Introduction: Building a Custom Coffee Pour Stand
For this project I've decided to make a coffee pour over stand for times when I don't want to brew a full pot of coffee. I originally was going to build a single coffee pour, but my wife convinced me to build a double pour and have space for cream and sugar containers. I like working with epoxy so I've added some design with coffee beans embedded in the epoxy.
Supplies
Materials
- Curly Ambrosia Maple project Board
- 2 - 1/2" Diameter 24" Length Wormy Maple Dowels
- EcoPoxy Flowcast SPR Epoxy Resin
- EcoPoxy Copper Metallic Pigment
- Tuck Tape - poly sheathing tape
- Walrus Oil Cutting Board Oil
- Walrus Oil Wood Wax
- 1/1/4" wood Screws
Tools
- Mitre Saw
- Table Saw
- Wood Planer
- Palm Router
- Drill Press
- Disc Sander
- Corded Power Drill
- Cordless Power Drill
- Heat Gun
Step 1: Wood Selection
I purchased a few amazing curly hardwood boards a few months ago as "Inspirational Boards" that would inspire me to build something. One of these would be perfect for this project....as the grain would really pop when I finished the wood with a wood oil. I dragged these into the kitchen and decided on the Curly Ambrosia Maple. I also had several hardwood dowels (wormy maple, walnut, and padauk) to chose from and decided to go with the wormy maple for a consistent color of the wood rather than 2-tone; as I would add some color in the epoxy resin with a pigment.
Step 2: Wood Base and Top
I cut 2 23 3/4" long pieces from the project board on the mitre saw; and then squared the pieces on the table saw, and cut to a width of 6 1/4 inches. I has some excess cut off on the width that will be used later. These 1" boards were then planed down to 7/8" on the planer.
Step 3: Holes for Coffee Pours and Epoxy Resin
Using the drill press, four holes were drilled on both the top and bottom boards with a 2 1/4" hole saw bit. Then a profile edge was added to each of the holes using a router and a 3/16" cove bit.
Tip: Because you are routing the inner edge on the circle, you will move the router clockwise to prevent kickback and tear out with your router.
Step 4: Profile on Outer Edge of Top and Base Boards
I added a profile edge on both the top and bottom of both the top and base boards using a router and a 45 degree chamfer bit.
Tip: Because you are routing the outer edge on the board, you will move the router counter-clockwise around the board to prevent kickback and tear out with your router.
Step 5: Resin Pours
Epoxy Resin was mixed per the manufacturers instructions and metallic copper pigment was added. The holes were covered on the bottom side with tuck tape and the resin was poured. I used a heat gun to eliminate any bubbles in the resin. When the resin stated drying to a jell-o like consistency coffee beans were added. When the resin further dried to firm but tacky state additional clear resin was mixed and poured. I slightly overpoured the resin as these boards were given a light plane through the planer after the resin cured.
Tip : the resin is overpoured as when is cures it will cure to a slightly convex shape being higher on the edges. Planing and sanding will give you a perfectly flat surface.
Step 6: Cutting Supports for Top and Bottom Boards
The supports between the bottom and top are 8" x 2 1/2" boards and 1/2" Dowels. The supports boards were given a similar profile as the top and bottom boards with the router and 45 degree chamfer bit.
I also cut 5" x 2" outside support pieces for the top board to house a 1/2" dowel along the back. The front edge of the board was also given a 45" cut, and these pieces also received a profile edge with the router and 45 degree chamfer bit.
Holes were drilled on the bottom of the Top Board and the top of the Base Board at 1/2" for the dowels using the stop on the drill press for accuracy. The dowels were then cut at 9" (8" for the height of the side supports and 1/2" to be recessed in the holes on both the top and bottom boards that were just drilled.
This same process was followed for the back support with a dowel on the top piece; the dowel cut to 21" (20" for the exposed dowel, and 1/2" in drilled holes on both the top side supports.
Step 7: Board Sanding
The tuck tape was removed from the back of the top and base board, and all boards were sanded going up in grit (100, 150, 180, 220). The boards were then sprayed with water to raise the grain. After the grain was raised the boards were again sanded with 220 grit to remove the raised grain.
Step 8: Drilling Holes to Attach Pieces
Holes were drilled to attach the various pieces. A countersink drill bit was also used so that the wood screws would not show. The supports were clamped to the Top and Base Boards and drilled though the top and base holes into the side supports with a cordless power drill. (No picture for this as my hands were full)
Step 9: Oiling and Waxing Pieces
All Pieces were oiled with Walrus Oil Cutting Board oil and let to sit overnight to let the oil penetrate the wood. Any excess was wiped off and the boards were then treated with Walrus Oil wood wax to seal them. I used a power drill and buffing pad but this step can be performed by hand.
I found it easier to treat the pieces prior to assembly.
Step 10: Assembly of Coffee Pour Stand
The Coffee Pour Stand was screwed together with 1 1/4" wood screws in the predrilled holes.
The only tricky part was to first attach the 2 top supports with the front screws only, then turn them sideways (first picture) to attach the screws through the top to the side supports. These are then turned back and the dowel inserted on the top piece, and they cover the screws that attach the side pieces and the back screws are then inserted from the bottom (the last 2 pictures).
Step 11: Enjoy a Cup of Coffee
Boil a pot of water and enjoy a cup of coffee with your new Coffee Pour Station!
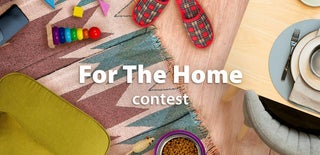
Participated in the
For the Home Contest