Introduction: Building a Rubber Stamp With Fusion 360
Fusion 360 is a CAD/CAM program that is free to students, educators and hobbyist. It is very easy to learn and I would like to show you how you can use it to make a rubber stamp. For the stamp we are going to use the logo for our local Makerspace Factory Two in Flint, MI.
The first thing that you are going to have to do is to sign up for the program at https://www.autodesk.com/products/fusion-360/stude... .
If you are not a student or a educator but are a hobbyist you can also get the program as long as you are not making 100K with it. This makes it very attractive to a lot of people and I have found that it is very easy to use.
I will go over a lot of the different buttons and show you how to use some of the features. I will not be able to go over everything that the program does because I do not have the time for that. So let's get started.
Here are some shortcuts that I have used that will help you navigate. All of the mouse buttons are used so I will call them out as follows.
LMB (left mouse button)
RMB (right mouse button)
MMB (middle mouse button)
The mouse buttons will do different things depending on where you are on the screen. If you click in the middle of the screen it will work differently than if you click on the side panel or top ribbon.
After you have downloaded the program you will have a data panel on the left side with some different things to look at. Here is how to look at them so that you can see what is done.
Step 1:
LMB click the folder that you would like to open up. You can now LMB click the file that you would like to see. When the program brings the file up you can now use the radio buttons at the bottom of the screen to show how the file was built.
This is an easy way to learn how to use the program as you can see what others have done to build things in the past.
I will now show you how I built the stamp with the 3D printer and the Laser cutter at Factory Two. The first thing I did was to RMB click on the (Unsaved) at the top left of the screen. From this I choose "New Component". What happens now is that the program will install "Component 1;1" in the timeline and in the Browser. LMB click (slowly) on the "Component 1;1" and rename that to "Handle". I do this so that I know what part I am working on. I also want to have a "Base" so I do this over however again I call the part "Base". Go back and hover your cursor over the "Handle1" and LMB click on the circle to activate the Handle.
You won't see much difference however if you had already built some parts they would be a much lighter color.
Step 2:
Time to check what units you are going to be drawing in. Most people in the United States use the English system of inches while our friends across the pond would use Millimeter. I am comfortable with either and you can change on the fly. You can make one part in Millimeter and one part in inch and they will work together. Here we are going to use inch. One inch is equal to 0.0254 of a meter. Nice thing about this is that the program will figure this all out for you. No need to do all that math.
Now that you have the units set to inches click on the "Sketch" on the top ribbon. Or if your cursor is in the middle of the screen you can hit the "S" key. this will bring up the "Model Toolbox". You will find some things in the tool box and I use this a lot. It is far easier for me to type the "S" and click on the tool I need. If the tool is not in there just start typing what you want and it will come up. As you start typing the command you want there will be a bunch of things it could be. If you LMB Click on the little arrow off to the right side of the command it will be added to the "Model Toolbox" the next time you need it.
Step 3: Building the Handle.
Make sure that the small circle on the right side of the "Handle1" is chosen. This is important because you want to be able to save each part out separately. Sketch on the "Front" plane by choosing it after picking your line tool. You can also just hit the "L" key to start a line and then you will also have to choose a plane to sketch on.
Planes and surfaces.
Planes and surfaces are what drives the program. You must click on a plane or a surface to be able to sketch on your project. It doesn’t matter what plane you choose because we have no surfaces as of yet to sketch on. I am going to pick the front plane. You can do this by clicking named views and choosing the plane or just pick one on the nomen (short for nomenclature).
Putting your mouse in the middle of the screen type “S” on
the key board and choose the two point square. IT IS IMPORTANT THAT YOU Have the start point on all projects locked down to the center of the program. If not it will be out in space and will disappear on you when you are working on it. All bad.
LMB click the center of the lines and then move your cursor up. You will see that the program is showing a highlighted number and you can actually type a number into this spot and hit the tab key. This will install the number into the appropriate spot and move to the next number so that you can type this number in. I picked 3 for the upright and .250. If you do not get the number into the right spot and the sketch closes out you can always type the “D” key for dimension and change the dimension to what you would like it to be.
Under the “Create” key on the top bar you will find the “Revolve” button. Choose this and then the part that you just created. Choose the axis after you have picked your part profile as in figure 3.
