Introduction: Budd Lugnut Knob
In the past, most of my Instructables have been more function over form. Frankly, I have to admit the fact that viewing many other Instructables that are so overly the top awesome and just generally well thought out has changed my outlook on this project. I wanted to shift the ratio and do something that was somewhat a mixture of form and function.
Step 1: The Problem
The main reason this is even an instructable in the first place is the problem. That problem is, the drill press I have at home doesn't have any knobs on the handles. I don't know why...I don't know how...I don't know...I just don't know. Just like how I can't tell you how the table ended up with so many holes drilled in the table, I can't tell you the reason the knobs are missing, they just aren't there. All three (**four) of them. Its very uncomfortable to use, so consequently, the machine doesn't see a whole lot of use. (Honestly though, who would knowingly drill a hole straight through their project into the table?? Repeatedly?? Previous owners, that's who...)
The second part of this problem is the drill press I use almost daily in certain times of the year at work, has handles, but when you focus in on them as opposed to the drill press itself, they're really rather cheap and plastic. I suspected this was going to be the replacement option from most drill press manufacturers. I didn't even research this because I knew I was probably going to be unsatisfied with putting new plastic handles on an old drill press.
So now there was this situation where there had to be something that would look better than a plain ol' plastic knob that would probably cost too much for what it really is. But it couldn't just look better, it would have to work better and add some character. Originally, since this was located in an automotive based shop I thought maybe just...different shift knobs. Well its a cool idea, but I could only find two shift knobs floating around and making thread adapters or cutting the handles and re-threading each with the right thread for the shifter knob just seemed like maybe it wasn't the right fit this time. Then it hit me. Maybe I could use old lugnuts and craft my own handle. So this is my take on something creative and artistic that had form and function; a basic knob on a drill press. I took a lot of pictures so be sure to look at all of them if you get lost and hopefully things will make sense.
Step 2: Source the Materials
The drill press that needed knobs for the handles had a 5/16" NF (national fine) thread. Whatever you might make this for will most likely have a different thread, so check that out. If it happens to have 5/16 NF, then you're in luck! This is what you'll need for each knob.
- 2 of 5/16" NF nuts. 1 for each knob and 1 for the making that should be able to be reused a couple of times.
The lugnuts I used were old, rusty and of surplus in a size that doesn't fit our trucks. 3/4"-16 I believe by measurements that I took. Not totally sure on the sizing but they are Budd on the outside. If you're reading this and are wondering what I mean by Budd, its a type of standard truck wheel that is stud piloted due to the taper on the lug nut. A 1.5" socket fits the nuts.
- 2 of old stripped or rusty, unused Budd Lugnuts. You could easily substitute these for new ones although..I would almost be willing to bet if you stopped by a local tire shop they would probably have a pile of stripped Budd Lugnuts if they service truck tires.
- 1 of 5/16" flat washer (preferably used)
- 1 of 3/8" flat washer (preferably used). I originally started out with all 5/16" flat washers but then some tinkering made it better to use the bigger 3/8" washer instead.
- 1 each of a 5/16" NF bolt and 3/8" NC or NF bolt & 3/8" nut to match. Each about 1" to 1.25". The length is not super critical. These are just to jig everything up.
Step 3: Clean Your Parts
I threw my materials in the sandblast cabinet for a quick cleaning. If I didn't have that option, I would use the wire wheel on a bench grinder or a 60 grit flap disc on an angle grinder.
Step 4: Start by Making Some Captive Nuts
So it just so turns out that a normal 5/16" flat washer fits almost perfect in the interior beveled edge of this budd lugnut. When I first tried it, I knew then this project had to happen.
Grab that 5/16" NF bolt and stick it in the vise. Run one nut down a ways, enough so that you can fit a flat washer and another nut on top to hold it in place. Then, with the whole assembly snug, you are free to weld the washer to the nut.
Repeat times three (**four). Then clean them up a bit with the wire brush.
Step 5: To the Press!
Being that this was all relatively something I just dreamed up and didn't really do much planning, I ended up coming up with other ideas in the process.
One of these ideas was to concave a washer in the press to make a dome shape that would better suit the top of the knob. I started out with 5/16" flat washers but then switched to 3/8" washers because the concave shape shrinks the circumference of the washer just enough so that the 5/16" washer no longer fit how I wanted it to.
