Introduction: Anodized Aluminium Nozzle With Build in Heater, Ultra Fast and Slim
Update 16/06/2015: Up to 100mm/s now :)
Update 13/07/2015: First print test with up to 80mm/s using the 0.3mm nozzle. Check step 5 for the videos.
Update 12/06/2015: New parts arrived so I made a new heater with a screw in nozzle and added a heat break. (Step 2 has the images)
Update 09/07/2015: Printing ABS...Could not wait for the new parts to arrive so I made a new teflon holder for the current nozzle and started a testprint with ABS, to be found after the upload in the video step.
Update 07/06/2015: After breaking two of these tiny and expensive 0.3 and 0.4mm drill bits I decided to give up on drilling them.
Instead I will order some srew in nozzle tips and re-design the heater to take them instead of having a tiny hole.
Will make replacement / change of size easier too as you only need to warm up the nozzle and unscrew the tip.
Principle of anodized amulinium for a direct core heating system will remain.
Next update once the nozzle tips arrived.
Update 06/06/2015 2.: And it truely does work! Video is ready, some more will follow soon, so check the step with the videos and fault analysis.
Update 06/06/2015: Uploaded an image of the first failed attempt, heat barrier failed but heater design is solid.
Meet the next generation of print nozzles - anodised aluminium!
From the main image you might think: Ok, it looks like a nozzle but where is the heater?
All common print heads have either a heating resistor or a heater cartridge - both require extra room inside the hotend.
By using anodised aluminium I am able to wrap the heating wire directly onto the nozzle as the oxide layer is a perfect isolator.
This is still a prototype but it is the 8th generation so far.
If you want to know more check the next steps.
Step 1: What You Will Need and How Machine the Nozzle
1. Access to a lathe.
2. A regulated DC power supply, best a lab power supply.
3. Sodium Hydroxide and Sulphuric Acid (Battery Acid).
4. Nichrome wire - I used 30 AWG for my nozzle.
5. Small crimps to connect the heating wire as it can't be soldered.
6. Heatsink Plaster - not the kind for your CPU, but for GPU and Northbridge, I used silcone based heatsink paste rated for 300° Celsius.
7. Temp sensor of your choice - in my case the standard type for my old Mendel, please select according to your hardware.
8. Depending on the capabilities of the lathe you will need a drillpress as well.
9. M6 stainless steel screw and suitable tap - you can substitude for imperial sizes if the printer is not metric.
If you are not comfortable by drilling into stainless steel on you lathe check for already drilled "heat barriers" or screws at your favourite printer supply store.
10. A bit of Telfon or PEEK rod.
11. Kapton tape.
Let's start with the material:
I used 8mm round bar from the home depot - not the best choice but more about in the anodising part.
I cleaned it up on the outside to make it round instead of bumpy the way it came.
Next step is to drill the nozzle hole for the filament.
For your first try stick to the bigger sizes, like 0.7mm, I used a 0.4mm hole for this model.
To keep the drill alive I glued it an old pen and used it by hand, these tiny drills are expensive and fragile...
For better print quality the nozzle is turned down at a slight angle so that only a tiny amount of material is left around the drilled hole.
Creating a thread for the heating wire.
I used a counter clockwise thread but the direction does not matter.
What does matter is that you need 12-14 turns so the wire is in the right range.
10 or less turns only if your hardware is capable of using less than 8Ohm heatng elements without going up in smoke.
16 turns if the lenghts does not matter too much and you want to save some energy. - The heating wire will still work fine with 16 turns.
So you see there is enough room to play so it is very hard to mess it up.
Please keep in mind 30AWG wire was used - if you use a different diameter you have to double check the resistance before with the number of turns to get it right.
I left just enough material to fit the thermistor right at the nozzle output.
Inside magic...
For 3mm filament I drilled a 3.5mm hole all the way down so there is as little material as possible left between this heating chamber and the outer nozzle hole.
The longer the nozzle hole the more pressure is required to push the filament through.
For 1,75mm filamet drill a 2mm hole here.
Next is a 5mm hole about 8mm deep.
This hole is now tapped with a M6 thread.
If you have a tap with a flat bottom it would be perfect as there will be no 5mm section left before the heating chamber.
If not just keep reading as we will sustitude.
Last but not least the hole for the thermistor is drilled - care must be taken not to drill too deep.
