Introduction: Battery Powered Tube Amplifier
Tube amplifiers are loved by guitar players because of the pleasant distortion that they produce.
The idea behind this instrunctables is to build a low wattage tube amplifier, which can be also carried around to play on the go. On the age of bluetooth speakers, it is time to build some portable, battery powered tube amplifiers.
Step 1: Select the Tubes, Transformers, Batteries and High Voltage Supply
Tubes
Because power consumption in tube amplifiers is a huge problem, the choosing the right tube can spare a lot of power and increase the playing hours between recharges. Some long time ago there were battery powered tubes, which powered from small radios to airplanes. Their great advantage was the lower filament current required. The picture shows a comparison between three battery powered tubes, the 5672, 1j24b, 1j29b and a miniature tube used in guitar preamps, the EF86
The choosen tubes are:
Preamp and PI: 1J24B (13 mA filament current at 1.2V, 120V max. plate voltage, russian made, inexpensive)
Power: 1J29B (32 mA filament current at 2.4V, 150V max. plate voltage, russian made, inexpensive)
Output transformer
For such lower power settings a cheaper transformer can be used. Some experiments with line transformers showed that they are quite good for smaller amplifiers, where the bottom end is not a priority. Because of the lack of an air gap the transformer works better in push-pull. This also requires more taps.
100V line transformer, 10W with different taps
(0-10W-5W-2.5W-1.25W-0.625W and on the secondary 4,8 and 16 ohms)
.Luckily the transformer I got also had the number of turns per winding specified, otherwise some math would be necessary to identify the adequate taps and the highest impedance available. the transformer had the following number of turns at each tap (starting from the left):
725-1025-1425-2025-2925 on the primary and 48-66-96 turns on the secondary.
Here it is possible to see that the 2.5W tap is almost in the middle, with 1425 turns on one side and 1500 on the other. This small difference could be a problem in some bigger amplifiers, but here it will just add up to the distortion. Now we can use the 0 and 0.625W taps for the anodes to obtain the highest impedance available.
The primary to secondary turns ratio is used to estimate the primary impedance as:
2925/48 = 61, with an 8 ohm speaker this gives 61^2 *8 = 29768 or approx. 29.7k anode-to-anode
2925/66 = 44, with an 8 ohm speaker this gives 44^2 *8 = 15488 or approx. 15.5k anode-to-anode
2925/96 = 30, with an 8 ohm speaker this gives ^2 *8 = 7200 or approx. 7.2k anode-to-anode
Because we intend to run this in class AB the impedance that the tube is actually seen is only 1/4 of the calculated value.
High voltage power supply
Even this small tubes also require higher voltages at the plates. Instead of using several batteries in series, or using those huge old 45V batteries I used a smaller switched mode power supply (SMPS) based around the MAX1771 chip. With this SMPS I am able to multiply the voltage coming from the batteries to values as high as 110V without any problems.
Batteries
The choosen batteries for this project are Li-Ion batteries, easily obtained in the 186850 package. There are several charger boards available online for these. One important note is to buy only known good batteries, from trusted sellers, to avoid unnecessary accidents.
Now that the parts are roughly defined it's time to start working on the circuit.
Step 2: Working on a Circuit
Filaments
To power the tubes filaments a series configuration was choosen. There are some difficulties that must be discussed.
- Because the preamp and power tubes have different filament currents resistors were added in series with some filaments to bypass part of the current.
- The battery voltage drops during the use. Each battery has initially 4.2V when fully charged. They quickly discharge to the nominal value of 3.7V, where they slowly decrease to 3V, when it must be recharged.
- The tubes have direct heated cathodes, meaning that the plate current flows through the filament, and the negative side of the filament corresponds to the cathode voltage
The filament scheme with voltages looks like this:
battery(+) (8.4V to 6V) -> 1J29b (6V) -> 1J29b // 300ohms (3.6V)->1J24b // 1J24b // 130 ohms (2.4V)->1J24b // 1J24b // 120 ohms (1.2V) -> 22 ohms -> Battery(-) (GND)
where // represents in parallel configuration and -> in series.
The resistors bypass the extra current of the filaments and the anode current flowing at each stage. To correctly predict the anode current it is necessary to draw the loadline of the stage and choose an operation point.
Estimating an operation point for the power tubes
This tubes come with a basic datasheet, where the curves are plotted for a screen grid voltage of 45V. Since I was interested in the highest output I could get, I decided to run the power tubes at 110V (when fully charged), way above the 45V. To overcome the lack of a useable datasheet I tried to implement a spice model for the tubes using paint_kip and later increase the screen grid voltage and see what happens. Paint_kip is a nice software, but requires some skill to find the correct values. With pentodes the difficulty level also increases. Since I only wanted a rough estimation I did not spend much time looking for the exact cnfiguration. The test rig was built to test the different configurations.
OT Impedance: 29k plate-to-plate or approx. 7k for class AB operation.
High voltage: 110V
After some calculations and testing the grid bias voltage could be defined. To achieve the choosen grid bias the grid leak resistor is connected to a filament node where the difference between the voltage of the node and the negative side of the filament. For example, the first 1J29b is at the B+ voltage of 6V. By connecting the grid leak resistor to the node between the 1J24b stages, at 2.4V the resulting grid voltage is -3.6V in relation to the GND line, which is the same value seen on the negative side of the filament of the second 1J29b. So, the grid leak resistor of the second 1J29b can go to ground, as it normally would in other designs.
The phase inverter
As seen in the schematic, a paraphase phase inverter was implemented. In this case one of the tubes has a unity gain and inverts the signal for one of the output stages. The other stage acts as a normal gain stage. Part of the distortion created in the circuit comes from the phase inverter losing balance and driving one power tube harder than the other. The voltage divider between the stages was choosen so that this only occurs at the last 45 degrees of the master volume. The resistors where tested while the circuit was monitored with an oscilloscope, where both signals could be compared.
