Introduction: Resin Wood Coffee Table
I decided to make my own table when the cost of a table from a certain company was way too high priced and not the exact dimensions I wanted. This prompted me to look at Pinterest for cool table Ideas that I wanted to DIY. I found a whole bunch of Resin/Wood tables and decided to make my own as I was already using resin to do abstract flow painting and was pretty familiar with how to color it.
Step 1: Planning
After some sketches, I decided to try a simple design. I knew a lot of the design decisions would depend on what lumber I could find, but I knew I wanted to encase wood that had bark details and worm holes or fungus rot. Something with character. Nevertheless were my original ideas on paper:
Step 2: Gather Materials
First thing I did was look up “live edge wood slabs”. There I found websites like thelumbershack.com which gave me an idea for the type of wood that was out there to buy. I ended up going to a reclaimed wood store near where I lived and found 2 pieces I could not decide between. Each piece of wood was less than $50, so I bought both. One Walnut and one Willow. I then researched different resins and settled on Envirotex Lite. I chose it mostly because I had worked with it before on other projects and was a common epoxy used by other DIYers to cover bar tops. I also got the best price for 2 gallons off Amazon for this brand. To make the ‘mold’ for the table, I bought sheets of acrylic cut to the size I wanted, so I could just clamp them together to form a pen for the resin. Finally, I purchased some golden flow acrylics in the color I wanted. I knew I wanted a blue table so I bought 4 different blues.
Supplies:
Piece of wood, cut down to size
Pieces of Acrylic
Clamps
Masking tape
Envirotex Lyte – 2 gallons
Nitrile Gloves
Golden Fluid Acrylic
Orbital Sander
Sand Paper in grits 60, 100, 150,220, 320, 420
PolyCrylic
Wood Conditioner
Wood Stain
Hairpin Legs
Wood Screws
Rustoleum Paint and Primer Spraypaint
Degreaser
Handheld Torch with extra Can of Butane
Disposable cups and popsicle sticks
Respirator that at least blocks sanding Plexiglas. Don’t skimp save your lungs.
In case you need to fix mistakes
Acetone
Heat Gun
Chisel
Step 3: Prepping for Pouring
I wanted the table to be a cool kinda turquoise blue so I created test pucks next to samples of the two woods. Upon seeing the pucks, I decided to pick a ratio of 1 drop to 4 ounces of resin. This ended up being a benchmark as I ended up adding more color once I began the pour.
So I needed to create the pen. I peeled away the backing on the acrylic sheets and used extra-long clamps to clamp the acrylic pieces to form the 5 sided box. I then balanced the bottom on wood pieces I bought from Home Depot.
**Remember to check that the pieces are not bowed or warped before buying**
I then used my phone to level the bottom so I could create a level surface for the resin (which will spread to be level). I probably could have used two more clamps on the long side of the 40”x18” but it ended up working out okay. For the wood, I cut it lengthwise to fit the 40” length, and kept the width. This way two sides of the table would be clear resin.
Step 4: Patience
The next step was to pour.
**remember to check how the 1:1 ratio is measured for your particular resin**
Make sure to measure properly and mix thoroughly. I didn't mix properly or something on my first pour and as a result my bottom layer did not cure properly in spots and proved to be a huge pain later on. Measure 1:1 as specified. This happens to everyone and it just made my life worse. Once the resin is measured properly, color as preferred and pour. All you really need is 1-10 drops to maintain a rich and clear color. Too much paint will cause the resin not to cure properly and the table won’t be see-through. In addition, this project is very forgiving since an accidental drop or two won’t drastically affect the color and the table will still look uniform in the end. Just try to be consistent. I lined the bottom of my acrylic bottom with tape because I was paranoid about the epoxy sticking to the bottom acrylic piece (my original tests would get stuck… mostly because I mixed wrong or it was too cold in the garage). You do not need to do this. Keep the acrylic bottom clear, save yourself some time. The key to this table is mixing the epoxy well and making enough to pour the epoxy in 1/8” layers. This ensures that the epoxy can out gas, and allows you to clear out the air bubbles later with the torch. After each pour, I went in with a crème brulee blow torch about 10-15 minutes after pouring and heated up the epoxy in areas where there were trapped bubbles. It is important to keep the torch moving, as you do not want to burn the epoxy. I believe a heat gun would work as well (not a hair dryer, that would be a disaster). I then covered the table while it cured and waited 24-48 hours before pouring the next layer. This ensured that each layer properly cured. Overall, my 1 inch thick table took about 2 weeks. Patience is key.