If you drilled too deep with the 3.5mm drill you will notice a hole in the hole, if so then I am sorry but you have to start over and leave a tiny bit more material when using the 3.5mm drill.
With the angle of the drill bit it should be a tight fit for the 2mm thermistor hole but it will fit.
It is drilled just deep enough so the glass body will sit flush with the outer diameter.
That is all for the machining on the actual nozzle.
For the connection to the mounting part I use a 6mm stainless steel bolt.
The stainless steel bolt has the head cut off and a 3.5mm hole drilled through.
It it best to remove the thread on one end if your can not tap all the way to the 3.5mm hole inside the nozzle.
This way you can bridge the big gap left from the tapping (unless you have a flat cutter).
To assist with a good seal and to keep the molten filament in the melting chamber I also made a Teflon washer to go between bolt and inner hole of the nozzle.
Sorry no pic here, just a 2mm thick washer with a 3.2mm hole for the filament.
If you want a universal nozzle for both filament sizes you can still use a bolt with 3.5mm hole but make the Teflon washer with a 2mm hole and a slight funnel shape on the top to aid the filament getting in.
You can also get bolts with a slightly larger hole that allows to use Teflon sleeves of different sizes to cater for the 1.75 and 3mm filaments.
The options here are all yours ;)
Update 12/ß6/2015:
If you can't drill these tiny holes use my updated design as shown in the images below.
In the above pic you can see the new hotend mounted with a GPU cooler from an old graphics card - had no thick aluminium rods at hand to make a proper one ;)
Now the parts seperated:
The Teflon mount is a bit longer as my x carrier is a weird design and I needed some clearance for the heat break as well.
The stainless steel screw is now drilled open to 4mm so a Teflon tube can be used to reduce friction.
The heater design is basically identical to the old one only that it has a tapped hole for the screw in nozzle.
To get better temperature readings the hole for the heat sensor is drilled a bit into the thread of the nozzle.
Will upload some pic of that if required but I think it is pretty clrea anyway.
Tomorrow I will do the elcetrical connections and try a test print.
We are done with the hard work, let's continue with the anodising...
Step 2: Anodizing the Nozzle
There are Instructables about anodizing out there, so I will keep it short here.
The nozzle is first cleaned with acetone or alcohol to remove any remaining oil and fingerprints.
Now we use about 2 teespoons of Sodium Hydroxide in a glass to remove any oxides that have formed as well remaining fingerprints.
From now on gloves on or use use tools to handle the nozzle but not your bare fingers.
The anodizing takes place in a small container with diluted batterry acid.
If you dilute acids always add the acid to the water never the other way around!
For this small piece I set the current to 60mA @ 16V for the first 10 minutes, then down to 20mA for 90 minutes.
After a good rinse under water time to give it some color.
I wanted a copper tone but it turned out my combination of cheap aluminium and food coloring was no good.
Previously I used high quality aluminium with a good hardness and it colored really well using green food coloring.
Anyway you might see the slight gey of the oxide layer in the picture, the color complete dripped off during the sealing process.
But a quick check with the multimeter confirmed that there is no conductivity, just to double check if the anodizing worked as planned :)
Not that the color would really matter anyway as you won't see much of it in the finnished product, so you can skip the coloring if you don't care.
Most food colors won't survive the heat so if you really want a fancy looking hotend you have to use proper anodizing colors.
To seal the oxide layer I boiled in water for 40 minutes.
Step 3: Why Using This Way to Make a Hotend?
Mainly because of the size and low weight.
A nice side effect is that this nozzle goes from room temperature to 200° in a few seconds, while normal hotends can take a few minutes.
Most people know anodised aluminium from colored tools, drink bottles or outdoor equippment.
A little known fact is that the oxide layer, which is the bit that can take the color, is also a really good insulator.
I combine weight reduction with even faster response times.
Step 4: Adding the Nichrome Wire and Thermistor
Now comes the fun part of getting the wire properly onto the threaded bit of the nozzle.
For me it works best to just warp it with a lot of tension directly into the grooves.
If you still have too much flex and it unwrapped you wrap onto a lightly smaller diameter first and push the windings onto the nozzle.
I secured the ends with rubber bands once all was in place.
To keep it in place and to give a better heat distribution we now fill all the groove in the thread with the heatsink plaster till even with the high bits.
