Introduction: Amber Ring
Last year, as Christmas approached, I uttered the phrase I'm sure many of the users of this site have before me:
"I'm going to make all my Christmas gifts this year!"
When it came to my significant other, something special was required. I decided to make a ring using her favourite stone - amber.
Previously, I'd only ever used amber in colour-related similes, so fixing it to the ring was an obvious empty space in my mental toolbox. In my research, I found images of the style I wanted to make, but few clues on how a jeweller would fix the stone with no mechanical means of setting it. I'm still not thoroughly sure how a jeweller would do it, and I'm sure this is sacrilege, but I used CA glue.
I've never made any kind of jewellery before, and given the possibility of mistakes, I used brass for the ring itself rather than a precious metal. Silver wire beading encapsulates the amber, which adds interest; more crucially it conceals the bond between the amber and the ring below.
Step 1: Tools and Materials
For this project, you will need a few tools. I have sorted them into categories; essential, and make-life-easier-useful.
Necessary tools:
Drill with suitable (for soft metals) bit
Hacksaw (Or rotary tool with cutoff wheel)
Clamps and vice
Blowtorch
Small round file (Or needle files)
Measuring device
Useful extras:
Tweezers or forceps
Calipers
Rotary tool with HSS burr or similar, sanding drum, polishing discs
Automatic centre punch
Materials:
Brass round bar 22mm (7/8") in diameter
0.5mm (0.02") silver wire
Fine solder (Preferably jeweller's silver solder, but I used electronics solder because I'm a savage)
10mm x 8mm (3/8" x 5/16") piece of amber
Polishing compound
Cyanoacrylate glue - also known as superglue
Step 2: Cut Off a Blank
Before I started the project, I got all creepy and measured my partner's finger while she was sleeping. I used a small strip of paper, wrapped it round her finger and made a mark where the paper ends met. This, when straightened out, is the diameter of the finger. After I'd taken off my balaclava and sneak-around clothes, I went out into the workshop to do some measuring.
First, I turned my attention to the brass bar, which, at the time, was far longer than the average finger and not nearly annular enough.
Using the hacksaw or cutoff wheel on the rotary tool, cut off a small disc from the brass bar. It doesn't need to be particularly precise, but it must be wide enough to shape down to the final dimensions. I used a bar 22mm (7/8") in diameter, because that gave me enough width to accommodate the 19mm (3/4") inside diameter whilst maintaining enough thickness to shape down.
Step 3: Drill Through the Middle
Using a pair of calipers, scribe a line around the circumference of the blank, forming a circle which is 19mm (3/4") in diameter. This will guide the material removal from the middle of the brass.
Using a centre punch, mark a point in the middle of the brass for the drill bit to sit in. This doesn't need to be central - it will only provide a divet for the drill bit to bite into and prevent slippage.
Next, using a drill with a suitable HSS bit, drill a hole through the brass. Of course, if you have a drill press, you can use a much large drill bit and almost forgo the next step, but I don't, so I can't.
Step 4: Shape the Brass Into a Ring
Now there is a hole in the brass, but it's way too small for anyone's finger.
Enlarging the hole can be done in a number of ways; a rotary tool can come in handy if you have a small HSS/Tungsten Carbide/similar milling cutter. Just go slowly with it to avoid excessive heat build-up. When the hole gets larger, switch to a sanding drum attachment and keep going - this will make it much easier to keep the inside of the ring circular - the larger the diameter of the attachment the better.
If, like me, you have a bent for hand tools, you can use needle files to begin with, progressing onto a larger round file when the hole is wide enough.
Shape the outside of the ring as well; remove some of the thickness of the ring, round over the edges, and file a flat face into one side for the amber to sit on.
Step 5: Polish
After all that filing, the surface of the brass is probably course and textured. We want it to be smooth and shiny.
We can bring about this change using progressively finer grades of wet or dry sandpaper - start with a course grade, such as 120 or 240, and work your way up, at each step making sure the marks from the previous step are removed completely. I went up to 600 grit, which is the last preparatory stage before the polishing.
