Introduction: Bag Made of Wood and Vegan/faux Leather
For this bag you do not need any electrical tools for the wood, only manual force and patience. I divided the project over several days. A laser cutter would make it a lot easier, even an electric fret/scroll saw would help. Don’t you have electric tools, just like me, no worries! Making it by hand is certainly just as much fun and gives a lot of satisfaction and maybe some muscle pain.
Frankly, this idea is not my own. A while ago I saw someone walking with a bag with wooden sides. Flowers were cast in resin on the wooden sides. I liked it so much that I wanted to make it myself.
I regularly make wooden hangers with resin and the sides of the bag were actually no more than giant bezels, so I should be able to make them.
To make a bag from the two sides seemed a bigger challenge. I decided to use Kraft Tex for the bag it self. Kraft Tex is cardboard that has been processed in such a way that it combines the properties of paper, fabric and leather and is very strong. I work with the raw version and you must first crease and wash it. After this it look like leather and is certainly just as strong, which is why it is also called ‘vegan’ or ‘faux leather’. It is also prepared for sale then you can skip this step.
For the image on the wood I chose a sea theme. Because you are not allowed to bring shells or sand from the beach here, I used Sculpey a polymer clay. The closure and studs come from the hardware store. I have made a lining for the bag but this step can be omitted. Instead of sewing you can also glue, but sewing is preferred.
Frankly, this idea is not my own. A while ago I saw someone walking with a bag with wooden sides. Flowers were cast in resin on the wooden sides. I liked it so much that I wanted to make it myself.
I regularly make wooden hangers with resin and the sides of the bag were actually no more than giant bezels, so I should be able to make them.
To make a bag from the two sides seemed a bigger challenge. I decided to use Kraft Tex for the bag it self. Kraft Tex is cardboard that has been processed in such a way that it combines the properties of paper, fabric and leather and is very strong. I work with the raw version and you must first crease and wash it. After this it look like leather and is certainly just as strong, which is why it is also called ‘vegan’ or ‘faux leather’. It is also prepared for sale then you can skip this step.
For the image on the wood I chose a sea theme. Because you are not allowed to bring shells or sand from the beach here, I used Sculpey a polymer clay. The closure and studs come from the hardware store. I have made a lining for the bag but this step can be omitted. Instead of sewing you can also glue, but sewing is preferred.
Supplies
For the sides:
Paper
Cardboard
Glue stick
Pencil
Ruler
Cutting mat
Rotary cutter
Scissors
Hobby knife
Glue clamps
Glue (eg E6000)
Wood glue
Hand-drill
Brush
Sandpaper
Sanding block (option)
Fretsaw bracket
Fretsaws
Fretsaw board (with clamping device) and clamp
Saw key (option)
Plywood /I have used 6 mm plywood
Derwent inktense pencils and blocks
Sculpey / Fimo or similar clay
Oven
Acrylic paint
Gloves
Safety glasses
Heat gun (option)
Casting resin
Dye (option)
Level
Rudder blade
Masking tape
Wax paper
Studs
Cleaning material for resin/glue
Kitchen paper
Baby seesaws
Alcohol
For the bag:
Paper
Pencil
Ruler
Cutting mat
Measuring tape
Clamps
Pins
Needles
Basting thread
Hobby knife
Scissors
Rotary cutter (option)
Sewing machine (option)
Sewing thread
Lining fabric (option)
Kraft Tex
Fusible Interfacing (Option)
Buckle
Closure
Let’s start!
