Introduction: 5-Axis CNC Milled Knob Using Fusion 360 Manufacturing
I'm a 3rd year university student studying Design Engineering at Imperial College London. The first thing about me, I love spending time in the workshop. I am very fortunate in my universities expansive tool and machinery availability and I try to make use of that as much as possible.
One of those tool that I've come to love, and spent a lot of time in the past year learning, is a 5-axis CNC milling machine called the Pocket NC V2-10. This is a really small enclosed CNC mill that has a lot of possibilities but is quite limited in the workpiece size.
The background of this project is that I wanted to build a wooden dice roller, like the one seen here, with a dowel running down the center, that you could rotate so that you can select which side the dice comes out. I created and fabricated that entire design, but once it was finished, it was an elegant wooden project, with a bare dowel sticking out of it. I thought it needed a knob.
Obviously very few people will need a knob for the exact purpose I need it for, but there are lots of different projects, where a nice aluminum knob would be elegant and function well. You can customize the CAD and therefore machine it to your specifications.
The purpose of this Instructable is to help with the design, prototyping, and fabrication of the a knob using Fusion 360 design workspace and manufacturing workspace. When I went out looking for resources on how I could start CNC milling components there was no easy to understand guide that I felt truly helped me. I made a previous guide, for a dial component, but I've learned a lot since then, and every single project comes with new challenges.
PLEASE DON'T BE DISSUADED BECAUSE IT LOOKS COMPLEX!! I know this from personal experience. CNC machining is so fun once you get into it, and the learning curve can be steep, but there are so many resources out there. For me, this one here was helpful because it was specifically in terms of the machine I was working with. I jumped into the deep end by starting with 5 axis milling, but if you wan't to get into it, it would be easier to start with 3-axis.
Supplies
Reusable Supplies:
- 5-axis CNC mill
- I am using a Pocket NC V2-10 which is a very small 5-axis CNC mill which I am fortunate to have access to through my university. I will go through this guide with context to this machine, however most of it should work with other CNC milling machines. Other machines will have different settings, so please consult with each machine.
- 6mm, 3mm, & 1mm Milling Bits for Aluminum
- Depending on the size and design of your stock, other size bits may work, however for the size of my dial, these are the 2 bits that are best sized, You want a bit as big as possible that will fit for your component as it means it can take away material much faster.
- 6mm flat end mill bit
- 3mm flat end mill bit
- 1mm round end mill bit
- Hacksaw
- The machined component is still attached to the stock once complete, so to separate them, a hacksaw is the easiest way
- Ruler/Measuring Tape/Calipers
- Needed for measuring out stock and placement on the vice. Having a pair of digital calipers is an incredibly useful tool
- File
- After using the saw to cut the piece off of the remaining stock, there will be sharp edges which is good to remove.
- Drill Press/Drill
- Used to create the hole in the bottom of the knob so that it can actually be attached to things. A drill press is much easier as it ensure everything is perpendicular and aligned and easier to get the correct depth than a hand held drill.
- 3D Printer (Optional)
- A very useful tool for prototyping design before final fabrication process just to ensure you like the final size and form before spending hours of your time with the CNC. I didn't do that for this project but I would recommend in general.
Consumible Supplies:
- Aluminum Stock Material
- I used aluminum 6061 which is the most common alloy to use in machining and is what was available for me.
- The size of the stock material will depend on how big of a dial you want to design, and also critically, how big of stock material can the milling vice handle. The Pocket NC V2-10 can only hold very small work pieces so it is very size limiting. For this project I used round bar aluminum stock material with a 25mm diameter, and a length of 100mm. A few important things to not about size
- 1. I got the wrong diameter at first lol. Don't be me. the Pocket NC V2-10 has a vice for round material which has a 24-25mm collet, but I bought 25.4mm (1") material so it didn't fit inside the collet. To fix this,I just threw it on the lathe to turned it down a bit.
- 2. if your vice can handle it, it's always better to get a larger stock material and remove material, because you can't add back material to the stock. Also important because the machined finish of the aluminum is much nicer than the factor finish, so it is best to remove material from all the surfaces
- 3. The factory cuts for the material can be quite off so don't expect it to be exact.
