Introduction: Car Wheel Bicycle - the Learn to Weld Project
This whole thing started off with me finding rusty holes in my car and I figured for the cost of paying someone to fix it I could buy a welder and do it myself, seems logical, right?
I was speaking to a friend about needing to learn how to weld and he said why not build a bike (we originally met while I was working in a bike shop and he came in looking for parts for a chopper he was building) he lent me a couple of books by Atomic Zombie, who you should check out, that dude builds some cool stuff.
His website and forum can be found at www.atomiczombie.com
After toying with the idea for a while it seemed like a good one but I was concerned that it wouldn't come out right so it was decided that I would build something a little silly, so, hence the car wheel bicycle was born.
Step 1: Tools and Meterials
So you're going to need some stuff,
Materials
Very few raw materials went into this but the few that did are...
- Car wheels, obviously!
- Some mild steel tubing, 1 1/4" and 3/4" about 4 meters of both
- A donor bike
The donor bike was used because it was an easy way of getting all the bicycle parts that were needed, after all it is a bike! also there are some bits of the frame that have very precise dimensions, the inside of the head tube and bottom bracket shell where the bearings go have what is called an interference fit meaning the bearing cups are pressed in and won't fall out, the tolerance of an interference fit is a tiny amount something in the hundreds of a millimetre, I would never be able to create these dimension with the tools I have so it was easier to cut these parts from an old frame, you can see in the third picture all the parts that I used from the BMX.
Tools
Again I didn't use that many tools to build the bike but here's a little list.
- A welder, any welder will do as long as it sticks metal together, I have a MIG welder
- An angle grinder with cutting and sanding disc's, I found a flap disc work best for sanding
- Measurement devices, tape measure, vernier gauge
- A drill and a couple of bits
- Spanners and Allen key's for the bicycle parts
- And a hammer, bigger ones are more fun but smaller ones still do the job
I also used a bench grinder and belt sander but you can do it all with the angle grinder if needs be.
And of course there's some safety stuff, goggles, ear defenders, welding mask and gloves, and a fire extinguisher.
I didn't start out with the extinguisher that was a later addition after my shirt caught fire while cutting with the grinder,
I have figured out that all these tools want to do is hurt you, please be sensible, concentrate on what you're doing, wear eye and ear protection, ask someone for help if you're not confident and don't weld while wearing shorts, those hot bits of metal will find their way into your shoes, trust me.
Step 2: Preparing the Wheels
All you needed from these wheels are the rims and tyres so the centre can to go.
Grab the grinder and a cutting disc (the thin ones are better) and get cutting, oh, let the air out of the tyre first.
I started by trying to grind the welds but I didn't get very far, it's much easier to cut around them and smooth them off later with a flap disc.
You can see in the fourth picture that I cut into the rim so these scars had to be fixed, I used a small piece of angle iron so the earth clamp had somewhere to attach to because I didn't remove the tyre, I don't have the tools but I'm sure a local garage would have done this for me.
Once the scars were welded up I smoothed them off with the flap disc.
Step 3: Making the Hubs
Using the hubs from the BMX was going to be a problem because they aren't wide enough but there's a simple solution, make them wider.
Start by cutting the axle in half, then you need to widen it, I used another axle you could use some rebar or some other suitable metal.
The reason I cut it in half instead of joining the two end to end is because they have different thread sizes and I wanted to use the cones and nuts that came with the hubs so I know they will go back together afterwards.
The hub body Is done in the exact same way, cut them in half and weld the half's to each end of a tube.
The tube I used is 1 1/4" because its the same size as the hubs so once the welds were ground down you can't tell how they were made.
Make sure the hubs are wide enough, the way I did this was by measuring the width of the tyre and used that measurement as the distance between the hub flanges.
I found it best to only weld 10 - 15 mm at a time and then rotate the hub and repeat until you get back to where you started.
Step 4: Spoking the Wheels
Now you have the main components of the wheel it's time join them together.
This was a tricky part because the rim needed to be centred (dished), round and true on the hub, this is done in three stages.
Getting it centred..
To get the centre lines of the hub and rim on the same plane I measured the overall width of the hub, subtracted the width of the tyre and divided that number by two, that gave me the height the tyre had to raised off the bench so the hub stuck out evenly on each side.You can see in the first image the tyre is on some pieces of wood and the hub has some sheet metal under to get the measurements correct.
Making it round..
I started this by measuring the inside diameter of the rim, subtract the diameter of the hub, and divided by two, this was the (temporary) spoke length, these needed to be exactly the right length otherwise the wheel would have ended up being egg shaped, I made four of these temporary spoke and used welding magnets to make sure they were at right angles to the hub, once I was happy I tacked them in place.
Making it true..
I refitted the axle and put it on some stands to spin it up, It was fairly straight but needed some tweaking, there was one spot that was out but luckily it was next to a spoke so I cut the tack, held the rim where it needed to be and tacked it back on, any other adjustments was done by bashing the spokes with a hammer, a crude but effective method.
So now you need to decide what spoke pattern you want for our wheels I was originally going to have 5 spokes all down the centre line but after talking this through with a friend he was concerned about the hub not being strong enough to take the weight in the centre with out some serious gusseting and also the forces exerted when cornering or bumping into stuff, he suggested the 6 spoke design with triangulation towards the centre of the rim, I'm glad I listened to him because I really like how the wheels turned out.
