Introduction: Aluminium Casting and Why You Need to Be Careful
With interesting projects comes the possibility for interesting problems or as a recent Instructables competition puts it, Epic fails.
Maybe I should be concerned that when I checked the emails this morning and saw the competition for epic fails that I had at least 2 options ;)
I have been melting metal for a few years now, in this instructable I will detail a few of my experiences along the way and a few things that I do not recommend for your own safety.
My first metal melting experience was with a coal fired foundry. It was created with a 20 litre stainless steel bucket on the outside and a 4 litre bucket on the inside, a pipe came through the side of the bucket and was connected to a vacuum cleaner on blow. The space between the 2 buckets was filled with normal concrete and while it did melt metal it also spewed small hot coals once it burnt down a little.
My first crucible was a section of 100mm galvanised pipe with some steel plate welded to the bottom. 5 or 6 years ago when I made this earliest foundry I did not have the skills to make the crucible myself so one of the fitters from work made it for me. While I no longer use I do still have it.
The photo above is pretty much my second foundry. It was LPG fired and was reasonably effective.
Like the first foundry it was made with ordinary concrete and through some miracle it did not explode or spit at me.
In ordinary concrete the cement adsorbs the water in the mix thus at high temperatures it can release the water.
Water is many times the volume in steam form (1600 x I heard once) and water turning to steam inside a closed volume can result in extremely dangerous steam explosions where concrete can go flying.
In the photos above I am melting brass from old tap ware in a commercial clay graphite crucible bought off Ebay.
In the second photo I have poured the brass into my so called 'metal muffins'.
As you can see here muffin tins make great ingot molds
Step 1: My Current Furnaces
Around a year ago I decided that more serious metal casting was on the agenda.
Like any mad scientist I went to Google, Instructables and YouTube and read and read.
Not wanting to spend a great deal I settled on a home made refractory mix of Perlite and Calcium Aluminate cement. I don't know the exact chemistry but CA cement performs MUCH better under heat than ordinary cement. Perlite is a processed natural substance, sort of like pumice, super light and fluffy, with excellent insulating properties.
In the photo you can see the furnace just after me making it.
On the outside is a section of 200L oil drum, then the home made refractory then the 'hot face' was a commercial 'muffle ring' made of Clay Graphite mixture. Muffle Rings are used in large furnaces to 'extend' the sides of the crucible so the solid metal can be piled above the crucible and not spill out. The metal will obviously melt down to a smaller volume and be contained by the crucible itself.
The muffle ring was approx. 400mm diameter.
As per proper commercial refractory one should always proceed slowly with warming up their new furnace to slowly drive off any remaining water in a controlled fashion, failure to do so can result in problems as described in the introduction.
Step 2: Current Generation of Furnace Running
Here is shown my first new generation of furnace running.
I dont know exactly what temperature I was achieving but I was able to (just) melt brass, my best guess would be in the vicinity of 1100 degrees C.
This burner was dual fuel starting on LPG to warm it up before applying waste oil then turning off the gas.
The burner used a spa pool blower and a dimmer style speed control to vary the airflow.
I was too stingy to spend any serious money on a 'proper' furnace nozzle so my oil delivery system consisted of old mineral oil in the blue tank then pressurizing the tank with my compressor, the oil was then delivered by a hose to a nozzle with a 0.5mm (or thereabouts) hole and squirting into the hot furnace and burning.
So long as you apply air in the correct proportions to the oil you can achieve a relatively clean and smoke free burn.
You can see in both photos the furnace glowing super hot, both of these are radiant heat only, the intense glow is not combustion. See in the second photo the perlite 'composite' lining of the lid glowing red hot also.
Note in the second photo my safety gear, this would be the very minimum; Polycarbonate face shield (performs incredible in the heat, still on my first one), Leather welding jacket, Cotton overalls, Leather work boots.
Note here I am wearing ordinary (but quality) welding gloves, soon after this photo I bought some proper aluminized gloves of eBay after some serious burns to my hands. I found that when exposed to furnace exhaust air that the gloves can just heat up too fast and by the time you realised that they were hot that you could not get them off fast enough.
Also around this point I discovered steel 7lb fire extinguishers as the best crucibles that no money can by. I contacted a guy who supplies and certifies fire extinguishers and he has given me a number of them during the last year and they make the ideal crucible and last for quite a number of melts before the steel flakes off too much.
Step 3: When Aluminium Catches Fire, the Thing That I Never Saw on Any Casting Website
Struggling to melt Brass I spoke to a rather helpful commercial refractory supplier who recommended that I use Kaowool to insulate the furnace. The ideal would have been the outside of the hot face but I didn't want to make another at this point so I loosely lined the inside of the furnace with Kaowool and I was quickly able to reach brass melting temperatures.
Kaowool is a ceramic blanket (mine was 50mm thick and rated to approx. 1300 degrees C)
One fateful night about a year ago I was melting aluminium scrap into ingots. I had asked my wife to grab the camera for us to take a video to show an interested family member when I saw the flames change from orange to a more yellow color.
The flames and furnace seemed to almost twinkle for a moment(best explanation I have sorry) before a bright white/yellow flame shoot up from the furnace to a height of a metre or so.
The flame was not explosive and was directed straight up out of the furnace (We would liken it to a fountain firework only much bigger and more intense). While we were outside we removed anything that might catch alight from nearby and turned off the air and pulled out the burner.
I would approximate that there was between 2 and 3 litres of molten aluminium in the crucible, this burnt for say between 2 to 3 minutes (was still burning after we had scurried around moving nearby 'stuff') and in this time it consumed all of the aluminium in the crucible and destructing the crucible itself.
In the photo to the right the spongy mess is all that remained of the crucible after the experience. I believe that the Aluminium burn melted or burnt the Kaowool on the sides in the bottom of the furnace.
The refractory base while damaged was not 'burnt through'.
My research since leads me to believe that the temperatures in the furnace after aluminium ignition probably reach towards 2000 degrees C but I have no way of knowing.
Not long after this I discarded this foundry and built another.
To answer the question before it arises the metal I was melting was extruded aluminium conductor.
Step 4: Summary
Still a year or so on I still have not seen anybody mention of Aluminium catching alight during casting.
Undoubtedly the melt was way too hot but still...
Just as I close I might add the 2 simplest things learnt so far from my casting experiences.
Safety Equipment is your Friend.
Volatile liquids that turn to gas then fireballs (Including Oil, LPG, Methylated Spirts) are your Enemy and should be treated with extreme caution.
Stay tuned, I hope to post another epic fail in the next few days.
Hmmm a home made Vacuum chamber, what could go wrong.....
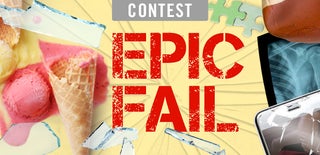
Second Prize in the
Spectacular Failures Contest