Introduction: Build an in Ground Swimming Pool
Hello and welcome to another insanely awesome Instrucable on doing something incredible.
I'm Sam, I'll be your guide to do something you thought you would never do: build and install your own in ground concrete swimming pool! We aren't talking a silly above ground pool you bury, we are talking custom 15,000+ gallon dream pool! Follow along as we learnt to build a pool in just 8 easy steps.
For this project you will want some basic tools that you most likely already have, some tools you didn't know you wanted, and at least a few tools you'll rent. Oh, you will also want to have money and a lot of courage! The money side is dependent on how big and how crazy you go with the project, the courage is required if you continue on to at least step 1, and my favorite step, Demo!
Still reading? Great! Now just to get this out of the way:
Disclaimer: This is a how to on how to dig and install a pool, but you should only attempt this project if you feel comfortable with all the steps, file all the required permitting applications with your local gov't and have every step inspected by your local gov't. Your pool design should be reviewed and stamped (signed and sealed) by a professional engineer for permitting for the city or county where the pool is being built. No one should attempt a project like this outside the purview of local building codes and inspections. This guide is intended to provide a good fundamental for building a pool but is not a comprehensive list of relevant building codes. If for any section you do not fully understand the relevant building code, you should hire a subcontractor for that section.
In no way is this Instructable or it's author liable if you dig a hole to china, find an ancient Native America burial ground, become rich from archaeological discoveries, build a bad pool, compromise the structural integrity of anything on your property, file for divorce from project management stress, release the Kraken, or anything bad. Build and dig at your own risk.
Disclaimer over, lets Demo!
Step 1: Demo
You've pulled your permits right? Good. Once you pick you location where you want to install you pool, you'll need to get rid of everything there. This is a good time to discuss your pool shape and features with the engineer you have hired. You can find Professional Engineers (PE's) in most places to layout the legal side of you pool design for you.
I had a paver deck with a screen enclosure and sunken built in hot tub. I said "had" because I tore it all out. Now, for the fun part. I rented a bobcat and had a 40 yard dumpster dropped off.
Expert Tip Here: I had about 1200 sq ft of pavers, that alone would cost 800 - 1,000 in dumpster fee's for weight. I put an add in craigslist for free pavers, 3 guys showed up and took them all from yard for free. I didn't have to work to remove any of them, or pay to dispose of them and they stayed out of a landfill! Win Win Win here.
Driving a bob cat is both fun and easy.... it's actually a lot of fun... I recommend everyone try it. This will also make insanely quick work of you big project. You can rent these all over the place for about $300 a day and a lot can be done in one day with these things!
Once done with demo, you should have a nicely cleaned area so you can layout your plans.
Step 2: Dig and Rebar
If you are so inclined you can now rent an excavator and start digging. The digging part is easy, however you won't realize how much dirt will come out of your yard until you start digging. We had 6 dump trucks of dirt removed for our project, crazy amounts.
You have options here. You can sub this all out and that's a smart but expensive route. You can dig yourself and call around on the dirt you will be removing: you may find someone who will take it for free (because they will sell it somewhere else) or you might find someone who takes it for a small fee, or you can use it to grade out your yard. Just realize at this step a lot of dirt will be coming out of the ground. Important note: Do NOT get ride of 100% of the dirt.You will need some dirt to back fill and grade after concrete. It's hard to know exactly how much you want left, but don't get ride of so much you have buy more later.
Before you or anyone else digs a deep hole in your property Call Before You Dig to identify any underground utilities.
http://call811.com/before-you-dig
We should talk about ground water here. If your property floods in a rain or you are low lying, you can expect to hit water when digging. If you do, it's critical you have a plan established for dewatering your hole as you dig or you can create problems for yourself. Also, while we are here, are you planning on digging near your house? Please familiarize yourself with the "angle of repose" before you get within 7 ft of your dwelling. If you dig too dip and close to your house you can undermine the foundation of your home and create a major problem. The concept of angle of repose covers that. Google that, and check with your engineer.
Expert Tip: Do you have a lake or standing body of water near your place for you dig? If so, you can use Google Earth to measure the elevation of your property to the top of the water in the lake (or whatever) to get a good estimation on how far the water table is below your property. This should only be used for estimation purposes only.
Building the cage. The rebar you use to reinforce your concrete is called the cage. We use rebar in concrete because concrete is very good at compressive loads, but it's awful at tension. By code the concrete is reinforced with rebar and spacing might be subject to local codes: typical is #3 bar 12 inches on center. This is very easy work but back breaking labor intensive. Spending some $'s on extra hands here is smart money.
