Introduction: Build the Ultimate High Power LED Desk Lamp!
I wanted the perfect desk lamp, so I made my own. You can machine the parts from the CAD model out of metal, or just 3D print them.
Materials:
- cooling body for the high powered LED
- 100mm aluminium tube
- 20mm carbon fibre tube
- spray paint
- spray primer
Electronics:
- high power LED module
- suitable constant current power supply. (more info the next step)
- If you want to keep it simple: Only an LED light bulb and a light bulb socket.
- standard electronics stuff (solder, heat shrink, crimp connectors)
- a 100k ohm potentiometer
- wago wire clips
Tools you need:
- This really depends on how far you want to go. I used a CNC and a lathe, but you could just 3D print all of the parts. I guess if you have access to a lathe and a CNC you will already have all the hand tools I used.
- A soldering iron. (This one is amazing!)
- Polishing Wheels
Step 1: Make the Design Suit Your Needs.
You could rebuild the desk lamp exactly as you saw it in the video, but of course you can modify all the files with Fusion 360 to make it suit your preferences. All CAD Files!
You want to 3D print the whole thing?
I would advice you to print all parts using 100% infill in ABS or PLA, but make sure to double the diameter of the surfaces where the hinges are friction locked.
The desk lamp is mounted through a hole in your desk. If you don´t want to drill a hole, you could modify it a little bit to make it clamp to it. Be creative and make this your design! I would love to see what you make!
Step 2: Chose Your LED
I am using a 12 LED Osram Oslon module with 4000K which is daylight white. This is the best colour in my experience. You can use any LED module though. Anything above 5W probably needs cooling. This one uses 30W. You can get a lot of LEDs already mounted to a little metal plate. This makes it easy to mount and solder them. Otherwise you get tiny tiny LEDs with even smaller leads.
What power supply should I get?
I recommend spending some bucks on this. The Meanwell power supply that I got has great build quality and protects the LED. It also has a dimmer function build in. You can Dim the LED over PWM, a 1-10V voltage drop or with a 1-100kOhm resistor. So that means you can controll it with a potentiometer or any micro controller.
Take note of the following:
- Power supply outputs a constant current
Power supply is rated equally or below the rated current of your LED. - Power supply is rated to the same voltage as your LED.
- Power supply has a housing (Its not worth it to build your own in my opinion.)
- Power supply is dimmable
What is a constant current supply?
You want one of those. Unlike a battery, this power supply outputs a constant current. For my LED module that is 0.8A at 32V. You want a power supply that matches your LED. Ask your supplier if you are not sure. Its their job to give you advice.
LEDs get warm when a current passes through. That in turn causes even more current to pass through. This is a loop that ultimately makes the LED run much hotter and with more current that it is supposed to. The current limiting power supply will ensure a long lifetime of your LED.
Is there a simpler way?
Sure! You can use one of these and add a standard LED light bulb. They have the power supply build in. They are not as bright, but you don´t need the cooling and all those other electric components. The cable comes with a switch after all.
Step 3: Machine the Heat Sink.
You could of course just buy a pre made cooling body and adapt it to your application, but you can also machine the one I made. The CAD files also contain all the CAM operations. That should give you a starting point. I am using a 30W LED. With this heat sink it reaches a maximum of 60°C which is allright. The lampshade also dissipates some of that thermal energy.
Here was my general CAM approach:
- Drill holes to screw down the work piece.
- Only spot drill very shallow holes to mark the position of the LED mounting holes. Finish them later by hand.
- Cut the outline of the star shape.
- Remove the excess with a bandsaw.
- Flip the workpiece and machine the back with the groves.
I took very shallow cuts. 0.3mm depth of cut at 1000mm/min.
Then you can tap the holes that wedge the heat sink into the lamp shade and cut slots. Countersunk screws will open up those slots and clamp the heat sink in place later on.
Step 4: Machine the Hinge That Holds Up the Heat Sink.
The little tap that holds the heat sink goes into the slot that you already have cut. Screws would have to be very small and long, which is impractical to drill. So I glued it in place with epoxy. I checked West System Epoxy and that stuff is good up to 90C° apparently.