The first four pictures show the process with a 5/16" washer. The next two show the difference in size between the two. The last four show the 3/8" that I ended up sticking with because of the fitment.
Either way I used the same process to press both size washers. Center the washer in a used 3/4" nut in the press with the proper size bolt (In this case 3/8") in the hole and run the press down to concave it. This worked surprisingly better than I thought it would.
I got three of 3/8" flat washers to match concave wise and they fit perfect.
Step 6: Tack Everything Up
When I first started welding, I tended to tack something together and then weld it up. Now I prefer to just get everything tacked together and then take my time with the welding. It makes for getting all the squaring and measuring out of the way first and then all that is left to do is weld everything up. Then... wait for it to warp. At least distortion won't matter too much in this project.
Start with a 3/8" bolt and square it in the vise. This is the easiest way I found to jig everything up. Run a nut down a ways on the bolt and then put a lugnut over the bolt onto the top of the vise. Now slide a washer down onto the 3/8" nut and you should be able to adjust the washer so that it just has a slight gap above the lugnut. This gap is important because it will allow the weld (once ground down) to make the perfect transition between the taper on the lugnut and the dish on the washer.
Once you're set, run another nut down to keep the washer in place and make sure everything is centered (I honestly just eyeballed it) then tack it up.
Repeat times three (**four).
.
Step 7: Tacking Part Two
For part two you will need the 5/16" NF thread bolt again.
Square the bolt in the vise. This time it has to count because squaring it will ensure that even if the welded washer is slightly off, both nuts will be parallel and square with the vise. This means that your knob will thread down evenly and not all wobbly.
After placing a lugnut over the bolt, run a captive nut down the bolt with the nut facing downwards. I aimed to get the washer level with the flat spot on the lugnut. Center everything up and then run another nut down on the bolt to protect the exposed threads from weld splatter.
Repeat times three(**four).
Now you should have three of each lugnuts. Three with captive nuts and three with concave washers.
Stay with me, it will start to take shape.
Step 8: Time to Weld
Here is a tip. When welding captive nuts to, anything really, if you put the slightest bit of nozzle dip in the nut with the bolt threaded in there, it seems to eliminate any splatter effecting the threads. It does tend to start on fire though so don't use a lot. A little goes a long way.
Proceed to weld all of the tacked parts thoroughly. The pictures explain pretty much. I ended up using what I call a constant tack method where I kind of just make tacks but continue onto the next tack before the last one cools down. Its really pretty fast and a tid bit more accurate than trying to lay a constant bead in this case.
Repeat times three (**four).
On the concave washer lugnuts you will need to weld up the hole as well. This might take a bit of practice and patience if you're a beginner. Don't worry if the welds don't look perfect. Good penetration and fill material is what you're after.
Repeat times three (**four).
Step 9: The Grind
When you're all done welding I suggest you take a break and let everything cool down for awhile. After things are cool, you can start the grinding and shaping process.
For the captive nut side, I ground down all the welds flush and then gave it a quick flapper wheel to smooth it up.
For the concave washer side I basically did the same only being very careful not to go to far with the grinder. The flapper is a little easier to go slowly on the basic shape you want.
Basically I just got things to the rough shape I wanted.
Repeat times six (**eight).
Step 10: Taking Shape
I made sure the areas to be welded were clean with a quick flapper pass on the edge of the lugnuts. Then it was time to get them tacked together.
For this you need one of each captive nut side and a concave washer side. Both should face in opposite directions with the flat side of the lugnuts facing each other. I clamped them to my bench with an approximate 3/32" gap between them. This was so when I welded them and ground them down, there would be good weld still there. Square them up as best as you can, clamp them down and tack them up.
Repeat times three (**four). When you're done they should look like the last two pictures.
Step 11: Weld the Two Halves Together
Take your time alternating to opposite sides as welding these together will create quite a bit of heat. This step is pretty explanatory though. If you made it this far, you're getting close to a rad drill press knob.
I placed them on a scrap piece of tubing to cool so as not to create a hot spot in my bench.
