Introduction: Arduino Waveform Generator
Feb. 2021 update: check out the new version with 300x the sampling rate, based on the Raspberry Pi Pico.
In the lab, one often needs a repetitive signal of a certain frequency, shape and amplitude. It may be to test an amplifier, check out a circuit, a component or an actuator. Powerful waveform generators are available commercially, but it is relatively easily to make a useful one yourself with an Arduino Uno or Arduino Nano, see for example:
https://www.instructables.com/id/Arduino-Waveform-...
https://www.instructables.com/id/10-Resister-Ardui...
Here is the description of another one with the following features:
* Accurate waveforms: 8-bit output using R2R DAC, 256-sample shape
* Fast: 381 kHz sampling rate
* Precise: 1mHz steps frequency range. As accurate as the Arduino crystal.
* Easy operation: waveform and frequency settable with single rotary encoder
* Wide range of amplitudes: millivolts to 20V
* 20 pre-defined waveforms. Straightforward to add more.
* Easy to make: Arduino Uno or Nano plus standard components
Step 1: Technical Considerations
Making an analog signal
One shortcoming of the Arduino Uno and Nano is that it does not have a digital-to-analog (DAC) converter, so it is not possible to make it output an analog voltage directly on the pins. One solution is the R2R ladder: 8 digital pins are connected to a resistor network so that 256 levels of output can be reached. Through direct port access, the Arduino can set 8 pins simultaneously with a single command. For the resistor network, 9 resistors with value R are needed and 8 with value 2R. I used 10kOhm as a value for R, that keeps the current from the pins to 0.5mA or less. I guess R=1kOhm could work as well, since the Arduino can easily deliver 5mA per pin, 40mA per port. It is important that the ratio between the R and the 2R resistors is really 2. That is most easily achieved by putting 2 resistors of value R in series, for a total of 25 resistors.
Phase accumulator
Generating a waveform then comes down to repetitively sending a sequence of 8-bit numbers to the Arduino pins. The waveform is stored in an array of 256 bytes and this array is sampled and sent to the pins. The frequency of the output signal is determined by how fast one advances through the array. A robust, precise and elegant way to do that is with a phase accumulator: a 32-bit number gets incremented at regular intervals, and we use the 8 most significant bits as the index of the array.
Fast sampling
Interrupts allow to sample at well-defined times, but the overhead of interrupts limit the sampling frequency to ~100kHz. An infinite loop to update the phase, sample the waveform and set the pins takes 42 clock cycles, thus achieving a sampling rate of 16MHz/42=381kHz. Rotating or pushing the rotary encoder causes a pin change and an interrupt that gets out of the loop to change the setting (waveform or frequency). At this stage the 256 numbers in the array are recalculated so that no actual calculations of the waveform need to be performed in the main loop. The absolute maximum frequency that can be generated is 190kHz (half of the sampling rate) but then there are only two samples per period, so not much control of the shape. The interface thus doesn't allow to set the frequency above 100kHz. At 50kHz, there are 7-8 samples per period and at 1.5 kHz and below all 256 numbers stored in the array get sampled each period. For waveforms where the signal changes smoothly, for example the sine wave, skipping samples is no problem. But for waveforms with narrow spikes, for example a square wave with a small duty cycle, there is the danger that for frequencies above 1.5 kHz missing a single sample can result in a the waveform not behaving as expected
Accuracy of the frequency
The number by which the phase is incremented at each sample is proportional to the frequency. The frequency can thus be set to an accuracy of 381kHz/2^32=0.089mHz. In practice such accuracy is hardly ever needed, so the interface limits to set the frequency in steps of 1mHz. The absolute precision of the frequency is determined by the precision of the Arduino clock frequency. This depends on the Arduino type but most specify a frequency of 16.000MHz, so a precision of ~10^-4. The code allows to modify the ratio of the frequency and the phase increment to correct for small deviations of the 16MHz assumption.
