Introduction: Buttons Using PLA Waste From 3D Printing
One of the benefits of 3D printing is that there is very little waste. But there is still some.
I wanted to find a use for the small scraps of PLA at the ends of rolls of filament that are too short to use. So for molding and casting week on the Fab Academy course I made buttons. And the same technique could be used to make other objects such as fridge magnets, hair clips and jewelry.
Thanks to Luiz Bueno for teaching me how to use a milling machine, which was ideal for this project. But you don't need high tech equipment. The Instructables Mold Making Class shows how to make molds with traditional techniques for anyone who doesn't have access to a laser cutter or milling machine: www.instructables.com/class/Mold-Making-Casting-Class
I like to print with PLA for environmental reasons, because it’s made from cornstarch. It melts at about 180°C which means it’s easy to cast leftover bits in the oven and it smells like candy floss when heated.
This activity is a record of the techniques I used and tips I found useful, rather than a foolproof set of instructions. There are safety hazards such as the use of an oven and molten plastic and it is not suitable for unsupervised children.
Materials
50ml Polycraft T-20 Translucent Silicone Rubber (comes in 2 parts - A and B)
35mm x 25mm x 15mm Milling Wax (if using a milling machine)
Scraps of 3mm acrylic or laser plywood and glue (if using a laser cutter)
Scrap PLA filament (Polylactic Acid)
Newspaper
Equipment
Laser cutter or CNC milling machine
Computer with design software (I used Autodesk Fusion 360™)
Oven
Oven tray
Oven gloves
Wire tray, or other heatproof surface
2 old plastic pots, e.g. yogurt pots
Spoon
Chopsticks or similar
Wire clippers
Step 1: Design the Mold
Buttons can be made face down or face up. Those made face down in the mold will have a matt finish and can have detailed designs on the surface. They also show up any flaws in casting and might show the grain if the mold is made from wood. Buttons made face up have a shiny smooth finish, often with a curve at the edge.
My designs are available to download below
~ or ~
Use Fusion 360™ or alternative software to design buttons.
- Draw the buttons as they will look when finished, making the holes for sewing at least 3mm diameter.
- Arrange the buttons with a 3mm gap between each one
- Draw a 5mm wide rectangular frame around the buttons allowing 3mm clearance from the edge of the buttons (as seen in the photo)
Step 2: Make the Form for Casting
Send the design to the laser cutter or milling machine and cut out the parts. If using laser cut parts, glue them together and allow to dry.
I used a milling machine to make the mold for face down buttons because it is ideal for design elements such as ridges or indentations. I used a laser cutter for face up buttons because it’s quicker and it was a way to use up waste wood.
I originally made the small upright posts (for the holes to sew on the button) less than 3mm diameter. They were too fragile and broke off with repeated use.
Step 3: Casting the Mold
To check how much silicone is needed, fill the mold with water. Then pour the water into a measuring jug and record the volume. Dry the mold.
Protect the work surface with newspaper
Mix Part A and Part B of the Polycraft Silicone Rubber compound in equal proportions
Stir the mixture thoroughly and quickly with a spoon.
Then pour it into the milled or laser cut form.
Leave to dry. The brand of silicone I used took 15 minutes.
Remove the silicone from the form using fingers.
I used Polycraft T-20 Translucent Silicone Rubber because I knew it could withstand 200°C in the oven. I also tested Smooth-On OOMOO™ 25, (which is the blue mold shown in the photos of the next step) but it degraded after a few uses.
Step 4: Make the Buttons
Warning: Take care with this step because the PLA will be hot when you take it out of the oven. Also although PLA is generally considered safer than alternatives such as ABS, a study on 3Dsafety.org suggests it may give off potentially harmful fumes if melted above 200°C. So please don’t be tempted to turn the oven up too high.
Preheat the oven to 180°C
Place the mold on an oven tray and overfill each button shape with small pieces of PLA. I used wire clippers to chop the PLA into tiny bits. Avoid covering the upright posts, but going over the edge of the mold is OK.
Place in the oven for approximately 6 minutes, until the PLA has softened
Use oven gloves to remove the tray and mold from the oven and place on a heatproof surface.
If the PLA has melted over the edge of the mold, use a chopstick to carefully push it back within the rim, then put it back in the oven for another couple of minutes.
If there isn’t enough PLA to fill each button shape, add more PLA and put it back in the oven for another couple of minutes.
Leave on a wire tray or heatproof surface to cool.
Remove the buttons from the mold.
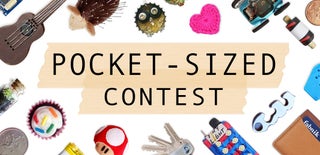
Participated in the
Pocket-Sized Contest
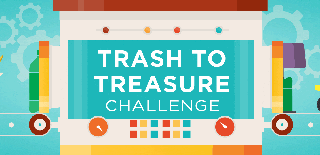
Participated in the
Trash to Treasure