As you can see the spot at the bottom left is where the
nomen is situated. You now have the chance to see what you have created. You can hold the MMB down and by holding the shift key you can look at this from all sides. LMB click the “OK” button on the “Revolve” menu.
Step 4: Building the Handle.
You can move this around by MMB clicking and holding and moving your mouse. Another thing that makes this program really nice is the ease of being able to go back and change things on the fly. At the bottom of your screen is some icons as to what we have accomplished. This is called a time line and we can move back and forth in time to change things up.
I am going to go back and change the shape of the handle. To do this RMB click on the sketch icon in the time line. Choose “Edit sketch”. This will bring up your sketch that you have made. Let’s change the shape of the handle a bit. Choose the spline tool from the sketch menu or type it into your sketch tool box as before.
Add some mass to the project and then stop the sketch. RMB click revolve and add the new part to revolve. Don’t worry about messing up as you can always start over. By moving the handle at the right of the time line you can move back and forth to see what you have done to build a project. You can also see the way others have built projects and this is a great way to learn the program. There are also some buttons on the left of the time line to let you move back and forth in the time line. Play with these a little and see what they do.
Let’s add our Embosser to the end of our handle. Because we have a surface now on the bottom of the handle we can use this to sketch on. Move the part so that you can see the bottom of the part. This is done by holding down the shift key and the MMB and moving the part around. When you can see the bottom of the handle RMB click the circle. Choose the “Create Sketch” and the part will move to normal view (Normal view is looking straight on). With your mouse in the middle of the screen press the “C” button. This will give you a Center Circle tool. As you move the mouse to the middle of the part you will find that it will snap to the center and you can LMB click the middle of the project and move the mouse to another spot to LMB click and you will have the center circle. I am going to make this 3 inches around. Now hit the “Q” button on the keyboard to activate the push pull tool.
Make sure that you choose both the outer circle and the inner circle. Your part should look like figure 5. Make sure that the operation is set to “Join” and the distance is .75 then LMB the “OK” button.
Step 5: Adding a Cut Out in the Handle.
I called mine “Embosser handle”. When you save the file it will show up in your folder. This may take some time to get it to the web but it will get there. You are now able to access this from any computer with the program on it with your name and password. Let us move onto the base. Hover over the “Base” and click the bullet to activate it. You will see that the part that we just built is now a lighter color meaning that it is not active. To move the part around you can click on the bottom of the square on the left side of the screen or hold the shift key and MMB and move the mouse around to find what you want. Use the “P” button to project the part that we just built. Click the bottom surface and it will change colors. You can now push the “Q” button and make this part .75 inches long.
Step 6: Building the Base for the Stamp.
Now make this side .75 or ¾ of an inch. One of the nice
things about CAD is that you can do math right in the program without a calculator. If you type ¾ in the box it will put the .75 in there for you.
LMB click the “OK” button to complete the feature.
You now have a stamp with a bottom and a handle. We need to make up some medallions to with this.
At this part of the program I am going to use the logo for Factory two. You should choose something that you want to make up that is personalized. You will follow the same sequence of operations and will have your own part.
Step 7: Making the Factory Two Logo.
I am going to make a new part up for this to show you how
you can add stuff to your project. I could just as easily go to the top and RMB on the Embosser handle and make a new component again and go from there. I want you to be able to build things from projects that others have put together. So we are going to click on the “+” button on the top ribbon.
Our screen now looks like the one that we had before we started to build the handle and base components. We are now going to build a line that is 2.75” in length. To do this move your mouse to the center of the screen and push the “L” button on your keyboard. You will be prompted to pick a plane. Looking at the Square on the left of the screen I can see that I want to use the top plane. I will pick the one that corresponds to that plane. Once I choose it the sketch will turn normal to my choice. I make my line 2.75 inches starting under the nomen. Choose the “D” button for dimension on your keyboard and pick the center of the nomen and the bottom of the line. Move to the right and MMB click. You will see a dimension of the part and also be able to change the line.
Your part should look like this after you are done see above.
You can type 2.75/2 in the box instead of 1.375 as they are the same to the program, you don’t have to do the math.
Now choose the “Insert” at the top ribbon and pick attach canvas. Select the top plane (the one showing) and then select the image and it will be placed into the part. Use the highlighted part and move it till it fills the screen as in figure 10.
