Introduction: Bandsaw Stand From Scrap Lumber
I have a portable bandsaw that I absolutely love- it's one of my favorite and most useful tools. Cutting small pieces of metal with any degree of precision can be difficult however. What I needed was a stand to turn it into a benchtop saw.
This is a super simple low cost stand that is very easy to make and can be built in an afternoon.
Let's get started!
Step 1: Tools and Materials
Tools needed
Portable bandsaw- mine is the DeWalt DWM 120 model
Drill
Various size drill bits
3/4" forstner or spade bit
Materials
2" wood screws
Wood glue
2ea 1" x 4" x 14" long wood board (I used pine)
2ea 1" x 4" x 5 1/2" long wood board
1ea 4" x 4" x 20 1/2" long post
1ea 4" x 4" x 9 1/2" long post
2ea 8" x 8" x 3/4" plywood triangle
1ea 12" x 12" x 1/4" thick Aluminum plate- I used a piece of salvaged Aluminum I found but you could also use a thicker piece of wood. Aluminum plate can be purchased from Online Metals.
Power strip with switch- make sure it can handle the saw amperage
Large zip tie
Step 2: Build the Base
To build the base take the longer 4" x 4" post and set it behind the shorter 4" x 4" post as shown in the first photo. Take one of the plywood triangles and glue and screw the triangle to the posts as shown.
Remove the D shaped handle from the saw and set the saw next to the upper post. Note where the handle mounting hole is located. Glue and screw one of the 1" x 4" x 5 1/2" wood pieces to the top of the post so it covers the handle mounting hole. Now flip the stand over and attach the second upper wood piece and plywood triangle to the opposite side of the stand. The two upper pieces of wood will be used to mount the saw to the stand.
Step 3: Mount the Saw
Begin by drilling a hole where you want the handle mount to be located- this hole should go through both upper wood pieces. Test fit the handle mounting bolt in the wood pieces- it needs to go all the way through both wood pieces.
Since my saw bolt wasn't long enough I used a forstner bit to make a counterbore for the bolt head so the bolt would reach all the way through. Once this was done I was able to hold the saw in position and slip the bolt through the handle bolt hole to secure the saw to the stand.
Once I was happy with the saw fit I removed it and added the feet to support the stand by attaching the 1" x 4" x 14" long wood boards to the bottom 4" x 4" post using glue and screws.
Step 4: Add a Base Plate
In order for the saw to be useful a base plate to support material during cutting needs to be added. I used a 12" square of 1/4" thick Aluminum plate to make the base plate- this was a piece of scrap material that I salvaged from an old casting machine. Lots of different materials could be used to make this but the most important thing is that it be rigid.
Remove the blade foot from the saw and set it on top of the base plate. Use the foot as a template to mark a line where the blade needs to fit through and mark the position of the foot mounting holes. Now drill two holes in the plate in order to mount the plate to the saw. I made a countersink for each hole with a drill bit so the mounting screws would sit flush with the top of the plate. Once that was done I cut a slot for the blade and mounted the plate to the saw.
Wrap a large zip tie around the back post and the saw trigger. Now mount a switched power strip to the front of the forward stand foot and plug the saw into the power strip. Now when you turn on the power strip the saw will turn on.
All done!
I've been using my saw like this for over a year and it's been great. I can cut through any material just like before when holding the saw by hand but now I have a much greater degree of control. Cutting small pieces is no longer a problem at all!
If you have any questions when making your own stand please don't hesitate to ask!
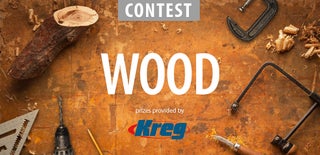
Participated in the
Wood Contest 2016
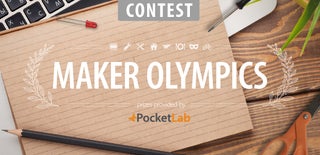
Participated in the
Maker Olympics Contest 2016