Introduction: Building a Guitar: Telecaster Thinline
In this article I will show you how I built my first electric guitar. This project took place over almost a year. I am not a professional luthier and I made this guitar mainly by hand with the tools I had.
I chose to make a telecaster thinline because it looks great and it is easy to find templates on the Internet. A telecaster thinline is a semi-hollowbody guitar : it has some cavities inside the body.
Supplies
Tools:
Here is a list of the main tools I used for this project.
- Chisels
- Files and Rasps
- Fret saw
- Router for the body cavities (not mandatory)
- Drill
- Jigsaw
- Sandpaper
- Orbital sander
- Soldering iron
As you can see, there is not much need for power tools to build a guitar, although they make work faster and easier.
Hardware:
- Harley Benton locking tuners
- Neck Fix Bushing
- Strap locks
- Bridge
- Frets
- Knob
- Pickups
Mono Jack plug, 3-way switch, mini-switch, 2 pots
Step 1: Preparation
I decided to make the guitar out of mahogany for the body and the neck and ebony for the fretboard. I bought the wood from a specialized website. The two parts of the body were already glued together. I don’t have a jointer nor long clamps so I preferred not to do it myself.
I used 10mm thick MDF and a jigsaw to make the templates for the body, the cavities and the pickguard. I finally decided not to make a pickguard for my guitar. This website provides templates for a large number of guitars as well as instructions for printing a full size template.
Usually for a thinline guitar, you make the front and back parts of the body with two different pieces of wood. I made mine with the same piece so I had to split the body blank in two. I didn’t have a band saw, so I had to use a hand saw instead to make the cut. It therefore took much longer than expected !
Step 2: Making the Top
The top is made from the thin part of the body blank (~10mm). I started cutting it to shape with a jigsaw and used some files and sandpaper for the finish.
Then I cut the f-hole and glued maple veneer on the inside to make it look better. I soaked the veneer strips in hot water and taped them on the template to let them dry to shape.
Step 3: Routing and Gluing the Body
In this step, I routed out the internal cavities of the guitar body. I borrowed a router for this because it would have been quite difficult to proceed without it. I fixed the template to the thick part of the body with double-sided tape and used the router with a ball bearing bit to make the cavities.
Then I cut out the body to shape and glued the top and back parts of the guitar body together.
I also made the electronic cavity and a cover to access the pots later.
At this point the body is almost finished!
Step 4: The Binding
One the side of the guitar you can see the glue joint of the top and back part of the body. The wood grain didn’t match perfectly, so I decided to make a binding to hide the joint. This step is not necessary at all, but is simply a matter of improving the visual of the instrument.
Once again I wanted to use the maple veneer that I used on the f-hole for the binding. So I shaped the strips using my template as described above.
To make the notch for the binding on the body you usually use a router, but I couldn’t get one at this stage so I made a little jig to help me draw a line on the side all around the guitar. I then used a chisel to remove around 1mm of wood to recess the veneer strips on the body.
The result looked quite terrible as there were a few big gaps between the veneer strips and the body on the sides of the guitar. So I made a second binding to hide the unsightly joint. This time I paid more attention when marking my lines to make them as clean as possible.
For the second binding I used ebony dust from the fretboard and superglue. It took a long time to sand it flush with the body but the result ended up looking really good !
Step 5: Making the Neck
For the neck, I started by glueing a paper template to the neck blank with spay adhesive. I then cut it into shape with a jigsaw. I finished it with a plane for the sides and a file for the round shapes.
I then cut the channel for the truss rod by hand with a chisel. I made the channel a little bit deeper than the truss rod height and glued a piece of wood on top of the truss rod to close the channel. It is easier to glue the fretboard afterwards because you don’t have to worry about putting glue on the truss rod.
Step 6: The Fretboard
For the fretboard, I started by cutting the fret slots on the fretboard blank with a fret saw. This is the only tool I had to buy for this build. I made every thing else with the tools I had on hand but you really need a 6mm saw to make the fret slots.
For the fret spacing, I used a fret calculator. Take your time to cut precisely the frets slots: you don’t want your guitar to be out of tune!
Then I glued the fretboard on the neck. I used two pins that helped the fretboard to stay in place while the glue was drying. The fretboard tends to move with the wood glue so you can use two little pins under the fretboard to lock the fretboard in place.
Then, I trimmed the fretboard to size and use a homemade radius guide to create the neck radius. I ended up making the radius with a hand plane because my radius guide didn’t have the right angle.
Step 7: Setting Up the Frets
First, I cleaned the slots and I hammered in the frets. Then comes the difficult part of making the neck playable. For me, it was the most challenging part of the whole project.
I watched a lot of tutorial on YouTube for this step. I followed the process described in this video of That Pedal Show because it uses tools I already had. Most luthiers use some special tools to dress the frets end, etc. The luthier in this video only uses a sharpening stone and a triangular file. I took my time and the result is not perfect but it plays nicely.
Step 8: Shaping the Neck
I shaped the neck using a rasp and sandpaper. I just checked the shape of the neck from time to time and made small changes until it was perfect.
I then drilled hole for the side dots and filled them with toothpicks. I didn’t want to make dots on the fretboard.
Then I made a small inlay on the headstock with the chisel and filled it with ebony dust and superglue and ebony.
Step 9: The Neck Pocket
The neck pocket is another critical part of the build, you must make sure that the center lines of the neck and body match perfectly.
I marked the location of the neck pocket with tape, then used a drill to remove most of the material. I finished it with a chisel, removing some material little by little until the neck fits well into the body of the guitar.
I used metal inserts to hold the screw heads because it looked good.
Note: You can see on the pictures that the body is covered with paint tape. I used paint tape continuously in order to protect the parts that were already finished.
Step 10: The Pickups
Then I had to make the pickups cavities in the body of the guitar. I didn’t have a router for this so, once again, I used a drill to remove most of the material and finished with the chisel.
I used maple veneer and open pickup covers to cover my pickups. I had to do several tests until I found a way to drill the holes for the pickups screws into the veneer without breaking the veneer.
Step 11: The Electronic
For the wiring, I originally wanted originally a 3-way switch like the telecaster, a volume knob and a tone knob with a push-pull to split the humbuckers but there was not enough room for the push-pull and the telecaster switch in the electronic cavity. So I ended up using a classic 3-way switch, 1 volume knob, 1 tone knob and a small switch to split the pickups.
Seymour Duncan provides all the wiring diagram you need here.
Step 12: The Finish
Here is the last part: the finish. I sanded the guitar to a very fine grain. Then I applied 3 or 4 coats of teak oil and sanded between each coat. Next I applied wax.
Finally I put all the hardware on, made the final adjustment and the guitar was complete !!
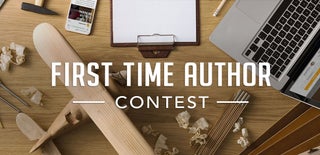
Second Prize in the
First Time Author Contest