Introduction: Cold Metal Casting and Patina on Skyrim Dragon Priest Masks
I was recently comissioned to make a Morokei Dragon Priest Mask from Skyrim. I decided that since I couldn't find the perfect Morokei colour I had in mind in a regular metallic paint, I would use cold-casting techniques to create a realistic metal finish exactly how I'd envisioned. This led to many experiments in different metals, using different techniques to produce patinas and weathering effects.
Casting is often seen as an expensive hobby, but in this instructable I give tips on how to keep costs to a minimum, and offer unique advice from my own experimentation, some of it quite contrary to what I've read and seen in videos.
My previous instructable shows how I created the mask in the first place (3 years ago now!) and this instructable shows how I cast it, as well as how to apply a patina and weathering effects. Be warned that many of the chemicals used are very toxic, and great care should be taken when handling them. You will need gloves, eyewear, breathing apparatus and protective equipment when handling the patina solutions and the polyurethane casting solution, but the general rule as always is just don't do anything daft.
Step 1: Preparing the Master
I had already built my master mask with which I would make the mould, but there were some things I was unhappy with. Certain surfaces weren't quite as smooth or consistent as I would have liked so I used a mixture of bodyfiller, sandpaper and high build primer to properly prepare the surfaces as I should have 3 years ago!
If you havent got something to make a mould from yet or you want to make a dragon priest mask the same as mine, refer to the older instructable on my profile.
Filler is used to fill in deeper inconsistencies or to otherwise raise certain areas, and high build primer eliminates the smaller problems such as scratches, pinholes and slight surface roughness. It can be sanded with a fine wet and dry sandpaper to make the surface as smooth as you like.
Step 2: Mouldmaking
Ive had a tub of Scarva mouldmaking silicone for about 2 and a half years, which is well past its use by date, but it worked fine although it took a while to go off.
I made a skin mould which is the most appropriate for this mask, however if you're casting something like a small sculpture or figure then it might be better to make a block mould or a two part mould. I have little experience with these other moulds but there is a wealth of information on mouldmaking on the internet.
Quite simply mix the two part silicone thoroughly according to your product's instructions and apply it in layers taking care not to leave any thin spots (it wants to be about 1cm all over). I left it a good 12 hours to cure but check the details for your specific product.
My original mould was far too thin and was making very distorted masks, so to cheaply thicken it up I used silicone sealant and spread it on thickly just like I did with the real mouldmaking silicone. This worked perfectly, and makes me wonder if its even necessary to pay for real mouldmaking silicone. In any case, I was left with a thick, sturdy mould.
Before removing your master (demoulding) its necessary to make a rigid shell so that the silicone doesn't distort and produce bad castings. The best thing to use would be a plaster of Paris fabric wrap such as mod roc, which you simply wet with water and wrap on with your hands. I didn't have any, but I did have an over-abundance of filler so I wrapped the silicone in cling film and coated it in filler in two halves.
I also cut out two plywood arcs which was made to the shape of the mask and whose function was to enable me to bolt together the two halves. Two thin steel strips cut with tin snips also allowed me to bolt around the jaw. The images should make this easier to visualise.
After everything has cured, take the mould apart piece by piece and carefully peel the silicone from the Master. Silicone moulds eventually wear out but you can massively prolong their lifespan by being careful with them. You should now have a skin mould of your mask.
Pictured first of all is my thin mould, and the last 4 images show the making of the thicker mould.
Step 3: Casting
The method I used to cast the masks is slush casting. Essentially you pour in the mixture and slush it around to coat every surface, slowly building up thickness in several coats. Since I wanted the mask to be metal, the first coat must include the metallic powder.
I found that the best ratio for my purposes was around 3:2 powder to polyurethane. This produces a viscous mixture but not so thick that its too difficult to move around. The more metal powder the better until its unusable, but I would encourage you to experiment as I did.