Paper
Cardboard
Glue stick
Pencil
Ruler
Cutting mat
Rotary cutter
Scissors
Hobby knife
Glue clamps
Glue (eg E6000)
Wood glue
Hand-drill
Brush
Sandpaper
Sanding block (option)
Fretsaw bracket
Fretsaws
Fretsaw board (with clamping device) and clamp
Saw key (option)
Plywood /I have used 6 mm plywood
Derwent inktense pencils and blocks
Sculpey / Fimo or similar clay
Oven
Acrylic paint
Gloves
Safety glasses
Heat gun (option)
Casting resin
Dye (option)
Level
Rudder blade
Masking tape
Wax paper
Studs
Cleaning material for resin/glue
Kitchen paper
Baby seesaws
Alcohol
For the bag:
Paper
Pencil
Ruler
Cutting mat
Measuring tape
Clamps
Pins
Needles
Basting thread
Hobby knife
Scissors
Rotary cutter (option)
Sewing machine (option)
Sewing thread
Lining fabric (option)
Kraft Tex
Fusible Interfacing (Option)
Buckle
Closure
Let’s start!
Step 1: Sort Wood
I soon found out that making pendants is something different from a large version for a bag. It started with the wood I used: 6 mm plywood. When sorting it sounded like hardwood. When I started sawing it turned out that it is rock hard and takes a lot of effort to saw. Also the saws are blunt quickly, so if possible choose a softer type of wood and save muscle pain.
I sort 9 pieces of wood with the following measurements: 4 of 17 x 26 cm, 4 of 17 x 30 cm and 1 of 17 x 35 cm.
The biggest one I will use to protect the table top when I later attach the fretsaw board to the table top with the clamp. The other boards determine the size of the bag I want to make. Eventually I will use 7 boards.
I sort 9 pieces of wood with the following measurements: 4 of 17 x 26 cm, 4 of 17 x 30 cm and 1 of 17 x 35 cm.
The biggest one I will use to protect the table top when I later attach the fretsaw board to the table top with the clamp. The other boards determine the size of the bag I want to make. Eventually I will use 7 boards.
Step 2: Make Pattern for Wooden Sides
The backside
Draw a rectangle on paper measuring 25 x 15 cm and cut out. Fold the rectangle in half once in width and then in length, draw a round corner with a glass (on the open side of the paper) and cut the corner around. After unfolding, you have a rectangle with round corners. Glue this rectangle to sturdy cardboard with a glue stick and cut out. You now have a mold for the back of the wooden side.
The edge
Draw another rectangle, but this time measuring 29 x 15 cm. Draw a guideline at a height of 25 cm. Fold in again in the same way as the back, but fold the paper across the width to the guideline. The protruding part of 4 cm becomes the part for the carrying strap. Make sure that the long side is on the inside when folding in half lengthwise.
Again draw a round corner with a glass (same distance as back). Then draw a straight line from the top of the protruding part down to round corner. First cut, on the open side, the line on the protruding part down to the drawn curve. Now cut the marked curve. After unfolding you have a pattern like the back but with a 4 cm long lip. Fold up again, make sure that the long side is inside again, and draw an edge of 1.5 cm wide on the open side. The easiest way to do this is to dot and connect a line at a short distance. Cut out this line. Unfold and you have a border for on the back.
Only an opening has to be made for the carrying strap and rounded the corners a bit. So fold in half again but now lengthwise. Draw a line on the lip so that it is slightly rounded, on the outside edge of the paper. Just above the center, draw a rectangle on the side of the fold, 2 cm deep and 1 cm high. Cut out all drawn lines and unfold. Glue the pattern on sturdy cardboard with a glue stick and cut out. You now have a mold for the edge.
The support edge for the flap of the bag on the backside
Using the template from the back, draw a support edge of 1.5 cm. Do this by marking the top of the mold to about 6 cm either side on the side. Measure 1.5 cm in the same way as at the edge. Cut out, glue with glue stick on cardboard and cut.
Place the molds on top of each other and check that they are even, trim a little if necessary.
Draw a rectangle on paper measuring 25 x 15 cm and cut out. Fold the rectangle in half once in width and then in length, draw a round corner with a glass (on the open side of the paper) and cut the corner around. After unfolding, you have a rectangle with round corners. Glue this rectangle to sturdy cardboard with a glue stick and cut out. You now have a mold for the back of the wooden side.