A zip tie goes through those little slots and secures the power cable of the LED.
Step 5: Machine the Plugs for the Carbon Fibre Rod.
The aluminium plugs were inspired by race cars. They need a really tight fit to funcion properly. That way you can take them appart for maintenance and you don´t need any glue.
There are 3 parts to this. One plug at the top that connects to the heat sink and 2 at the base that make the carbon fibre rod tilt. Just check out the CAD files and the drawings. It is all in there.
A little tip, make sure your flats for the screws are actually paralel to the friction surfaces of the hinges.
Step 6: Machine the Knob (Or Buy One...)
I used a fine thread for the knob. That gives a little more adjustability since the angle of the threads is more shallow. You could also just buy this knob, but you are probably going to have to settle for a standard sized thread. They should both work.
The best way to machine this part would be out of steel on the lathe. I only had flat aluminium stock though, so that was no option for me. I finished it on the lathe though to get a better finish.
Attachments
Step 7: Machine the Table Mount.
The way I mounted the desk lamp to the table is very similar to kitchen sink appliances. They are both round and hollow on the inside. The faucet lets water pass through and the desk lamp the power cable for the Led. They are also both mounted the same way with a nut on a threaded rod.
This component consitst out of the decorative top sleve, a pice of hollow threaded rod and an M16 nut. Initially I planned to make the sleve and the threaded rod out of one piece. However, the steel that I bought off ebay was hardneded and removing that much material would have taken me ages. So I went the easy route and machined them out of two parts.
Attachments
Step 8: Polish All Metal Parts.
First I sanded my parts from 80 up to 2000 grit and then I polished them. I am using these polishing wheels that you can put into your drill press or cordless drill. I add a little bit of polishing compound from time to time and keep going until everything is shiny. That takes about 2 minutes for this piece.
Step 9: Prepare the Carbon Fibre Rod.
I just got any odd carbon fibre rod off ebay. Is is plenty strong, but it was critical that it would be as light as possible. The tiny hinges don´t have a ton of foce to hold up the heavy heat sink.
You can drill them with a standard metal drill bit and chamfer them so the cable doesn´t get damaged. I would advice to drill these holes at the very end when you know where the cable goes.
Step 10: Machine the Lamp Shade and Spray Paint It.
This part is called "Can" in the CAD files. It is 100mm in diameter and 150mm in length. You can order this already cut to size. Then you only need to add the through hole for the carbon fibre rod and you are good to go.
This part could be printed in one go together with the "heat sink" if you were to use a standard light bulb and a standard socket. This would also make the whole lamp lighter and reduce the stress on the hinges.
Paint is optional : D.
Attachments
Step 11: Print the Electronics Housing.
You can download the CAD file and print it as is, or you can adapt it to your components. You might want to add a USB socket to charge your phone, or to connect USB-sticks to your PC.
Step 12: Prepare the Electronics.
The power supply I used has 6 cables coming out of it. 2 go into the socket, 2 go to a potentiometer for dimming and the other 2 go to the LED. Since this is an led power supply, you can hook it up directly to yout LED.
I used a mix of WAGO wire clips, soldering and automotive wire shoes to connect everything. You should add a few quick disconnect points into the power cable for the LED. That makes the assembly easier.
Step 13: Assembly! Whopp Whooop!
This is self explanatory I guess. If you made it this far, you know how to put things together. The electrics box gets screwd into the underside of your desk together with the power supply.
Step 14: Congrats!!!
You now have your own beautiful, poweful and unique high power LED desk lamp. (Designed by Max Maker : ) )
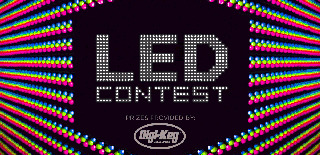
Participated in the
LED Contest 2017
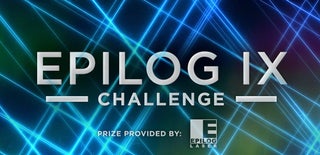
Participated in the
Epilog Challenge 9