Introduction: Colorful Christmas Carousel
Ive enjoyed turning objects from wood and other materials for more than 20 years and there are some types of things always get produced at certain times of the year, Dibbers spring and decorations in winter (preferably before Christmas).
Some time back I made a Carousel as a bit of messing around it had 4 ornaments on two Christmas trees and two snowmen. The carousel was a small platter suspended from a turned post using some gold thread.
The original had no color applied to it other than the natural shades of the wood itself. This year I wanted to remake my original design and hopefully improve on it and add so color as well. I could fib and say that I designed the whole thing at the start and then started turning, but no I started at the lathe made the decoration then went back taking measurements from the finished article. Using these measurements I have created a model of the decoration on Trimble SketchUp - you can see the images above.
Step 1: This Is the Finished "Colorful" Decoration
The finished toy is far better than the original with more ornaments, the inclusion of color and the replacement of the thread for chains and metal fittings It has also appeared in the woodworker magazine something which I am quite proud of.
Its also 90 to 95 % recycled the base and the Platter come from an old set of nested tables that I picked up in a charity shop a number of years ago and are still producing various bits and peace’s. The ornaments come from various bits of pen blanks that where either damaged in some way or to small for pens, however the most recycled material used in this project comes from my children’s cot, my youngest is 14 now so will not be needing it anymore – the cot provided the wood for the central post. I think the finished object looks great and am now thinking of maybe making a larger one.
Step 2: Tools Required
Tools and materials used on this project include roughing gouge, ¼ spindle gouge, a Rober Sorbey scraper, parting tool, a Simon Hope decorating wheel and a set of callipers. There are other general tools used abrasives etc., but the other important materials are a mixture of Bees wax and liquid paraffin which is used during sanding to both help keep the fine particles trapped as well as to fill the grain giving a more stable surface for finishing. Also I used Yorkshire grit which is a kind of waxy past with built in abrasive the particles of which reduce in size as it is worked resulting in a ever smoother finish.
Step 3: Start at the Bottom
The turning starts with the base and the platter, the base needs a blank approximately 11 cm across and the platter needs to be a little more than 15 cm.
To turn the base I needed to pack out the screw chuck so I drilled an 8 mm hole in a piece of plastic a little under 1 cm thick and threaded it onto the screw chuck, I put the same size hole in the center of the base blank and mounted it on the lathe. Using the roughing and spindle gouges’ I turned the wood into the round and then coved out the face using the edge of a steel rule to ensure that there was a curve in the base. This allows the carousel stand to sit level on a flat surface.
Step 4: Decorate the Bottom As Well
To finish the bottom of the base I coated it with the beeswax and liquid paraffin mix wiping off the excess (good for your hands as well) then sanded through the grits from 120 to 400. I then added a few rings with the tip of a skew chisel in case another wood turner picks the piece up to look under it.
With the bottom of the base done I turned the wood over and shaped the top side with a bit of a stretch OG curve finishing the disk with a bead around the edge.
Once happy I finished the surfaces as per its bottom and used the Yorkshire grit to get a smooth finish. The way to use the grit is to apply the paste with a clean tissue and then buff using clean tissue, changing to a clean bit as you polish/abrade the surface. When the tissue appears clean following a buff your done.
Step 5: Turn the Platter
For the platter I used a bench drill to put a small hole in the middle of the blank, then I used a 37mm fostner bit to bore a hole in the center. I worked from both sides turning the wood over before the bite had cut all the way through and used the small hole to re-align the bit before finishing the center hold. To mount platter on the lathe I changed to a set of pin jaws and used the hole as the chucking point.
To ensure safety I brought the tail stock up against the plastic I had used on the screw chuck earlier.
The underside of the platter was turned to give it a slight curve. It was then sanded using 320 and 400 grits and the beeswax mixture applied to keep the dust down. Once finished it was flipped over on the chuck and a piece of tissue used between the two to help protect the surface
This reclaimed wood from the table top is pretty tough so again I used some scrap and the tail stock to support it while I removed the bulk of the material. I shaped the scrap into a cone so that it would fit into the central hole and started to turn.
Almost finished and I had a snag the scrapper I was using caught the surface dug in and moved quite suddenly towards the scrap wood – You can see the result.
Luckily no injury and no lasting damage, there was still enough wood in the center to work with the scrap support and as this was going to be removed at the end all was good.
Step 6: Adding a Pole
The pole for the carousel came from another well used and recycled source – my kids cot my youngest is 14 so I don’t think we will need it anymore. I turned it using a skew chisel making a fairy simple shape that included an 8mm tenon to fit the home in the base.
Before parting off I removed it from the lathe and used a bench drill to put a 4mm hole at what would be its top. The pole was then returned to the lathe for sanding and finishing before being parted and finally cut off at both ends.