At this point all underground plumbing (main drain, any bublers, etc) should be installed and pressure tested. More information the underground plumbing can be found in the Plumbing step. Typical pressure testing for all underground (plumbing that will be under the pool only) is to be pressurized to 35 PSI and maintained without any loss for 15 mins. I encourage you to pressurize the system and hold it there for several hours to check for a leak. Once the concrete is in, you will never be able to fix this. Take the time here to make sure it's right
At this point you should be ready for inspection before concrete (gunite). You will have the steel, setback, equpotential bonding (see the electrical section for more information) and underground plumbing inspected BEFORE concrete.
Step 3: Gunite
I don't know anyone who does their own concrete work here. If you can or did, bravo. For everyone else, this is the part of the project you can to sit in a lounge chair with a cold drink and watch professionals do good work.
BUT do watch them, do check they are doing what's correct, and check for anything that looks wrong. Ask questions and point things out. They work for you here, don't be afraid to be the boss. Tony Danza isn't the boss here, you are. Bad 80's joke, sorry.
Once the concrete is done, don't do anything for 24 hours: don't get in, don't do a hand print like it's your Hollywood Walk of Fame, and don't scratch your initials into it like you did growing up. Just look and be impressed with how far you have gone!
24 hours over? OK good, time to talk controversy: Watering your pool. What's that you ask? Well, it's the practice of using a hose 2 - 3 times a day to soak your pool as it cures. A typical concrete job takes 28 days to reach 90% strength. During that time,water is leaving the concrete as it dries. Now, most concrete jobs are pretty even, a 4 inch slab is mostly 4 inches everywhere, a 12 inch column is 12 inches all over the place. Your pool? You'll have 8 inch sections, and 18 inches sections. The rate at each of those sections cures will not be consistent.
Will watering you concrete a few times a day make a more consistent cure and prevent any cold joint? Hard to say for sure. I don't think anyone has really taken the time to take this to task with the scientific method. What we do know is, it almost certainly won't hurt. It's worth it for the first 10 - 14 days on the curing curve.
My vote is water your pool and watch it grow into a true beautiful thing in a few short weeks.
Step 4: Plumbing
Plumbing isn’t hard; purple stuff, blue stuff, twist, push together and hold 30 seconds. Pretty simple. I’m just kidding; it’s actually a little harder than that... Like 10% harder, you aren’t building a rocket ship.
Lets cover a few things first:
1. Primer (aka purple stuff) – This isn’t Kool-Aid so don’t drink it, but it is important. Various sources online will tell you this stuff is critical or it’s a waste of money. If you research this yourself you’ll read about amorphous crystalline structures, transition states, solvent welding and on and on and on.
Here is the important part, using the purple stuff almost certainly doesn’t create a weaker joint by changing the welding properties of the final PVC weld, but it almost certainly remove debris and other containments from your connections and makes an amateur plumber more likely to have leak free joints. It’s a cheap enough insurance for the less experience plumber so that it’s a no brainer.
2. DWV versus pressure fitting. DWV stands for Drain, Waste and vent and is not rated for the pressure on a pressurized pool system. During the inspection phase you will most likely need to maintain 35 PSI and it’s really unlikely that DMV fitting will hold that pressure. The fittings are cheaper than a Pressure fitting, but you get what you pay for here. If you have a friend with a pool leak, he probably has DMV fitting somewhere leaking.
3. Critical step for connections. When making connections with fittings or pipe to pipe, the main reason for leakage is not seating the connection fully. It’s so critical that you push the connection all the way to the seat of the fitting and give a little twist. You will want to hold each and every connection for 30 seconds. Take your time here, it’s worth it. These two operations together ensure proper solvent across the entire connection. Using a good technique here makes chances of leaks really low.
There are 3 part to the plumbing: the underground (stuff under the concrete), from the pool to the pad (still underground but not under concrete), and all the stuff at the equipment pad and mostly above ground.
The plumbing under the concrete must be inspected before the concrete is in. From the pool to the pad can be done later, don't get caught up on this right now. And obviously the equipment pad stuff is done last and inspected right before you can fill the pool.
Do not Do not Do not put water in your pool until you have confirmation from your building inspector you have reached that step. They can shut you down and make you drain your pool if you get ahead of yourself. Ask questions and listen to their advice.
Step 5: Electrical
What kind of car does an electrician drive?
A Volts-wagon. Bazing. Tip your waiter I'll be here all week.
