Introduction: Basic Fluidyne Heat Engine
Welcome to my first instructable! I will be showing you how to build a Fluidyne engine cheaply, primarily from plastic PVC piping.
You may be asking, "what the heck is a Fluidyne?" Invented in 1969 by the UK's Atomic Energy Authority, It is a heat engine (similar in principle to a Sterling engine) that uses a working fluid (commonly water) as the 'pistons' and the expansion of air due to heat to drive the water. As the water is pushed down to a cooler point (usually a separate cylinder that acts as a cold side) the expanding gas also cools, contracting and allowing the water to rush back upward, generating power. There are no moving parts in the engine itself, just the movement of water and air acting as analogues to pistons.
A notable use for this engine has been as a water pump is rural areas, where access to electricity and precisely manufactured engine components are hard to come by. It should be noted that this engine isn't very efficient when compared to a mechanical engine, but it's very reliable, long lasting, cheap to build, and easy to construct.
Now, onto the build!
Step 1: Tools and Materials
As stated in the intro, this particular engine is made mostly out of PVC pipe (mostly as a cost saving measure). However, you can using essentially any rigid water proof material:
- 3/4 inch PVC 90 degree elbows - 4
- 3/4 inch PVC tee socket - 1
- 3/4 inch x 2 feet PVC pipe sections - 2 (You can also buy one large piece and cut it to size)
- 3/4 inch x 10 inch steel nipple - 1
- Thread seal tape roll note: this is to create a water tight seal between the steel nipple and the PVC. There are better options (including the use of adapters and adhesives) but this was the cheapest in my case.
- PVC cement (I actually just used rubber cement, but you really should use the correct bonding agent)
- Small plastic bottle cap (for restricting air flow)
Tools:
- Hair dryer (or other heat source)
- Something to cut PVC (I used a hand saw, but a PVC cutter would be better. Many hardware stores will also cut for free/low price)
- marker (for making cut lines)
- Rubber mallet (for taking piping into place)
- Funnel (trust me, it makes adding the water much easier)
Optional:
- Valve: I didn't use one, but it can help you fine tune the engine by adjusting flow rate.
- Pipe supports: They make it much easier to work with, but aren't necessary.
- Balloon: For observing air displacement on the output. You could also use a spirometer for more precise observations (the manual ones are around $6 USD)
- PVC to steel coupling: This is the way you're suppose to make a connection between these materials. They're kinda pricey, and I had difficulty even locating some, but they will give the best results.
- Thinner tubing for the air section: as I understand it, this helps to drive up the temperature differential by restricting the flow of air from the hot side to the cold side.
- Regenerator: most heat engines use a regenerator, which is an internal heat exchanger made of a material which air flows through easily. It stores heat as hot air passes through it, then partially reheats cool air passing back through it, improving engine efficiency. I've read that steel wool can be used as a cheap regenerator, but have yet to try this.
Step 2: Cutting the Pipe to Size
There wasn't an exact size I was going for with most of these cuts, so bear with me.
The small sections used to connect the elbows at the top and bottom were measured out by placing the elbows next to the pipe, adding 3/4 of an inch of space between them, and marking off. The 3/4 inch between them is for tolerance due to imperfections in my cuts. See pictures for more detail.
The cold side cylinder that runs parallel to the steel nipple is simply measured and cut to the exact same length as the steel nipple.
While you're in a cutting mood, you should also cut that bottle cap into a restrictor plate. I found that scissors worked fine for the thin plastic, but a thicker plastic cap may require a saw.
The remainder of the cut pipe will be used in the next step.
Step 3: Dry Fitting and Assembly
Always dry fit all the pieces before gluing! Mistakes happen, wrong parts are purchased, both can be fixed if caught in time.
The order of assembly really doesn't matter assuming you take care to align all the parts, and making sure everything is properly fitted. Still, I'll walk you through how I did it:
1. Apply cement to the ends of the 10 inch piece of PVC pipe (remember, the cold side?), as well as the top socket on the tee connector (the bottom of the T), and to one of the sockets on an elbow piece. Press the three parts together, tap gently with rubber mallet.
2. Next apply cement to the two short pieces (used to join the elbows at the top and bottom) on one end each, as well as inside the socket of the elbow at the top of the cold side, and inside the socket of the tee on the same side. Attach them together the same as the other connections.
3. Now wrap the steel nipple with the thread sealing tap on both ends, press an elbow onto each end (with both of their open sockets facing the same direction).
4. Apply cement to the exposed ends of the short segments and inside the elbows on the steel nipple, line them up, and press both the top and bottom together. Use the rubber mallet to gently tap all the connections, to confirm a good fit.
5. Use cement on the final tee socket and the remainder of our pipe we cut from earlier, press together. smear cement on the other end and attach the final elbow. Apply cement to the inside of the open elbow socket and to the end of your final section of pipe, press together, and gently tap all connection to confirm fit.
Take a moment to make sure everything is properly aligned by placing the whole thing on a flat surface; it should lay completely flat, with none of the parts sticking up higher than any others. If it isn't aligned properly it could affect performance.
Step 4: Setup and Operation.
Fill with water to about the half way point on the cylinders. I did this by popping the elbow piece off of the hot side's top (since it's just sealed with thread sealing tap), and estimating the fill height. The long tube to the left side is called a tuning tube; you can calibrate the perform of the engine (to a certain extent) by adding/removing water from this tube. This involves a hit of trial and error, tinkering will be necessary. If you were driving a water pump or other machinery, you'd use this tube as the power output instead.
From here it's very simple: Apply heat (such as a hair dryer) to the top part of the hot side cylinder to heat the air inside. This will cause the air to rapidly begin expanding toward the cold side cylinder, but the flow will be restricted by our bottle cap. As the air pushes in it will simultaneously displace the water in the cold side (in the tuning tube as well), while beginning to cool down and contract. This will eventually result in the air rushing back to the hot side, both due to contraction and the water forcing its way back up the cylinder. The hot side water will be slightly displaced before forcing the air back up, and the cycle will repeat.
Step 5: Conclusion and Final Notes
This design is very basic, and very low cost due to my minuscule hobby budget. As such there are many improvements and alterations that could easily improve this concept greatly, many of which you can find easily online. Adding a regenerator, valves, smaller tubing for restricted air flow, changing the geometry of the whole thing, etc., etc. I will be improving the design as I have time/money, and will likely publish updates to better illustrate the concepts.
This is meant as a demonstration of concept and I hope it intrigues you as much as it did me! Due to the inherent flaws of this design, I would not recommend using it for any serious work. seriously, there are much better designs out there. But if you just want something to play around with till you can build a proper one, this'll do the trick.
This is my first Instructable, thanks for reading it! If I've made any errors, please let me know so that I can fix my embarrassing mistakes. I admit that I got kind of excited and rush right into making this, so there are bound to be issues.
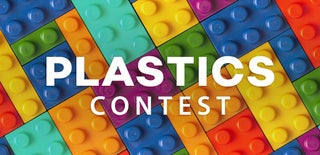
Participated in the
Plastics Contest