Step 12: The Grind (Part 2)
Okay so now that they are cool, you can use the 5/16 NF bolt to hold it in the vise to grind the side welds down to smooth. I went carefully with a grinder down close to flush, then finished with a 60 grit flapper to blend the welds in.
This process took a long time, but mostly its just tedious. Get a pattern down and be patient. Grinding and blending 18 (**24) short welds isn't that bad...(haha!) If you did a good job welding then it should blend fairly easily.
After that was done they were close to the general shape that I wanted but not close enough to the look. They still needed some final polishing.
Step 13: The Rather Dubious But Totally Worth It Step
I know I will probably catch a red flag from the safety police for this step, but honestly I've seen worse. I'm by no means suggesting this is how you should do it. I'm just showing how I did it. And how I did it was very carefully and full of common sense. By all means if you had/have or have access the proper tools (like a lathe), you should probably take advantage of that. I didn't and so this was my next step.
Take your trusty mock up 5/16 NF bolt (which by now its probably almost worn out) and cut the head off. Then grind two flat spots on the end of it so as to hold still with a crescent wrench, pliers, vicegrips, etc. Thread the bolt into the knob and tighten the lock nut so it looks like the fourth picture. This gave me enough to chuck the assembly into the same drill press I was working on in the first place.
With it chucked into the drill press on a slow speed, I made sure it was spinning "centered" and not wobbling around. Then, with it tightened it up good, I turned the drill press on and carefully, lightly, and slowly used the same 60 grit flapper wheel on an angle grinder to polish the dome in more uniform manner. The results were more what I was after than what I started with.
If you have any porosity at this point, it will show up. If that is something that is of concern to you then I would suggest grinding it out and fixing it before you get to this step. If you look closely, some of the welds ended up with some porosity and I can only attribute that to poor cleanliness. I'll admit, it bugs me a little bit to see porosity in my welds because usually it isn't there. Honestly, I'm not heartbroken about it because I was kind of going for a one piece cast look that wasn't perfect, identical, or symmetrical. It suits the character of this drill press better anyway. Lesson learned.
Step 14: Finishing (Optional)
So after the somewhat final polishing was done I decided that they looked pretty good but I still wasn't totally satisfied with the look. They were almost too shiny, if that's even a thing...
I considered clear coating them as is to prevent them from rusting but like I said earlier they kind of stood out too much and needed to be darker in my opinion. I considered painting but I just wasn't feeling it because they look so cool in their natural state. I finally landed on the idea to follow chocolatebrownies Instructable to color them with heat. I hadn't ever tried it and it looked cool so I gave it my best shot. I pretty much followed the instructable besides I used some straight 30w I had and did not use unleaded gas for a solvent.
I heated to a dull (really dull) cherry red with a oxy/propane rosebud and then dunked in oil and let set for awhile. Two turned out pretty nice the other one flaked off kind of severely as you can tell in the intro photo and some of these. Coincidentally, that one happened to have the most porosity. Not sure if that was related or if it was just because it was the first one I did and the oil was cold. Again, I'm not too bitter about it because it still looks cool and I could always refinish it in no time should I feel the need to.
The final step for me was to use my 60 grit flapper to take down the sharp edges and add accent lines in one step. There was still some oil residue left over from the coloring process even after cleaning them with solvent so I left it to keep the bare spots from rusting. I like the way they turned out and they work awesome.
Step 15: Make Sure You Count How Many You Need Before You Start...
If you noticed in the last step that all the handles didn't have knobs on them...well.
**Originally my plan was to make a smaller knob out of smaller lugnuts to match the design for use on the table height clamp. I thought this size of knob was going to be too big for that handle but as it turns out, it couldn't be a better size in my opinion. After making these and using them I've decided to put the most worn looking one on the table height clamp handle, then make one more now that I know how to heat color them better and hope that it matches the other two on the press handle.
I did just that (eventually) and I really couldn't be happier with the way they turned out. They look awesome, they feel better and solid, and of course they are the product of reusing things that in all honesty would've ended up going to get recycled. The last four pictures show the how they look on the drill press.
Thank you for checking this out!
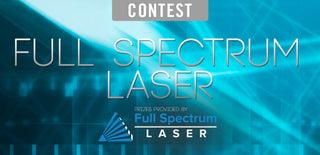
Participated in the
Full Spectrum Laser Contest 2016