Introduction: CNC Canoe Paddles
I was near the end of building my first cedar strip canoe and it didn't feel right to buy paddles for the maiden voyage. I figured it was a perfect time to learn some new skills and use my CNC to make a set of paddles.
Supplies
Paddle Materials
- Ash -1.25" x 1.25" x 60" for paddle core
- Eastern Redcedar - 1.25" x 1.25" x various lengths
- Wood Glue - Titebond 3 to laminate the paddle blanks
- Fiberglass Cloth - leftover 6 oz cloth from by canoe build
- Epoxy - West System 105 Resin / 207 Hardener
- UV Resistant Marine Varnish
- 80 / 120 / 220 grit sandpaper
Computer Programs
- Autodesk Fusion 360
Step 1: Modeling the Paddle Blade in Fusion 360
Autodesk Fusion 360 is an extremely powerful tool for creating 3D models and generating the associated CNC toolpaths. Did I mention that it is free?!?
I broke the canoe model into 3 separate parts since the maximum working area on my CNC is roughly 30" x 30".
I found the following YouTube video to be extremely helpful, even though the tutorial is for SolidWorks. The work process for Fusion 360 is basically the same. When trying to learn Fusion 360, YouTube is your friend!
Step 2: Modeling the Paddle Grip With Fusion 360
I followed a similar YouTube tutorial for creating the paddle grip. I found these tutorials to be excellent, and way more helpful than me typing out the steps that I took to model the different paddle components.
Step 3: Modeling the Paddle Shaft in Fusion 360
My original plan was to cut out the paddle shaft by hand. When I started cutting out the blade and the palm grip, I was having so much fun that I decided I wanted to rough out the paddle shaft with the CNC machine too.
Step 4: Generate Toolpaths in Fusion 360
There is just as much to learn in the Fusion 360 CAM environment as the design workspace. The intent here is to serve as a general work process guide. There are a lot of details that are dependent on your software, CNC machine, and personal preference that I will not touch on.
I generated separate toolpaths for the paddle blade, the palm grip, and the shaft and ran them on my CNC independently. For each one, I created a jig on my CNC wasteboard so that I could place the blade in the exact same position and complete two sided carves.
Toolpaths for the blade (1/4" downcut bit)
1st Side - 3D pocket operation, 3D Parallel Operation
2nd Side - 3D Pocket Operation, 3D Parallel Operation, 2D profile operation
Toolpaths for palm grip (1/4" downcut bit)
1st Side - 3D pocket operation, 3D Parallel Operation
2nd Side - 3D Pocket Operation, 3D Parallel Operation, 2D profile operation
Toolpaths for paddle shaft (1/4" downcut bit)
1st Side - 3D pocket operation, 3D Parallel Operation
2nd Side - 3D Pocket Operation, 3D Parallel Operation
Step 5: Mill Up Wood for the Paddle Blank
I found an eastern redcedar tree in my woods and didn't want it to go to waste. I milled narrow boards 1.25" x ~1" and used it for the blade and the palm grip.
For paddle core, I decided to go with ash because it is extremely sturdy. I used a table saw to create 1.25" x 1.25" x 60" blanks for the paddle core.
Step 6: Make Paddle Blank
Since I already had a full 3D model of all the components of the paddle, I knew exactly how big it had to be in order to carve it out. I made the paddle blank slightly larger than the intended paddle so to aid in clamping it down to the CNC wasteboard during the milling operation.
Step 7: Cut Out the Paddle Using CNC
I used the Gcode generated by Fusion 360 to cut out the different components of the paddle on my CNC machine
Step 8: Sand Until Smooth
The CNC machine does a good job of establishing the geometry of the blade. Sanding is needed in order to remove the tooling marks and smooth out the paddle
I started with 80 grit sandpaper and finished with 120 grit.
Step 9: Fiberglass and Epoxy the Paddle Blade
I decided to reinforce my paddle blade using fiberglass and epoxy. The technique is easiest to learn by watching YouTube. Here are some of the videos that I found to be helpful. The tutorials are from a canoe build, but the principles are the same.
Step 10: Varnish the Paddle
Once the epoxy has cured, I lightly sanded the blade using 220 grit sandpaper. The rest of the paddle I sanded using 80 and 120 grit.
In total, I applied 3 coats of varnish to the whole paddle, sanding lightly with 220 grit sandpaper in between coats.
Step 11: Enjoy Using Your Paddle!
Once the last coat of varnish has cured, the paddles are ready to use!
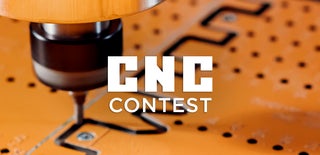
Runner Up in the
CNC Contest