Introduction: A Simpler Sliding Bevel for Woodworking
I have already posted an instructable on making a sliding bevel, so you may ask why on Earth I would be posting a second one. After all, there are more things one can do than sliding bevels, right?
There are a few valid answers to that question.
- First of all, the sliding bevel shown in my first instructable, although it is a beauty (if I may say so myself), takes a heck of a lot of time to make.
- Second and most important, in order to make it I used a heck of a lot of tools. Now there is nothing wrong with using tools if you have them, but the point of instructables is to show others how to make something. An instructable that begins with "go get yourself a metal lathe and a milling machine" especially when addressed to a woodworker (amateur or otherwise), which I believe is the main target group of this, is not very useful. So here is my simpler version, which requires nothing more exotic than a bench bandsaw (sorry, the bandsaw is pretty much necessary, unless you are a handsaw wiz).
- Third, there is a "modify it" speed challenge on and I thought I would show you how I modify a shop-bought, bottom of the line sliding bevel with a plastic body and mediocre hardware into a beautiful tool that will be a joy to behold and even more to use.
- And fourth, I had an order for this exact tool, so I thought I would just document it as I build it.
If you have already read my earlier instructable, I hope you will forgive me for being somewhat repetitive here.
Measure twice, cut once goes an old woodworking adage. The idea is that it is easy to make measuring mistakes, but much more difficult to fix them once you have used the (bad) measurement for cutting a piece.
So, measuring once is bad. Μeasuring twice is better. One would be justified in assuming that the next best thing is measuring thrice, but in fact it isn't. What is better, amazingly, is not measuring at all. Or at least, not using numbers for measuring, opting instead to transfer the measurement directly from one piece to another. This is the idea behind "story sticks", and it works well. When you are dealing with angles instead of lengths, the equivalent tool is a sliding bevel. The simplest sliding bevel would be two sticks joined at one end with a bolt and nut. Traditionally however, a wooden piece is used for one side of the angle and a metal blade for the other. This makes for a much more convenient and versatile tool. The blade has a slot which allows it to slide, hence the name.
In the past, woodworkers made their tools themselves, or at least some of them. Aside from their practical use, these tools were made in such a way as to showcase the skill of the woodworker. A sliding bevel is perfect for this purpose: It is relatively small, easy to make and the maker can with relative ease add "bells and whistles" to showcase his skills.
During the last 3 years, I have made around 10 sliding bevels, including those I made for the previous instructable. In case you wonder why anyone would want not one but two or even more sliding bevels, there are many reasons. First of all, of course, the practical one: Some videos and pictures shot while making the first one did not come out very well, so I preferred to make a second attempt. Secondly, a nice sliding bevel makes a great gift for a woodworker friend. Alternatively, you can sell them (I have several for sale in my my etsy shop, some similar to the one made in this instructable and others, more expensive, similar to the ones I made in the previous one). Last but not least, it is sometimes useful to have more than one, especially if they have different sizes. If you don't believe me on this point, check this: In the first picture of p. 67, you 'll see that the famous toolbox of Henry O. Studley contained not one, not two, but three sliding bevels. Of course, Henry O. Studley was the ultimate tool junky, so you don't need three sliding bevels just because he was using three...
A sliding bevel can also be used for metal work. Once you get acquainted with it, you 'll find that it will become your tool of choice whenever you need to transfer an angle - be it from another piece, from a design or even from a protractor.
A sliding bevel consists of 4 parts: A wooden body, a metal blade, a bolt and a nut. In the previous instructable, I made all four parts. In this one I only made the wooden body. I used a shop bought nut and bolt and the blade from a shop-bought sliding bevel. I did fine-tune the bolt and blade, so they would be more to my liking.
WARNING!
Woodworking, as well as metalworking, are inherently dangerous activities. Before starting almost every operation, especially those that involve power tools, you must ask yourself two questions:
- What could go wrong here?
- How can I prevent this?
Whenever using a power tool, you need to make sure that the tool and the workpiece are held securely. Do not use a tool if you are not comfortable with its operation. Do not rush things. In cases where there are hidden risks, I will indicate this clearly with a "watch out!" section in the respective step.
Step 1: CAD Drawings
Whenever I make something that is not totally trivial, I like to begin by making some drawings in a CAD program. This helps me better visualise the end result, try different variations etc. In some cases I try to then follow the design as closely as possible. In other cases I only use it as a rough draft and improvise along the way.
For this build, I had the drawings from the earlier build, so I didn\t need to make new ones. Still, I attach the pertinent one here in case anyone needs it.
