Introduction: A Trinket Box for Chains, Bangles, Rings and a Wrist Watch.
This Instructable is a step-by-step process of the modeling process of a trinket box with compartments for chains, bangles, a watch and ring slots using Fusion 360 CAD and CAM. The CAD part made use of features like extrude, emboss, sphere, cylinder, shell, split body, e.t.c. while the CAM uses 3D adaptive clearing operation, 3D face operation and 2D contour operation.
I, Adisa Taofik, a student of Mechanical Engineering at the University of Ibadan, Ibadan, Oyo state, Nigeria welcome you.
Supplies
Fusion 360 software
A CNC Machine/Router
Minimum of a 220*160*70 mm wood block
Step 1: CAD-Create the Base Box.
Create a 'box' of length 150mm, breadth 92.7mm and height 52.7mm. Then, use 'extrude-cut' (and the necessary sketch) to shell the box to a wall thickness of 5mm and a base thickness of 15mm.
Afterwards, on the inner base of the box, 'extrude-cut' the watch and chain compartment with the ring slots to your preferred sizes but ensure the minimum thickness of the base does not exceed 5mm.
'Extrude'/'emboss' whatever design you want the box to have on it.(For extrude you have to draw the sketch where you want the feature while for emboss, you can move the feature to wherever you want it.
Note: The dimensions was calculated with the golden ratio with the length as the constant.
Step 2: CAD-Create the Cover
Create another box of length 150mm,Height 35.4mm and a width 92.7mm.
On the width face of the box, Draw an 'arc' that will touch the two base point and the upper middle point of the box.
Use this line to split the body('split body') into two.
'Remove' the body that is untop of the curve.
Now, 'shell' the remaining body with the flat length face being open and a thickness of 15mm.
Draw a rectangle on the outer edge of the open face and 'offset' two rectangles from it with 5mm and 10mm each. Extrude the space between the two rectangles; this provides for the male part of the cover.
Extrude/emboss whatever design you want the box to have on it. For the curved part, you will need to emboss the pattern you want but ensure that the width of the pattern is equal to the length of the curve and not the length of the horizontal rectangle.
Step 3: CAD- Finishing Touches
Finesse your design and patterns with fillet and chamfers as due, fillet the sharp corners of the box to prevent the cnc tool from making sharp turns. (I used 1mm for the compartments and 2mm for others).
Add legs to the box with cylinder extrusions. Cross-check your design and be pleased.
Step 4: CAM-Input Setup Settings
Click on Milling, Go to Set up, Click Create new set-up.
In the Pop-up box, choose the operation type as milling. Select the machine you would use. Select your model. Choose the origin point. (I choose model origin, which is in the lower right corner of the base box).
Also, ensure the milling coordinates is accurate with the z axis aligning with the depth of the trinket box.
Go to stock, choose fixed sized box if you will be milling from a wood block.
Input the dimensions of the wood block. Click Ok when you are done.
Step 5: CAM-Operation Types; Adaptive Clearing
Click the drop down arrow beside 3D and choose Adaptive clearing.
In the pop-up box, Select the tool and the coolant(I used 3mm flat end mill and a mist coolant).
Go to geometry, Click on machining boundary and choose selection. then, choose face contours and click on all faces angled/perpendicular to the z-axis.
Select the rest machining box and let the source be from set-up.
Go to passes and change the maximum roughing step down to the diameter of the cutting tool.
Click Ok when you are done.
Step 6: CAM-Operation Types; Flat
Click the drop down arrow beside 3D and choose flat.
In the pop-up box, Select the tool and the coolant(I used 3mm ballnose end mill and a mist coolant).
Go to geometry, Click on machining boundary and choose selection. then, choose face contours and click on all faces angled/perpendicular to the z-axis.
Select the rest machining box and let the source be from previous operation.
Go to passes, change the stepover to roughly 8% of the diameter of the cuttting tool.
Tick Multiple depths box and change the 'maximum roughing step down' to the diameter of the cutting tool. Click Ok when you are done.
Step 7: CAM-Operation Types; 3D Contour
Click the drop down arrow beside 3D and choose Contour.
In the pop-up box, Select the tool and the coolant(I used 3mm flat end mill and a mist coolant).
Go to geometry, Click on machining boundary and choose selection. then, choose face contours and click on all faces angled/perpendicular to the z-axis.
Select the rest machining box and let the source be from previous operation. Click Ok when you are done.
Step 8: Repeat Steps 5-7
Repeat step 5-7 for each of the sides of the model.(6 times).
Under Set-up, change the z orientation to account for the side you are facing.( the z-axis will point opposite to where the tool will descend from).
The source of rest machining will be 'from previous operation' for all the recurring steps.
Step 9: Simulate & Post Process
After You are done, Go to Actions, Click Simulate and ensure no errors occur(Ensure the tool holder does not collide with the workpiece. Afterwards, Go to Actions, Click on post processor, click the drop down menu at post and choose the machine control software under library. Tick reorder to minimize tool changes. Depending on the capacity of your CNC machine, you can either tick all the operations and save or tick them each and save your nc code. Note: the attached file contains setup 1 and 2 of the operations.
Attachments
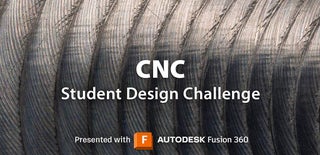
Participated in the
CNC Student Design Challenge