- 4. Having additional size is also important because you need stock material to be able to hold the workpiece in place
Step 1: Basics of 5-axis CNC Milling
CNC just stands for computer numerical control and is "the computerized manufacturing process in which pre-programmed software and code controls the movement of production equipment" [1]. CNC is a process for many different manufacturing process from water jet cutting, to lathes, to milling machines, to routers, to plasma cutters, etc. The process I'm talking about is milling which is a subtractive process of using a rotating tool-bit to remove material.
5-axis refers to how many degrees of movement the machine can move in. Most typical machines are 3 axis which means it has a x, y, & z movement and therefore can't do any sort of overhand. A 5 axis machine has a x,y,z,a, &b axis where the a & b axis are rotational axis. An example of these axis can be seen in the photo above which is a photo of the Pocket NC V2-10 machine. I made some stickers using a CNC vinyl cutter (an amazing tool btw) to cut out some axis labels so that you can identify their movement direction.
Step 2: Designing the Knob in CAD
The first step is to design the knob in Fusion 360. Because I know that my stock is 25mm, I need to make sure that my octagon fits within a 25mm circle.
It is important to think about when creating the design where a 3 or 5 axis milling machine would be able to create that. That means not having any impossible overhangs or places to reach. One method in addition to carefully thinking about the design is to use one of Fusion 360s many integrated features known as Accessibility Analysis. This tool in Fusion 360, will show you whether part of your design is accessible from a certain direction by indicating accessible in green and inaccessible in red. This functionality is especially useful for 3-axis CNC machines.
A rough guide for the process of designing the Knob can be seen in the screenshots above which are in chronological order!
Design Stages:
- Sketch 1: Creating an octagon using the polygon tool in a sketch window.
- Extrude 1: Extruding the octagon to the correct thickness.
- Geometric Pattern 1: This tool is part of an extension, but education users can get free access to all of the extensions. This could have been done more simply by making a rectangular pattern of spheres, but i wanted to test using the geometric pattern. This is then copied onto every single face of the octagon.
- Sphere 1: Making a large sphere which we will use to get rid of material at the top of the knob
- Combine 1: Combine the octagon knob and the phere, with the sphere as the tool body, and the knob as the target body.
- Chamfer 1: Chamfer all the top and bottom edges so that the final knob won't be as sharp
- Chamfer 2: Chamfer all the side edges, so that the whole knob is slightly more rounded, and less sharp edges.
- Sketch 2: Create a sketch to create the connection point between the final product, and the stock material, which is where we will cut once it's finished in the CNC.
- Extrude 2: Extruding the large cylinder, which will help reduce the friction for the knob when it turns as it means less surface area
- Extrude 3: Extruding the final connection point between the body and the stock material.
You will also need to create a CAD model for the stock material you have purchased. This is important because it lets the software know what the model you want to cut is, and what the original size of the material is so it know where and how much to cut.
OctogoonTOp
Step 3: Machining Setup
The next step after creating the design is to set it up for machining. For the Pocket NC V2-10 they provide the vice system as a CAD model so that you position your model correctly within the vice. For this design, since we are using round stock, and the vide for the round stock is different, we will delete the vice from the CAD file, and just leave the center ring which we will use a location reference. Most larger and higher end CNC milling machines wont have you do this as this step is not necessary for machines that have probing functions. That means that the machine can figure out exactly where the stock material is within the machine, however with the Pocket NC, you have to position your stock inside the machine relative to where you position it in the CAD inside the vice.
Once you have positioned the knob within the vice (step not needed if your CNC machine has a probing feature) you can finally go to the Fusion 360 manufacturing workspace! If you click on the design in the top left, the click on manufacture you get the the new workspace. By default it should being you into the milling section, however at the very top bar you can see theres also a turning, additive, inspection, fabrication, and utilities section.
The next thing to do is in the browser tree on the left side, right click Setups and click New Setup. This will begin the process for the machining setup. This is a very important stage which will differ between different CNC mills and so I will discuss for the Pocket NC mill and try to talk about general info. In the setup menu there are 3 tabs, Setup, Stock, and Post Process. The first thing is to go to the setup tab and make sure the operation is milling.