It's also necessary to dye the mixture because polyurethane cures an off-white, which doesn't really look right mixed in with metal. You can buy urethane dyes but I found that enamel paints work just fine, (its important you don't use acrylic water based paints because the polyurethane mixture will react with moisture to make gas, resulting in air bubbles.) but you will need to use quite a bit if you want to significantly alter the colour. I wanted my Morokei mask to have a slight blue tinge so I mixed aluminium, polyurethane and blue enamel paint in a ratio of something like 1:20 paint:everything else. What I found is that the aluminium powder doesn't much like the dye and the mixture can only really accept so much paint, with larger amounts of paint it would bleed out as the urethane cured or alternatively it would appear as streaks. The iron powder however did not have this problem, and brass did have this problem but to a lesser degree. Polyurethane without any powder could take any amount of paint.
Another method is to brush the dry powder on the mould. This was something of a double edged sword, because while it produced a richer and more metallic finish it was of course much more thin, so did not stand up to the aggressive polishing necessary to show off the metal. If you wanted a realistic but not super well polished finish, this is the best method. This is shown in the third picture.
When mixing, make sure the two parts of the urethane are fully mixed before adding anything else. I also added the dye after the plastic was mixed and added the metal powder last, I found this order worked the best through experimenting with small amounts.
Your first layer should be quite nice and thick so that it can stand up to polishing and if you decide to put scratches in or other weathering, it can be quite deep and still be metallic. Ensure that every surface is covered, and use a brush or a gloved finger if you have to because it will be very hard to match the colour if you need to do another surface coat.
Do the next layer while the previous layer is still tacky otherwise the layers won't stick properly. You could dye it if you want deep scratches and weathering but if not it doesn't really matter and you can stick to the natural off-white colour. Make sure that every surface is getting thicker - I found that the jaw part was too thin on my first few casts because it was hard for the mixture to get to, so in future castings I focussed on building up the jaw and temple areas.
The casting environment is also very important. Any moisture can cause air bubbles so cast in a dry environment and use plastic or metal tools. If you live somewhere warm the temperature may be ideal but I had to use a space heater and shut the door to get the temperature above the required 16°C, in the middle of summer. Allowing the urethane to cure near the heater (obviously not too close) increased the strength of the cast. Of course you also need good ventilation if you're going to be in a heated room with toxic chemicals.
Step 4: Preparing Surfaces and Polishing
Most polyurethane has a demould time of 30-60 minutes, but if you get the environment perfect it can be ready in about 10 minutes (although I'd recommend leaving it just to be certain). When my masks came out of the moulds I had to cut off some imperfections around the edges with a knife and also poke the eye bits out.
Online, all sources I've seen say that you should just rub the surface with 00 steel wool, but through experimentation I found that I got the best surface finish when I used a proper bench-mounted polisher. Strangely, tripoli polishing compound (the green soap you apply to the polishing mop) produced a much brighter shine than rouge (the red stuff) although usually you would start with tripoli and move on to rouge. It worked best when I used a lot of compound on the polishing mop and had to vigorously rub it off. Brasso also improved the polish as a final finishing compound, regular "metal finishing compound" however didn't improve the polish. Unfortunately it seems a lot of what you might know about polishing is turned on its head when it comes to polishing cold cast metal.
Of course you might not want a mirror finish on a replica of an ancient mask, but I found that its better to start with a perfect mask and weather it as it really would have been weathered.
Step 5: Weathering
Any battle-scars should be applied before the patina so that it naturally settles in the crevices as it really would have, making it look much more natural and realistic. You can do them with a file, but I found they look best when you cut into it roughly with a craft knife because it makes the scratch look less uniform. Also note that when you cut through the surface you'll expose real bare metal so gouges and scratches will already look real before any sort of paintjob.
You can also use a file to rough up high/protruding areas, but it might be a good idea to do this last so that it stays a lighter colour than the main colour. Experiment, and use your artistic vision!
Step 6: Patina
The chemistry of a patina is not crystal clear to me, and a lot of the information on the internet is contradictory or difficult to understand. My understanding is as follows:
An oxidising agent such as bleach or hydrogen peroxide decomposes to produce oxygen. Corrosion happens because the metal reacts with oxygen and makes a metal oxide, therefore an oxidising agent accelerates corrosion. Salt also accelerates corrosion because it is ionic and vinegar also speeds it up. Not too sure why vinegar works because a vinegar bath can be used to remove rust, but it seemed to work.