Seriously though, the electrical portion of your pool is the more serious part. Mistakes in all the other sections may cost you money, mistakes on the electrical side can be dangerous if done incorrectly. This is another section where if you are unsure, sub it out. If you are comfortable with the work, you can save a lot of time and money here. The thing to remember is the NEC code is your friend, take your time and do it to the code. The electrical code isn't there to make it more expensive or take longer, it's to make sure everyone is safe.
Eequipotential bonding (EQP) is one of the major keys here. The basic principle here is you want the potential voltage in all metal to be the same. Voltage can move from one place to the other when there is a difference in potential. If on one side there is 12V and 10V on the other, voltage can move from 12 to 10 (2V potential). If both sides are 12V then it can't move. That's as basic as I can make it, If you want more information see this video from Mr. Mike Holt on youtube. It's pretty good deeper explanation on the EQP bonding question:
You can see from my pictures, I have a dedicated green wire running back with the pool light as the EQP bond wire for the pool light.
Things to consider:
Spend the extra money now on low voltage color changing lights. They really give the pool that pop of awesome, don't use much electricity and aren't that more than a traditional light.
Invest in a Variable Speed pump. The operation cost of a variable speed pump is a lot lower than a 2 speed pump. You'll pay a little up front, but the cost saving are worth it. In fact, in many places variable speed pumps will become code due to electricity savings.
Lastly, read up on most of the NEC Code you'll need to know for the project here:
http://www.ecmweb.com/code-basics/pools-and-spas-p...
What your equipment ends up looking like here is really dependent on your selections for equipment and layout. Follow the code, talk with your inspectors and make good decisions here.
Step 6: Finish Work
I've done a lot of tile work. Tiled my entire house really. Didn't touch the waterline pool tile. This was mostly because we elected to have glass tile. That requires a special water laser level and a good skill set. Oh and I've got the skills....just not the laser level. If you do classic 6 inch ceramic tiles, it might not be that hard. However, as you come around the pool if you are off level by even a little, when you get to the end your tile won't line up. A typical bigger pool can be 100 to 150 linear feet. If each 6 inch tile is off by 1 mm (about the size of pencil lead) at at the end of only 100 linear ft you could be off by 7 inches or an entire tile. incredible unlikely, by compounding error like that make me reluctant on this step.
My advice on this section is hire professionals that you have seen their work on other projects. The finishing touches on the tile and interior finish make all the difference. Use reviews, and only use licensed contractors.
This is a perfect step for a cold drink and a lounge chair again. It's unlikely you can save money on this step as bulk ordering of materials by the Pro's offset any labor cost you incur. Overall if you do your own pool you stand to save 20 - 30% cost over a traditional pool builder, your fine subbing some stuff out. In our case, I bought a sheet of out water line tile on my own, and it was the same cost my contractor charged me to install it.
Just remember you are the boss here. Don't pay 100% upfront for the work, and ask questions. If it doesn't feel right, it probably isn't.
Step 7: Deck
Deck work is not fun work. It was like the least fun part of this. A real minus two on the fun scale. BUT(!) we saved a lot of money doing the work here. We saved so much by doing it ourselves that we were able to upgrade from regular concrete pavers to travertine decking! As the building inspector said, this is the stuff they put in the fancy houses. You heard it here first; the building inspector said I was getting the fancy stuff!
Decking is again a straight forward easy part of the process that decks a long time. The critical steps here are a good foundation. You’ll want to make sure you grade the yard with a slight pitch away from the pool. You’ll want to fill with 4 – 6 inches of concrete fines. You should plate compact every 6 inches. Compact compact compact. This keeps your deck from sagging in the coming years of enjoyment. You can use leveling sand at the top to make sure your deck maintains a pitch away from the pool. Did you remember to compact every 6 inches?
The other important thing here is the deck drain. Even though we do not have a concrete deck, we want to have a nice drain system to pull water away from the house. A paver deck does have some porosity to it and it will allow water to drain; however, it can be overwhelmed by a good solid rain or splash from the pool so you will want a deck drain installed to carry water away from the house. Don’t skimp on this, one time up front cost to prevent a lot of issues later.
If your doing your own deck, be ready to move some material. We moved in 12 tons of sand and concrete by wheel barrel. You can't use heavy equipment here, you'll risk breaking buried plumbing.
Step 8: Swim
And we are done, now you have a pool.
I hope you can swim, if not.... oh boy.... go here:
Instructable - How to Swim Freestyle
Have a cold drink and relax in your new pool!
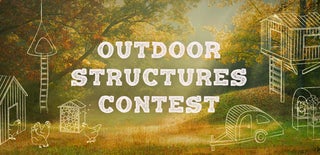
Participated in the
Outdoor Structures