Introduction: Cheap DADO Stack That Works and Is 'realitively' Safe for a Cheap Table Saw
Christmas 2016 I got a cheap 'contractor' bench saw from HF Tools.
I do very little 'wood butchering of dead tree carcase' (hesitate to call it carpentry) but I kinda enjoy playing with machinery and making 'stuff'
HF saw works more than well enough for the stuff I do but no way would I buy a Dado blade/stack costing more than the saw.
I've seen multiple posts on various sites asking or showing how to make a dado stack. There is a LOT of criticism from 'real' woodworkers (professional and hobbyist) about how unsafe a stack of carbide tipped saw blades are.
The main issues seem to be blade slippage and teeth chipping throwing carbide 'bullets' around.
There is a very simple and cheap way to help prevent this using ordinary cardboard, I used the separators from the cat-food we use but almost any relatively thin (1mm/0.040") non-glossy card can be used. Use only 'solid' card and not corrugated packaging. As always, do this at your own risk
Step 1: Choose Your Blades
First step is to realise this could be dangerous
You will need blades about 2" smaller diameter than the rated size for saw, the torque applied to smaller diameter blade of greater 'width' than stock should balance out motor power somewhat?
I got a five 8-1/4" diameter from eBay for about $4.95 each with free shipping to replace the 10" standard blade, total cost under $25.00 so made 'experimenting' a viable option. A lower tooth count would be better but these were the absolute cheapest I could find at the time, will look into getting a few sub 30 tooth and use 40 on outside edges only
Probably should have taken some measurements of spindle length before ordering as HF saw has a 'short' spindle, looks like 5/8" will be max width with blades straight up and down using all 5 blades?
Step 2: Card Washers -the 'safe' Drive Method
This is important, VERY, VERY IMPORTANT.
You will need a lot of card washers, I cut mine about 3" diameter with a pretty accurate 5/8" centre hole.
Centre hole needs to hold washer in place without being too far off centre and not have any 'tags' that could prevent full contact with saw blade. The fibers of card will compress very little plus the surfaces tend to interlock with each other and the ground face of saw blade. for fine adjustments you can use paper washers (as long as it's not glossy or waxed paper)
This is something I learned when training as precision machinist in mid 1970's, the amount of pressure paper and card can take without damage is pretty extraordinary, several tons more than '2hp' saw motor can provide even with the inertia of 3,000rpm blades
Do not use any type of plastic as it WILL slip.
Rubber is too compressible if your using re-cycled inner-tubes so DON'T
Step 3: Practice Setup and Blade Storage
When blades arrive.................
Simpler to assemble on a 5/8" bolt to make sure things will sit flat than mess around down slot of table saw plus you get a better idea of the width your going to cut
You can also check how much clearance you have between blade teeth for various set-ups and 'step' teeth for cutting clearances. Using a 'full blade' instead of chippers a dado stack comes with gives a much more 'gentle' cut requiring less power and a load less vibration than an angled cutting blade
If you have a long enough saw spindle, you can mount steel washers of varying thickness BETWEEN card washers to extend range/width, the picture is blade, card washer, steel washer, card washer blade sequence using all 5 blades to get about 1-3/8" cut width
I did this step before checking saw so will be making a few 'angled' washers to get wider cuts or a 'tube nut' and grind out blade holes to a larger diameter as I would like to be able to cut at least 1" wide. (no idea on blade centre hardness,being carbide tooth on steel blade it may be possible to drill them?)
3" long 5/8" nut and bolt also makes a simple storage 'device' to keep all the parts together
Step 4: Taking Things Apart
First, unplug machine to make sure it isn't possible for anyone to start it (I once had a boss destroy a bunch of expensive stuff by 'helping' while I was at lunch)
Remove insert/cover, unscrew the nut holding blade and remove original blade and drive washers. There are flats on the shaft which flats on washers align with, 'conventional 'right hand thread' which automatically tightens when running
I forgot to take any pictures, sure it's in 'blade change' instructions that came with saw?
Picture of 10" and 8-1/4" together for comparison
Step 5: Set Up 'stack' and Test Cuts
Add blades then card washers to get width you want,(or as much as you can get with simple set up)
I set up for 1/2" wide cut which surprisingly actually cut 1/2" wide slot.
I did not use the 'inside' washer but did use original pressure/drive washer under nut
Although I wasn't intending to actually make anything I got some short pieces
of old 2x4 pallet from outside garage. Damp and distorted but great for 'experimenting'
Didn't do any real measuring and guessed width/depth but decided to 'refine' things after making first cuts.
I never noticed knot until flipping piece over, 1/2" wide, 5/8" deep, not even a slight problem, almost zero vibration and quieter than a 'real' dado blade plus only took 5~6 mins to cut two 4"wide slots in 4x2's including 'set up' time
Step 6: Conclusions?
Worked way better than expected, very fast even though not as wide as I wanted.
Couldn't use steel washers because spindle is too short
There is a bolt at front bottom of spindle which rubbed on blade very slightly, (see pic of 'witness mark' polishing side of blade)
I'm not sure if it helped stabilise stack?
Fitting a thin washer before first blade will be next experiment, there are enough threads for it not to be a problem
Friction was minimal, I didn't notice until after doing the various cuts
Overall a good result and I will be using this for more accurate work
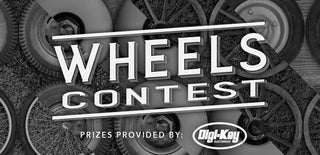
Participated in the
Wheels Contest 2017