Introduction: Circular Wood Resin End Table
Step 1: Material List
Materials:
Vacuum former:
3 24x48 pieces of MdF board cut into 24x24" squares
Jigsaw
Duct tape
Drill for holes
Vacuum
Tinfoil
Quartz infrared space heater
Polystyrene sheet
Table:
Live edge wood
Jigsaw
Wood round (Home Depot)
Resin (I used Art Resin)
Colorant (Liquitex or golden high flow acrylic)
Clear Packaging tape
Blow torch
Orbital sander
60,100,150,220,320 round orbital
sandpaper
Regular 320 and 420 sandpaper
Mineral spirits
Polyurethane
Cloth rags
Hairpin legs
Fixative
Wood screws
Sanding mask
Step 2: Step One: Plan
This is table 2.0. See my first table here.
After learning a lot from my first table, and having a commission for this one, I set out to not repeat my mistakes and make a table that looked more professional. While not perfect, the amount of mistakes I made with this table was probably only 15% the amount I made with the first one. Luckily almost all of the mistakes were correctable and so the final result turned out to be a level I felt comfortable to sell. I still don't have a tech shop or maker shop membership, so all of the tools and techniques I use were done with the intent to make the table as cheaply as possible. Because of this, there is a lot more rework than one would have to do if they had access to, for instance, an actual vacuum former.
I would not recommend making your own vacuum former unless you have done your reasearch and are responsible to not set your house on fire. My janky rig was fine for the purpose it served, and the time crunch; but just joining a tech shop for a month would have saved me a lot of frustration.
Step 3: Step 2: Vacuum Former
My friend wanted a circular table; and I realized that I would have to create a mold to pour the resin into. My design aimed to highlight the bark on the wood and I knew I wanted a channel of resin in between two halves of wood. I chose a diameter based on available wood rounds at Home Depot and Lowes, and knew I needed to make the top of my vaccuum former to be bigger than that.
To make a vacuum former, it's very simple. You need a box with a hole in the bottom and holes on top so you can create a vacuum that would suck the plastic over an object. See diagram below. In addition, you also need a heating element to heat up the plastic. So this is a two part project, make the vacuum cabinet, find a heat source to uniformly heat the plastic.
For the Cabinet, I bought the 24x48 pieces of MdF from home depot and had the guys there cut the board into 4 24x24" pieces. Once I got home, I cut 4 of the pieces down to 23x23". Home Depot didn't allow cuts smaller than 12 inches with their industrial machine, so I had to improvise with my jigsaw. I then went in and traced a grid on top of one and then drilled out the vertices of the grid, leaving a 2 inch border. This process took about 3 nights, as my drill ran out of power and my wrist kept cramping up. A drill press would have been perfect for this job, but janky worked in the end. I then used my orbital sander to finish off the extra ends to make the surface mostly flat. With 2 other flats, I traced a square with the edges one inch away from the edges I cut and cut out a window. I saved the 'picture frame' for the vacuum former. Finally with the fourth frame, I traced the mouth of my vacuum, and then dremelled out a large pinhole. I finally sandwiched them all together to form the vacuum cabinet. See diagram. I then took the two 24x24" boards and cut out a 22x22" window in order to make the frame for the plastic sheet. I could then clamp the sheet between the two frames for heating and forming.
The Heater Element:
I used this as reference to making the Former and Heater: https://makezine.com/2011/09/08/how-to-large-homemade-vacuum-forming-machine/
A lot of people use their ovens to heat the plastic to form their plastic pieces. Since I'm not trying to get cancer... I decided to heat my another way. Since my poly sheets were going to be big, I knew I probably needed something big to heat it up. Originally I tried to use just a heat gun, because I only really needed the parts of the plastic that were directly over the edges of the wood round to form down, but found that doing that created unnecessary stress in the plastic and the plastic even warped and broke to the point where it would be foolish to use. I knew I needed to make a homemade oven of some sort. Preferably one where I didn't have to poison myself or food I made. I found this tutorial that offered an easy relatively cheap solution that wouldn't burn down my garage. I bought four more 24x24" MDF boards and arranged them to make a 23x23" box. Looking at the video, I wish I had used thumb screw like he did so I would know the clamps on the plastic picture frame wouldn't accidentally prop up the sheet, breaking the vacuum seal. Hindsight is 20/20. After purchasing the heater element off amazon, I was in business.
The heater was strong enough to heat the plastic to be pliable, but I still had issues with the vacuum former. I used the heat gun to help soften the sides, and while not perfect (I needed a stronger vacuum). I managed to create a good enough mold for my table.
Step 4: Step 3: Preparing the Wood
I bought a second wood round from Home Depot and traced about 1/3 of the curve onto the wood making sure to capture the bark. I then traced another 1/3 for the other side. Since I only had a jigsaw, I roughly cut out the semi circles, then went in with a Dremel to more accurately shape the semi circle. I then sanded the rough edges smooth with my orbital sander.
Step 5: Step 4: Pouring the Resin
Step 6: Step 5: Varnish and Legs
The legs I used raw hairpin legs from Amazon. I first cleaned them with a degreaser, and then because I liked the look of the raw steel, sprayed them with a clear coat of krylon. When done, I then positioned them on the B-Side of the table so they wouldn’t show through the resin, and then pencil marked the holes. I tapped the holes with a screw and then went in securing the legs with the correct screw to the table.
Step 7:
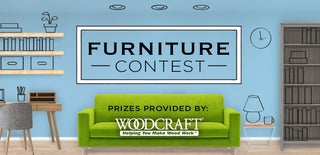
Second Prize in the
Furniture Contest 2017