Brass can take a lovely polish if prepared properly, although it doesn't last long before it tarnishes. Use a rotary tool with a buffing wheel charged with polishing compound - if the sanding was done thoroughly, this step will not take long. Alternatively, you could use a small amount of brass polishing cloth and elbow grease.
Step 6: Silver Wire
Next, turn your attention to the silver beading which will cradle the amber. I twisted some 0.5mm (0.02") silver wire into a two-core thread. Once twisted, it can be curled around the amber into the correct size - it should be fairly snug around the stone, but loose enough to make setting the stone easy later.
Using a pair of forceps or a clamp, hold the wire in the correct shape for soldering. The joint should be clean and tight. If using silver solder, make sure to first apply flux to the joint to allow the solder to flow. I was improvising (read, bodging) with some flux-cored electronics solder, so I didn't need to worry about this.
Using the blowtorch, heat the silver wire carefully under a controlled flame. Poke some solder into the joint, making sure that it flows into the gaps between the wire. Cut off any excess wire and be VERY CAREFUL NOT TO LOSE THE SILVER HOOP!
Step 7: Solder Wire Onto Brass
Before putting away the blowtorch, solder the silver hoop onto the brass ring. The brass will require more heat to get it up to soldering temperature, and don't worry about tarnishing the brass or the silver. the primary focus here is getting the placement right - if you get it wonky, it'll look weird when it's finished.
Hold the silver in place using needle-nose pliers or tweezers while you solder it. During operations like this, a vice really is invaluable, although if you have a soldering third hand, that would suffice. Suffvice? No, that's terrible.
Don't worry too much about the soldering from the previous step flowing - the surface tension of the solder should keep it in place.
Step 8: Final Polish and Test Fit
The heat from the blowtorch will likely have tarnished the brass, and, to some extent, the silver too. take this final opportunity to give the metals a final polish to remove any discolouration.
It might be necessary to go back to files and sandpaper to remove excess solder from the joint between the silver and the brass. Don't try to only remove the solder and skip the sanding - you'll get a better final finish if you go through each step again.
With the metals back to their former resplendent shine, test the amber for fit. The tighter the better, but if you have to bend the silver hoop to make it fit, it may be too tight. If this is the case, try either removing some material from inside the hoop, or desoldering and reshaping it.
Step 9: Knock Stone Onto Floor, Spend 10 Minutes Looking for It, and Glue
With the amber sitting precariously on the ring without adhesion, use your elbow to knock it onto the floor while reaching for your CA glue.
It's times like these which make you understand the value of having a tidy workshop. I spent 10 minutes looking for the stone in the sawdust, metal shavings, welding slag and oil spills.
Once found, the stone is ready for gluing; make sure the surfaces are clean, and put a small dab of glue onto the brass where the stone will sit.
Place the stone into its now permanent home, and apply a small amount of pressure using your fingers to hold it down for a minute or two until the glue sets. Next, put the ring upright somewhere safe overnight while the glue dries completely.
A few tips:
Make sure the stone is correctly orientated in the seat.
Try not to use too much glue.
Don't glue your fingers to the ring; you will not appreciate the irony.
Step 10: Done! Thanks for Reading.
And you're done! Inspired by this instructable, I made a presentation box from a half log of ash which was otherwise condemned to burn in the woodstove.
The brass will tarnish quite quickly when the ring is worn, but that's fine. The less like gold it looks, the fewer people ask me if the ring is that kind of ring.
Making a ring like this is relatively accessible; very few tools are required, and the project's total cost was minimal:
Brass round bar: £6.20 ($9.42)
Silver wire: £1.80 ($2.74)
Amber: £5.12 ($7.78)
Also, as I've just proved, you don't need any prior experience of jewellery making to make it.
Thanks for reading!
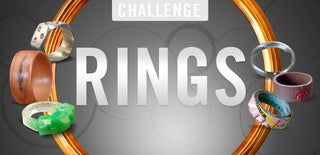
Participated in the
Rings Challenge