Step 2: Gathering Tools #1: Marking, Personal Protection
In this build I have used several tools, both for metal and wood working.
I also used some "generic" equipment:
--- Marking ---
- Indelible marker: I use it to mark metal (I later use alcohol to remove it) and wood (in places that will later be sanded).
- Pencil: Used to make marks where the marker cannot be used (e.g. in pieces that have already been sanded and/or finished).
- Marking knife: Unmatched for accuracy.
- Vernier caliper: Normally a machinist's tool, I use it all the time in my woodworking too.
--- Finishing ---
- Walnut oil: My oil finish of choice.
- Shellac: Applied after walnut oil, for added protection.
- Kitchen paper: used as a "brush" to apply walnut oil and shellac, among other uses.
- A pair of nitrile gloves: To keep my hands clean when applying walnut oil and shellac.
--- Personal protection ---
- Protective goggles: These are a must. Wearing them is the first thing I do upon entering my workshop.Please do not attempt to recreate this project without wearing goggles.
- Ear protection: I always use those when using power tools. They are a major annoyance, especially in the summer, but they protect my ears as they will protect yours if you make a habit of using them.
- Shop vacuum: Not strictly necessary, but it helps keep the space and the air clean, which is important for your lungs, among other things. I have one with an auto-start feature which is very convenient: Just connect the power tool to it and the vac starts as soon as the tool draws power. In an ideal world, I would have many of those and wouldn't have to cart it around the workshop. If you don't have a shop vacuum, you should at the very least wear a face mask when working wood.
Step 3: Gathering Tools #2: Tools and Supplies
For this build, I used the following tools:
- A desktop bandsaw (mine is a Metabo BAS 260). Theoretically you can do without the bandsaw if you are very skilled in sawing straight. In practice, I wouldn't even contemplate this project without the bandsaw.
- A belt sander attached to my workbench, with different grits of paper (P24 to P320)(optional). If you don't have one, you can use a palm sander instead. The belt sander however is much more aggressive, meaning you'll spend less time sanding.
- One or more 1/3 sheet palm sanders with different grits of wet-and-dry sandpaper (p280 to p1000). You can do your work with one, but if you have more you won't have to constantly juggle papers. Plus they are dirt cheep. I have 5 of those and used them all in this build. I could use a couple more.
- A drill press with a 6mm drill bit for wood and a 6.5mm bit for metal. If you don't have one, you can use a power drill instead.
- A bench grinder: for fine tuning the shape of the bolt head and the blade. Not strictly necessary but highly desirable.
- A 6mm chisel: to shape part of the bolt hole to match the shape of the bolt head.
--- Supplies---
- A piece of hardwood, around 2.1 X 2.8 X 20cm large. For this build I used walnut (this was what my customer ordered). I had an offcut from a previous build with the approximate dimensions needed, so I used this after trimming it.
- A shop-bought sliding bevel (for the blade): I used this one.
- A bolt and nut: I used a 1/4" brass hex-head bolt with matching wing nut. I find the color of brass complements wood much better than white metals.
Step 4: Prepare the Blade.
The first thing I did was to disassemble the shop-bought sliding bevel, throw away the plastic body and steel bolt and nut and keep the blade - the only part, frankly, that was worth anything.
I then proceeded to fine tune the shape of the blade on the bench grinder. I broke three sharp angles and smoothed all edges, which were too rough for my taste.
Step 5: Prepare the Body - Cutting
To make the wooden body, I started by marking the required shape and size using the indelible marker. I used the blade as a template. Using the bandsaw, I cut the body to size, then rough-cut the curved edges.
I left a little extra material, around 1 mm on each side, to account for the material that will be shaved away by sanding. In this step the exact size is not critical, except from the width, which must eventually (i.e. after the sanding) match that of the blade.
Watch out!
Whenever you use a bandsaw, you need to be careful to avoid approaching the saw blade with your fingers - especially the cutting side. Use a push stick whenever you approach the end of the cut.
Step 6: Prepare the Body: Sanding
I then moved to the belt sander. Starting with a coarse belt (P 40) I roughly shaped the body. Then I proceeded to sand it with progressively finer grits, up to P120, For the last 4 grit sizes (P150, P180, P240 and P320) I started wetting the workpiece with water, to raise the grain and cut it with the next grit. Otherwise the grain is just pushed down and is suddenly raised when you apply finish. With these last grit sizes I also proceeded to break the sharp edges.
