Introduction: An Easy and Cheap RPM / Tachometer Upgrade for the Mini Chinese Lathe
My 7 x 14" Chinese mini lathe had no RPM / tachometer when I bought it and I have been using it with no real idea of what speed it has been running at. Many of the old hands who use a metal turning lathe have never had a speed readout and many of them have added some form of readout. I have been doing some milling using end mills, and now that I have a speed readout I see I have been running the mill bits at too high a speed. So, I am very pleased I have sorted this out now and fitted this tachometer.
I have seen videos of a number of ways to add one of these speed readout to the lathe and I decided to go with this idea. I felt it was simple and did not break into the lathe too much.
Sorry the 1st digit is a bit faint in this image - I took a number of images to get the full display from this distance and they were all the same. The readout is clear on all 4 digits as the image in Step 2 shows.
Step 1:
Obviously the place to start is to find a tachometer at the right price and some ideas of how you are going to fit it to the lathe.
On eBay I found a AU$16 4 digit tachometer with hall switch sensor kit and built my design around this. Once you have this in your hands you can measure it up to see where you can install it. I chose to install it in its own box as I did not want to do much cutting into the lathe. Some people have in fitted it into the front panel of the lathe's speed control box. I have seen a few designs where the speed readout is above and behind the headstock, so this is the idea I went with.
Step 2:
The first step was to test the tachometer and where to place the magnet and hall sensor. As you can see from the images the sensor has a long threaded shaft to allow a large adjustment to reach the place where you put the little magnet (the kit comes with a small ceramic magnet) In the 1st image you can see that the readout is just placed where I could see it working but safe from the wires etc being tangled in the chuck or gears. (I actually 1st tested it with the magnet stuck on the chuck's backplate and held the sensor near it as the chuck turned - the way it works is as simple as that! ).
NB. The little magnet must be mounted with the right side towards the sensor - it will not work the other way around.
I decided I would mount the sensor behind the spindle gear and through a slot I cut out of the gear cover.
I found that If I made a steel washer with a small bent over piece I could mount the magnet at the back end of the lathe spindle between the two nuts. See the 1st image. this was made from a cut out from a galvanized joist hanger (I had an old one in the shed that we had used to put beams across an old pergola). Any piece of galvanized steel plate will do and the magnet will stick to it for the test. (the magnet needs to spin past the sensor once per revolution and needs to be around 1cm away)
Then I made a right angle bracket out of the same piece of galvanized plate. I drilled and tapped two 5mm holes into the belt drive cover plate alongside the belt gear and spindle gear and mounted the bracket.
A lot of measuring is needed to make sure the bracket will allow the gear cover to be put back into place. The cut out I made in the gear cover is shown in the images. Fortunately the cut went through the middle of the forward / neutral / reverse label. I had considered making a new label and sticking it elsewhere on the back of the lathe but the main instruction is still readable.
Step 3:
THE PARTS I USED TO MOUNT THE READOUT
After a lot of thought I chose to use some very simple, cheap and common PVC electrical conduit bits and pieces, an old 12 volt transformer (which I broke open to use just the transformer and rectifier board)
1x 20mm (or 25mm) 1 way conduit junction box
1x short length of 20mm or 25mm diameter conduit - we only need a short piece
1x 20mm (or 25mm) cable gland
As my hardware store had run out of 20mm cable glands I chose to use a 25mm one with a 25/20mm reducer. I already had a length of 20mm conduit at home so I chose to use 20mm. I'm sure 25mm would be a little more sturdy but with such a short length what I've set up is still pretty good.
Step 4:
I contemplated buying a plastic box to house the parts and, for a while, I wondered if I should keep the transformer (with it's mains power leads etc) separately, but, because the transformer only needs to be a very small one, I decided to build a little purpose made box out of MDF and paint it.
This box is made from MDF 6mm back and sides and a 3mm front. I added the pine frame in the back to enable the back plate to screw down.
There are so many ways one can build a box I'm only going to show a few simple pictures of the procedure I used.
The cut out for the display box needs to be measured carefully. As the display box has a clip on each side to hold it in place when mounted, I beveled the sides of the hole I made to help as my MDF front is 3mm - you can see the bevel in the images.
The base of the box will be drilled (25mm in my case) to take the cable gland on top of the conduit pipe. The placement of this hole will depend on the transformer and other parts you are putting into the box.
Step 5:
FITTING THE CONDUIT PARTS FOR THE CABLING
I held the junction box (with a short piece of conduit in it) on the back of the lathe headstock and got it square / vertical so I could mark the two holes I used to screw the junction box to the headstock.
I then drilled and tapped the two holes for short 6mm bolts (10mm is long enough) and screwed the junction box to the back.
I worked out approximately how high the readout box would be and cut the conduit. (A little pipe cutter does a beautiful job on the PVC if your have one)
Step 6:
PULLING THE CABLES
As you can see from the images I drilled two holes (10mm each) into the juction box on the opposite side to the forward / reverse lever. I put 2 rubber grommets into these holes to protect the cables from chafing on the hole edges.
I had originally thought of taking the mains (240v) wire from the inside of the lathe's control box, through the hole in the bed where the motor cable runs, then through a new cable gland in the tin motor cover, and up into the junction box. Then I decided to just run a cable with a 240v plug into the junction box and up the conduit. Yes, the machine now has two mains cords but that's not a problem. I may still run the cord through to the lathes power connections, but for now, it's working and I'm happy.
The cable for the hall sensor is taken over the top and round the back of the conduit to avoid it drooping onto the forward / reverse lever.
Step 7:
All that's left to do is to fit the readout box into the box I made and to wire up all the connections.
The electrical diagram I've included is available online if you search for it. I found it easier to follow than the instructions that came with the kit.
As you can see I have just used simple screw down connectors for the wires (I did solder all the lead ends before inserting then into the connectors)
And that's it.
One last note: I have not glued the conduit connectors together. They fit pretty tight and I can adjust the angle of the display to what suits me. I may still glue these joints at a later date.
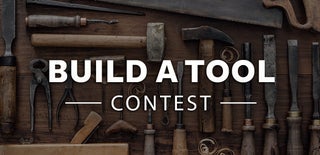
Participated in the
Build a Tool Contest