Introduction: Alien - Area 51 RGB Headphone Stand
This Instructables I guess I have been writing for the third time and the different thing is that every time I build this the process is entirely different and it's like the level of difficulty kept on increasing. So the first time I made it with simple hand tools, the second made with CNC but since I was new to that I didn't play much with that and the design kept quite simple. But now at the end of 2020, I made it so well that I don't think I am really gonna made one. The one downside is that it tremendously increases the working time. There are so many small details and areas where I have to machined first and then fill the resin and then machined again to remove the material so that I am able to install the led into the stand. There are some areas where the resin gets leaked out because of a very tiny hole and the next day when I came to see the result it's a complete disaster. I personally think that no matter how perfect you are these tiny mistakes definitely going to happen. There might be a chance that my work of approach is wrong but these things happen. I build two stands and the build time is 72 days. Yes, it looks insane time for these tinny little things but it happens. The design work took around 11 days because I need some inspiration and so many things needed to be designed in such a way that I am able to machine them easily with my 3 in 1 CNC and frankly say that is definitely a big test for that CNC as well. I can proudly say that machine works like a charm. Few minor flaws like tiny dust particles seen in the casting at 2-3 places I can say that this thing is definitely executed well from my perspective, rest I leave it up to you guys, that what you think about this build. The only change I wanted to do in this build for the next time is to use stabilized wood, but without any doubt that thing tremendously gonna increase the cost. I guess a normal person who never stepped into this manufacturing line he didn't know much about the complexity of this build but my maker friends will definitely know how tough this thing is. Again I thank you to give your valuable time to my Instructables.
Supplies
Material and parts used
Following are the list of material used in this build
● African wenge wood
● Two part slow set epoxy(low viscosity)
● ESP8266
● WS2812 led strip
● Power connector 2.1mm
● 5v 10amp power supply.
● Allen bolt 4mm
● Allen bolt 8mm for the neck 70mm long with nut.
● Wire
● Glue gun
Step 1: Material Cutting.
The wood I have comes in wide planks of 12" wide and 11⁄4" thick so I designed the layout in such a way that I am able to cut out one set at a time with my CNC. Luckily the size is under my machine limit so there wasn't much of a problem. So the initial size I cut onto the chop saw but the wood is so damn hard that the blade actually starts to smoke and struggle a lot. The entire room was full of smoke. With the required size, I make two cuts and then move onto my CNC for the flattening and contour operation. Here one thing you need to understand is that wenge cause problems to the health like sneezing, coughing and breathing issue and it kept on leaving colors to your hand which took time to fade away. So definitely consider these things in mind while working with wenge wood.
Step 2: Surface Roughing and Contour Path.
Since I didn't have many woodworking tools that's why I completely depend upon my CNC. But I think if you are able to acquire those planners and sander or at least know people who do this work definitely completed this task over those machines. It's surely gonna saves you a lot of time. The first thing I did is to put the machine onto the bed and then start the clamping process. The main goal is to prevent any wood movement due to the force of the tools during machining. On the three sides, I used stop blocks but onto one side, I use a wedge system for clamping. One thing I also measured is the thickness of the board even though it's 11⁄4" but due to light warpage and shrinkage it's uneven from different sides. Once I secure it completely with the help of 1" flat bit I started the roughing work. Once the one side has been completed I just flip it over and did the same on the opposite side. Once both the process has been completed I start the work onto the contouring process in which I have to remove the Alien head and the bottom triangle.
For the main contour of the putter periphery I use 6mm bit. Being wood I stick with 2 flute spiral endmill. For the inside cuts I uses 3mm bits. The one thing is absolutely necessary is to use tabs other wise it's going to be complete disaster if you are not using vacuum table or glue because at the final cut the workpiece ounces the bit and it gonna ruin the entire project. One thing I definitely want to suggest that try to leave some stock for the final pass it will increase the finish of your product because you are not removing too much material and because of very light cuts all the material removed leaves a much better finish.
Since there are tabs provided in the machining that's why I need to manually cut those tabs and that part is done onto the scroll saw. During this time eyes area are not removed don't know the reason but I didn't do that.
Step 3: Making a Jig and 3d Roughing the Head and Parallel Toolpath
Once the profile of the head and the bottom triangle is cut out the next thing I did is machining a pocket like the shape of the head into a piece of MDF so that I can place the head into that pocket and start machining the 3d hexagon into those wooden heads. The pocket to hold the cutout piece is a tiny bit larger than the headpiece so that the material is easily able to slide in and slide out. Now to ensure that my workpiece remains at its place and didn't move because of the vibration I use double-sided tissue tape to make it secure. Although it's a bit difficult to remove the material out but as far as machining is concerned the material stays in its place without any trouble.