Step 5: Releasing the Table
For my last pour of the table, I ended up pouring excess resin in all of the little wood bark crevices on the top face. For the final pour, I do not recommend coloring the resin since my doing so caused part of the top to be discolored. However, the next step was breaking the table free from its Acrylic Mold. I used a hammer and chisel to break the bottom off, as the sides came off easy. Unfortunately I was over zealous and broke the bottom acrylic piece (I wanted to reuse it), but that is okay. Had I been smart, I would have flipped the table over and done one more resin pour on the bottom to even the indents from the tape bottom, but I was foolish and thought it would sand down easy (it would have if I had known how to mix part A and B, Learn from my mistake ;_; )
Step 6: Sanding
I purchased a $30 Random Orbital Sander off of Amazon and bought grit in 60, 100, 120, 150, 220, 320, 420. The 60 grit basically takes material off, which is what I needed for the top. A planar sander would have been perfect for this job, but unfortunately Tech Shop costs a kidney to join so I had no access. Since this would be my personal table, an imperfect Orbital Sander was fine by me.
Please wear protection. I wore a respirator mask and safety glasses because I value my lungs, and was covered in dust at the end. Wear long sleeves and protective glasses so you have easy cleanup. It’s not pleasant. This step requires patience, but the end result is very satisfying. Sanding the back with the sticky spots was a pain though. I found the sticky spots when I started sanding which proved to be a mess.
Tip: feel the resin before you sand. It there is a sticky or soft spot, just tape off the sides and pour a thin layer of properly mixed resin to the - this will still retain the clarity of the resin and encase the sticky spot. If you do accidentally sand a sticky spot, you will have to do what I did and use a heat gun to heat up the smeared resin and chisel it out. Acetone can be used to remove the sticky residue until you hit a solid layer, but I found nail polish remover worked better than pure acetone. READ AND STORE THE ACETONE CORRECTLY. Please. It’s highly flammable.
I then sanded the chipped out part until it blended. Some sticky spots I noticed were able to be sanded if I used a light touch with the sander and didn’t leave the sander on it for long (sanding heats up the resin). Either way, be careful and fix the spots with another final layer of resin or layers of polyurethane finish.
Step 7: Finishing
To finish the table I cleaned off the surface of the table with a tack cloth and vacuum, and then used some wood conditioner and stain to finish the wood and attempt to cover up the colored resin stain. Once dry, I went over with Polyacrylic water based polyurethane. While the first coat looked good, subsequent coats did not. I recommend trying a spray polyurethane finish, but polycrylic can do the job. Coating with varnish made the surface of the resin really nice and revealed the crystal clearness of the resin layers.
Step 8: Legs
Based on the geometry of the table, I didn’t want to see the legs through the resin, so I had to settle for a three legged table. I liked the look of hairpin legs, and bought two normal hairpin legs and one hairpin leg with a long horizontal bar to add stability to the one leg side. I bought mine raw and cleaned them with degreaser and sprayed them with a two in one Rustoleum spray. I then placed them where I wanted and screwed them in… and it was done!
Step 9: Summary
While this table isn’t hard to make, there are a lot of little things that can go wrong. I already have a commission for my second table, and will do another Instructable on that. There are a ton of additional new skills this new one will require me to learn. It is important to double check every instruction, or you will end up like me and add 10+ hours trying to fix your mistakes. If I have access to a planar sander, I may refinish the table in the future. Overall, I will be keeping my table and am really look forward to perfecting my next one!
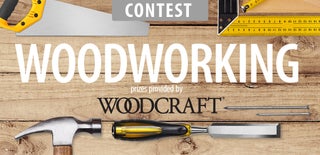
Third Prize in the
Woodworking Contest 2017