Introduction: Scrap Shop Dolly
You know how when you feel like doing something? I started this project feeling that feeling with the only prerequisite being that whatever the project was, had to be easily accomplished.
I use Harbor Freight furniture movers to move smaller 4 cylinder engines and transmissions around the shop as needed. Not an advertisement, just saying. This particular day I needed another dolly to cart a removed transmission around the shop, while the new transmission waited patiently on its own dolly during preparation for installation.
I had 4 casters awaiting their use on future project, but I needed this dolly temporarily. Then the rest of this happened.
Step 1: Intro Part 2
The Harbor Freight furniture mover comes at a local branch in two sizes, both at a very cheap price. They can be handy for shop uses in such tasks like I've mentioned with small motors, transmissions, sets of tires, etc. with a pretty good weight handling capability (the one in the picture claims 1000lbs capacity but somehow...I'm skeptical). That being said, for shop use, in my opinion they're far from ideal.
The design is basically four 3/4" boards, albeit hardwood boards, with two parallel overlapping the other two parallel and a big hole in the middle. I usually put a piece of plywood (or in this case osb) over these before I set a motor or transmission on them to provide a good level base but then I also need a shim underneath in the middle section to keep the top plywood from sagging. That notion got me thinking. Why don't I just build my own with a top deck included in the design? Why not indeed. As an added bonus this design will match the pair of Reclaimed Step Stools I made in a previous Instructable with some of the same scrap materials used for construction.
Step 2: Find Materials and Mill to Dimension
This Instructable is roughly based off of the smaller Harbor Freight furniture mover but only in the fact that its a dolly and somewhat dimensionally. The Harbor version I had as an example was the smaller version, measuring ~11.5" X 17.7". The one I'm making in this Instructable will be a full 12"x18".
All of these materials came out of my off cut scrap pile and consist of your basic 2x4 and 1x4ish stock. I say 1x4ish because most of these were broken or previously ripped smaller.
On a tangent, I still have loads of this 1x4ish material somehow. I keep trying to come up with new projects and ways of using it and it multiplies or something, I can't ever seem to use it up. This is literally the 4th project I've made entirely from the scraps of the original boards from a shelving project. It didn't even seem like there was that much in the pile when it was made initially! I don't know whats going on...
Regardless in order to make this dolly you need:
(2x4) >= length of
- @ 12 "
- @ 18"
(1x4ish) >= length
- @ 12"
- also enough to make a total width of 18"
In addition to cutting the 2x4's to consistent length across each pair, I planed them all down to a consistent thickness and to clean them up just to make the next step easier. I think that the thickness I ended up with was about 1 3/8". With the thicknesses close to the same, I ripped one edge off square and then ripped all the 2x4 boards to a 3" width with the square side up against the fence.
I ripped the bad/broken edge off of a bunch of 1x4ish boards, cut them to length, and picked out the best ones to use. I could then sort and set aside enough boards to end up with the total width (18") I needed for the completed dolly.
Initially I was going to work with the original shiplap section that the boards had on them. A lot of them were in poor condition and it was at that moment that I thought, why not rip them all to a consistent width and then cut my own shiplap? Why not indeed. Not constrained by the original shiplap sections, I ripped the remaining boards that were wide enough to a consistent width of 2.5". Later on I would realize that after the shiplap was cut, this would leave me short total wise. I just added one more piece in the end, no biggy, just something to think about.
Step 3: Cut the Half Laps
The half lap joint is pretty simple and strong. I'm using it in this application because it will allow me to join all of the frame pieces together with the end result being on one plane. This will accept the shiplap top deck splendidly.
I cut all of my half laps on the table saw using the nibble technique with a normal blade. I call it the cheat nibble technique where each cut is about an 1/8" apart and then you can snap off the remaining pieces that stick up with your fingers and trim the area flush over the saw carefully. Another option for this step could be a dado blade or I would imagine a tenon jig even.
However you decide to do it, the length of the half lap should be the same as the width of your stock and likewise, the depth of the half lap should be half of the the thickness of your stock. This should ideally always be done on a measure and check basis just to make sure you've got the lengths and depths dialed in before doing 8 cuts. I pretty much measured once and just went for it. It turned out pretty satisfactory.
When you're all done the pieces should look like the 2nd picture and fit together like the 3rd picture.
Step 4: Cut the Shiplap
Cutting shiplap is actually pretty easy once you've got your table saw dialed in.