To start the machining the first process is to do the 3d roughing. This is a time-consuming process like removing the bulk of the material so that the ball nose bit can easily able to remove the tiny bit material left and gives a nice clean finish. Although later on I tried a parallel path on raw material and it works perfectly well. So I guess if the stepover is .1 mm then you can easily use a tapered ball nose bit to make the 3d design on your workpiece.
Step 4: Constructing the Jig and Machined the Bottom Triangles
So like the headpiece the bottom base is also carried away in the same way. The first thing is making a pocket in the bed so that a triangular piece can be fitted inside that area and then start the machining process. So the design of the bottom triangle is like there is a 3d tapered onto the outside area but the inner area has a 2d machining. Since the outside has a 3d tapered that's why I decided from the inner side. So this area is actually for the led to install and the plan is like machined the wooden area and then fill out with resin and then machined again. So it's a long process to go. In the area where the text is going to be v carved at that area, the machining is done slightly lower than the rest of the thing otherwise it's going to be difficult to reflect onto the other side. So once the machining on the one side of the triangle is done I start the work onto the putter side which is going to be visible.
Now onto the top visible side of the bottom top triangle one thing which I didn't show is that the text area is already been filled up with the resin because after the machining the thickness of the wood leftover on those sides is only about 3 mm and since that's side is going to be recessed the thickness left is 2mm, so it is important to reinforce that area before carving the texts into them. The otter portion of the triangle is tapered and there are many areas where straight machining is required in steps so that's why instead of going with a parallel tool path I need to first do the 3d roughing and then go with the parallel toolpath. The parallel tool path is kept for later on in the process when resin filled into those designs. Along with the 3d roughing path, there is a 2d contour path also made for the led area and the alien head. The machining is done with a 2mm two-flute bit. Here the depth of cut is kept very low around .5mm deep. The text area has been machined with 3mm 10° v bit.
Step 5: Machining the Second Triangle
Once the work on the first triangle completed its starts to move onto the second one. Again here also I started from the inner side first because later on after machining it remains flat so that I am still able to stick the tape for holding purpose. The first thing is making a pocket for the Arduino which we need to install. From thereafter there is machining needs to be done for the led to set. The width of the led is around 12 mm that's why to make a nice tight fit of the led without glue gun I kept it 12 mm. From thereafter I flip the piece and start the machining onto the putter side also. Onto the base, I decided to put my logo with three heads to the periphery. So first step to do that is adaptive cleaning and from thereafter some 2d contour paths. The one thing for which I lost the footage is the logo machining process. In the first attempt, I first do the adaptive cleaning and then use the parallel toolpath but for the second attempt, I just use the parallel toolpath. The alien heads are going to serve as feet. The slots I made for the led was definitely not necessary but I want the base to be looks lighted that's why I added the light over those areas also.
Step 6: Filling the Resin.
Once the machining onto the top triangle of the base is completed it's time to fill it out with resin. I use aluminum tape to cover the rest of the area otherwise the resin gets absorbed by the wood and the oil effect gets changed a little bit. To create a reservoir over the text I use some glue gun to make a reservoir and then filled that area with the resin. The resin filling is done by the dripping method so that resin gets time to escape the air to come out. Since on the rest of the area the resin needs to be filled from inside that's why I have to put that area for the curing process. Once that text resin is cured completely I started the work on the remaining areas.
Again I use aluminum tape to cover up all the areas. The good thing about this tape is that it sticks very firmly to the surface compared to plastic tape or paper tape and also heat didn't affect the glue of the tape at all, that's why you can also use it for quickly hardened epoxy also. One thing here to note down is that don't fill the entire section of the top triangle at once because when the resin cures it shrinks and tries to contract which can cause a problem so that's why I need to go slow and steadily layer by layer. Once I fill it to the top I leave it to cure. Curring of this resin itself took 24 hr. Thereafter I started the work on the lower triangle. Here I cover it from the outer side with aluminum tape. And then fill out the resin. The resin was not filled out completely to the top just enough that is able to diffuse the light. In my case, I kept it around an 8mm thick layer. In all of the resin pouring process, you noticed that I pour the resin from high making sure to avoid bubble formation, and also slow setting epoxy gives you plenty enough time to allow the bubble to escape from the casting. Once the resin gets cured the parts are ready for the next step.
