Introduction: Brake Light Blinker for Motorcycles
Brake Blinker on a 2017 Kawasaki Ninja 650 ABS
Brake Blinker on a 2015 Kawasaki Ninja 300 ABS
Motorcycling is inherently dangerous. And part of that is due to reduced visibility. Everything we can do to tip the scale in our favor helps: high-viz gear, riding with the headlight/high-beam on, loud mufflers... Finally, one thing that can help raise safety via increased visibility is a brake light blinker! Especially with drivers who like to get a little too close at red lights. It's a cheap little device that pulsates your brake light to make it more salient and obvious. Here I'm going to run you through the steps to install it.
*Just in case it isn't clear, the brake blinker controller works as follows: As soon as you hold down the brake lever (either rear or front), the tail brake light blinks rapidly, then slowly, then stays constant for as long as you hold the brake lever. If you let go of the lever for even a fraction of a second, and press it again, the sequence starts all over again. If you release and press the brake lever within the sequence (while it is still blinking), it restarts from the beginning.
This DIY may be updated over time. To see the latest version of the project check here.
Difficulty: 2 out of 5
Tool Requirements: 2 out of 5
Time: 2 Hours
Cost: 2-15$
Last Updated: March 24, 2018
Disclaimers:
Working on any vehicle can be risky to both yourself and the vehicle. No warranties or guaranties, explicit or implicit, are made or implied regarding the compatibility, suitability or effect on any current warranties. All modifications should be made within the reader's capability and under their own exclusive responsibility.
A bit of motivation to keep making instructables always helps. I'm a participant in the Amazon Services LLC Associates Program as well as eBay Partner Network, affiliate advertising programs designed to provide a means for creators to earn fees by linking to their sites, at no extra cost whatsoever to you.
Step 1: What You'll Need
Parts
All you will need for this DIY is a GS-100A Brake Light Blinker. "GS-100A" seems to be the generic model number for the part, and a variety of manufacturers make generic versions of it at varying levels of quality. But in essence, they are all mostly the same. There are versions for "blinking" a single light, or dual brake lights (left and right). You will want to buy the model with two wires coming in, and two coming out (opposed to "3 in/ 3 out", or more), unless you have more than one brake light (like cars). I'll leave links to the little trinket below (multiple links for redundancy):
2x GS-100A Brake light flasher @ Amazon.com - This link is for two units. I think it's good to have a spare, since it's a cheap imported electronic device and it would suck if it's DOA.
iJDMTOY GS-100A LED Brake Light Controller @ Amazon - In case the 1st link is broken. This unit probably has better quality control.
GS-100A LED Brake Light Controller @ Ebay - The cheapest, unbranded ones I can find, but with slower international shipping.
Another unit worth considering is the 3rdBrakeFlasher Brake Light Blinker. It's a high quality, totally waterproof, made in America model with a lifetime warranty. If you want the best unit, this is probably it.
Note: Most brake light blinkers don't work well with the halogen bulbs. The bulb can't turn on and off quick enough to keep up with the blinker. If you are doing this install on a bike with a 1157 bulb (many Kawasaki and similar bikes), I recommend the JDM ASTAR 1157 Red 5730 24-SMD LED Bulb which I measured to be almost twice as bright as the stock bulb. Or, if you don't want to install an LED brake light bulb you can get a model like this one which is designed to work with halogen bulbs.
Tools and Supplies
These are the things I used to complete the project The items within parenthesis are optional depending on how you do the project.
- Multimeter: A staple in any automotive electrical project. I happen to be pretty satisfied with this one for quick work like this.
- Hobby Knife: For stripping wires.
- (Soldering Iron): I really like this unit because of the long cable (great for working on vehicles), adjustable temperature, and On-Off switch.
- (Rosin Core Solder): The rosin core helps solder dirty wiring.
- (Wire assortment): You'll want 16 or 18 Gauge Wire for this use (around 1 amp for a short distance).
- (Adhesive Heat Shrink Assortment): Wire corrosion on motorcycles is a big issue. The adhesive heat shrink helps seal the cable.
- (Liquid Electrical Tape): You can apply some of this if you really want to help make the wires corrosion and humidity resistant. It's a great thing to have in your tool box.
- (Ratcheting Terminal Crimper): This is a must-have for professional looking automotive electrical work. It's the only right way to crimp terminals (which is the right way to make connections). If you get one, make sure it includes multiple jaws. The one I use (albeit a little expensive - but worth it) is this one.
- (2.8mm 3 Way Connector): Only necessary if you want to make the control unit replaceable or removable. For the tiny cost, if you can, it's worth doing for the saved time later on. I used a 4 way connector in the tutorial since I didn't have a 3 way at hand. Either would work.
- (Dielectric Grease): For protecting electrical connections from humidity.
Step 2: Optional - Prep the Brake Controller
You can skip this if you simply want to do it the quick and easy way.