The Work Coordinate System sounds confusing but is just the framework that defines the location of the tool and the workpiece. The orientation defines what orientation it is going to be in when in the milling machine. For most milling machines X and Y are the horizontal plane movements side to side, and the Z axis is the up and down. It's important to set these based on what orientation the stock will be in the machine. The origin is where you set the zero point as. On the pocket NC the origin is a specific location defined in the vice CAD, but for machines with probing the origin is often someplace you set it on the stock material. That can mean when you probe the stock material for its location, you can set a corner as the origin, and then in the setup, you select that same corner as the origin. Then you select your model which is the CAD of the knob you just designed, and then optionally you can select a fixture. You only need to check the fixture if you have the vice of the machine in your CAD. When you select the fixture bodies, that is a sign to tell Fusion 360, that you don't want to machine these so it helps with the collision avoidance.
The next tab is the stock tab where you define the size and placement of your stock material. Since we made a body that is now most likely hidden to define the stock, we can change the mode from Relative, to From Solid and then select the solid that we created to represent our stock under models in the model tree.
The final tab is the post process tab which affects the G code fusion 360 generates. For the pocket NC machine, this can be left without making any changes however some machines might require changes so it is important to look at your machine guide.
Step 4: Understanding the Machining Toolpaths - Tool Tab
At the top of the machining workspace you can see the 2D and the 3D toolpaths. If you click on one, it will open up a menu and there will be 5 different tab and I will go through briefly the importance of each one.
This first tab is the tool tab. This is where you will select the tool bit that you are using. You can add tool bits into fusion 360 by going to the Tool library which is a button on the top under the manage section, where you can right click under local and create a new tool library (if your CNC is run by someone, they might already have a tool library they can share) and then at the top of the tool library there is a plus symbol where you can add new tools.
Once you have the tools you can head back to the toolpath you wanted and select the bit you just created for the specific toolpath. Then you select whether theres coolant or not, the Pocket NC has no coolant so you can disable it but many machines do have coolant. Then you define the spindle speed and speed of your machine and tool bit. I can't recommend any settings because each bit, material, and machine will be different so it's good to check any guides that comes with your machine and tool bits.
Step 5: Understanding the Machining Toolpaths - Geometry Tab
The geometry tab is where you will actually define what part of your workpiece you want to machine. This will often selecting machining boundaries defined by sketches or edges. The tool will then be either contained within that boundary, or be keep outside that boundary. There are other options in this tab which can be important and you can learn more about them by hovering your mouse over them and waiting for a few seconds for an info tab to pop up
Step 6: Understanding the Machining Toolpaths - Heights Tab
The heights tab is where you will define the maximum depth you want your cut to go. That is known as the bottom height and you can change it based on how deep you want. You can also change the top height which is the height where the tool will start machining.
It is generally good practice to offset the top height a little bit above where you think it will actually need to start just in case the stock is not exactly flat, or not positioned exactly where it thinks it is, then the tool bit won't go ramming into the stock. The clearance and retract height define how far the tool comes up to then go to its next pass or toolpath. These can be important to make sure your tool doesn't collide with the piece.
Step 7: Understanding the Machining Toolpaths - Passes Tab
The passes tab is where you will define how deep of cuts do you want your bit to make, and how much it should cut on the side as well. This tab can be quite confusing as there is a lot of options but the important ones to look at are the Optimal Loads, the Maximum roughing stepdown, and the fine stepdown. The optimal load is how much the bit will move the side when doing passes.
For example if you have a 6mm bit and you set the optimal load as 6mm then then entire cross section of the bit will be cutting. If the optimal load is 1mm, the the bit will only use 1mm from the edge of the bit in each cutting pass. A lower load means the bit will experience less stress but also cut more slowly. The max roughing step down tells the software how deep do you want to go in each pass.
