Introduction: Banksy Inspired Cast Aluminium Clock
I'd previously laser engraved some art board and replaced the original Safeway kitchen clock face with my design. While I was happy with it, once the mechanism died, I wanted a more pleasing solution.
Having recently built a complete aluminium melting and molding setup, I thought a cast aluminium banksy clock would look somewhat industrial and fit the Banksy motif well.
The clock face was cut with a router and circle attachment out of mdf. All logo's, lettering and hour dashes were created with Tinkercad and 3D printed. The resulting pattern was then popped into my largest molding box and rammed up with my own greensand mix. (AFS75 silica sand and 12% bentonite clay)
Luckily I was happy with the first pour as the whole sand banging, metal melting process takes about 2 hours.
The sprue, riser and gates were cut off with a hacksaw and the runners were cut down off the back with a benchtop mill. The German made movement was purchased from a local jewelry supplier.
My furnace has a babington burner which uses dirty motor oil as the fuel source with a small 25L compressor providing the necessary air supply. Once the oil drips are adjusted and running with 2 Bar of air pressure, there is very little smoke. I use about 1 liter of oil during a melt, roughly 35min.
The metal used was sourced from a local scrapyard and termed "clean cast", basically old motor cases, bike brake and clutch levers and an inlet manifold from a diesel generator.
Supplies
Complete metal melting/molding setup, ie furnace with its required tools, green sand and molding flasks with its required tools.
Salamander A4 clay graphite crucible.
3D printer.
Wood router with circle cutting jig.
9mm thick mdf, 250mm x250mm for the clock face
Lathe to cut the 2 degree draft angle on the disc edge.
Rough cut file to dress the clock face edges.
Benchtop mill to clean up the clock face back.
Hammerite grey, and smooth black paint.
Clock mechanism and hands, mine is a UTS made in Germany.
Step 1: My Workflow
Using the rat as an example, I first sourced an image from the web, converted it to black and white, imported into Inkscape as a bmp and path traced it. Its then saved as a "plain" svg (not an Inkscape svg) and imported into Tinkercad to create the stl file for 3D printing.
I originally used a 2mm height for the 3D files but got a lot of tear out when sand molding so I resorted to 1mm thick for the numerals, banksy logo and rat.
The hour dashes were easy enough to create in Tinkercad using 2 spheres joined with a cylinder and slicing in half, they were 1.5mm high.
I wanted the comic sans font as I thought it would take the molten metal much better than other fonts.
Procedure was as per the rat example, I imported a svg file into Tinkercad as they dont have native support for that font.
Once the wood/plastic pattern is made, its gets molded in the flask, pattern gets removed and molten metal is poured into the mold flasks.
After it has cooled down for about 15min the flask gets separated and the part removed and dunked into a bucket of water.
At this point it is cool enough to inspect and clean up with hacksaw and files.
Step 2: Draft Clearance Work Around.
The issue with Tinkercad is that you cant create the necessary draft angle on text to make it easier to release from the sand, so I left some of the brim on the parts as I was concerned that pulling the brim off would either leave an undercut of the first layer or the delicate parts would have layer separation.
I covered the mdf disk with a thick layer of polyurethane varnish in the hopes that it would act as a fillet between the plastic and the mdf.
Judging by the end result, this approach seems to have worked well.
Step 3: Molding the Pattern.
First the pattern is dusted with parting powder, then fine facing sand is rubbed through a sieve. Next the flask (drag) is rammed up with sand, flipped over and top half (cope)added.
It was at this stage I forgot to hold the bottom board when flipping and the pattern popped right out. Bit of an oopsie, but at least I got to see a preview and it looked good.
So, some careful lining up and I dropped the pattern gently back in.
Next I added the vents, sprue and riser and rammed up the cope with sand.
Once done, I remove the riser and sprue, cut the pouring basin and dust everything with parting powder(builders lime).
Next the drag and cope are separated to pull out the vent dowels and cut the runners. Everything is blown out to get rid of any loose sand grains. After that the drag and cope are joined and set on the backing board on the floor.
The furnace is fired up and all tools are made ready for the pour.
Step 4: Out of the Molding Flasks.
Its usually a coin toss as to how the finished product is going to turn out.
This was the case and even though I was happy, some air bubbles and pitting occurred. I also saw a "rat tail" which happens when 2 wave fronts collide and one has cooled down.
Thankfully I didnt get bad shrinkage on the clock face as that would have required another molding and pouring operation.
The fact that the three vents didnt make it to the surface and have smooth rounded tops leads me to think that it cooled down too quickly while pouring, I poured at about 700 deg C, medium cherry red.
On a side note, my first layer height for the plastic parts was 0.3mm and you can see the sand picked up the brim 0.3mm resolution quite well.
Step 5: Touch Ups.
Once the clock back was cleaned up with the mill, I used a dremel and small burr to see what I could do on the front face.
Where I'd dremel'd, the metal was a lot brighter than the surrounding area and decided to stop as I didnt like the look.
Finally the back was dressed with a rough file to remove all the bumps and make it more uniform to seat the mechanism.
Step 6: In Retrospect.
Hanging on the wall, it does look a tad small, but I was limited by the volume of my A4 crucible.
As can be seen from the 104gram leftovers, I cut it rather close.
Step 7: Adding a Wood Surround.
The clock looked a bit bare and a tad on the small side so I decided to make a wood surround.
Twelve pieces of meranti, 72 mm x 39mm, with a 75 degree angle on the ends were glued and clamped using a ratchet tie down strap.. This was then made circular with the wood router.
A sacrificial board was glued to the bottom and center drilled for the circle cutting jig.
Once the sides were cut with the straight flute bit, a 3/16 corner round bit was used for the inside and a 5/16 for the outside.
I used teak oil to finish it off.
The gold hands were tricky to see in a shaded room, so I painted them white for better visibility.
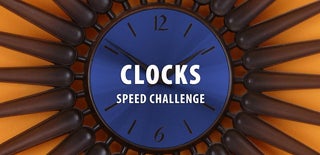
Second Prize in the
Clocks Speed Challenge