Honestly, I'm a fan of "correct" and elegant installations. This installation was made on my new Ninja 650 ABS so I felt like doing it right. That's why instead of simply installing the brake controller as is, I opened up the little box, connected the two grounds together (suppressing 1 of the 4 wires) and added a quick disconnect. You can do this too if you feel up to the task, but I recognize it's unnecessary.
Regarding why I did this, the two ground cables are pointless. One is redundant for the vast majority of people. 0 volts is 0 volt (working with low potential differences and short distances), regardless of if that's at the frame or the negative side of the brake light . So you can connect both negative wires from the controller (the one going in, and the one going out). In this case I decided to do it inside the little controller's box, and then encapsulate it again for waterproofing.
The encapsulation (also known as potting) was done with MG Chemicals Thermally Conductive Epoxy. The stuff is great for protecting electronics from humidity in motorcycle or automotive applications (especially HID ballasts). It's the type of stuff that once you try, you'll find use for elsewhere if you're an avid DIYer. Just mix the stuff like epoxy and pour it on whatever you want to protect.
If you don't feel like complicating yourself that much, there is an easier product for protecting electronics from moisture. It's called a "conformal coating", which you simply paint on. I like MG Chemicals Silicone Modified Conformal Coating and if you want to buy just one, the conformal coating is probably more versatile, albeit less protective.
After that, if you still want to add the quick disconnect, great. Just crimp on the connections and plug the terminals into the housings. I like soldering the wires to the terminals just for better reliability.
Step 3: Locate the Brake Wiring
I will be doing this installation on a 2017 Kawasaki Ninja 650 ABS, however virtually everything will be applicable regardless of the motorcycle in question. For the most part, it even applies to cars.
The first step will be to locate your tail light wiring. On most sport bikes like this one, it will probably be readily visible if you simply remove the rear seat. I removed the left side panel to make things easier for myself, as well as to store the brake light controller there. What you'll have to move or remove will vary on your bike.
Step 4: Identify Which Wire Is Which
The brake light will probably have 3 wires coming out of it. One will be ground (permanently at 0v respect to the chassis), another will be your position light wire (0v at bike off, 12v with ignition on), and the last wire will be the brake lightwire (12v when either brake lever pressed, 0v if not).
To measure this, unplug your brake light (there should be a connector somewhere near the brake light. Follow the wiring) and measure the voltages on the connector. You only need to find two wires - Ground and Brake Light.
Ground will probably be black. If you set your multimeter on "continuity", it should beep (or show 0 Ohms) between ground and any uncoated bolt on the frame (or your batteries negative terminal).
Next turn the ignition on. You'll see that one wire is always 12v. That's your position light. You can leave it alone.
There should be one wire remaining. That is the brake light. Double check it measuring the voltage while pressing and releasing either brake lever.
Step 5: Cut the Wiring and Make the Connections
In order to make the connections, you'll have to "tap" one wire, and cut another.
First, the ground wire. Don't cut this wire. Simply use the hobby knife to strip some insulation (without cutting the wire!). Then separate the metal wire strands (poke the point of the hobby knife in the middle, then rotate it) to make a loop. You'll connect the negative from the brake controller here. Thread the negative wire from the brake controller through the middle and twist it around making a solid electrical connection. Since you can't use heat shrink here, I recommend using liquid electrical tape to protect the wiring from wicking up water (which leads to corrosion - a big issue on motorcycles).
Next, the hard part. You're going to have the cut the brake light wire. I recommend doing this on the pigtail going from the brake light to the electrical connector so that, if for whatever reason you wanted to leave the bike totally stock, you could simply replace the brake light and remove all traces that it was ever there (electrical warranty work?). Then, remove some insulation off both sides and slip on the heat shrink before making the connections (if you intend to use heat shrink - I'd recommend it, though).
Before actually making the connections permanent, test the controller to make sure it works. Just in case the wires were misidentified or connected wrong. Just wrap the cable ends together (but make sure they don't touch each other) to test for a moment.
Once you've made sure it works, make the connections permanent, and protect the wiring. If possible, solder the connections. I like to do so to make sure they are reliable, however it requires careful technique. If you aren't familiar with that, learn more about crimping versus soldering before proceeding. Especially on something as important as a brake light. However, I'd be naive if I didn't at least let you know that many people (and shops, for that matter) would probably use the cheap and quick options - Electrical Splicers. All you have to do is insert the wire and push in the metal tab with pliers. They work well enough, but are not 100% reliable and are pretty bulky. I don't love them, but sometimes I use them if the situation is right.
Step 6: Test It!
And surprisingly, that's it! Test for functioning, and post an image of your bike below to prove you did it!
Anyway, thanks for reading my Instructable! Check out my profile to see what other projects I've been up to — here are some others you might like:
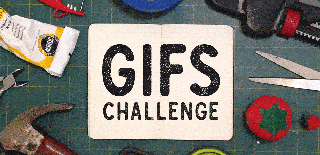
Participated in the
GIFs Challenge 2017
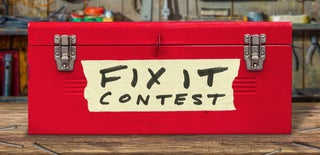
Participated in the
Fix It Contest