Introduction: CNC Machined Airplane Propeller
To further challenge myself in design and setting up tool paths in Fusion 360 plus two sided milling. I designed a propeller in Fusion 360, set up the tool paths, created a fixture and milled both sides on my own design and hand built CNC shown here. The prop is 2 feet long and 3/4" thick. I used plywood to test my tool path versus some more expensive wood and the different layers gave it an interesting look.
Supplies
Fusion 360, 3.5" x 26"-3/4" thick plywood for the propeller, 3.5" x 26"-3/4" thick MDF for the fixture and a CNC Milling machine and bits.
Step 1: The Design
I'm by no means an aerospace engineer, LOL. So luckily Fusion 360 has Add In's. I used the "Airfoil DAT to Spline" Add In. The DAT file I used was of a NACA4412 propeller off the http://airfoiltools.com/search/index website. This gave me a realistic airfoil design to the prop, although I took some artistic liberties near the hub.
First, I found a front view of a prop on line, inserted it as a canvas then used the fit point spline sketch tool to draw am outline of the prop. Drew the hub, center hole and 8 holes.
Since the prop is 24" long or 12" from center to end, I set up 10 offset planes at every 1.2", created a sketch of the airfoil, with rotation for pitch available in the Add In tool on each offset plane. Then I used the loft function to create the body from each sketch of each offset plane and with a little trimming at the end, I had a half a prop. Then used the circular pattern to create the other half. Added some fillets, extruded the holes in the hub using the first sketch. It looks like a propeller now!
I have also included the Fusion 360 file of my model and CAM to see how I actually did it.
Attachments
Step 2: Thinking Ahead for Milling
Since I was going to mill this on my CNC and it needs to be milled from both sides, the design needed some modifications.
First off I needed a fixture for proper indexing when I flipped the wood over. While Fusion 360 does allow you to draw or make fixture and show the the two bodies stacked together. I opted for the easy way out as I only planed to used 4 of the 8 holes in the hub with dowels and that's in the first sketch so I just used that. So if you turn on both bodies at the same time they overlap each other. Thus when I created the CAM or tool paths for the fixture and prop, I just turned on the appropriate body for each one.
I also added a stand off to the body of the propeller on the back side, one towards each end. This way when I flip the wood over and set it on the fixture the standoffs will give the propeller support from underneath while milling the front more on that later.
Step 3: Setting Up the Tool Paths
Next I spent a lot of time playing with different tool paths. In trying to keep it simple I used only 2 bits, 1/8" flat end mill and 1/4" flat end mill.
Since I would be milling from both sides, I set up the tool paths to only go slightly more than halfway through the stock from each side. I used the 1/8" bit for the eight 1/4" holes in the hub and the four in the fixture. Everything else was with the 1/4" bit.
In the setup make sure you set the Work Coordinate System (WCS) correctly for each side. The WCS must be flipped in the Z direction for the other side when you flip the wood stock. So for each side I used the bore function for the eight 1/4" holes, pocket for the larger center hole, 3D adaptive clearing to get the rough shape and a 3D parallel pass for a finishing pass.
For the fixture I just used the bore function to create 4 of the hub's 8 holes in the MDF stock.
Step 4: Milling
I generated G-Code using the post process function within Fusion 360. I split up and or grouped the post processes for the 2 different bits. So I don't have to change bits as often.
With the MDF clamped down in the CNC with the 1/8" bit in the spindle, I centered and zeroed out my CNC and bit in the center of the wood according to the WCS in the setup for the tool paths. I bore out the four 1/4" holes in the MDF for the fixture.
I removed the MDF and placed it aside and clamped in the plywood, with the same 1/8" bit I bored out the 8 holes in the hub. Then I changed out the bit to the 1/4" bit and continued to mill the entire back side of the prop.
While the backside was milling I pressed 4 wood dowels into the holes of the MDF fixture. The dowels were about 3/4" long.
Now I removed the plywood stock and clamped in the fixture I created. I put super glue on those stand offs I created on the backside of the model and pressed the backside of the propeller down on the dowels of fixture.
I then continued with the 1/4" bit installed and milled out the front side of the prop. Switched over to the 1/8" bit and bore the 8 holes in the hub.
I used flush cut saw and cut the stand offs off the propeller and removed the prop off the the fixture's dowels.
Step 5: Finish
I did some very light sanding and used some polyurethane to finish it off. If you look closely you can see the airfoil design and pitch to the propeller. Of course I wouldn't use it on an RC plane, I designed and built it as a decoration.
Challenge accepted, LOL. I learned a lot through this process and I hope you all find it helpful. I'm sure there are a number of ways to model and CAM this in Fusion 360 and I look forward to any suggestions.
Thanks for looking and reading my Instructables. I've also entered it in the CNC contest.
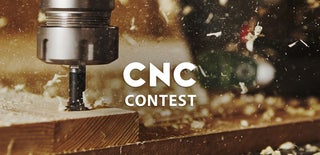
Participated in the
CNC Contest 2020