Introduction: Backyard Teak Bar Top
My goodness is it ever hot this summer in North Texas. Luckily my brother and his wife have decided to install a pool and outdoor kitchen at their house this year. The original plan was to have granite counter tops and a granite bar top. Really pretty but the way all of the dimensions worked out it ended up that they would have a lot of (very expensive) left over material if they wanted the bar top to be granite. So a couple months ago I get a text from my brother...
Brother: How wide of a board can your surface planer take?
Me: 12 inches... what's up?
Brother: Need you to build a bar top for the outdoor kitchen.
Me: LOL, ok. Sure, we can figure something out for that.
And with that we have the start of another woodworking project! Oh... and hey... Instructables has another Backyard Contest going on as well! Woooooo Hoooooo!!! Project time!
Supplies
I have a fairly extensive assortment of power tools that make the job so much easier. Table saw, router table, compound miter saw, random orbital sander, surface planer, as well as a multitude of various types of clamps. I also used a few hand tools like chisels, Xacto knife, bubble level, wooden stir sticks, hammer, scissors, etc. And I absolutely love my Husky work table. The top is dead flat and you can adjust the table top up or down as required. I used West System epoxy for the majority of the glue up but we also used some Titebond for the trim pieces. Loctite construction adhesive bonded the bar top to the substrate. Helmsman by Minwax finished the project to give it a nice weatherproof shine. We selected teak wood for its weather resistant and rot resistant properties. I had not ever worked with teak before and it turned out to be wonderful wood to work with and it is absolutely gorgeous.
Step 1: Taking Measurements and Creating a Design
First step was to measure the bar top substrate and make a sketch to work to. There was a support post and a rain gutter downspout that we had to work around. The post and downspout kind of complicated the design. But accurate measurements helped to make it all workable. Once the measurements were made I drew up a full scale drawing using AutoCAD. I've included a PDF file of the image for reference. Each part was drawn up in three dimensions and the entire bar top was assembled virtually. Wow... I avoided so many mistakes by building the bar top using AutoCAD. I also had a reference that I could use to provide all of the dimensions for every part. It took quite a bit of time to do the drawing but it was time well spent.
Attachments
Step 2: Dimensioning the Pieces
My brother had purchased 8 teak boards. They were a little under 6 inches wide, about 1 and a half inches thick, and around 6 feet 4 inches long. I went ahead and ran them through the surface planer to ensure they were all the same thickness. The design I came up with has a 2 inch overhang on the ends and backside of the bartop. We went with a 7 inch overhang on the front where the barstools would be. Overall length of the bar ended up being just under 12 feet and the width for most of it is 19 inches. The width was increased to nearly 22 inches on right end of the bar to accomodate the support post and downspout.
I used the two straightest boards to make the frame pieces and ripped them into thirds (first two pictures). Next I set up my compound miter saw to cut the cross pieces. I clamped on my try square to simplify making repeatable cuts (pictures 3, 4, and 5). I wanted the parts to overlap and interlock so a rabbet bit was installed in the router table and half lap joints were cut on both the frame and cross pieces. I figured this would give me stronger glue joints and overall make it easier to assemble and clamp. Once again the Husky adjustable work table was used as an outfeed table (last two pictures).
Step 3: Glue Up and Initial Sanding
For the adhesive I chose West System epoxy. The 105 resin, 206 slow hardener, and the 406 colloidal silica. It's best to also buy the metering pumps to ensure you are getting the proper mix ratios of hardener and resin. The colloidal silica is a thickening agent. Once the resin and hardener are mixed you add the colloidal silica and mix it in until you achieve the consistency you want. This keeps the epoxy from running out of the joints and does a great job at gap filling. With no colloidal silica in the mix the consistency is kind of like maple syrup. I added enough to end up with something around the consistency of ketchup. Other applicatons call for a really thick consistency (like peanut butter) but that's not what I needed here. One thing about epoxy is that the cure rate is highly dependant on temperature. The warmer it is then the faster it cures. That was kind of tough in the summer Texas heat where the garage is over 100 degrees F. So I kept the epoxy in the house to keep it cool in order to achieve longer work times. Bottom line... this stuff is pain in the backside to use but it is an awesome adhesive and you get great results. It is crazy strong, waterproof, has good gap filling properties, and more than adequate work time.
