1"x3" board and glue them together.
Finally, saw your 1"x3" vertically to get two .5"x3" boards. Because of the thickness of your saw, they won't be exactly .5", but that's not important for our needs. Cut one of the boards to 16". This is the static arm of the clamp. Cut the other, just shorter, to 15.75" for the hinged, adjustable arm.
Step 3: Sanding, and Creating the Bevel Edge of the Clamp
For the bevel edge of the clamping end, of the '3rd hand', I performed most of the work on my bench sander, however you can do this by hand. Reduce one edge of your 2"x3"x2" pieces till you end up with a 20 degree bevel and make sure you round the corners. Leave the back side square for attaching to the clamp arm, but sand down all other square edges around the bevel so that they're nice and rounded.
Sand all of your pieces with 100 grit sandpaper. You don't have to be perfect as we'll sand again later. Just smooth out any rough spots.
Step 4: Drilling
Take the 1"x3"x16" piece you created for your base and mark the exact center of the board using your combination square. Drill a hole just large enough for your carriage bolt to pass through, taking care not to fray the wood. A great way of stopping this is to put a piece of tape over where you intend on drilling, and a scrap piece of wood under to drill into. That should leave you with nice clean holes. You're going to need to drill a hole through your 2"x3"x2" block so that it can be attached to the base.
Next, drill two more holes in your clamp arms in the center of the board, roughly 6" from the base. Make the hole on the static arm just large enough for the carriage bolt to pass through, and the one on the hinged arm slightly larger. This board will need to be able to move, so we want to ensure the bolt will slide through it easily.
Finally drill two small holes on your hinged arm for the hinge itself, and two in the lower edge of the 2"x3"x2" block. The hinge will be sandwiched between the block and the arm to allow it to actuate smoothly.
Step 5: Gluing and Screwing
Now you need to start gluing. Attach the block and one of the beveled pieces to the static arm as you see in the first pic, and attach the other beveled piece to the top of the hinged arm. Again, if you used two pieces to make up the block, it should be fine. Just make sure you let the glue set well before moving on.
When the glue has dried, assemble the hinge on your clamp, just as you see, in the third pic. Leave your screws loose, and align you clamp before tightening them down permanently.
*note*, when attaching the block to the static arm, you don't need any metal fasteners as the force exerted on it pulls it together rather than apart, so there's no need for screws or nails. The glue will hold just fine.
Step 6: Final Assembly and Sanding
Once your glue has dried, and your clamp is assembled, you can install your carriage bolts. Tap the 4" bolt up through the base and 'set' it into place. Next tap the 5" bolt through the static arm, of the clamp and 'set' it into place as well, making sure it passes smoothly through the clamp arm. Put a washer over the bolt and then a wing nut. Mount the clamp onto the base by passing the 4" bolt through the block, then put a washer with the wing nut on top and tighten it down.
Now sand everything down with 150 grit sandpaper to remove any burrs that may have been left behind from construction.
*note* I've seen clamps with leather patches covering the clamping blocks, but, in this design they are completely unnecessary. We've sanded and rounded all the edges so there's no risk of it denting your tooling leather, and the raw wood provides enough friction so that your piece won't shift when clamped.
Step 7: Finished
You're done and your '3rd hand' leathercraft clamp is complete and ready for use. I wouldn't recommend putting any oils or finishes on the wood as this can transfer to your leather, so just keep it raw and simple. Now have fun sewing those projects up knowing you have better control over your stitches.
I hope you enjoyed the instructable and thanks for following.
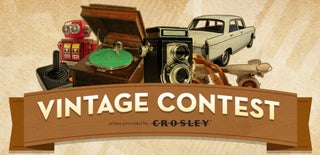
Participated in the
Vintage Contest
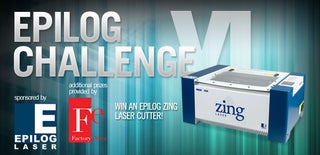
Participated in the
Epilog Challenge VI