Step 7: Parallel Toolpath for Bottom Triangle.
Once the resin gets cured I again apply the double-sided tape and then placed it into the pocket which I created. Now, this is the time when you realize how important it is to install the limit switch in your machine. If you have to do a repeated job over 2 different things then the only thing you need to remember is the co-ordinate. If you know the coordinate you can repeat that job number of times. The bit I was using is a 4mm tapered ball nose bit having 10°angle and the tip diameter is 1mm. Then I start the parallel tool path over the triangles. This is definitely a lot more time-consuming task. It took around 2hr for one program to execute completely. The step over plays important role in providing finishing. The stepover of the bit I kept for my machining is around .1 mm. Now here I was worried that I don't machine too much area that's why the depth of cut I kept is around .1 mm and I noticed that there are so many areas where the resin gets absorbed by the wood which is visible so in the second run I go with .2mm depth of cut with wd40 along with it. I found that wd40 increases the quality a lot better than a dry cut. That's why you see me spraying wd40 many times during the machining process.
Step 8: Led Area in Eyes.
I was confused about how to install the led into the eyes, like the last time I didn't want to do anything into the acrylic portion and I also don't want to depend upon reflection because this time the eyes are milky white. So I came with the idea of wall mounted acrylic. In this, I machined an offset area from the original eye dimension. The depth was kept around 20mm of that offset tool path. The process was almost the same as stick the double tape onto the front side and then place it into that pocket that I made earlier and then start the machining process. For this, I use a contour tool path to do the machining work. The area to stick the tape onto the surface wasn't that much but even then those small areas are plenty strong enough to hold the headpiece to its place. Along with those led areas, I also made some slots for the wire to hide so that they did not obstruct the way and the good this is that it all went pretty well as I expected.
Step 9: Machining for the Second Time in Top Triangle to Lay the Led.
Now the most difficult part which I kept for the last and the reason for this is because holding area wasn't too much so I need to come up with something different. I use the center triangle as a hold-down area. But even then there is slight flexibility in that setup. I definitely did the facing operation but for the adaptive clearing, I decided to place some backer underneath that and then start the machining process. All of this machining done with a 3mm bit.
Step 10: 3d Print the Molds and Cast the Resin
To save the resin I decided to made some 3d prints a tiny bit larger than the required dimensions and then use them to cast the resin. Compared to a square section this process will eventually be going to save some material. To easily release the material it's good to spray a mold release. One thing that is absolutely mandatory here is that it's good to use slow setting resin so that you are able to cast these molds in one go and the good thing about that is you can get even molds compared to layer by layer casting. I noticed that problem that's why mentioning it here and this problem is absolutely mandatory to be considered. The color I used to mix in the resin is an acrylic color which works very fine.
Step 11: Maching the Casting of Head and Bottom Triangle.
Once the machining of the wooden parts completed I start the work onto the resin casting. So there are 3 different operation takes place in that. Both the head area and the triangle area needs to install the led strip. So first thing is to perform the facing operation, from thereafter flip the piece, and perform the facing operation again. Once the facing operation complete with the help of a 6mm endmill I did the contour operation which decides the final dimensions of the head and the triangle areas.
Once the contour operation is finished with the help of a 3mm two-flute bit I perform a contour toolpath to make a slot into the casting so that I am able to install the led strip into that cavity for the lightening effect. The thickness of the led strip is around 2mm so there is plenty enough space to bend the led without making any trouble. Into the triangle area, I also need to make a slot to hide the wires which need to perform separately. One thing that needs to be taken care of is that the casting you have to make, make sure to cast 3-4 mm extra to go safe. I went into a problem because of this issue and need to do the casting again.
Step 12: Machining of Eye and Neck.
Machining eyes and neck is another big problem in this project. I have to recast these things multiple times because of some issues during the machining and one time there is some problem in the casting. But the key to success is that you need to first make a layout onto the work surface onto which you are going to place the job. The reason for this is that you are able to align the job properly according to the requirements. Believe me, it gonna save you a lot of time and material.
Since there is no place to hold the material I have to use the tape method, but one thing I did here is that I use laminated plywood which actually makes a strong connection with both the surfaces and believes me this trick really works flawlessly. I have some long endmills which really helps a lot in this part. I didn't go all the way to the bottom because I don't want to decrease the holding area and the. During the next process, it might lose some of its strength. But this material I later on removed with the help of a trim router. The next process in the eye is a rounding process in which I use a tapered ball nose bit with a parallel toolpath. With a little bit of wd40, I get a much better finish than dry cutting.
