Introduction: Briar Smoking Pipe / Bowl
I'm not a smoker. I've never been attracted to that kind of physical entertainment since I'm just deeply addicted to fresh air. And I presume that with all the bonfires I've made I already have been cheating enough to my lungs. Nicotine is no friend of mine.
In fact, I should say that I'm not a smoker in the 'regular meaning of the word'.
I do smoke, sometimes, though, but only sweet potatoes.
I like sweet potatoes. They're a peaceful tool to relax and to relativise a lot of the crazyness of this life. Sweet potatoes are a natural product, by using them you're doing no harm to anyone, and like any other vegetable using sweet potatoes shouldn't be an excuse to get rid of any form of responsibility. No working with heavy machinery, for example, no driving and no complicated heart-surgeries combined with them. It's all about common sense, you know. Enjoying, sharing & celebrating life & the good things.
Most of the time I mix those sweet potatoes with some tobacco in a lovely handmade cone, but since I'm a woodworker & someone who thruly believes that the making makes at least half of the pleasure, I wanted to make my own sweet potato pipe - or 'a bowl', as they call it.
Step 1: Getting the Right Stuff
You can make pipes from a lot of wood species, but I learned that the good ones are made of tree heath - Erica arborea, also called 'briar' ('bruyère' in french). Not the stem is used, I mean the stuff that's above the ground, but the root aka what's IN the ground.
It's loved by pipe-makers since this root is hard, fire resistant and extremely beautiful. Since the plant grows on acid soils it's not easy to find and thus expensive, which is why pipe makers also use cheaper woods.
Erica is a plant of the old world - Eurasia & Africa - and in particular for the Mediterranean Bassin. I've no idea if the plant has been taken to the other side of the Atlantic.
Those briar roots aren't like those of any other wood species. They're made of large, meteorite-like devices called 'burls'. These serve as a sponge for the plant to survive the dry climate. They absorb water, and minerals, in the wet season and release it gradually during summer. Those minerals make the burl - almost - fire resistant. Briar burls are magic pieces of art.
Of course I could have chosen cherry to make my pipe, but why play easy if you can play hard?
You know, a few years ago we lived in southern France, and during our hikes in the eastern Pyrenean Mountains I already had noticed some of this Erica, without paying too much attention to it.
Untill I decided to be a pipe maker.
So I went back to that hot spot on the hills and started to dug out those burls. I had never seen these things before, so when I got the first appearance of what seemed like a really big concretion I completely freaked out. It may seem weird, but if so it's clear you never had that feeling of being in the mountains and harvesting a thing that had been hidden for maybe 100 years or more in the ground.
So I harvested a few very nice burls, put them in my backpack and went back on the track, enjoying the scenery & the wildlife of the autumn in the mountains.
Step 2: Boiling the Burls
First thing you do when you've become the lucky owner of a few fresh briar burls is to wash them to get rid of the soil and, more important, to boil them. Most pipe-makers cut the burls into workable pieces before boiling, but I don't think that's really important.
Put them in bowling water to leach out the tanines. For some reason you don't want them in your pipe. One reason might be that 'they affect the taste of the smoke'.
The boiling water will colour brown and your kitchen will be loaded with the smell of cabbage. Or worse, bad cabbage.
Keep changing the water till it stays clear. That means that the last taniner has left the house.
Pictures:
A few of the harvested - already boiled & dried - burls. Sometimes you just have to be on the right moment on the right place. I lost the pictures of the boiling process, but I guess you all know how a big bowl of water looks like ;)
Step 3: Drying
Store the burls in a non-ventilated humid area.
You read it well.
They have to dry very slowly to avoid cracking. Spray them moderately with some water - obviously - every day, turn them regularly and repeat this process until they're completely dry. You'll notice that gradually they will get covered by some moisture. Don't worry, that visitor is a partner in the game.
The whole process can take several weeks or months. I did this for almost 6 months untill I felt that the biggest burl was ready to get processed. Patience is the partner of the pipe maker.
Picture: 'pourriture noble' ake noble moisture...
Step 4: Intermezzo
Instead of continuing right away I set the project aside and went on other challenges. We left southern France again and moved back to the north of the country. And all those burls went with us.