Leave enough time so the silicone will fully cure, rushing here is a bad idea!
Once the silicone is cured small crimp connectors are used to attach the wires to the harness.
Soldering won't work!
I subsituted with some copper tubing from an old fridge, it is used for the thermostat connection and just right after drilling the inner hole out a bit.
Small crimp connectores as used for the header for circuit board connectors work best but I ran out :(
With them you simply cut off all that is not being crimped and keep the rest for the connection.
The wire closest to the nozzle outlet will be bend 90° up to be joined near the top wire end or directly at the bottom.
I crimped at the bottom here...
To ensure there won't be any short if a loop of the wire gets loose somehow a few layers of Kapton tape are wrapped around the nozzle, then the wire is put up and again secured with a few layers of Kapton tape.
If you prefer you can use telfon tape from the plumbing section to substitute here and only use the Kapton tape for the finnish when the thermistor wires are added.
Time to do a final resistance check make sure we neither have a short, nor a broken wire.
The thermistor is glued in with the heat sink plaster and secured with a bit of Kapton tape.
Once the plaster is fully cured the entire nozzle is wrapped tightly with several layers of Katon tape - this gives us some added insulation.
I only have an old Prusa, so the the final nozzle will be based on that design.
If your nozzle holder differs simply match your system at the end of the stainless steel bolt. The Instructable is about the actual hotend not the mount for the printer. You can use Teflon PEEK or aluminium for the mount to your X axis carrier / extruder.
I had the Teflon at hand so there is the 6mm thread and the 3.5mm hole throughout together with a standard J-head mount.
For size comaparison I added the standrad J-head in this picture.
The big washers are a test fo a simple heat sink as I want to try to print some nylon wth this head.
The thermistor is glues in as well and all is ready to be soldered to the connecting wires.
Still waiting for new wiring harnesses to arrive, but as soon as they do the nozzle will get a testrun and I will upload a video of it as well.
On earlier models I also substituted the Kapton insulation with a tube of aluminium.
It looks nicer but requires additional steps for the machining and it takes several days for the heatsink plaster to cure in the enclosure so I abandoned that design for now.
There was no noticable gain in performance with the extra aluminium mantle and it just does not justify the extra work if you only have a small tool shed.
I hope you like the idea and try it out one day.
If you do please post some pictures.
Step 5: Images and Videos
Well, the first the first testrun was not as good as expected.
After just about 10cm of printing the extruder started to make grinding noises due to the pressure.
Turned out the nozzle and heater system worked quite well, just not the short stainless steel bolt as a heatsink.
The teflon washer I put between bolt and nozzle expanded as well and the filament made it's way up the bolt as you can see it even formed a good thread inside the teflon holder.
Will have to get some PEEK or a thicker bolt with a Teflon liner to prevent the jamming.
If I find the parts I will fix the bolt and liner problem and hopefully can do a successfull print in a few days.
The heater itself performed quite well and till the jam the nozzle extruded quite fine too.
Sadly I have no thick alu stock to make a proper sized finned heatsink, but maybe I can find a small CPU cooler to substitute.
Here is a short video showing that extruding by hand works quite well using a teflon connection:
Here is one showing the extrusion at 60mm/s in the printer for a testrun.
Mind you I did use the wrong drill and it is a 0.7mm hole and not 0.4mm as stated on the previous steps.
Extrusion test at 60mm/s in the printer:
PID autotune as a showoff for the heating speed.
If you find a nozzle with under 20W of heating power that is faster let me know ;)
Last but not least a final and short print test.
As expected the thin Teflon connection is too flexible and ruins the print by making the nozzle wobble around.
But it still prooves the concept is working fine, will have to make a solid mount with Teflon until I get my hand on some PEEK for higher temperatures.
I might actually make another nozzel but with a longer "neck" and an 8mm outside thread that screws directly into the holder.
16mm Telfon rod will still have some flex but should be good enough for some decent prints.
Already ordered some polished stainless steel heat barriers as I can not properly polish mine, if this works ok I will update accordingly.
09/07/2015:
Printing ABS works really well, although the nozzle holder (teflon) becomes soft after a while causing the nozzle to wobble.
But with the new parts this will be fixed for good hopefully.