The edge
Draw another rectangle, but this time measuring 29 x 15 cm. Draw a guideline at a height of 25 cm. Fold in again in the same way as the back, but fold the paper across the width to the guideline. The protruding part of 4 cm becomes the part for the carrying strap. Make sure that the long side is on the inside when folding in half lengthwise.
Again draw a round corner with a glass (same distance as back). Then draw a straight line from the top of the protruding part down to round corner. First cut, on the open side, the line on the protruding part down to the drawn curve. Now cut the marked curve. After unfolding you have a pattern like the back but with a 4 cm long lip. Fold up again, make sure that the long side is inside again, and draw an edge of 1.5 cm wide on the open side. The easiest way to do this is to dot and connect a line at a short distance. Cut out this line. Unfold and you have a border for on the back.
Only an opening has to be made for the carrying strap and rounded the corners a bit. So fold in half again but now lengthwise. Draw a line on the lip so that it is slightly rounded, on the outside edge of the paper. Just above the center, draw a rectangle on the side of the fold, 2 cm deep and 1 cm high. Cut out all drawn lines and unfold. Glue the pattern on sturdy cardboard with a glue stick and cut out. You now have a mold for the edge.
The support edge for the flap of the bag on the backside
Using the template from the back, draw a support edge of 1.5 cm. Do this by marking the top of the mold to about 6 cm either side on the side. Measure 1.5 cm in the same way as at the edge. Cut out, glue with glue stick on cardboard and cut.
Place the molds on top of each other and check that they are even, trim a little if necessary.
Step 3: Marking on Wood
Draw the template for the back 2x on the wood, the template for the edge 4x and the template for the supporting edge 2x. Marking is easiest by securing the template with clips on the wood. Draw the support edge opposite each other with the end against each other, you now have an O, this is easier to cut out.
I put a small x on all pieces at the bottom so that I know what the front and bottom of the wood is. Moreover, if one side deviates slightly from the other side, the deviating side is all on the same side and you will have to sand less.
Now drill a hole in all the pieces to be cut out with the hand-drill so that you can get the saw through it.
I put a small x on all pieces at the bottom so that I know what the front and bottom of the wood is. Moreover, if one side deviates slightly from the other side, the deviating side is all on the same side and you will have to sand less.
Now drill a hole in all the pieces to be cut out with the hand-drill so that you can get the saw through it.
Step 4: Sawing, Sanding and Gluing
Attach the saw board to the table, use a piece of wood to protect the bottom of the table from the clamp. Tighten the clamp as tight as possible. With the help of a saw board it is easier to saw because your workpiece is free and yet has support. My saw board has a clamping device which is handy and help to put your saw in the fretsaw bracket without force and also your saw will sit tightly in it. Also handy is a saw key or wrench with which you can tighten the wing nuts of the fretsaw. Attach the saw with the teeth down. You can now start sawing. Tip: keep some sawdust. Mixed with wood glue you can use this to fill any irregularities.
Start with the backsides to get in. Saw quietly make sure that you let the wood do the work at corners, that means, you turn the work very quietly and not the saw! If you make the turn with the saw, 9 times out of 10 your saw will break.
As soon as the back sides are ready, cut out the two support edges. Do this by first sawing the inside, then the outside edge and finally the two small edges connecting the support edges. You cut out the inner part by loosening the top of the saw, inserting the saw through the drilled hole and attaching it again in the fretsaw.
The edges are an extra support for the flap of the bag. Now that the backs and supported edges are ready, we stop sawing and sand all parts. The gluing has to be done in parts so we better start gluing first. Use a good wood glue and follow the instructions for the glue. Lubricate (in my case) with a brush the support edge, make sure you apply the side where the cross is on. Let it sit for a minute or two and glue the support edge to the top of the back. Make sure that the cross on the back is on the other side than where you glued the support edge. Align the outer edges and place clamps to join the parts together. Repeat with the second back. Allow to dry according to specified drying time.
Now the front edge follows.
