Introduction: Cardboard Storage Shelf From Single Box
I received a package in a big cardboard box, and I decided to transform it into a 4 shelves storage shelf unit. And if you think cardboard is weak, I'll prove you that you can put a lot of weight on each shelves. Now, let's get started!
Supplies
For this project, you will need :
- A big cardboard box
- Hot glue sticks and a hot glue gun
- An utility knife
- A ruler
Step 1: Cutting the Legs
The first step consist of cutting the four legs of our shelf unit. I cut the legs using the corners of the box. There's four corners and we need 4 pieces so it's perfect! Each legs are 4 cm x 4 cm x 84 cm
Step 2: Cutting the Shelves
In the last step, I've cut the legs out of the cardboard box. That made some left overs and I'm using the sides of the box to make the shelves. I cut two shelves from each pieces. There is one side on each shelves that is already folded, I'm going to do the same for the 3 other sides of the shelf.
Step 3: Cutting Each Shelves to Size
Before I bend the 3 other sides of each shelves, I cut some extra cardboard on each sides, then I cut the corners so it's easier to fold the shelf in the next step.
Step 4: Bending the Sides of the Shelves
One side is already folded, so I bend the 3 other sides by applying a lot of pressure on the line using a big metal ruler. That way, it's easier to fold the cardboard right on the line. So i fold the four sides of each of the four shelves.
Then, I put some painters tape on each corners so they stay temporary in place while I put some hot glue on the inside of each corners of each of the 4 shelves.
I now have four shelves but there still some work to do to make them heavy duty.
Step 5: Reinforcing the Sides
I add a piece of cardboard on the inside of each sides of the shelves to add some strength to the shelf, especially because the lines in the cardboard are on the horizontal instead of vertical, so it's weaker without the cardboard reinforcements I added.
Step 6: Reinforcing the Middle of the Shelf
Now that the sides of each shelf are build tough, the middle is still weak and to fix that, I'm adding a center brace and four smaller pieces to add some strength to the core of the shelf. Trust me, it will be able to take a lot of weight for a cardboard shelf.
Step 7: Fixing the Legs of the Shelf Unit
Now that the four shelves are done, it's time to add the legs. I first glue in place two legs, on one side, on the bottom and the top shelf.
Step 8: Fixing the Legs
Then, I glue in place the last two shelves, then I complete by gluing the last two legs in place.
I want my shelf to take a lot of weight, so I'm reinforcing the inside of the legs between each shelves.
Step 9: Finish Result and Load Test!
Time to test the build, I tried with 133lb total (60kg) of weight and it pass the test easily. I plan to use this shelf unit to store some computer pieces inside a melamine closet unit.
And the beauty of this build is that it's almost free to build, you just need a couple of hot glue sticks and voila!
Thanks for watching, if you like this project, please check my youtube video. Thank you!
Step 10: Youtube Video Tutorial
If you would like to support me and my work, the best way it by watching my youtube video! :-)
Thank you everyone for the support, I'm working hard to bring you more cool cardboard projects!
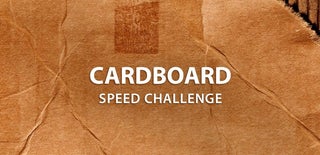
Grand Prize in the
Cardboard Speed Challenge