Introduction: Adding a Analog Milliamp for Your Laser Cutter
This is for everyone that has a K40 or K50 and higher quality laser cutter and is tired of losing money on Tubes that seem to die faster than they should. This is also for the winner of the Epilog Laser Contest I hope this helps you out on your journey with laser cutting!
For those that don't know, adding a Analog Milliamp Meter to your laser cutting system helps you keep an eye on how much power is running through your CO2 tube. If you run too much power, it deteriorates the lifespan of the Tube. It also can help you diagnose potential problems in your system, like a dying Tube, or a faulty Power Supply.
This presentation will show how I installed my own Analog Milliamp Meter into my Orion Motor Tech 50W Laser and will cover proper Wiring Techniques, Hole Cutting and Proper Laser Testing.
Please be safe if you choose to do this yourself.
Step 1: SAFETY
LASER CUTTERS USE HIGH LEVELS OF ELECTRICITY!!!
There is always a risk of shock or electrocution when dealing with any electronic device. When dealing with a class IV laser that risk becomes higher.
- Make sure to wear well insulated clothing/safety items. (Gloves)
- Keep the machine turned off and unplugged. (leave unplugged for 12 hours to be safe)
- Double check connections to make sure they are secure to reduce risk of arcing.
Not all laser cutters are the same. Different makers use different color wires, different power supplies so connections may not be the same.
Attempt at your own risk, please only attempt with proper electronics training and knowledge of your laser cutter.!!!!
Step 2: Materials
3" twelve gauge wire (black or black and another color)
1 Wire cutter
1 Wire stripper (or knife)
4 Ways to connect wire (Electrical tape, 4 pieces of heat shrink, 2 ring connectors, liquid electrical tape)
1 DC Analog Milliamp Meter (MAKE SURE YOU GET DC!)
1 Two inch BiMetal Hole Saw + Drill
1 Roll Painters Tape (or a Magnet)
1 Plastic Bag
1 Pencil
2 Sheets Sand Paper
I already had most the supplies like the electrical tape and the tools. All I needed to purchase was the Analog Milliamp Meter and I got it from Amazon for under 10$. Try to look for one that doesn't go any higher than 30 milliamp cause you will get a more accurate read on your power and you should never go over 20 milliamps power.
Step 3: Finding the Right Wire
For safety concerns wait 12 hours after you have turned off and unplugged your laser before touching wires
First you must locate the ending terminal wire of your laser tube. Depending on your laser this could be different color wires but for the majority they are going to be BLACK PURPLE or YELLOW wires. Orion Motor Techs "50W Laser Cutter" is going to be BLACK
If there is conduit covering all the wires go ahead and take it off, it will make much much easier.
For other laser cutters you can figure out which wire it is by looking at the power supply. It will be plugged into the L terminal. If you will look at the power supply it will be the leftmost wire on the power supply wire panel. Trace it from the power supply to the negative end of the tube for confirmation if needed.
There are very heavy gauge wires in your laser cutter case. DO NOT TOUCH THESE! They most likely lead to the positive end of your laser cutter, and can KILL YOU!
Step 4: Cutting the Wires and Prepping
- Go about halfway along the BLACK Wire and make a precise cut. Make sure both (now cut) wires have lots of flexibility to move.
- Look at where you want the analog meter to sit and measure out how much NEW Wire you will need to reach that, then add an extra foot.
- Make sure the NEW Wire you are using is the size of, or larger wire than what is provided by the laser, 12 gauge should do.
- For the wire the is still attached into the L Terminal, strip about 1/2 inch - 1 inch of insulation of the free end of the wire.
- Repeat step 4 for the wire that leads FROM the Negative End of Laser Tube.
- For both the New Wires that you have measured out and cut, strip both ends about 1/2 inch - 1 Inch.
You should now have six wire ends that have all been stripped of insulation. One leading FROM the Negative End of Laser Tube. One leading TO the L Terminal. Four from the NEW Wire extenders.
Step 5: Cutting the Holes
- Figure out where you want your Analog Milliamp Meter.
- Mark the Top and Bottom of space to be cut.
- Place a Plastic Bag on the INSIDE of laser to protect circuits from metal dust
- Put painters tape on the BOTTOM of where you will cut (makes it easy to see where you have cut all the way through and will stop some metal bits from falling down)
- Use Two Inch Bi-Metal Hole Saw to punch through metal.
- Use high speed for drill but push down slowly and firmly to cut hole. Stay level.
- Don't overwork drill, stop periodically and use painters tape/magnet to clear away debris.
- Once the hole has been cut, use sandpaper or other deburring tool to dull the edges of cut.
- Check to see if meter fits.
- Mark and drill holes necessary for securing Analog Milliamp Meter.
The hole you cut is based off the back end of the Meter. Make the smallest hole you can so it fits nice and snug and doesn't move around or allow you to see into the machine.
Step 6: Wiring the Meter Up
There are a few ways to connect wires. I will first say how I did it. Then I will tell the proper electricians way.