The construction line was so that you can bring the medallion in with the correct dimensions. Move the circled corner in and out to make the ends line up with the ends of the line. LMB click the “OK” button to complete the feature.
Press the “C” button to get a center circle. Make a circle that is 2.75” and click the enter button to build the circle. LMB click the circle and then hit the “Q” on the keyboard to extrude this out. We are going to extrude this out to .5 inches.
Step 8:
Move your mouse up to the block on the right side of the screen and using the arrows move it so that the part looks like the part shown above. You can make the part larger on your screen by rolling the middle mouse button. If you hold down the mouse button and move the part it will move the part on the screen. What I want to see is the small leaves on the very left side of the logo. Using the screen display button on the bottom of the screen make the display show a visual style of “wire frame”.
Creating the leaves.
We are now going to create the leaves on the left side. Use the “Spline tool” and trace the leaves clicking where you want an anchor point to be. If you don’t get them perfect don’t worry you can add move the points by stopping the sketch and then grabbing them with the LMB and moving them.
Your part should look like the one in the picture above.
We will now extrude these with a cut the “Q” command and choosing all of the leaves. Extrude this out to -.200 (you will get a cut showing up). Now you can select all of the leaves that you just copied by holding the shift key down and RMB clicking each. You can now mirror them. Under the “Create” command you will find “Mirror” about 2/3rds the way down LMB click on this.
Choose features and select the “XY” plane as the one to mirror across as in the picture above.
Step 9: Leaves Added.
You can now repeat this on the top leaves. If you are having problems read through the previous instructions.
If all went well your part will look like the first picture on this page. On the sketch menu choose “Arc” then “3 Point Arc” trace the edge of the arc that is shown. Go back to the Sketch menu or type in “Offset” in the “Model Toolbox”. After you have created the two side by side arcs close them with the “L” line command. You can then extrude them with the “Q” command. Do the same on the top. You can now make the two boxes alongside of the “TWO” by using the two point rectangle and tracing the boxes. Extrude this “Q” command to -.200”. Your part will look like second picture above.
Step 10:
Adding lettering.
All we have to do to complete this is to add the letters. To do this start a sketch and choose the “Text” option on the sketch menu. You must then pick the plane that you are going to sketch on. Move the box on the left of the screen around until you find a spot that is comfortable for you to draw. Once you have the sketch ready you may have to move the letter direction by grabbing on the small circle and moving it to the top. You will now use Gill Sans MT font and make the height .400. Your sketch should look like picture above. Make sure that you leave room for the gear in the middle as we are going to have to sketch this up.
Stop the sketch and then using the “E” key on the keyboard extrude this part -.200”. Going back and grabbing the “C” center off of your keyboard lets choose the top surface and sketch a donut where the gear is at. You can then extrude this out -.200.
Step 11: Build the Gear and Add It to the Medallion
Now using the same idea you can type the “TWO into the box as below.
Build the gear and add it to the Medallion.
Now we are going to add the gear to the FACT (gear)RY. To do this we are going to build a gear up and then bring it into the project. The gear is .250” in diameter with a root diameter of .200” of an inch and a center hole of .125”. So the first thing to do is to push the “+” button at the top ribbon of the screen.
Step 12: Gearing Up
Make two circles up as described above. I added my first tooth to this but you can do it later if you want. Whatever is easiest for you. You can also bring the picture of the gear into the drawing if you would like to make sure that you get the right size. The top of the tooth is .019 thousands and the bottom of the tooth is .027 thousands. You have the rest of dimensions below Figure 20 to plug into this. There will be eleven teeth on the gear. I drew them around the center as it was easy to copy them as I used the picture to follow the gear along. Here I have turned off the picture and only show the drawing see the photo.
After you get the gear drawn you can extrude it to .200” of an inch. Remember to extrude the whole part. If you miss something you can always go back and pick it up. Now you need to save your part.
Inserting the gear into the medallion.
After you have drawn up the gear bring the Medallion leaves into the program by LMB clicking them. Drop the gear into the drawing by opening up the Data panel and RMB clicking on the gear. This will allow you to drop this onto the drawing. After you get it situated where you can move it readily LMB click.