Buffering and amplification
The resistor network has a high output impedance, so its output voltage quickly drops if a load is attached. That can be solved by buffering or amplifying the output. Here, the buffering and amplification is done with an opamp. I used the LM358 because I had some. It is a slow opamp (slew rate 0.5V per microsecond) so at high frequency and high amplitude the signal gets distorted. A good thing is that it can handle voltages very close to 0V. The output voltage is however limited to ~2V below the rail, so using +5V power limits the output voltage to 3V. Step-up modules are compact and cheap. Feeding +20V to the opamp, it can generate signals with voltage up to 18V. (NB, the schematic says LTC3105 because that was the only step-up I found in Fritzing. In reality I used an MT3608 module, see pictures in the next steps). I choose to apply a variable attenuation to the output of the R2R DAC then use one of the opamps to buffer the signal without amplification and the other to amplify by 5.7, so that the signal can reach a maximum output of about 20V. The output current is rather limited, ~10mA, so a stronger amplifier may be needed if the signal is to drive a large speaker or electromagnet.
Step 2: Required Components
For the core waveform generator
Arduino Uno or Nano
16x2 LCD display + 20kOhm trimmer and 100Ohm series resistor for backlight
5-pin rotary encoder (with integrated pushbutton)
25 resistors of 10kOhm
For the buffer/amplifier
LM358 or other dual opamp
step-up module based on the MT3608
50kOhm variable resistor
10kOhm resistor
47kOhm resistor
1muF capacitor
Step 3: Construction
I soldered everything on a 7x9cm prototype board, as shown in the picture. Since it got a bit messy with all the wires I tried to colour the leads that carry positive voltage red and those that carry ground black.
The encoder I used has 5 pins, 3 on one side, 2 on the other side. The side with 3 pins is the actual encoder, the side with 2 pins is the integrated pushbutton. On the 3-pin side, the central pin should be connected to ground, the other two pins to D10 and D11. On the 2-pin side, one pin should be connected to ground and the other to D12.
It's the ugliest thing I've ever made but it works. It'd be nice to put in an enclosure, but for now the extra work and cost doesn't really justify it. The Nano and the display are attached with pin-headers. I wouldn't do that again if I'd build a new one. I did not put connectors on the board to pick up the signals. Instead, I pick them up with crocodile leads from protruding pieces of copper wire, labelled as follows:
R - raw signal from the R2R DAC
B - buffered signal
A - amplified signal
T - timer signal from pin 9
G - ground
+ - positive 'high' voltage from the step-up module
Step 4: The Code
The code, an Arduino sketch, is attached and should be uploaded to the Arduino.
20 waveforms have been pre-defined. It should be straightforward to add any other wave. Note that the random waves fill up the 256-value array with random values, but the same pattern gets repeated every period. True random signals sound like noise, but this waveform sounds much more like a whistle.
The code sets a 1kHz signal on pin D9 with TIMER1. This is useful to check the timing of the analog signal. That is how I figured out that the number of clock cycles is 42: If I assume either 41 or 43, and generate a 1kHz signal, it clearly has a different frequency from the signal on pin D9. With the value 42 they match perfectly.
Normally, the Arduino interrupts every millisecond to keep track of time with the millis() function. This would disturb the accurate signal generation, so the particular interrupt is disabled.
The compiler says: "Sketch uses 7254 bytes (23%) of program storage space. Maximum is 30720 bytes. Global variables use 483 bytes (23%) of dynamic memory, leaving 1565 bytes for local variables. Maximum is 2048 bytes." So there is ample space for more sophisticated code. Beware that you may have to choose "ATmega328P (old bootloader)" to upload successfully to the Nano.
Attachments
Step 5: Usage
The signal generator can be powered simply through the mini-USB cable of the Arduino Nano. It is best done with a power bank, so that there is no accidental ground loop with the apparatus that it may be connected with.
When switched on it will generate a 100Hz sine wave. By rotating the knob, one of the other 20 wave types can be chosen. By rotating while pushed, the cursor can be set to any of the digits of the frequency, which can then be changed to the desired value.
The amplitude can be regulated with the potentiometer and either the buffered or the amplified signal can be used.
It is really helpful to use an oscilloscope to check the signal amplitude, in particular when the signal supplies current to another device. If too much current is drawn, the signal will clip and the signal is heavily distorted
For very low frequencies, the output can be visualised with an LED in series with a 10kOhm resistor. Audio frequencies can be heard with a speaker. Make sure to set the signal very small ~0.5V, otherwise the current gets too high and the signal starts clipping.
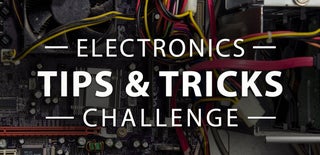
Participated in the
Electronics Tips & Tricks Challenge