I started making the final spokes by marking a line on the hub and on the rim so they were all attached on roughly the same line, measured, cut and notched the spokes so they sat in place properly and then welded them in. I did one side while the temporary spokes were still in place, when I had one side of the final spokes welded solid I cut out the temporary ones and finished the other side.
Step 5: The Forks
I thought I'd ease myself into this frame building malarkey by starting with something simple like the forks.
The BMX forks I had were a little too short and nowhere near wide enough.
I started by cutting the legs roughly in half and then removed the upper section from the steering tube,
You can then add in any extra tubing you need to get the forks to the length and width you want.
Once the two legs were finished I bolted them to the wheel and clamped some box section to them to keep them straight while I added the steering tube back on.
Step 6: The Frame
If you are not familiar with the names of the tubes that go into a bike frame check out the first picture as that will explain it more simply than I can.
Once I the front end was done I put it on the workbench with the rear wheel and started with the frame,
First off I cut and welded the down tube to the head tube then I taped another piece of tube to a box that looked like it was about the right height for ground clearance and clamped the together as best I could to keep them straight while welding.
Then chain stays were a little confusing at first because they needed some triangulation in them,
I ended up cutting a slice about 3/4 through the tube, bending it slightly, and welding it back up.
This gave a subtle kink to the tube which was just enough, then it was just a case of making a copy for the other side and attaching the between the dropouts and down tube.
I couldn't do the seat stays until they had somewhere to go, so I balanced the seat tube on some random bits of box section to get the height right and tapped it to another cardboard box to get it the right distance away from the rear tyre then measured and fitted the lower top tube to hold the seat tube in place while I did the seat stays.
I didn't take any pictures of the seat stays but they're basically just a copy of the chain stays.
Once the rear end was complete it was onto the upper top tube.
I wanted this to have a bend rather than an angle where it goes under the saddle and to the seat tube, not having a tube bender handy, or at all, it took a bit of thinking but I decided to do a similar thing as the stays but with more slices (see pic 6 & 7) when the radius looked nice I welded up the slices, ground it smooth and fitted the upper top tube to the rest of the frame.
Step 7: Brakes and Gears
By complete luck the Sturmey Archer sprockets I had fitted on to the hub as if they were meant to be together,
The rear disc brake rotor is mounted onto the hub by drilling and tapping holes and then it's spaced away from the sprocket so the chain doesn't come in contact with the disc, the spacers were welded to the sprocket and then the sprocket was welded to the hub.
The front disc is mounted the same way but without the spacers.
The caliper mounting brackets are made from the same bits of angle iron that was used for earth clamp when welding the wheels,
To get the measurements right I put the caliper on the rotor, placed a zip tie around the lever so the caliper didn't move then held the angle iron in place and marked it where the holes need to be and also a rough shape to cut out. The angle iron I used is 3 millimeters thick, in hindsight 5-6 millimeters would be more appropriate.
When you have a nice looking bracket bolt it to the caliper and weld on the frame.
In all the excitement I forgot to take pictures of the rear brake but it's done in the same way as the front.
Because the bicycle cranks aren't wide enough for the chain to reach the rear wheel there had to be some kind of shaft to move the drive over far enough, and because it's a heavy bike I wanted some gears so I came up with the Sturmey-Archer 3 speed trans-axle (photo's 6, 7 & 8).
Using a front hub from a mountain bike I added the axle the left hand side of the Sturmey axle, Cut the MTB hub in half and added a small section of tubing the welded that to the Sturmey hub, then welded another sprocket to the end of that.
Because the sprockets on the left hand side of the trans-axle and rear wheel are welded on to their respective parts it keeps the Sturmey-Archer hub shell spinning as if it were built in a wheel as it's intended to be, meaning that I have full functionality of the gears and ratchets in the hub so I can coast if needed.
Some dropouts were made to fit the trans-axle out of angle iron and then attach to some 3/4" tubing and mounted to the frame with some extra bits for bracing to prevent twisting of the trans-axle.
Before it was striped down for painting I had to go for a quick test ride.
Step 8: Paint and Admire
To prepare for paint I stripped everything down, smoothed off the crappy looking welds with a flap disc, re-welded some bit, smoothed them off again and roughed the surface with some sand paper so the paint would stick.
Because I never removed the tyres from the wheels they needed to be masked up with some tape.
Everything was coated with a few layers of zinc primer, the zinc in the primer helps protect the steel from rusting.
Then it had a thick coat of yellow filler primer to hide all the unevenness and ding's I had created.
Then there was sanding, lots and lots of sanding to get a nice smooth finish, when I was happy I gave it another coat of zinc primer so the colour was even for the final paint job.
And there you have it, The car wheel bicycle aka The learn to weld project.
Before starting this I didn't know how to weld, I didn't know how to notch a tube and I didn't know anything about bicycle frame design but with some determination, a few mistakes, a few burn hole in my shirts and my skin I made it, and if I can do it so can you.
A big thanks to my friend Jocke for the advice, the help and awesome photos, without him this probably wouldn't have happened.
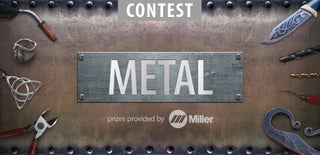
Grand Prize in the
Metal Contest 2016