13/06/2105: Extrusion test of my hotend with a 0.3mm nozzle:
After quite a few operator melt downs during the bed calibration I finally managed to do a first print with the 0.3mm nozzle:
It was not mentioned on the sellers website but the green filament is extremly UV reactive and messed with the light of the cam.
Might be nice for some fishing lures ;)
Printing was done at 40mm/s with 0.1mm layer height.
Corners never looked better but calibrating everything for such a small nozzle is a real pain...
Here the same but a bit later in the print with 20% more speed:
Last for tonight, printing at 80mm/s only slowed through the acceleration control.
Not sure what others think but I am quite impressed with this new design.
Will make the holder shorter once the PEEK arrives to gain a few cm more build height.
Update 16/06/2015: Printing with 100mm/s...
The result is not 100% perfect and still needs some finetuning for the filament settings as the infill is still a bit too much, same for the outer perimiters.
But I think with proper settings 120mm/s should be no problem.
Speed settings used in Slic3r for the tokens:
Perimeters = 100mm/s
Small perimeters = 40mm/s
External perimeters = 50mm/s
Infill = 120mm/s
Solid infill = 40mm/s
Top Solid infill = 20mm/s
Bridges = 30mm/s
Gap fill = 20mm/s
Mind you the hardware is Gen1 Mendel Prusa and nothing fancy...
The finetuning for 0.3mm nozzles is just a pain, there is no real margin for error anymore.
What works with a lot of different filament and extrusion settings on a 0.7mm nozzle needs perfect tuning.
I will keep tuning to reach my 120mm/s goal for perimeters and infill.
Already this nozzle prints faster than any of my J-heads ever did :)
Since speed is better observed on big objects, printing a Wades extruder at 100mm/sec:
Cranked it up to 120mm/s and even higher but now my hardware is maxed out LOL
Had several freezing of the printer at speeds around the 200 mark, so either improving the hardware or settling for speeds around 150mm/s.
In any case for the cost of under 20 bucks in parts not a bad result at all.
Step 6: Fault Analysis and Improvements
06/06/2015:
As I had earlier and much bulkier versions of this nozzle working fine I was starting to wonder where the problem might be.
After the extrusion failure I decided to spend another hour in the workshop making a new stainless steel bolt with a 3.1mm hole this time. Instead of doing a full test inside the printer I did a test by hand and was surprised how easy I could push the filament through, creating a nice stream of molten plastic. However, when I stopped for a few seconds to get a better grip I could not push any filament through at all. A quick check revealed the filament expands inside the stainless steel "heat barrier", especially once the entire system warmed up fully. In my first attempts of making a nozzle using anodised aluminium I used an outside thread on the nozzle and it was mounted directly into a Telfon piece for mounting. There was little to no friction at all and no expansion either. But my aim here is to make a nozzle that is slim, easy to make and can perform above the 300° C range. So far the only thing really stopping this is the connection between the actual nozzle and the mount. Here in AU I have massive troubles finding PEEK rods at a reasonable price, 80$ for 30cm is "cheap", this rules out making a high temp version using PEEK at this stage. However, with an outside thread of 8mm and directly mounted into a Teflon mount it is working great for PLA, ABS should work too but Teflon already starts to soften at these temps.
Far from optimal but with only very little friction, graphite is the only thing I have left to try until I find a find some cheap PEEK or make a new nozzle with outside thread. So off to the workshop to make a graphit connector and hoping the best it will be strong enough to at least survive one decent print.
06/062015 2.:
Graphite turned out to be a nighmare on the lathe and was far too soft and brittle.
But getting desperate to show it really does work I made a new "heat barrier", this time from Teflon - just for testing purposes!
And as the video showed, it really does work well, but it also showed someone was not careful when grabbing the tiny drill - the hole is actually 0.7mm and not 0.4mm :(
Anyway, it works and in a few days I will make a more permanent solution by making just a single Teflon mount that holds the nozzle directly.
Won't be good for really temps, but the main thing is the nozzle works, making a stainless steel heat barrier with a teflon liner will be the next step.
I will now try to mount the nozzle in the printer and do a test print.
It it holds up the result won't be perfect as the thin teflon rod is very soft, but let's see how we go :)
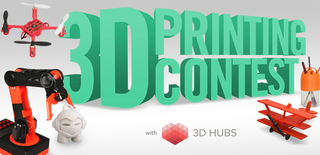
Participated in the
3D Printing Contest