Each front edge consists of two layers, so saw 4 times and glue two times. The easiest order of cutting for the edge is: first the outside, then the recess for the carrying strap and finally the inside. This way your work will continue to have the most support while cutting. Saw two edges and glue them together in the same way as the support edge. Make sure that the adhesive layer is on the side of the cross and that you can see the cross from the edge that comes on it. Let it dry. Repeat this step with the other two edges.
The glue I use dries after 60 minutes but I leave it for an extra hour. Sand any imperfections on the inside of the edge. That is still easy, as soon as the edge is on the back, this is more difficult. Sand the outside at the end. Once you've finished sanding, glue the back and edge together. I do this by smearing the edge, on the side where there is no cross, with glue. After 2 minutes, I press the edges onto the smooth backs and fasten with glue clamps and leave it until the other day.
The next day we can do the finishing. Fill any small holes and sand until everything is nicely even and smooth. When the woodwork is finished, the polymer clay follows.
Start with the backsides to get in. Saw quietly make sure that you let the wood do the work at corners, that means, you turn the work very quietly and not the saw! If you make the turn with the saw, 9 times out of 10 your saw will break.
As soon as the back sides are ready, cut out the two support edges. Do this by first sawing the inside, then the outside edge and finally the two small edges connecting the support edges. You cut out the inner part by loosening the top of the saw, inserting the saw through the drilled hole and attaching it again in the fretsaw.
The edges are an extra support for the flap of the bag. Now that the backs and supported edges are ready, we stop sawing and sand all parts. The gluing has to be done in parts so we better start gluing first. Use a good wood glue and follow the instructions for the glue. Lubricate (in my case) with a brush the support edge, make sure you apply the side where the cross is on. Let it sit for a minute or two and glue the support edge to the top of the back. Make sure that the cross on the back is on the other side than where you glued the support edge. Align the outer edges and place clamps to join the parts together. Repeat with the second back. Allow to dry according to specified drying time.
Now the front edge follows.
Each front edge consists of two layers, so saw 4 times and glue two times. The easiest order of cutting for the edge is: first the outside, then the recess for the carrying strap and finally the inside. This way your work will continue to have the most support while cutting. Saw two edges and glue them together in the same way as the support edge. Make sure that the adhesive layer is on the side of the cross and that you can see the cross from the edge that comes on it. Let it dry. Repeat this step with the other two edges.
The glue I use dries after 60 minutes but I leave it for an extra hour. Sand any imperfections on the inside of the edge. That is still easy, as soon as the edge is on the back, this is more difficult. Sand the outside at the end. Once you've finished sanding, glue the back and edge together. I do this by smearing the edge, on the side where there is no cross, with glue. After 2 minutes, I press the edges onto the smooth backs and fasten with glue clamps and leave it until the other day.
The next day we can do the finishing. Fill any small holes and sand until everything is nicely even and smooth. When the woodwork is finished, the polymer clay follows.
Step 5: Making Figures With Polymer Clay
Follow the instructions on the packaging for processing the clay, I use Sculpey.
Knead a piece of clay and roll out to a 3 mm thick piece. Cut out the figures you want. I choose a sea theme but everything is possible. Bake the clay figures. No clay, no problem, dried flowers also go or beads, gears, screws; choose a design that you like.
After baking and cooling, I painted the figures with Derwent Inktense pencils, which after being wetted with water form a waterproof color, acrylic paint is another option.
Knead a piece of clay and roll out to a 3 mm thick piece. Cut out the figures you want. I choose a sea theme but everything is possible. Bake the clay figures. No clay, no problem, dried flowers also go or beads, gears, screws; choose a design that you like.
After baking and cooling, I painted the figures with Derwent Inktense pencils, which after being wetted with water form a waterproof color, acrylic paint is another option.
Step 6: Create Composition
Once you have made your choice and collected all the parts, it is time to make a composition to see if it works out as you want it. This will be different for everyone. For my sea theme I first draw a background on paper, which I will later paint on the wood. I used the mold to get the drawing fit into the wood. After I placed the drawing, I put the clay figures in it and a dried sprig of sage. I made several compositions and of each composition I made a photo from which I chose one. Now that I know the composition, I can transfer the drawing to the wood but first paint a base layer on the wood.