The preamp stage
The last two 1J24b tubes consist of the preamplifier circuit. Both have the same operation point since the filaments are in parallel. The 22 ohms resistor between the filament and ground elevates the voltage at the negative side of the filament giving as small negative bias. Instead of choosing a plate resistor and calculating the bias point and necessary cathode voltage and resistor, here the plate resistor was adapted according to the desired gain and bias.
With the circuit calculated and tested it is time to make a PCB for it. For the schematic and PCB I used Eagle Cad. They have a free version where one can use up to 2 layers. Since I was going to etch the board myself it makes no sense using more than 2 layers. To desing the PCB it was first necessary to also create a template for the tubes. After some measurements I could identify the correct spacing between pins and the anode pin at the top of the tube. With the layout ready it is time to start the real build!
Step 3: Soldering and Testing the Circuits
SMPS
First solder all the components of the Switched mode power supply. For it to work correctly the right components are required.
- Low on resistance, high voltage Mosfet (IRF644Pb, 250V, 0.28 ohms)
- Low ESR, high current inductor (220uH, 3A)
- Low ESR, high voltage reservoir capacitor (10uF to 4.7uF, 350V)
- 0.1 ohm 1W resistor
- Ultrafast high voltage diode (UF4004 for 50ns and 400V, or anything faster for >200V)
Because I am using the MAX1771 chip at a lower voltage (8.4V to 6V) I had to increase the inductor to 220uH. Otherwise the voltage would drop under load. When the SMPS is ready I tested the output voltage with a multimeter and adjusted it to 110V. Under load it will drop a little bit and a readjustement is required.
Tube Circuit
I started soldering the jumpers and components. Here it is important to check if the jumpers are not touching any component legs. The tubes were soldered on the cooper side after all the other components. With everything soldered I could add the SMPS and test the circuit. For the first time I also checked the voltage at the plates and screens of the tubes, just to be sure that everything was OK.
Charger
The charger circuit I bought on ebay. It is based around the TP4056 chip. I Used a DPDT to switch between a series and parallel configuration of the batteries and a connection to the charger or to the circuit board (see figure).
Step 4: Enclosure, Grill and Faceplate and Finish
The Box
To box this amplifier I choose to use an older wooden box. Any wooden box would work, but in my case I had a really good one from an ammeter. The ammeter was not working, so I could at least rescue the box and build something nive inside it. The speaker was fixed at the side with the metal grill that allower the ammeter to cool down while in use.
The tube grill
The PCB with the tubes was fixed on the opposite side of the speaker, where I drill a hole so that the tubes are visible from the outside. To protect the tubes I made a small grill with an aluminium sheet. I make some rough marks and drilled smaller holes. All the imperfections were corrected during the sanding phase. To give a good contrast to the faceplate I ended up painting it black.
The Faceplate, sanding, toner transfer, etching and sanding again
The faceplate was done similarly as the PCB. Before I started, I sanded the aluminium sheet to have a rougher surface for the toner. 400 is rough enough in this case. If you want you can go up to 1200 but it is a lot of sanding and after the etch there will be even more, so I skipped that. This also removes any finish that the sheet had previously.
I printed the mirrorred faceplate with a toner printer on a glossy paper. Later I transfered the drawing using a normal iron. Depending on the iron there are different optimal temperature settings. In my case, it is the second setting, just before the max. temperature. I transfer it during 10 min. approx., until the paper starts to get yellowish. I waited for it to cool down and protected the back of the plate with nail polish.
There is the possibility of just spraying over the toner. It also gives good results if you can remove all the paper. I use water and towels to remove the paper. Just be careful not to remove the toner! Because the design here was inverted I had to etch the faceplate. There is a learning curve in etching, and sometimes your solutions is stronger or weaker, but in general when the etch seems deep enough it is time to stop. After etching I sanded it starting with 200 and going up to 1200. Normally I start with 100 if the metal is in bad shape, but this one was need and was already in good shape. I change the sandpaper grain from 200 to 400, 400 to 600 and 600 to 1200. After that I painted it black, waited one day and sanded again with the 1200 grain, just to remove the excessive paint. Now I drilled the holes for the potentiometers. To finish it I used a clear coat.
Finishing touches
Batteries and parts were all screwed to the wooden box after the faceplate was positioned, from the speaker side. To find the best SMPS position I turned it on and verified where the audio circuit would be less affected. Since the audio circuit board is much smaller than the box the adequate spacing and correct orientation was enough to make the EMI noise inaudible. The speaker baffle was then screwed in place and the amplifier was ready to play.
Some considerations
Close to the batteries end there is a noticeable volume drop, before I could not hear it, but my multimeter showed that the high voltage decreased from 110V to 85V. The heaters voltage drop also decrease with the battery. Fortunately the 1J29b works without a problem until the filament reaches 1.5V (with the 2.4V 32mA setting). Same goes for the 1J24b, where the voltage drop reduced to 0.9V when the battery was almost drained. If the voltage drop is a problem for you, there is the possibility of using another MAX chip to convert to a stable 3.3V voltage. I did not wanted to use it, because it would be another SMPS in this circuit, which could introduce some extra noise sources.
Considering the battery life, I could play a whole week before I had to recharge it again, but I only play for 1 to 2 hours a day.
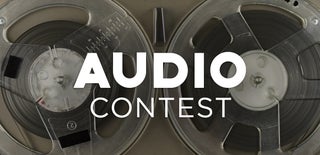
Participated in the
Audio Contest 2018