The goal here is to cut half the thickness of the board as a saw depth, and half the thickness of the board set between the blade and the fence. So the key dimension in this step is half of the thickness of the board.
It took me a few passes on a scrap to get this setting close. I never planed these boards so they're all hypothetically slightly different thicknesses. That affects the accuracy of the cuts some what. Again, its best to set it up close and double check to avoid making a mass error.
Once set up, I ran all the boards through edge ways first on one side. After that was done, I could flip the board flat on the table saw and cut the final cut for that side.
On every board besides the end pieces, each edge got an alternating cut as illustrated by the picture. I'll add some text to the photo to clear this up if its confusing when you read this.
That completes the shiplap procedure so that these boards will overlay each other. Nothing better than fresh homemade shiplap. One thing to take into consideration on this step is that the use of a featherboard would most likely result in more accurate cuts, especially on longer pieces. My pieces were only 12" and I didn't have many to do so I didn't bother with a featherboard.
Step 5: Glue Up
Spread glue over the half lap areas, put the frame together, and double check squareness. Square is not super critical in this application, but its always good to practice when building anything. If the pieces are cut equally and the half laps are accurate you should be pretty close to square anyway.
I used two 1 1/4" #8 screws in each corner and a clamp while the glue dried. At the time I literally only had 9 left in the package otherwise each corner probably would've gotten 4 screws and no clamp.
Step 6: Add the Shiplap
This is pretty self explanatory, however, I did orientate the frame so that the longer sides were on top of the shorter sides half lap wise.
As far as the shiplap goes, I started on one end parallel to it and made sure I was staying parallel across the whole frame. The boards don't have to be super tight fitting together either. In fact, I left a little breathing room between them just because. I just used a few 1 1/4" 16 gauge brad nails to affix them to the frame. I believe I shot two in the top and one through the shiplap. Seeing as the boards mainly just have to stay in place and most of the forces will be downward on the dolly, I didn't see the need for a stronger fastener.
I chose to run the shiplap in the shorter dimension because I could use more short pieces up and I felt like the more shiplaps, the stronger the top. Each piece is supported by its neighbor and so on, its surprisingly rigid when fully assembled. I feel like it would take a lot to break it.
When I got to the last piece, I ripped it to size for a perfect fit. You could just as easily, affix it and then trim it off as well. Or you could just cut a piece of 3/4" plywood to size and never think twice about any steps dealing with shiplap period. You do you. I'm trying to use some scraps.
Step 7: Add the Casters
This is kind of the frustrating part of the whole build. 4 individual casters cost more than a complete pre made dolly with 4 casters on it.
That's okay because these casters have the potential to be made of better quality than the Harbor Freight furniture dolly caster, if you make it so. Mine were most likely still originally bought from Harbor Freight...sigh, again not an advertisement by any means, just saying. The thing was, I had the casters, but needed the dolly.
So basically, I just put them at each corner, with the pad centered within the shorter 2x4 ends. I was mainly paying attention to leave enough material for the screws to sink into without splitting the wood. Once that was done I could mark and pre drill some holes. I attached the casters with lath screws because the wide head barely spanned the holes in the mounting pad. I would normally use lag screws with washers for this, but didn't have enough and didn't want to use screws with separate washers. It should be fine for what I'm using it for. I could always change it later.
Step 8: Use It!
This dolly easily supported me jumping on it (ballpark 190lbs same as when I tested my Custom Wooden Crutch) and skating across the shop. With the lath screws the only thing holding the casters on I didn't want to put any more weight on it but, it supported a GM 4L60E with the torque converter and some residual oil left in it (ballpark 180-200lbs), which is what I made it for, with no problems at all. I can move it around effortlessly when ever it gets in my way.
And there you have it! Now you can build you're own awesome looking heavy duty shop dolly and hopefully reduce your scrap pile. I would imagine that this idea could be expanded and adapted to the exact size of what you needed it for as long as the appropriate framework was made and casters were rated for the weight.
I hope that this helps or inspires you in one way or another. At the very least, I hope you enjoyed reading along. It was a fun easy build for me and helped in keeping the shop productive and organized. Thanks for checking it out!
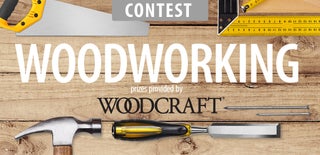
Participated in the
Woodworking Contest 2017