If you have a cut where you need to go down 10 mm then most likely yo wont be able to cut the 10mm depth right away, so instead the max roughing stepdown tells the software how deep the bit should go. If you set it as 2mm, then it will cut away 2mm at a time and instead of cutting the 10mm in 1 pass it will cut it in 5 or 6 depth passes. These setting are very important so that you don't break the bit. One a curved surface, the roughing stepdown will cut away the material quickly, but it will leave it looking like a stair case. But if you use really small roughing stepdown to have a smaller stair case effect and smooth surface, then the machining will take too long, That is what the fine stepdown is for. It will make a lot of the rough larger distance stepdowns and then come back again and between each large stepdown, it will make a lot of smaller passes. You can define this distance as smaller to have a nicer finish.
Step 8: Understanding the Machining Toolpaths - Linking Tab
The linking tab is also slightly confusing as there is so many different options. Most of the options you can probably leave as defaults but one of the most important ones that you might want to changes is under Ramp, and change the Ramping angle and helical ramp diameter, For softer materials you can have a larger ram angle but for harder materials like aluminum you want a shallower ramp angle. A ramp is a helix that the machine does to get deeper into the material instead of going straight down. A smaller ramping angle will cause less stress on the bit.
That's all for the tabs under the toolpathing so you should have a general idea what to do! From my experience it can take many hours of trial and error to get things to work but there's some huge enjoyment when you finally get the toolpaths to look good. Some of the toolpathing will have 1 additional tab which is called Multi-Axis which can be useful if you have a 5 axis CNC but for this project it is not necessary as it also requires the machining extension.
Step 9: Creating the Toolpaths
The steps below outline how to using the integrated toolpaths inside of Fusion 360 manufacturing to machine out the part we want. It is important to realize that there are a lot of different settings, and it can take quite a bit of time adjusting the settings for each path, part, and machine.
I've included time-lapses of the actual machining process to compare it to the simulations and to show the end product after each step, but it's very important to realize that all the machining has been done after the toolpaths were created, and not step by step. This is important because the order of the toolpaths might change, or you might want to change the position of the part, or even the design of the part.
Step 10: Creating the Machining Toolpaths - Path 1 - Facing
The first toolpath is the facing tool. The facing tools is used to get rid of large amounts of material, and is typically not a finishing pass. It just moves the tool. back and forth to get rid of material. Here we are just getting rid of the top part of the stock material which doesn't have a good finish.
One really important feature to use in the Fusion 360 manufacturing is that once you've created the toolpath, right click on it in the tree on the left, and click simulate. This will simulate the tool path and you can speed it up and slow it down and see how it moves. This is also useful because at the bottom green bar, if there's any collision within the toolpath, they will show up as little red bars on the timeline and you can hover over it to see the problem and click on it to go to that moment in the simulation.
Step 11: Creating the Machining Toolpaths - Path 2 - Creating the Octagon
The second tool path, is to use the same facing tool, but to face each of the 8 octagon sides. This process is a little manual as you have to copy and paste the same tool path 8 times, and change the x-y orientation of the tool so that the machine is oriented correctly.
Step 12: Creating the Machining Toolpaths - Path 3 - Swarfing the Chamfer
The 3rd path is to using the swarfing toolpath. This is the first true 5-axis move, as the previous toolpaths have been 3+2 axis machining. To use this toolpath, you will need the Fusion 360 machining extensions, which is free to access for students, and even though it says a 30 day trial, students can keep renewing the license over and over. This toolpath is super quick, especially because I made the chamfer very small.
Step 13: Creating the Machining Toolpaths - Path 4 - Rough Top Divet
The 4th toolpath is a roughing path to create the divot in the top of the knob. In the CAD the divet is a perfectly smooth curve, and we need a smaller toolbit to create that curve, but it would take a long time for a smaller too to get rid of all that material. What we can do, is use a larger tool for a roughing pass, where we take away a lot of the material, and then use the smaller tool bit, to create the final shape and surface finish while not needing to take away much material. This makes the whole process much faster.
This path uses 3D adaptive clear. This is most likely to be the most common toolpath you use for most machined parts. It will automatically recognize your pieces and avoid it in 3 dimensions. This is also known as a roughing pass so typically you do another pass after this to increase the finish but for my application, most paths will be ok as the adaptive clear.