On the top ribbon click on the “ASSEMBLE” and then “Joint” or you can hit the “J” key to pick this up. Grab the center point of the gear and the center point of where you want it to be and join these two together with the LMB.
You medallion is now done with one exception. That is that it is forward and not backwards. If you copy anything with it the design will be backwards. To fix this we are going to make a copy across a plane. The first thing we need is the plane. So go up to the top ribbon and choose “CONSTRUCT” “OFFSET PLANE” and choose the back of the part. Then I used 2 inches to move the plane away so that I could work with it.
Step 13: Mirroring the Medallion
I chose the whole body from the timeline and then picked the
plane that I just created and clicked the okay button as shown in the second photo. This will give me the mirror image that I desire to make my stamp up with.
Adding the Medallion to the stamp.
Go back to the “EMBOSS LEAVES” part and bring the “MEDALLION LEAVES” into the drawing by using the data panel as with the gear LMB click on the “Medallion leaves” and then LMB click the “Bodies” turn off the lightbulb by the “Body1.
This will leave only the part that we would like to laser cut as our medallion. Now create an offset plane by LMB clicking the “construct” icon on the top of the page and choosing “offset plane”. The program will ask you for an offset plane to use and you will choose the top of the part. The letters should be backwards so that they are correct when the stamp is used.
Step 14: Laser Cutting the Medallion.
After you have created the plane you will start a sketch on
the plane that you just created. This will now have all of the information that you need to create a “.DXF” file. This is the file that will be sent to the laser cutter. To do this RMB the plane you just created and select “Save as a .DXF”. Take this to the laser engraver and use the software on this machine to complete your project. It is as easy as that.
Now you can turn on the “Base” component. Clean up the inside by using the “Combine” command and choosing the cut option to cut the letters out of the base. Make sure that you keep the tools. Now you can go back and clean up the base so that it won’t stick together. You only want the “Medallion to sit into the part not to have the letters to get hung up on. Use the project command and grab the circle on the inside and then extrude it to remove the lettering.
Your base by itself should look like the second picture on this page.
Step 15: 3D Printing the Handle and Base.
Now we are ready to save them for the 3D printer. Go through
the “BROWSER” window and uncheck all of the components except for the “Component4”. This will be the last component built.
Now you can RMB click on the “Component” and LMB “Save as
STL”. This will get you to where the program will create a .STL file for you. This might take some time. You want the make sure that the refinement is at “High” and then LMB click the “OK”. This will bring up a file for you to save it to. You can save it to any place you want.
A bit about .STL files. STL Files are made up of a lot of different triangles. And essentially that is all they are. Now that you have your file saved as a .STL you can bring it into any 3D printer and it will work.
About 3D printers. There are many types of 3D printers but all will use the .stl as a file extension. Some printers will have support material and some won’t. The ones at Factory Two do not have support material. In this way if you are building a part with things that hang out (say your arms are held out and you want to 3D print this image) the parts have no support and will sag. To fix this problem you can add things to your parts to hold them up. They will be broken off later to make your part work.
You can build things from very small parts to rockets that go into space with your designs. Again your imagination is going to be your only stopper.
You can also by clicking on the Model tab you will find a lot of things under there that I did not talk about. “Patch, Sheetmetal, Render, Animate, Simulate, CAM and Drawing” are all things that you can do with Fusion 360.
This is just the start of learning Fusion 360 and finding out what it can do for you. It will bring your parts and mechanisms to light and make everything easier to create. You see after you have drawn up something you can place it into the 3D printer, laser cutter, shop bot or CNC Lathe, mill or plasma cutter. The only thing that will hinder you is your imagination.
Lars Christensen is on Youtube.com and has a great channel to learn how to do CAM (computer aided machining). Lars also talks about how to use the different machines and has some very useful tricks. If you go to Youtube.com you can find a plethora of different things that you can do with Fusion 360. Lars Christensen is not the only person who shows things on Fusion 360 and you will find many more gurus for fusion on youtube.com.
I would also take a look at a few other videos on Fusion to learn some things that you can do. Creating Verones and using surface modeling and building artistic things is all at your fingertips. Good Luck.
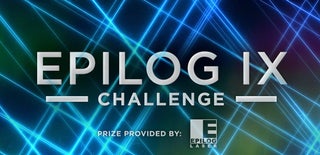
Participated in the
Epilog Challenge 9