Introduction: How to Make Wooden Clamps From Scraps
When I am working on projects I notice two things regularly. First, it is very hard for me to throw away scrap wood. I tend to keep thinking that there will be some future use even for small bits of material and store them roughly sorted by type and size in different containers. I have to confess I sometimes even "rescue" scraps of material out of the trash bins from the shared makerspace where I use the laser cutter.
Second, while I am in the middle of some glue-up I often wish for an extra pair of hands. I have a collection of bar clamps in different sizes but I often find even the smaller ones to be too big and bulky. I have also used painters tape to hold parts in place but this does not work well for situations where a bit more force is needed.
So with this project, I am going to tackle both issues in one go! I will make small wooden spring clamps out of scraps.
Step 1: Material and Tools
Material:
- Wood scraps
- Old bike tube or rubber bands
- Sandpaper
- Wood Glue
Tools:
- Laser Cutter, Scroll Saw or Fret Saw
- Knife or Scissors
Step 2: Designing the Spring Clamps
I used this Thingiverse Project as a basis for the clamps but basically re-designed everything from scratch. There were two main reasons for this:
When I tried to open the DXF file from Thingiverse in Inkscape or Illustrator some of the curves turned into straight line segments and some just looked weird.I wanted to make my clamps with rotating jaw pads instead of fixed ones to distribute the grip force over a larger area.
By the way - I was not sure if "Spring Clamp" is actually the right term to describe this style of clamp but as technically a rubber band is a tension spring where energy is stored by stretching the material (I was not sure about this - but I looked it up on Wikipedia...) this should be correct.
Below you can download my final cut files:
Step 3: Cutting and Assembling
I cut all the parts on a laser cutter at my local maker space. Each clamp is made out of twelve parts: three parts each for the left and right main body of the clamp and three parts each for the jaw pads.
After sorting the parts, the first thing I did was to lightly sand the top of the two middle parts for the main body on both sides. There is not much sanding required. The idea behind this is to just remove a little bit of material so that the jaw pads can rotate freely.
Next, I glued the main body parts together. While the glue was drying I turned to the jaw pads. For each side, I glued the bottom part and the middle part together. As the middle jaw part is quite small it is a bit fiddly to align it correctly with the bottom part.
With this done, the jaw pad part can now be joined with the clamp base. I found that it makes a difference from which side you insert the jaw pad. So try both and use the one that rotates easier.
When gluing the final piece of the jaw pad, be extra careful to avoid excessive glue and make sure that the jaw pad can turn freely in both directions.
Now that both clamp halves are ready, the only thing left to do is to join the two and add the rubber bands. For the rubber bands, I used an old inner tube from a bike tire which I cut in strips about 3 mm ( 1/8 in) wide.
The resulting rubber bands are pretty strong and more durable than regular rubber bands in my experience. In addition, it's a nice way to upcycle the tube instead of just throwing it into the trash bin. You can control the clamping power by the number of rubber bands used.
Step 4: Using Clamps to Make Even More Clamps
Once the first clamp is assembled it can be used to make even more wooden clamps!
The clamps work great for light-duty clamping and for small parts. I now use them regularly when gluing multiple layers together.
I am not 100 percent happy with the rotating jaw pads. They work okay but the tolerances are quite tight and they sometimes can get a bit stuck. I might redesign them for a future version. If anyone has ideas for a design improvement please let me know in the comments!
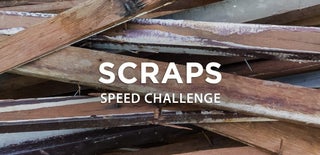
Second Prize in the
Scraps Speed Challenge