Step 7: Paint Wood
For the base layer I chose a white hobby acrylic paint for outside, actually there was not much to choose because I had nothing else. In itself this is a very good paint, but because you can only put the work piece outside after three days, I assume the drying process continues for three days. Therefore I do not dare to start with the casting resin before this three days period.
Fortunately, it is paintable after 4 hours. I diluted the white paint with a few drops of dark blue so that the white paint has a blue glow. After the paint has dried for four hours, I first decide to varnish the remaining woodwork, using a Harris clear acrylic spray can. I tape the acrylic paint and apply two layers of clear acrylic outside. As soon as the varnish is dry, I make the drawing with Derwent Ink pencils and Derwent ink blocks, the latter are useful for larger areas.
As soon as the drawing is finished, I edit it with water so that the colors run out and become waterproof. I also let it dry. When everything is dry, I glue all parts with a clear glue, I use the photo I made of the composition as an example. When this is done I let dry everything for 3 days before I start using the casting resin. In the meantime I draw the pattern for the Kraft Tex and lining and prepare it.
Fortunately, it is paintable after 4 hours. I diluted the white paint with a few drops of dark blue so that the white paint has a blue glow. After the paint has dried for four hours, I first decide to varnish the remaining woodwork, using a Harris clear acrylic spray can. I tape the acrylic paint and apply two layers of clear acrylic outside. As soon as the varnish is dry, I make the drawing with Derwent Ink pencils and Derwent ink blocks, the latter are useful for larger areas.
As soon as the drawing is finished, I edit it with water so that the colors run out and become waterproof. I also let it dry. When everything is dry, I glue all parts with a clear glue, I use the photo I made of the composition as an example. When this is done I let dry everything for 3 days before I start using the casting resin. In the meantime I draw the pattern for the Kraft Tex and lining and prepare it.
Step 8: Pattern for Kraft Tex
First I calculate how much Kraft Tex, fusible interfacing and lining I will need. Using the wooden side I measure the circumference. Because the bag must have an overlap I take the circumference + 15 cm extra.
Then I decide how wide I want to make it and make the width equal to the height of the side.
For the bag I need a piece of Kraft Tex of 90 cm x 29 cm; for the interfacing the same and the lining a piece of thin fabric of 93 cm x 32 cm. For the carrying strap I need a piece of Kraft Tex of 145 cm x 6 cm.
I once bought a number of rolls of Måla drawing paper from Ikea, ideal for drawing patterns, among other things.
I start with the belt and measure a strip of 145 cm x 6 cm. The belt will be made of doubled Kraft Tex so eventually it will be 3 cm width. The length includes the loops for attachment. The length of the belt will vary for everyone.
For the bag I calculate the distance from one side of the lip, over the bottom to the other side of the lip, where I completely drop the wood into the Kraft Tex. To allow the flap to run along the lip, the pattern should be narrowed by 1.2 cm on each side.
Because this way the opening of the bag would only have the width of the lip, I had to remove a piece of Kraft Tex at the front of 6 cm. This must be removed over the width, with keeping a lip on both sides that remains over the wood. On the other side, a small piece of 3 cm long and 1.2 cm wide must be cut on both sides. See the drawing, I will only cut this as soon as I put everything together!
Finally, two strips must be cut for the closure: a strip of 12 cm x 3 cm and a strip of 23 cm x 3 cm. In the first strip I make a notch in the middle on both sides of 2 cm long and 1 cm deep, this strip will be for the ring. With the second strip I do the same but now a notch of 3 cm long and 1 cm deep, this strip is for the hook.
Then I decide how wide I want to make it and make the width equal to the height of the side.
For the bag I need a piece of Kraft Tex of 90 cm x 29 cm; for the interfacing the same and the lining a piece of thin fabric of 93 cm x 32 cm. For the carrying strap I need a piece of Kraft Tex of 145 cm x 6 cm.
