Introduction: Circle Cutter/Pipe Fitter for Plasma Cutter
Plasma cutters are great, but you need a steady hand to make a really great cut. Failing that, a guide will give you a really clean cut every time and this adjustable circle cutting compass really comes in handy! It's cheap, easy to build and when you see the results, you'll never make another curved cut without one!
The unit clamps onto your torch head and provides a pivot point for making circular cuts of any radius you choose.
And if you need to cut circles in wood, consider my Circle Cutting Jig for your Table Saw.
Step 1: Tools and Materials
Tools
- Drill
- Drill bits
- File
- Vice
- Hammer
- Oxy/Acetylene torch or welder
- Plasma Cutter
Materials
- Steel Rod (I'm using ¼", but the size isn't critical)
- Block of aluminum (Apx. 1"x1"x⅝")
- Carriage bolt (¼"x¾")
¼" Wing nut
- 2ea. U-bolts (sized appropriately to clamp to your torch head)
Step 2: Cut the Rod
As is my custom, I'll refrain from giving exact measurements because your torch head may not be the same size as mine. It's best you build this unit to fit your equipment. In fact, now that I think of it, there's no reason you couldn't make one of these for your Oxy/Acetylene cutting torch.
Cut two pieces of rod slightly longer than your torch head and file a point on one of them. Bend the ends to right angles in a vice with a hammer. De-burr the rough spots with a file. One is the mounting rod, the other is the stylus.
The mounting rod should be as long as your torch head and clear the trigger. These factors will determine the length of each side and where to place the bend. The stylus of the radius rod should be located at the same elevation as the plasma arc. These factors will also determine the length of each side and where to place the bend.
Step 3: Make the Clamping Block
Take a block of aluminum and drill two parallel holes through it. They should be the same size as the steel rod you are using. These holes will clamp the two rods to each other and secure the stylus in place. You can start with a block the exact size of your finished unit, but I prefer to work with a larger piece and cut it down after drilling. Wood or plastic would work, but it's probably best avoided because things get hot around a plasma cutter.
After you drill the rod clamping holes, drill a hole through the block perpendicular to and in between the clamping holes. This will be where you place your locking bolt. I used a ¼" carriage bolt and pressed it into one side with the vice to secure it.
Split the block down the middle through the two clamping holes. Since the holes were the same size as the rods, now thanks to the width of the saw blade, they are smaller than the rods and the locking nut should secure the rods in place nicely.
Step 4: Weld It Up and Assemble It
Remove the sheet metal saddles from the U-bolts and weld them onto the ends of the mounting rod. Take care to align them well so that when installed, the rod is parallel to the handle of the torch head. The U-bolts will likely be too long for the application, so feel free to cut them down. You may want to put wing nuts on them too for easy removal.
Mount the rod to your torch head taking care not to over-tighten and crack the ceramic diffuser at the tip. Using the aluminum block clamp install the stylus and secure it in place.
It's ready to use!
Step 5: Using the Compass
The reason we have a stylus is because we will use a center-punch to locate the center of the radius we want to cut. If you want to round off the corner of a piece of metal, determine the radius you want, measure in that distance from the two edges and center-punch the intersection. See illustration.
What if you want to fit some pipe? This is the real reason I built this thing. Measure in ¼" from the end of your pipe and center-punch on both sides. Adjust the stylus to the radius of the pipe and cut a half circle off each side of the pipe. Afterward you'll have two ¼" tabs that can be easily cut off by hand. With practice, you'll be very happy with the fit! See the video above for my very first attempts using this great tool.
The one I made does a radius of up to 16", but you could make a longer stylus. Just remember the larger the radius, the more opportunity for flex in the stylus and that flex could translate directly into a rougher cut.
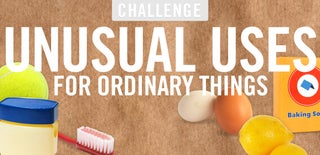
Participated in the
Unusual Uses Challenge

Participated in the
Metal Contest