The number one secret when shaping a curve with the sander (especially with a belt sander, which is very aggressive) is to keep the sander (or, when the sander is fixed as in this case, the workpiece) constantly moving. If you leave it stationary, be it for just a moment, you will produce a flat surface instead of the curve you want.
The second secret is not to expect the shape to be completed when rough sanding. With the coarse grit, you should simply aim to approach the final shape. Instead of a curve, at this step you will only get a series of flat surfaces. As you progress through finer and finer grits, however, the workpiece will almost magically take the shape you want. As you progress from coarser to finer grits, you should apply less and less pressure, in order to remove less and less material and leave a better surface.
One last trick: When you sand flat surfaces, use two steps for each one of them: sand it in one direction, then turn it around 180 degrees horizontally and sand it again (in the opposite direction this time). The reason for this is that it is very difficult to keep a uniform pressure on the workpiece. You may be pressing more toward the back side, or toward the right one. When you turn the piece around, you will compensate for this and remove an equal amount of material from both sides. Keep doing this with every successive grit and you will get good results. It goes without saying that here, as everywhere, practice makes (almost) perfect.
Watch out!
When you use a stationary belt sander (and many other machines), you need to be extra careful that the belt doesn't catch your sleeves. I've spent thousands of hours on this specific belt sander, so doing this is second nature to me - but even this doesn't mean I am safe. I had a friend, a professional machinist with several decades' experience at the time, who lost a finger in a work accident.
Step 7: Prepare the Body: Make the Bolt Hole
It was now time to make the hole for the bolt. For this, I started by placing the blade on top of the body and making a small mark with the marker. Then I moved to the drill press and made the hole using a 6mm drill bit for wood. The bolt is 1/4" (around 6.25 mm) and I wanted the hole to be slightly oversize, so I used a 6.5mm bit to enlarge the hole to its final size (bits for wood usually come in 1mm increments, but metal ones come in smaller steps). Having completed the hole, I checked that the bolt moves freely within it.
Step 8: Prepare the Body: Cut the Slot for the Blade
The next step was to cut the slot for the blade. I started by marking the ends using the blade. I marked both sides, since the slot ends in different positions.
I then moved to the bandsaw and started by making a cut up to the first mark. I then lifted the front (sawblade-facing) side of the blade to a 45 degree angle to cut the oblique end of the slot. This would be dangerous if I held the body only by hand, so I placed underneath it a block of wood to stabilise it. In this way, the operation was completely safe (or at least, as safe as a sawing operation can be).
With the slot completed, I inserted the blade into it to check the fit. It was perfect (as expected, since no measurements were made...)
The edges of a slot were a little rough, so I inserted a piece of P240 grit wet-and-dry paper and smoothed them.
Step 9: Prepare the Body: Enlarge the Hole for the Bolt Head
Now I had to enlarge the hole in order for the hex head of the bolt to nest in it. I started by assembling the sliding bevel, making sure that the head had the correct orientation, then tightening the nut and marking the head position into the body with the marking knife.
I started the (enlarged) hole with a 9mm drill bit on the drill press (just shy of the 10mm distance between opposite sides of the hex head). I made a 3mm deep hole. I then used a 6mm chisel to shape the hole into the hexagon I had marked. I made very small cuts, completely by hand (without using a mallet), until I had the shape I wanted. I then checked with the bolt and again it fit like a charm (again, no measuring, just transferring from one piece to the other...)
Step 10: Improve the Bolt Shape
I didn't like the surface of the top of the bolt head, so I disassembled the tool and broke the edges of the bolt head on the bench grinder, then used the palm sanders with successively finer grits of paper (P120, P240, P320, P500, P800) to give it a nice, satiny texture. This was of course not necessary, but having spent several hours to make this tool it wouldn't make sense to leave something I didn't like.
Having done this, I decided to improve the other end of the bolt too.
Step 11: Finish the Body
With the tool disassembled, I used a piece of kitchen paper soaked with walnut oil and wiped all surfaces with it. After about 15 minutes, I wiped the excess oil with a paper towel. I then applied 3 coats of shellac in the same way (with a piece of kitchen paper), leaving it to dry around 5 minutes and sanding with progressively finer grits of sandpaper between each coat: P600, P800 and P2000. I then applied a final coat and the body was ready.
Step 12: Assemble
All that remained to be done was to assemble and admire it! And then, of course, to start using it.
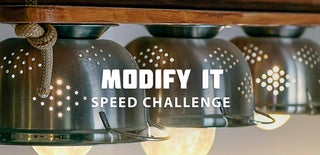
Participated in the
Modify It Speed Challenge