My Way To Wire
- Take the wire from the L terminal and weave the wire strands together with one of the NEW Wire extensions.
- Twist the two wire ends together.
- Cut one piece of electrical wire a little longer then the length of exposed wire and wrap it LENGTHWISE.
- Now wrap over that electrical tape at a diagonal angle and make sure that it is tight and well insulated and covers both edges of bottom layer of tape.
- Repeat steps 1 - 4 except with with the wire from the Negative End of Laser Tube and the second NEW Wire extension.
- Weave the wires back into the conduit and up towards the hole to keep things neat.
- Push both wires through the hole.
- Attach the wire from the L Terminal to the POSITIVE Terminal of the Analog Meter by wrapping it around the screw and tighten the nut.
- Attach the wire from the Negative End of Laser Tube to the NEGATIVE Terminal of the Analog Meter by wrapping it around the screw and tighten the nut.
The "Correct" Way To Wire
- Put a piece of Heat Shrink around one end of wire.
- Follow steps 1 and 2 and 4 from above.
- Use a flame or heat gun to shrink the Heat Shrink around the electrical tape and wire ends.
- Repeat steps 1 - 3 for other wire.
- Follow steps 6 - 9 from above.
- Instead of wrapping the wire around the screw use a piece of heat shrink to attach a ring connector to the ends of both NEW Wire Extensions.
- Put the screw from the Analog Meter through the ring connector and screw it down securely.
- Lather over every connection with liquid electrical tape.
Using heat shrink is usually more secure and "airtight" of a connection. Using the ring connectors also keep the circuit more enclosed and makes a easier and safer attachment to the Analog Meter.
Step 7: Securing and Testing
Checklist Before Test
- We are all wired up.
- The Wire is well insulated
- Wire has been pushed into the conduit neatly
- We have secured the Analog Meter to the machine.
- The correct wires are attached to the right terminals.
Make sure your machine is properly grounded.
Make sure you are still wearing protective equipment.
Carefully plug in your machine.
Carefully turn on your machine. (I used a piece of wood from a distance (I'm cautious))
- Don't use the pulse button.
- Start up a simple test file and do it at LOW power.
- If the meter dial goes LEFT instead of RIGHT the wires are backwards. (if it goes Right skip to step 8)
- If it goes LEFT, turn machine off, unplug, wait for capacitors to discharge and switch wires on the back of the Analog Meter.
- Repeat steps 1 and 2.
- If problem persists (or any other problem occurs) then check to see that you have a DC Analog Meter.
- If problem persists (or any other problem occurs) then check to see the wires from the Tube and Power Supply are correct.
- If problem persists (or any other problem occurs) then check to see that the wires are well insulated and connected properly.
- If problem persists (or any other problem occurs) then test the Analog Meter with another DC circuit (like a computer fan)
- Do multiple tests, slowly raise the power until you reach about 18 milliamps.
- Never go higher than 18 Milliamps for "50W or 40W Chinese Lasers"
COMMON PROBLEMS
Problem Group One
- Wires are not connected properly and circuit is not complete.
- Wires are not connected properly and causes a short or creates arc.
- Wrong wires from power supply were cut.
- NEW Wire extensions are too small a gauge for circuit.
- Wires are backwards on the AC Analog Meter
Solution
Connect Wires Properly
Problem Group Two
- You have a AC Analog Meter instead of a DC analog Meter.
- You have a faulty Analog Meter
- You have a Faulty Power Supply
- You have a Faulty Co2 Tube
Solutions
Replace Hardware (start from cheapest to most expensive)
Test without new hardware or separate from laser i.e. Test DC Analog Meter with another circuit
Step 8: Extra Info
When it comes to Laser Cutters, especially Chinese Laser Cutters you have to monitor how much power you are pushing through your tube and system.
Most Chinese Laser Cutters exaggerate the wattage of their tubes.
- A "40W" tube is most likely a 35W tube.
- A "50W" tube is most likely a 40W tube.
- A "60W" tube is most likely a 45W-50W tube
Real tube lengths-ish
- 55 x 800mm = 40
- 55 x 1000mm = 50
- 55 x 1200mm = 60
- 80 x 1200mm = 80
- 80 x 1400mm = 100
The exaggeration comes from the "Max Power" not "Rated Power" and running at the Max power will kill the tube a lot faster than if you run at the Rated Power.
Even knowing the Rated Power you still need to make sure you don't push too much power through your tube so you need to monitor the Current. For some 60W tubes you want around 22 mA or less and you want less and less mA for lower wattage tubes. Most people have around a 45W tube so try and keep the Current around 18 mA or around what the manufacture has suggested or even go by your own tests if you have the time. Just keep in mind lower Current = Long Lifespan
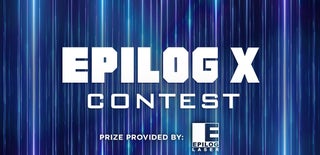
Participated in the
Epilog X Contest