Step 14: Creating the Machining Toolpaths - Path 5 - Final Top Divet Swirl
This is the 5th toolpath, and the tool for this one has changed from a 6mm flat end mill, to a 1mm ball end mill.
This is the finishing pass for the previous path, and leaves a really nice finish.
Step 15: Creating the Machining Toolpaths - Path 6 - Dimples
This path is actually 8 separate paths copy and pasted which the orientation changed each time to create the dimples. This was the part of the machining process that took the most time, as each side of the octagon took ~10 min.
As you can see in the simulation, it is also very computationally expensive to create and simulate these toolpaths. I have a old computer, so it took a long time to generate all of these paths.
Step 16: Creating the Machining Toolpaths - Path 7 - Roughing the Base
This 7th passes uses a rotary contour pass. Unlike the previous paths which are all milling functions, the rotary contour works much more like a lathe. This path is getting rid of the material below the knob helping to form the final shape.
Step 17: Creating the Machining Toolpaths - Path 8 - Chamfer Base
This is the second swarfing toolpath which is being used to create the second chamfer on the bottom of the knob. This is the second full 5-axis toolpath move.
Step 18: Creating the Machining Toolpaths - Path 9 - Final Base Cut
The final toolpath for this project is another rotary contour pass. The purpose of this pass is to create a very thin stub that connects the knob to the stock material. This little conntion point made it super easy to grab a saw and then saw it off the stock material
Step 19:
The post processing is an import part you actually export the toolpaths you have create as g code files so that the CNC machine can read and understand what you are trying to do. For the first machined piece of any part, I highly recommend exporting each toolpath individually as individual g codes, rather than the entire setup. If you export the entire setup as one g code, then the CNC machine will machine all of them, however if there are issues with the paths you have created it won't stop unless you force it to stop. If you export each toolpath individually you can upload to your CNC one by one to make sure each step works.
To actually post process you can right click on the toolpath and click Post Process. The post process setting will vary widely based on the machine you have but I have shown a screenshot of the settings I use for the Pocket NC V2-10 machine.
Step 20: Vicing & Fixtures
In the first photo, you can see what the typical fixture system for the pocket NC V2-10 looks like, which is a simple vice with little grub screws to hold the workpiece in place. you can move the grub screws back for larger pieces, but overall it is a really limited fixture system.
In the second photo you can see the fixture has been replaced with a cylindrical fixture. This fixture is designed for cylinders and has a 24-25mm collet. You can see in the next few photos the process of installing the round fixture systems and how the aluminum stock material slides into the work piece.
Again one of the biggest problems with this CNC machine is the lack of probing. The machine doesn't know how tall the stock material is so I have to take a pair of calipers to measure how tall the stock is sticking out from the base of the fixture to accurately input that into the CAM software.
Step 21: The Machining
In the video above you can see the machine figuring out the tool length offset. This is critical and has to be done so that your piece can be machined properly. What this is doing is moving the bit and pushing a button which then measures the length that the bit is extending from the toolholder. This data is critical for the machine.
One of the best resources to use before you start to machine, is to simulate all of the toolpaths in the Penta Simulator which is specifically for Pocket NC machines. It can be found at https://sim.pocketnc.com/. When you upload the G-code it can make sure that you aren't exceeding any geometry limits of the machine with the g-code.
Step 22: Finishing Touches
Once I had the knob fully machined, it still had a stub, and no hole in the base to actually work as any sort of knob. What I did was to use a file to file down the stub to a flat surface, and then put the knob in a paded vice (to make sure not to scratch or damage it) and then used a drill press with a large drill bit to create a shallow hole in the be of the knob. The knob can then be fitted onto any sort of shaft or dowel. You can see image of the final product above, and what it looks like on the product.
Please let me know if you have any questions and I am happy to reach out and help you as much as I can! I am still in the learning phase for this CNC machine and I have a lot more to learn.
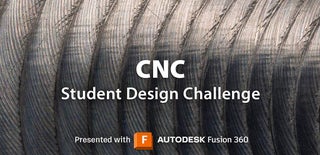
Second Prize in the
CNC Student Design Challenge