Introduction: Apprentice Maze Puzzle Box
I love puzzle boxes and I wanted to design my own puzzle box since I started with laser cutting. I am not exaggerating when I tell you that I have a list with a few dozen ideas for all kinds of puzzle boxes with various mechanisms. But I learned in the past the hard way that it is generally a good idea to start simple when doing something for the first time. So I resisted the urge to design a really cool, complicated mechanism and settled on something simple yet elegant (at least I hope that is what it will be…). I will call it the “Apprentice Maze Puzzle Box”.
Step 1: Material and Tools
Material:
- 3 mm Birch Plywood
- Sandpaper (180/320 grit)
- Black paint (I used milk paint)
- Wood Glue
Tools:
- Laser Cutter
- Orbital Sander (optional, the sanding can also be done by hand)
Step 2: Concept
The difficulty of this puzzle box will be fairly easy. I probably would rate it a 3-4 on a scale from 0 to 10. If you don’t want to know exactly how to open the box, don’t read the following paragraph or watch the video. But if you read through the instructions and build the box, it will be pretty obvious anyway…
How to open the Maze Box
As the name suggests, the main element to open the box will be a maze located on the top of the box. The maze can be rotated and there is a little pin inside the maze. The pin can be moved with the help of a slider on the front of the box. By rotating the maze and moving the slider, the pin can be navigated through the maze. Once the pin is in the center of the maze, two circles on the left and right side of the box are free to move. One circle has to be moved back and the other one forward. This unlocks the top lid and the box can be opened.
Step 3: Modeling the Mechanism in 3D
After I sketched out some ideas for the locking mechanism on paper, I used Fusion 360 to create a complete 3D model of the puzzle box. This allowed me to test if all the interactions were working as planned and make adjustments in case they did not.
Each part that will be cut on the laser is modeled as a separate component. Once, I had all the parts modeled and was happy with the design, I copied all components and laid them out flat using a planar joint. Then I used the CAM module in Fusion to create the paths for cutting and exported them. Using the CAM module has the big advantage that the kerf compensation will be automatically done, one just has to choose the right value for the kerf. For more details about the workflow, have a look at this video: Fusion360: DXF export with kerf compensation for laser cutting
Below you can download the cutting template as PDF or SVG:
Download – Apprentice Maze Puzzle Box PDF
Download – Apprentice Maze Puzzle Box SVG
NOTE: The locking mechanism requires tight tolerances to work smoothly. Therefore it is important to consider the kerf width when cutting. By testing different settings I found that a kerf compensation of 0.1 mm worked best for me (and this is included in the templates). But this depends on the type of laser machine and material you are using. I recommend adjusting to your kerf width before cutting for the best results.
Step 4: Preparation of the Material
Currently, my favorite workflow is to sand the top and bottom surface of the wood and add masking tape before the laser cutting. Sanding the complete panel in one go is much quicker than sanding the individual parts afterward. I also find that the masking tape holds on better to the wood when the surface is smoother. Just make sure to get rid of all the sanding dust before the masking.
Step 5: Laser Cutting and Engraving
I cut everything on a Trotec Speedy laser cutter at my local makerspace. On two parts I used engravings to exactly mark the position of other parts that will be glued on top.
Step 6: Sanding, Staining and Oiling the Wood
I do not like the look of laser burnt edges on boxes, so I designed all the finger joints of the box to be 0.3 mm (0.01 in) longer than necessary to have excess material that can be sanded away. As I already sanded the wood surface before laser cutting, there was not much additional sanding needed there. I just did a final light sanding with 320 grit and then proceeded with staining and oiling. On all the parts that will not be stained, I applied a coat of linseed oil.
I used milk paint for the black parts. It was my first time using milk paint and overall I really liked it. It gives very good coverage and is easy to apply. One thing I did not consider though is that the milk paint needs to be sealed because otherwise it will rub off from the moving parts and stain the parts it is in contact with. Luckily I had some clear spray lacquer at home and two thin coats fixed the problem.
Step 7: Assembling the Box Lid
Below you find a short description of the assembly steps. Please also refer to the pictures in the image slider to see which parts are needed for each step and where they need to go. The complete part overview and all the assembly drawings are included as a PDF document when you download the cut template above.
- Glue the maze (M_AZ) and the ring with the small cutout (M_RI) together. Make sure that the cutout on the ring and on the maze align.
- Glue the four wall parts (L_FR, 2 x L_SI, and L_BA) and the top of the lid (L_TO) together.
- Glue the four distance holder parts (L_DI) to the side walls with the circular holes.
- Place maze and check if it rotates freely (sand the hole if it doesn’t). Next, combine the parts L_AF and L_MG as shown in the drawing. Glue the parts L_AF and L_MG to the lid using the maze as a guide for placement. Make sure that the maze is still rotating freely.
Step 8: Assembling the Lock Mechanism
After completing the lid, continue with the lock mechanism. All the moving parts of the mechanism are held in place with the help of wedges. This way it is easy to fine-tune all moving parts if necessary.
5. Glue the two MB_G parts onto the maze backplate (MB_P) using the engraving as a guide. Then place them on top of the maze. Next place the slider guide (S_GU).
6. To make the two sliders which are locking the to box, glue parts LS_P, LS_CO and LS_A together as shown in the drawing.
7. Place the two lock sliders so that part LS_A is in the rectangular cutout of the slider guide (S_GU).
8. Make sure the lock sliders are moved all the way outward (in the “locked” position”) and then glue the circles (LS_CI) centrally on the slider plates (LS_P)
9. Next, assemble the maze slider. Glue the parts MS_BR, MS_T, MS_BO, and MS_PL together. After the glue has dried for these parts, glue the two small pins (MS_PI) together and then on part MS_T. Use the engravings for placement.
10. Place the maze slider in the slider guide. The pin should be in the center of the maze.
11.Add the locking plate (L_LP) on top and fasten everything using the two wedges (L_WE)
When you have completed the assembly of the mechanism, you should test if all sliders move easily. All the moving parts of the mechanism are held in place with the help of wedges. This way it is easy to fine-tune all moving parts. Originally the tolerances on the maze slider were a bit too tight and I had to sand down the edges for smooth movement. I corrected this in the downloadable template so only small adjustments should be necessary.
Step 9: Making the Bottom Box
The last steps are to make the bottom box.
12. Glue the four wall parts (2 x B_FB and 2 x B_SI) and the bottom of the box (B_BO) together.
13. As the final step glue the four inside walls (2 x B_IF and 2 x B_IS) in.
Step 10: Putting It All Together
The only thing left to do now is to close the box. To do this make sure that the maze pin is in the middle of the maze and the lock sliders are in the “unlocked” position (pushed outwards). After putting the lid on you can move the two lock sliders on the sides to lock the box and then navigate the pin in the maze all the way outwards.
Now the maze puzzle box is ready to be given away to somebody to figure out its secret!
If you make your own box following this tutorial I would love to hear from you! :-)
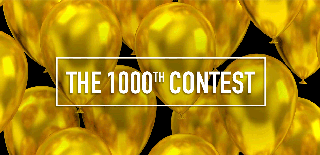
Participated in the
1000th Contest