I forgot my pipe project for a while, and it's only a few days ago I found them accidentally again in a forgotten toolbox.
Time to set the project back on track.
Step 5: Faceting
Contrary to most other projects, this one doesn't start with a nice design. You have to make the pipe in function to the burl, and therefor you need to know how much workable 'meat' you've got.
Those things are very irregular, you know, and so you've got to cut away the ribbled stuff to see how much solid wood is inside.
If you have a bandsaw, fine, go on. I don't, so I used a disc sander and I really believe it's the best tool to use with smaller burls like the one on the pics. With a sander you can remove precisely as much as you want until you've got a facet without cracks, intrusions or holes. Impossible to do it right first time with a bandsaw since you just can't see inside the burl. Sometimes those natural cracks go all the way through the middle.
Use the tool you feel best, and try to get a nice solid block out of that burl.
Step 6: Rays & Rules
Before you'll starting to drill some holes in your workpiece, you need to know it better.
You know, if you cut a briar burl in half you'll notice a constellation of rays going from the center to the outside. To get the best visual benefits from your pipe those rings have to follow the 'way of the smoke' aka from the chamber to the channel. There seems to be a rule in pipe making that 'the outside of the burl is also the outside / upside of the pipe'. Look at some minimalistic pipe designs, you'll notice the 'raw' surface of the burning chamber. That's the area that was in contact with the soil, obviously.
To know how these rays go you just have to wet the surface slightly with some water.
Enjoy the scenery.
Pictures:
On the first pics you see a burl I just cut open for science. Notice the complex structure of the briar, the cracks and the beautiful natural artwork.
On the next pics you see my workpiece with some water to it to visualise the nice pattern.
Step 7: Chamber & Channel
A pipe is quite a simple device. It's just a burning chamber and an exhaust channel with some wood around.
I know, there ARE more complex pipe designs but I'll stick to the minimalism here ;)
Before you're gonna design the pipe you need to drill those 2 cavities.
The base of the burning chamber needs to be 'bowl-ish'. Not flat, I mean. Flat burning chambers are less effective than round ones since you won't have full combustion, and dirt will get stuck in the sides.
Try to get it round, and use round drill bits. No forster bits or paddle bits.
I used a conic drill bit but round router bits ar just perfect. Some pipe makers design their own bits starting from a paddle bit.
Drill the chamber first, before the channel.
Diameter chamber: 20mm.
Diameter channel: 6mm.
Use a tower drill to get it precisely. I did it freestyle - I just felt it was gonna be my lucky shot - but the chances on failure aka not matching the two holes are extremely high. Work miticulous, and do not like me...
Whatever, I did have my lucky shot. See that last picture with the light inside. Bulls eye in the pipe!
Step 8: Raw Design
This step is as optional as can be. You don't need a nice design, you just need a good pipe.
Again, it's the burl that will tell you which way to go, at least with smaller burls.
It was gonna be my first pipe, so I choose a very minimalistic design: a round burning chamber and a nice conic channel.
Use a band sander mounted upside down. You've got no idea how much this setup pays to sand nice & straight. I started with a heavy grit of 40 and once I got the brutal shape I changed to 120.
Step 9: Finer Sanding
Sand as if it's your last day on earth.
240, 400, 600 & 800.
Every time you mount on grit level the design of the briar will become more appealing.
Step 10: Oiling
Sweet satisfaction at the end.
Walnut oil.
Let the magic begin.
Step 11: Glamour Shots
I just hàd to show you these pictures, because this briar is definitely one of the most beautiful woods I ever worked with.
If it were a sword we would say that it's 'kissed by the flames'...
But it's no sword. It's a pipe, dude.
But it will be kissed, definitely.
Step 12: Not an Addict
Fill the chamber with some sweet potatoes and enjoy the moment.
Can't wait to test it for real...
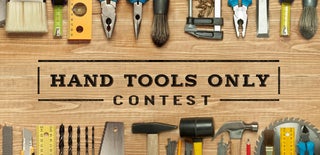
Participated in the
Hand Tools Only Contest 2017