I once bought a number of rolls of Måla drawing paper from Ikea, ideal for drawing patterns, among other things.
I start with the belt and measure a strip of 145 cm x 6 cm. The belt will be made of doubled Kraft Tex so eventually it will be 3 cm width. The length includes the loops for attachment. The length of the belt will vary for everyone.
For the bag I calculate the distance from one side of the lip, over the bottom to the other side of the lip, where I completely drop the wood into the Kraft Tex. To allow the flap to run along the lip, the pattern should be narrowed by 1.2 cm on each side.
Because this way the opening of the bag would only have the width of the lip, I had to remove a piece of Kraft Tex at the front of 6 cm. This must be removed over the width, with keeping a lip on both sides that remains over the wood. On the other side, a small piece of 3 cm long and 1.2 cm wide must be cut on both sides. See the drawing, I will only cut this as soon as I put everything together!
Finally, two strips must be cut for the closure: a strip of 12 cm x 3 cm and a strip of 23 cm x 3 cm. In the first strip I make a notch in the middle on both sides of 2 cm long and 1 cm deep, this strip will be for the ring. With the second strip I do the same but now a notch of 3 cm long and 1 cm deep, this strip is for the hook.
Step 9: Kraft Tex Cutting and Processing
Because I want to make the belt in one piece, I cut a piece of Kraft Tex with a length of 145 cm and 48.26 cm width.
The Kraf Tex that I have left over can be used for another project. I buy it per bolt, which is much cheaper, a bolt is 10.5 yards x 19 inches (9.60 m x 48.26 cm). The white variant of Kraft Tex is also easy to paint, the results are good with ready-made textile paint as well as with natural dyes.
Use tailor's chalk and clips (do not use pins!). I first draw the pattern of the carrying strap on the piece of Kraft Tex and cut it with the rotary cutter. I cut a piece of 92 cm from the remaining piece, from which I will cut the bag after washing. I do this because the whole piece is very big and clumsy to crease. I take a few more cm because it shrinks about 1 cm at 90 cm.
After cutting the ‘fabric’ I wrinkle the piece for the strap and the piece for the bag into a wad and put it in cold water for a few hours. I keep the remaining piece unprocessed for a later project. After being in the water for a few hours I take it out and hang to dry. After drying I repeat the process, only this time I use warm water and let it stand until the water has cooled, which is about an hour or two. Dry again and repeat the step, but use cold water again. After it has been dried for the last time, the Kraft Tex has a beautiful leather texture. Both sides can be used, but I prefer the ‘smooth’ side.
The Kraf Tex that I have left over can be used for another project. I buy it per bolt, which is much cheaper, a bolt is 10.5 yards x 19 inches (9.60 m x 48.26 cm). The white variant of Kraft Tex is also easy to paint, the results are good with ready-made textile paint as well as with natural dyes.
Use tailor's chalk and clips (do not use pins!). I first draw the pattern of the carrying strap on the piece of Kraft Tex and cut it with the rotary cutter. I cut a piece of 92 cm from the remaining piece, from which I will cut the bag after washing. I do this because the whole piece is very big and clumsy to crease. I take a few more cm because it shrinks about 1 cm at 90 cm.
After cutting the ‘fabric’ I wrinkle the piece for the strap and the piece for the bag into a wad and put it in cold water for a few hours. I keep the remaining piece unprocessed for a later project. After being in the water for a few hours I take it out and hang to dry. After drying I repeat the process, only this time I use warm water and let it stand until the water has cooled, which is about an hour or two. Dry again and repeat the step, but use cold water again. After it has been dried for the last time, the Kraft Tex has a beautiful leather texture. Both sides can be used, but I prefer the ‘smooth’ side.
Step 10: Cut Out Pattern From Fusible Interfacing and Lining Fabric
I make a lining for the bag because I like it, but you don't have to. Pin the pattern on the fusible interfacing, the interfacing I use is suitable for bags and quite stiff. Cut the interfacing without seam allowance. Then iron the interfacing on the lining fabric.