In the first picture I started the glue up process at the easy end of the assembly (opposite the side with the support post and downspout cutout). Pretty darned good result on the mitered corner (picture 2). In the third shot you see my standard clamping strategy... a couple of pipe clamps and bar clamps. Oh... I also need to mention that I masked all the areas that I wanted to keep clean with clear packing tape. Epoxy is a mess to work with and I always manage to get it everywhere. And like I always say... it's easier to peel off tape than to sand off glue.
In the fourth picture I'm playing around with different cross piece arrangements to end up with a pleasing grain pattern. And in the next shot I couldn't resist doing a fit check for a place setting. Plus it was really hot and I was ready for a beer!
The sixth picture is where the first tricky part occured and that was when I had to splice in the next pair of frame pieces. But having a bunch of clamps helped keep everything tight and aligned while the epoxy cured.
Pictures 7, 8, and 9 show progress as I glue in more and more cross pieces. I ended up buying pipe coupler fittings to extend the length of my pipe clamps. I eventually ended up with 14 foot pipe clamps!
The next dozen pictures show working through the tricky part of the glue up. A few of noteable shots: Picture 11 show the relief cut I had to make on one of the parts to accomodate the PVC downspout fitting. Pictures 12 and 15 show the cutout area for the downspout and support post... you can also get a good look at the joint detail of how everything fits together. Pictures 17 and 18 show the final glue up that we can do prior to installation. The short backside frame piece is totally masked with clear tape at this point. It's only in place to ensure the glue up is tight and square. It won't be permanently installed until after the bar top is set in place on the bar substrate. Clamps off in the next two shots. Picture 21 is after sanding with 80 then 220 grit sandpaper using the random orbital sander. And last two pictures show the molding I made with some of the scrap teak I had left over.
Step 4: Preparing the Bar Top Substrate
For the most part the bar top substrate was in pretty good shape but there was quite a bit of mortar squeeze out that needed to be ground down. The angle grinder and masonry disc made short work of that task though! It's hard to see but my brother is wearing safety glasses and has ear plugs in.
Step 5: Bonding the Bar Top to the Substrate
So working time for the construction adhesive was stated to be 20 minutes. Being that this was a very big glue up we didn't have time for pictures but it wasn't complicated or difficult at all. All of our prep work gave us a high probability for success. Picture 2 shows the bar top substrate ready to go... smooth, clean, and level. We used a caulk gun and squirted out a couple tubes' worth of adhesive and then carefully set the bar top in place. We checked to make sure it was level (and it was). All that was left was to let it cure for 24 hours. The bar top was really heavy. It took three of us to maneuver it into place. But with all that weight there was no need to apply any clamps or additional weight on top.
Step 6: Completing the Glue Up
Coming down the home stretch now!
The bar top has had 24 hours of cure time and it is ROCK solid. Wow... that construction adhesive is amazing. Now it's time to glue the final pieces into place. First step was to install the the short backside frame piece. This was done with the West System epoxy. That also takes 24 hours to cure. Then finally we used some Titebond exterior wood glue to glue down the trim pieces around the support post and downspout. Yay! It turned out great!
Step 7: Finishing
The bar top was finish sanded with 220 grit sandpaper, wiped clean, and then coated with the Helmsman finish. In total 3 coats were applied and we sanded between coats. SWEET!!! A glass of wine to celebrate a job well done in picture 6. Final shot... ready for the first pool party!
I hope y'all enjoyed seeing the process and as always comments and questions are welcome.
My brother ended up saving a LOT of money by going with the teak instead of the granite. Rather than thousands the entire cost was in the hundreds! So fantastic results, very happy with the finished product, and saved a lot of money. I'd call that a successful project.
I might provide an update later with a few shots of the first pool party. Hmmmm.... then again... I might not. Me in a swim suit is actually not a very pretty sight! LOL!!!
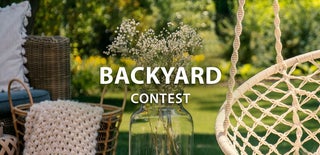
First Prize in the
Backyard Contest