Introduction: Aqua Casting Silver for Jewelry
Hello there everyone!
Today I'm going to give you a spiel I call:
Aqua casting Silver For Jewelry101
This method produces a variety of naturally unique shapes one can use to make truly one of a kind Jewelry with!
I will walk you through the formative steps of making the base for such pieces of jewelry.
Supplies
- Safety Gear-
-Gloves, Leather is my go to, but good heat-resistant gloves are a must!
-Eye protection, better safe than sore-eye!
- A Crucible, I make my own but they can be purchased from pmcsupplies.com and other such metalworking retailers online.
- Crucible tongs: I, personally, used a pair of my more beat-up metalworking tweezers for this. Proper crucible tongs are a limb-saver, though.
-Borax ( 20 mule team can be found in the laundry aisle of most grocery stores.)
Borax will act as our flux and help get our scrap metal melting faster and pull out impurities.
- A metal container filled with water. ( I repurposed an old Cream pitcher. )
It does not necessarily HAVE to be metal, but glass and plastics are BAD.
-A Torch ( I'm using a Bernzomatic micro torch) -Butane for the torch
-A fire Proof surface ( I have a small set up with a Big Rock (tm) Elevated with a thick porcelain dish, and a repurposed metal Candy-dish filled with a mix of sand and clean, unscented, kitty litter to act as a heat sink.)
-A Graphite Rod
-A fire extinguisher A staple of any good Pyromaniac's workbench.
Step 1: Assemble Your Gear & Prep Your Work Area.
You will want to work in a well ventilated area. This cannot be stressed enough.
This can be accomplished by working near-to an open window, having an established fume hood, or a cheap electric box fan pointed toward an open window nearest to your work station as to suck air out the window.
Lay out your heat-resistant surface of choice:
My set up is very small and "pretty redneck" and employs the use of a repurposed candy-dish, a large flat river stone, sand & kitty litter... Yup, Kitty litter. Unscented.
An ideal set-up would involve fire bricks, a ceramic soldering board and/or a Honey Comb board. These are easy enough to obtain from sites such as Riogrande.com or pmcsupplies.com.
Be sure you have a Fire Extinguisher near by.
You want your work area to be devoid of anything that doesn't have to do with your current task.
Put on your safety gear ( glasses/goggles, Gloves &/or a dust mask/respirator. Denim or Leather Apron for bonus points in safety.)
~ A word about Heat Sinks.~
I had assembled my work area working on minimal space, so the action is happening on an elevated metal candy dish I repurposed and filled with a mix of clean, unscented kitty litter and pre-washed playground sand to act as a heat sink.
A good heat-sink takes a lot of the guesswork out of accidentally pointing the business end of the torch at my more flammable than I'd prefer desk.
It's a weird set up and not preferred, or practical, but it's proven it's self to be safe enough in my time soldering things as the sand evenly distributes any overflow heat & the dish it's self doesn't get hot enough to burn my desk.
Kitty litter is mostly if not completely made of Clay, which doesn't make too bad of a heat sink it's self in this pebbly form.
Step 2: Assemble Your Scrap Metal & Borax It Up.
In this fashion, you can melt down Silver, Gold, Copper and a handful of other metals.
In my crucible I started off with a little bit of my scrap silver, adding a pinch of Borax before I took the torch to it.
You want to start with clean metal free of patina, enamel, gemstones & etc otherwise there will be fumes, exploding gemstone bits & your metal will be more difficult to melt.
Borax will help strip some patina & oil from being handled. It acts as a flux & makes things melt a little quicker.
When heat hits the Borax it's going to puff up like Styrofoam and may or may not float out of the crucible.
This is what your dust mask/respirator is for, among other things.
Step 3: Getting to "Liquidus Temperature"
Keep your heat on your scrap bits, adjusting if/when necessary and adding Borax if/when you find it necessary.
I would start with a smaller lump of molten metal and progressively sprinkle more scrap in until the lump was the size I felt I wanted it to be.
....and now we wait.
The process can take 10 to 15 minutes & depending on how high your torch is set, you may or may not need to take a break, let the torch cool off & refill it with butane.
This is perfectly fine, remember to add another little pinch of Borax to the partially cooled lump of metal before you resume, if this is the case.
You will know when you have reached "Liquidus Temperature" when the lump becomes a wet looking, glowing red blob & jiggles when disturbed, with no sharp points of un-melted scrap poking out of it when/ if stirred with a Graphite Rod or other means.
Step 4: Pour Your Blob.
Once you feel you have a reasonably wobbly blob, You are free to pour it into your quenching chamber.
I repurposed a metal Creamer and filled it with room-temperature water. Regular water, from the tap. Nothin' fancy.
I have in the past, improvised with ceramic mugs & they work just as well. NEVER use glass or plastics.
The water shouldn't ever flash-boil, thanks to our makeshift heat sink.
Experimenting with different temperatures wields different results.
It's going to make a bit of noise, such as bubbling, squeaking and high-pitched squeals. This is normal as the molten metal is being cooled at a quick rate.
The more you cast, however, the dirtier the water will get & the less pretty your end-blob will be, water needs to be changed periodically as our Borax flux will shed into it.
Be careful though! The quench pot'll still be hot to the touch even with a heat-sink in use!
Step 5: Let Cool and Admire Your Handywork.
It's never the same thing twice.
From here you can let your imagination soar & your logical thinking of form, structure and geometrics run wild.
Trapped air pockets make a great spot to set stones.
Natural holes to string a leather cord or a jump-ring through.
Hammer the boring round one into sheet metal....
Some might have to be melted down again and again before a certain shape just jumps out at you but...
The possibilities are endless!
Each one will be unique in and of it's self, just like the person reading this tutorial.
Step 6: Resources
For metal shot, casting supplies as well as higher-budget tutorials and written/video media on the subject of metal casting:
riogrande.com
pmcsupplies.com
kingsleynorth.com
For setting up a proper soldering / casting station
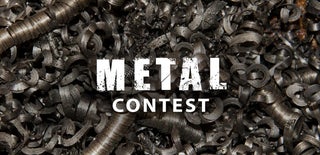
Participated in the
Metal Contest