After ironing cut the lining fabric with a seam allowance of approximately 1 to 1.5 cm. Fold the seam allowance around the interfacing and pin it. Baste the folded fabric. After this step I check if the lining fits on the woodwork. Note: do not cut the 3 cm on both sides we still have to cut yet.
I decide that I would also like a few pockets on the lining, but since it is already quite a bit of work, I used the pockets in an apron that I once bought at the thrift store because it was a nice fabric. I baste the pockets on the lining and make a key-cord from one of the cords of the apron.
After ironing cut the lining fabric with a seam allowance of approximately 1 to 1.5 cm. Fold the seam allowance around the interfacing and pin it. Baste the folded fabric. After this step I check if the lining fits on the woodwork. Note: do not cut the 3 cm on both sides we still have to cut yet.
I decide that I would also like a few pockets on the lining, but since it is already quite a bit of work, I used the pockets in an apron that I once bought at the thrift store because it was a nice fabric. I baste the pockets on the lining and make a key-cord from one of the cords of the apron.
Step 11: Cut Out Patterns From Kraft Tex
Note: do not use pins, but clips! Unlike real leather; once you make a hole, for example with a pin you keep seeing it, see the sample I made with the sewing machine. Use a slightly larger stitch on the sewing machine (I use 3.5 mm) and do not go back and forth with the machine too often, or fasten with a knot. I prefer a knot.
Moisten the Kraft Tex slightly before sewing it is easier to process and use a sturdy needle. Iron all parts of Kraft Tex, if necessary, at a low temperature and do not use steam!
The belt was cut before washing and can now be stitched. Fold in half, with the help of clips, and stitch both sides. If you do not have a sewing machine you can glue it with a spray glue but avoid stains.
On the other piece of Kraft Tex I first draw the pattern of the bag, using the lining as a pattern. Then I cut out the big lines with the rotary cutter, for the small corners I use scissors. After that I cut the strips for the closure.
Moisten the Kraft Tex slightly before sewing it is easier to process and use a sturdy needle. Iron all parts of Kraft Tex, if necessary, at a low temperature and do not use steam!
The belt was cut before washing and can now be stitched. Fold in half, with the help of clips, and stitch both sides. If you do not have a sewing machine you can glue it with a spray glue but avoid stains.
On the other piece of Kraft Tex I first draw the pattern of the bag, using the lining as a pattern. Then I cut out the big lines with the rotary cutter, for the small corners I use scissors. After that I cut the strips for the closure.
Step 12: Assemble Lining and Kraft Tex
First stitch the pockets on the lining and remove the basting thread.
Attach one half of the buckle to the cord, make a loop with a piece of the remaining cord with the other end of the buckle and attach it to your bunch of keys.
Place the Kraft Tex around the wooden side and determine where the closure should go, then sew the closure.
Place the lining on the Kraft Tex and stitch all around with the sewing machine. Now sew the extra seams on both sides where you still have to cut the 3 cm. Make an extra seam of about 4 cm with about 5 mm spacing of the already stitched seam where the center of the 5 mm is 1.2 cm from the side, now cut 3 cm in between the seams.
To prevent fraying of the lining fabric, you can touch it with some clear nail polish. Finally, I measure where the studs should be and draw dots with tailor's chalk. I mark 1 cm from the edge and mark every 4 cm width
Once the sides are ready, the bag can be put together. But finish the sides first. The paint has hardened enough, the resin can now be cast.
Attach one half of the buckle to the cord, make a loop with a piece of the remaining cord with the other end of the buckle and attach it to your bunch of keys.
Place the Kraft Tex around the wooden side and determine where the closure should go, then sew the closure.
Place the lining on the Kraft Tex and stitch all around with the sewing machine. Now sew the extra seams on both sides where you still have to cut the 3 cm. Make an extra seam of about 4 cm with about 5 mm spacing of the already stitched seam where the center of the 5 mm is 1.2 cm from the side, now cut 3 cm in between the seams.