The next problematic thing is how to machine neck the length of the neck exceed more than the bit I have so that's why I have to do this in two separate parts. The good thing is that it went pretty sweet. So the first thing I need here is to create a work-holding system to hold the neck because the tape method is not gonna work on an 80mm long piece. The chances are pretty high that is going to fail at any time. Then I machined two different pockets the first pocket dimensions are equals to the 3d printed neck case and the second pocket is equaled to the required dimensions of the neck. During this build, I made so many different setups to machined these things which really consumes a tremendous amount of time. But gladly the neck machining goes well in two different parts.
Step 13: Partially Filling the Eyes With Resin.
During the starting of this build, two things I didn't know first is how to connect two heads by making the bolts completely hidden. Second thing is that how to connect the neck with the headpiece.
For the eyes what I did is that I covered the backside with the help of laminate and glue gun so that resin will not leak out because this is the crucial part and I already wasted a lot of time and the advantage of using laminate is that you can easily able to remove this because epoxy wasn't able to grab it very tightly and when you use a little bit of heat gun it easily releases the material. So after closing the o e side I use a piece of rod and colored some of its area around 6mm so that I am able to guess the depth of resin I poured into the eye socket because too much resin will not allow led to getting into the machined area. Once the resin cured it's ready for the next process in which this has to be connected with the neck and the bottom triangle.
Step 14: Machining the Neck Cavity.
I think in the entire build, every day I kept on thinking that how I am going to connect everything together and how to machined that area. So I came up with a vise-like contraption. But before that, I have to do some preparation. With the help of double-sided tape, I first connected the 3 head pieces together. Then I made my own wooden vise on which I am going to hold the head for machining. The vice contains two wooden blocks connected together with an M10 thread rod. Once the one jaw is secured to its place with the help of a threaded rod I bring the second wooden jaw closer to the fixed one and make it secure properly. Then with facing and contour operation made the vice completely square with the gantry because from here after I have to take reference from these areas to make the head completely square. The next operation is a crucial one because I have to clamp the head pice perfectly square to the bit and I have no option to take the reference. Then I found that those hexagons are in a straight line so I measure the distance of the hexagon from the bottom and along with that I also have to keep it square. This process took around an hour to align. Then by remembering my god I start the machining process. The height of the machined was too much that there is a high chance of flex, that's why to minimize that thing I went slow and steady and able to achieve a task which at a time seems almost impossible to me to achieve. During this task, one thing is to take care of is that machined that area with the bit having a radius equals to the fillet used in the neck design.
Step 15: Drilling for Fastener and Power Connector.
Now the build reaches the final stage in which I have to connect it with a fastener and also attach a power connector. So again I use double-sided tape to hold the pieces together and form thereafter Use the previously drilled holes for the reference and then with the help of a 3.5 mm drill bit drill the holes. Make sure not to drill thought holes because that looks completely horrible. I also drill the holes into the eye area also so that bolts remain hidden inside this area. The holes in the eyes are drilled just by eyeballing. Then after drilling the holes with the help of an M4 thread tap I tap those holes. Along with those holes I am also going to use nuts to make it double secure.
For the power connector, I measure the center distance and from thereafter with the help of a 1⁄2" step drill, I drill the hole by making sure that the connector has a very tight fit inside that hole.
Step 16: Connecting the Neck With the Head and Bottom Triangle.
Now all the work left is to connect the neck. Before proceeding to the connection part, I need to first buff the neck because after that it would be extremely difficult to polish that once it gets connected to the bottom triangle. I use a 3M buffing compound and with the help of an angle grinder and buffing pad start the buffing process. The one slide disadvantage of buffing I get in this process is that it slightly round of the edges, and sometimes it removes the tiny detail. But It all ent good and after a few minutes, the neck becomes nice and shiny. Here one thing you have to note down that the grinder is running at lower rpm and only by doing that you are able to get a good smooth finish.
