Introduction: Clay Heart Tealight Holder
This is a simple way to make a heart shape tealight holder from clay. Here I am using a clay which fires white at stoneware temperature, but other clays can be used. I use an Indian wooden print block to add the motifs but of course other wooden blocks could be used.
Step 1: What You Need
Clay - suitable for hand-building, modelling.
Roller guides about 2 cm deep.
Plastic heart shape cookie cutter. This needs to be plastic, not metal and at least as deep as you want the holder to be. Other shapes, such as circles, egg shapes can be used but avoid ones that are too elaborate.
Rolling pin with blunt style end.
Base with absorbent surface such as cork or wood. I find old cork table mats work well.
Knife.
Pallet knife.
Modelling tool.
Wooden print stamp - I use an Indian printing block but any stamp made of wood can be tried.
Step 2: Rolling Out the Clay
Place your ball of clay on your base of wood or cork. Flatten it with your hand and then roll it out evenly using the guides. It needs to be about 2cm deep.
Step 3: Making the Shape
Once you are happy that your clay is an even thickness, press your cutter into the clay. Remove the surplus from the edge with your knife.
Step 4: Making the Hole for the Tealight
Press the end of the rolling pin into the clay in the centre of the shape. Gently rotate the rolling pin until you have the shape that you want. Remember that the clay will shrink when fired so make sure that the hole is bigger than you will finally need it to be. You can smooth the edges with your fingers at this stage but don't remove the clay from the cutter shape.
Leave the piece to dry for several hours, depending on local conditions.
Step 5: Adding Decoration
When the clay has dried enough to be firm but still plastic, gently remove the piece from the base using a metal pallette knife.
At this stage you can use your block to imprint motifs into the surface. In this example I have nor added any colour but you can use oxides or coloured slips as well to highlight the imprints.
Reverse the item and leave it in a place where it can continue to dry further.
Step 6: Remove From the Cutter and Dry Out.
When the item is leather hard and starting to shrink from the cutter, gently tap it to release.
You can then tidy up any rough edges, etc using a modelling tool.
Once you have finished working on the piece leave it to dry thoroughly and evenly before firing. Because of thickness of the clay it is important to ensure it is as dry as possible.
Fire it to a temperature appropriate for the type of clay.
I use a brush on clear glaze fired to stoneware temp but other glazes can be used. I find that because this piece is quite robust it is quite easy to once fire, applying the glaze with a brush to the upper surface once it is completely dry.
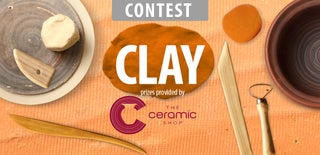
Participated in the
Clay Contest 2016