To prevent fraying of the lining fabric, you can touch it with some clear nail polish. Finally, I measure where the studs should be and draw dots with tailor's chalk. I mark 1 cm from the edge and mark every 4 cm width
Once the sides are ready, the bag can be put together. But finish the sides first. The paint has hardened enough, the resin can now be cast.
Step 13: Finish the Wooden Sides With Resin
Use gloves and safety goggles in a well-ventilated area! Use wax paper to protect your desk.
Each resin brand has its own manual, which I use is 1: 1. I roughly calculate the content (length x width x height) that I need per side which is 300 ml per side. I could not find a good casting resin on the island where I live, but I had old casting resin that is still well cured although discolored.
I solved this problem by coloring the yellow resin with a little bit of color liquid. I did this by adding a drop each time and stirred until completely absorbed. Stir a little longer than you should according to the instructions, it is good if all the dye has been completely absorbed by the resin.
Keep in mind that if you use dye, the sharpness of the image fades, the colors also fade and old resin gives more air bubbles which cannot be removed. Fortunately with a sea theme that is not that bad.
Make sure the wood is level and gently pour the resin. Prick air bubbles away with a pin or use a heat gun. Let it cure according to the instructions before proceeding. The resin I use is a resin for jewelry and do not need to be polished.
Each resin brand has its own manual, which I use is 1: 1. I roughly calculate the content (length x width x height) that I need per side which is 300 ml per side. I could not find a good casting resin on the island where I live, but I had old casting resin that is still well cured although discolored.
I solved this problem by coloring the yellow resin with a little bit of color liquid. I did this by adding a drop each time and stirred until completely absorbed. Stir a little longer than you should according to the instructions, it is good if all the dye has been completely absorbed by the resin.
Keep in mind that if you use dye, the sharpness of the image fades, the colors also fade and old resin gives more air bubbles which cannot be removed. Fortunately with a sea theme that is not that bad.
Make sure the wood is level and gently pour the resin. Prick air bubbles away with a pin or use a heat gun. Let it cure according to the instructions before proceeding. The resin I use is a resin for jewelry and do not need to be polished.
Step 14: Assemble the Bag
First sew the carrying strap on wooden sides, otherwise this will no longer possible with the sewing machine.
I stitch the strap on both sides by first stitching a rectangle and then stitching a cross in the rectangle for optimal strength. After the strap I glue the Kraft Tex piece by piece on the wooden side and immediately fix it with studs. So I go around at the first side and then do the other side.
Remove any glue stains immediately with some alcohol. When the last stud is in, the bag is ready. You now have a one of a kind bag. To be on the safe side, allow the casting resin to cure for a few more days before using the bag.
I stitch the strap on both sides by first stitching a rectangle and then stitching a cross in the rectangle for optimal strength. After the strap I glue the Kraft Tex piece by piece on the wooden side and immediately fix it with studs. So I go around at the first side and then do the other side.
Remove any glue stains immediately with some alcohol. When the last stud is in, the bag is ready. You now have a one of a kind bag. To be on the safe side, allow the casting resin to cure for a few more days before using the bag.
Step 15: Things I Will Do Different Next Time
Next time I make the back of 3 mm plywood and the edge out of one layer 8 mm plywood. This will reduce the weight both by wood and resin. Making it narrower can also reduce weight, still this bag weighs 300 grams less than my heaviest shoulder bag.
Although the colored casting resin does not look out of place, next time I go for uncolored resin. Doing so, the cast components and drawing will remain fully visible.
Meanwhile I keep dreaming of a laser cutter.
Although the colored casting resin does not look out of place, next time I go for uncolored resin. Doing so, the cast components and drawing will remain fully visible.
Meanwhile I keep dreaming of a laser cutter.
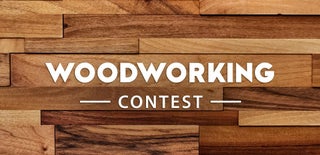
Participated in the
Woodworking Contest