If you're knowledgeable in chemistry perhaps you can come up with a better concoction and can get your hands on some more specialist chemicals (I couldn't even get hydrogen peroxide because apparently it's good for making bombs!). There's probably also an opportunity to create a kind of electrochemical cell using the different corroding metals you can cast and the salt water may act as a salt bridge, but my limited and fading knowledge of chemistry isn't enough to figure that one out. If you do have access to specialist chemicals the following website may be helpful for making more patina colours: http://www.sciencecompany.com/Patina-Formulas-for-Brass-Bronze-and-Copper.aspx.
The following are different methods which I tried:
Bleach, Vinegar and Salt Bath
This worked fairly well for the iron mask and made a reasonably good layer of rust overnight. It smelled appalling so I covered it over and left it outside, as far away as possible. This made both the rusty mask and the brass patina, however it did have some drawbacks. I put the brass mask in a bit longer after the first picture and it didn't go so well, its now quite streaky and uneven, so if you choose to use this method it may be wise to do it for only a short period of time. Also, this made the urethane yellow and slightly sticky. I was expecting this to wear off but after about 3 days there had been no change.
Smelling Salts
I tried enclosing my copper masks in a tub with some smelling salts, using the ammonia released to create the patina. After around 2 hours there had been no change whereas the bath had produced good results in that amount of time. I cannot speculate as to the quality of the patina that would have been produced had I waited, but it would certainly take longer.
Spray-on Bleach, Vinegar and Salt
I found that when spraying on the solution it was more easy for runs, streaks and droplets to form, making the patina a bit less natural and consistent. This was the primary way in which I corroded my copper mask, and I actually really like the results despite it being quite inconsistent.
Bleach, Vinegar and Salt Fumes
I found that the most intense patina was on the parts just outside of the solution. I'm not sure which of the ingredients are actually contributing to the patina (presumably the salt isn't adding anything to the fumes?), but putting a mask in a sealed environment with some of the solution forming vapours produced what I thought was the most natural and rich patina. It also didn't make the urethane sticky, so I think this is the best method of those I've tested.
For my iron powder mask, I found that the rust wasn't really settling in the places I wanted it to, so using some leftover iron powder I mixed it with a small amount of paint and dabbed it on with a paintbrush, then dusted more iron on top so as much bare iron was exposed as possible.
I also used some fine steel wool to rub off the patina in high spots, this compensates for the fact that the mask would have been handled extensively in the time it would have taken to naturally form such a patina. Also, using the steel wool and rubbing in a random motion made lots of tiny scratches in the surface, only noticeable up close but greatly adding to the realism.
Step 7: Paint Effects
Some patina effects weren't doable, for instance aluminium only corrodes to a thin layer of white crust and Morokei is supposed to be made out of moonstone, so I added a dirt effect by rubbing in various different dark colours with a rag, as well as using washes (thinned out paint which seeps into gaps) and dry-brushing techniques (Only having a small amount of paint on your brush therefore only getting paint on higher spots).
I also made an over-weathered, totally non-canon mask to test weathering techniques and, well, because I thought it would be cool. To do this I used the same techniques except I applied more paint, and of course I put some blood on there too. Also, in order to make the edges seem worn I used a file to expose the underlying, brighter metal under the surface.
Step 8: Lessons
I did a whole lot of experimentation in this build, and most of the things I learned are presented in the earlier steps, but below are the main lessons that I learned:
- First and foremost, do not believe what you read on the internet and experiment for yourself. I read that you should only use 00 steel wool to buff the surface and any more would ruin the finish. I decided to aggressively polish my masks using a bench grinder adapted into a polisher, and the results were phenomenal.
- It can be tricky to know when to stop when doing a patina or weathering, but having a few different examples to experiment on gave me a better grasp of what looks good and what doesn't, so I would encourage you to experiment before you make your final product.

Third Prize in the
Metal Contest
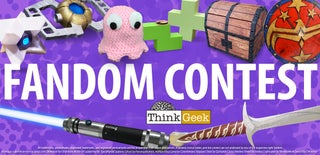
First Prize in the
Fandom Contest