After that, I drill the hole in the headpiece and the final drilled hole is 8mm since the bolt is a tiny bit undersized, so there was no problem in inserting the bolt into the hole drilled in the neck. To hold to the bolt at a fixed distance what I did is to wrap some tape around that bolt and from thereafter it went tightly inside that hole and kept stuck at the desired area. Now I have to jam that bolt to its desired position. So first I did is spray a little amount of wd40 so that epoxy didn't stick with the rest of the material and clean the bolt with the help of acetone. Then I cut a small triangular piece from the face shield and insert that into the machined area so that it acts as a barrier if anything gets leaked out I am easily able to remove the neck. The neck already has a hole inside it in which I am going to insert the led. By making sure that bolt stayed at the right height I start filling that hole with epoxy but not up to the full depth. Since it was cold that why I need to use a little bit of a heat gun to heat the epoxy to activate it. The next day the neck came out very easily without any trouble which is a clear indication that every effort made execute perfectly well. Now I need to connect that neck to the head. Since I already drilled the hole the only thing left is to make a visible end so that we are able to fasten that bolt by inserting a nut into that bolt to make a strong connection. With the help of a drill and rasp file, I made a box inside the headpiece and now it's ready for the connection.
Connection with the head is a temporary connection but with the bottom triangle, I need to make a permanent connection. For that I make it secure inside that triangle cavity and then hold it with the help of a glue-gun. To prevent the resin to flow in the neck I close that hole with an old casting mold of the neck and then fill it with the help of resin. The next day resin cured and the neck is permanently fixed to its place. Then with the help of a drill bit, I remove that orange mold and with the help of a file make that area completely flat.
Step 17: Magnetic Eye
I want my item to be repairable, so by keeping this thing in mind I drill down the partial holes at the back of the eye to make some space for the bolt head to sit into, and then along with that, I am also going to add some neodymium magnets. That's a pretty easy task just drilling a 5mm hole for the magnet and 7 mm for the bolt head and then apply a tiny amount of superglue and put it with the help of the bolt head.
Step 18: Polishing and Finishing
Once most of the thing gets completed I do the final polishing process. I hold the resin piece into the vice and then with the help of an angle grinder and buffing compound start the polishing process. Before this, I sanded down the surface up to 600 grit both the wooden part and the acrylic part by clamping it together to make everything completely flush. The resin area onto the wooden part is difficult to polish because the wood has textured and if I went to polish that area all the polish get stuck into those areas which later on is extremely difficult to remove so I avoid it.
For the finishing, I was actually confused about whether to use spray finish or use linseed oil. The wenge turned black with the oil finish and I decided to keep the finish natural so I go with the oil finish. I pour the oil into a container and dunk the wooden parts into it. Then I place that container into the vacuum so that all the oil gets absorbed by the wood. This thing also going to stabilize the wood and prevent moisture to enter the wood. Then I remove it out of the container and allow it to dry completely and I repeat this task 3 times to make it stabilize. The good thing about linseed oil is that within a few hours it gets dried out by itself by living and nice natural wood finish and also enhance the wood grain.
Step 19: Electronics.
Frankly said there is nothing complicated about this part. All the LEDs need to connect in series by making sure to follow the arrow made onto the strip. First of all, I cut down the strips to the right length for a perticular area and thereafter I start the work on soldering them together with wire. I also need to make sure that the wire will not obstruct the path while closing the pieces together. In the Arduino pin D1 is used for signal and to provide power to Arduino I also solder the wire to the ground and voltage pin. With the help of glue-gun wires are glued to keep them to their place. A small hole has been drilled into the neck so that wire can be easily deeded out of the neck to the head area. Here you can also able to see the connection of the bottom area to the headpiece. Bolt inserted into that piece and then secured it with the help of a nut and tightened it completely. Now the only thing left is to assemble all the pieces together and put the code into the Arduino.
To connect it to over the wifi network all you need to do is to connect with wifi whose IP address starts from 192.168.-.-. I found that on the other IP address it gave some trouble. Once you fi the default I'd password and click on the wifi name a WiFi manager page open up and all you need to do is to connect with your wifi network by filling its password. Here also make sure that the default static IP it showed is 192.168.1.222 also make sure if there is any other device using this IP make sure to disconnect that first do that stand able to connect with it. Usually, it gets connected without any problem and the only thing you need to do is to open the browser on your phone or computer and type 192.168.1.222 and web software is open up and from there you are able to choose your favorite program which suits your setup.
Step 20: Finally
This is the moment which I have been waited for over 2 months that How this design is going to come out. I was worried about whether I am able to complete it or not. But I guess with God's blessing and dedication I am able to succeed in my task.
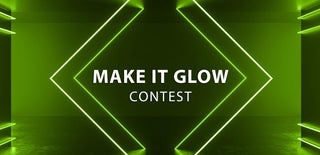
Second Prize in the
Make it Glow Contest