Introduction: Breadboard Training Lab
If you design electronic circuits, chances are that you've tested your design out on a breadboard before finalizing your PC board layout. Over the years, I've used all manner of breadboards. My dad even built a custom one for me on a beautiful wooden base. With more than one project always in the making, I found that I needed to have more than one breadboard on hand at any given time. I've always liked my HeathKit ET-3400 digital training lab, but I wanted something a little more modern. I based my breadboard trainer design on that lab, right down to the color scheme. As with most [all?] of my projects, nothing is critical and I encourage you to make it your own!
I built this several years ago and, back then, I usually only took finished photos of my projects. I never thought I'd be sharing the build details with others. Luckily, in this case, I still have the original SketchUp design that I did so I was able to explode that diagram and show the various steps that I took in building this.
Materials Needed:
- 1x6 pine board
- 1/4" oak plywood
- paint and/or stain
- and assortment of screws
- mini ATX power supply
- mini LED panel mount voltage meter (eBay - under $3 from China)
- solderless breadboard x2 (MB-102 type or similar)
- rocker switch
- LED
- banana jacks x2
- binding posts x4
- serial LCD module (or 8/4-bit module with serial adapter)
- microprocessor dev board - TI Launchpad (or your preferred board)
Step 1: Cut the Wood
Using the diagrams, cut the 1x6 board to the dimensions shown in the first photo. I know that the diagram shows these pieces as being 1/2" thick. Ignore that. They are actually 3/4" thick. The angles for the two main panels are pretty much arbitrary. Make sure that you cut a 1/4" slot along the inside bottom edge of the front and the back plate as well as the inside bottom edge of each side plate. On the side plates, leave about 1/4" on either side of the groove uncut since this edge would be seen as a hole once everything is assembled. These grooves exist so that the bottom plate will mount flush. You can route the edges of these four pieces now if you'd like.
From the 1x6, you will also need to cut the supports shown in the second photo.
The top plate, the bottom plate, the breadboard panel and the power panel are all cut from 1/4" oak plywood using the dimensions shown in the third photo. You will need to bevel the top and bottom edges of the power panel as well as the front edge of the top panel so that when mounted, they will all sit flush. This was pretty much trial and error for me.
Step 2: Drilling and Cutting
Using the components you've selected as a guide, cut and drill mounting holes for the LCD panel, the LED voltmeter, the binding jacks, the banana jacks, the power switch, the power LED, the cooling fan, cooling vents and the power jack. For my build, I used small, 4-40 standoffs to mount the LCD panel and the voltmeter. Of course, depending on your particular needs, you may have more or less that you have to cut. I had planned on adding a small speaker, myself, but I haven't got around to that - yet.
Step 3: Building the Box
Glue the front plate, the back plate and the two side plates together to form a nice little box. You may also want to use a couple of brad nails in each joint for added rigidity - I know I did. Now, we need something on to which you can screw the breadboard, bottom, power and top plates. Glue the support pieces in as shown. The four upright supports are glued into each corner. The back support and the four side supports are all glued to the box a half inch below the edge. Once the plywood pieces are screwed down to these supports, they will be recessed down about 1/4" inch.
Place the plywood plates in place and drill pilot holes for the mounting screws as shown. Take the plywood off and enlarge the holes so that the screws just barely drop in. I found that the pilot holes would strip very easily since I am using a soft pine wood. My solution for that was, after carefully inserting and then removing each screw, to place one drop of liquid (not gel) Super Glue into each hole and smear it around (relatively quickly) with a straight pin. This is absorbed by the wood and makes it a lot more sturdy. Don't put the screw back in until the glue has fully dried, though, or you will not be able to remove it!
Step 4: Building the LaunchPad Carrier (optional)
My favorite microcontroller to work with is the Texas Instruments MSP430. For programming, I use a cheap (<$10) "LaunchPad" development board. The only problem with this is that there are no provisions for mounting this board, so I had to improvise a carrier into which the board could slide along slots.
The photo shows the dimensions. Basically, the base is a 2-1/2"x3" piece of 1/8" plywood. Each of the rails are 3/8" square with a 1/16" deep, 1/16" slot cut 1/16" below the top of the rail. As you can see, this leaves a square hole on each side when the pieces are glued up. Before painting, you can fill this small hole with wood putty.
You can either glue this carrier to the breadboard panel or you can screw it down. If you choose to screw it, be sure that you drill countersunk holes into the base of the carrier and be super duper sure that the screw heads cannot possibly make contact with the dev board.
=[ UPDATE ]=
... or if you would rather... I have designed a 3D printable model of the carrier. I will upload the file here, or it can be downloaded from Thingiverse. Please note that this .stl is in inches, not millimeters.
Step 5: Stuffing the Box
For this step, you will need to cannibalize an ATX power supply. Once you have removed the complete power supply from the case, you'll want to remove (desolder) all of the computer power wires, only leaving one each for +5v, +3.3v, +12v and ground. As you can see from my photos, once you have decided on a mounting location for the circuit board, you may have to cut the heatsink(s) down to fit underneath the breadboard panel. I had to cut mine down at an angle. Leave as much as possible to help with heat dissipation.
Mount the fan and fan grill. I used a piece of scrap screen wire for a grill on mine. The vent cover was made by cutting the original case's vent slots out as a panel and then screwing that over the vent opening on the back panel. Mount the AC power jack to the back panel.
Mount your LCD panel (if used), the mini voltmeter, banana jacks, binding posts, power switch and power LED to the power panel.
Wire everything together.
Mount your LaunchPad carrier (or the dev board of your choice) and the two solderless breadboards. For mine, I first screwed the breadboards to a metal plate which I then screwed to the wooden panel. Obviously your mounting needs/methods may vary.
Step 6: Making It All Pretty
My way of doing things may seem counterintuitive, but... it works for me.
Now that everything is mounted, I took everything back off to colorize the trainer. Why didn't I do the color first and then mount everything? I didn't want to risk scratching the paint/stain trying to locate everything. But that's just me. Work your own method of madness :)
So, once I took everything back off, I painted the top panel, the power panel and the breadboard panel with a matte finish, off-white acrylic paint. I then stained the back panel, the two side panels and the front panel with a couple of coats of custom-ordered, "Island Water" blue, water-based Minwax stain over which I applied two coats of polyurethane.
Once everything has dried, all of the panels are screwed back together.
Your breadboard training lab is now complete.. or at least it is as far as I've gone. I am sure that you will want to add additional features/functions to yours as needed. I encourage you to share photos of your build here so that others can get ideas for their own. Hopefully, you got something out of this instructable. Until next time...
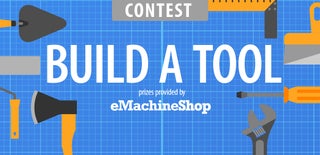
Participated in the
Build a Tool Contest 2017