Step 7: Make Some Toys
There are materials other than wood. I initially thought about using some scraps of resin pen blanks and made a snowman and a tree. But they were vetoed by both my wife and daughter who said that wouldn’t go – looking at the finished product I have to agree, they did not go to waste however , I turned individual bases for them so they became decorations in their own wright.
Step 8: Coloring the Decoration
Adding color is easy – I just used a few sharpies to color in the trees and hats – Its best to turn the lathe down a slow as possible and use the side of the pen rather than the tip this helps to get an even cove and avoids lines
Initially I made six decorations, but due to objections to the resin had to make a few more in wood. One of which was a tree with a spiral line around it a little like tinsel.
Step 9: Cutting a Spiral
NOTE This bit can be a bit scary for the beginner so only do this if you are happy with your ability
To make the spiral line I first shaped and sanded the tree. I then took a Skew chisel and deliberately did something the normally happens by accident.
With the lathe running slowly and starting at the tip of the tree, I held the skew at a slight angle. This had the effect of dragging the chisel along the tree to its base leaving a nice even cut line. If your not happy doing thins then you can always draw a line on the tree, however using the chisel is quicker and gives an even spacing.
I then tool a pull saw and carefully cut along the line turning the lathe by hand and then sanded the edges of the cut using a round file wrapped in Abranett.
It was then just case of inking the line with a red sharpie and coloring the rest of the tree The snowmen needed faces and a little more decoration, this was added using a pyrography pen, I applied the details in pencil first to avoid mistakes giving them scarves and buttons.
Pyrography leaves the edges a little rough/burnt, to give the pen work sharp edges I used the tenons to hold the snowmen in the lathe and sanded with 400 grit on a slow speed.
Step 10: Adding Some Shine
All of the wooden ornaments where then stood on a length of wood with 10mm holes drilled in to stop them falling over . They where then given a couple of coats of lacquer to finish them off before being epoxied in place once the holes where drilled in the platter. The main parts of the carousel where then all polished using a buffing wheel on the lathe
Step 11: Position the Toys on the Platter
Before I could attach the ornaments I had to make a jig so that I could hold the drill bit in exactly the same place while using the indexing wheel on my lathe to set the location for the hole being drilled.
To make the jog I used a spare bit of wood – in this case it came from a Mahogany door frame. I then used calliper’s to get the diameter of my too rest support, removing the material until the require diameter was obtained. I then turned the top section to a diameter that would allow me to drill a 10 mm hole through and still have enough wood to hold the weight of the drill if I just jet it hang.
Once turned I used a hole guide to make a series of holes in the top section – the position is not important as you Adjust the position of the hole relative to the work piece when you mount it on the lathe.
To mark out the holes I started by counting the number of indexing points on my lathes pulley wheel and then divided this by the number of holes I needed to get the number of clicks to turn the platter before locking it off to make the hole. As a check I turned the wood to each point and made a small mark through the jig using a pencil.
Once happy with the location of the locations for the holes I adjusted the jibs position so that when the drill bit was pushed through the hole made in the work piece would be about half way between the inner and outer edges. With the bit in the drill and pushed through the hole so that the chuck touched the jig I moved the jig so that the tip of the bit touched the wood. Then keeping the tip touching I moved the jig closer – the distance between the chuck and the jig is now the depth of the hole that will be made in the platter.
Once the jig was secured in place all I had to do was rotate and lock the platter in place to each hole point and drill the 6 holes required.
Before finishing with the jig I lowered it so that the drill tip was closer to the center of the platter. I then used a little hand pressure to mark the platter at four points that would take the screw eyes for hanging the platter later.
Step 12: Put It All Together
To hang the carousel on the original I used small screw eyes and string, for this one the same eyes are needed, these are screwed into the wood at the four points marked around the disk. Then I attached a jump rind to the end of the chain and threaded the other end through the hole in the top of the pole. Once through I held the platter at the height I wanted above the base and guesstimate the length of the first chain and cut it. I then put another jump ring on a separate chain and held both on some long nose pliers, I then cut the second chain to the same length as the first. From there it was just a case of re threading both chains and attaching the
jump rings to the separate eyes on the platter.
To keep the carousel level I adjusted it by eye, once happy I upset the balance a enough to pull a few links though the hole in the pole. I then applied some epoxy resin and pulled the platter the other way and did the same on the other side. Once re-levelled the glue was left to harden.
Step 13: What to Do With the Extras
Once the Carousel was finished I still had the spare ornaments that where rejected by my wife and daughter, so I turned each a base in boxwood to give some additional decorations to go with the carousel.
Hope you like this project I think its great and had a lot of fun making it.
If you enjoyed this guide and found it useful please consider voting for it in the competitions it has been entered for.
Thanks for reading
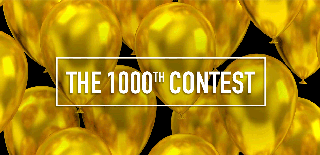
Participated in the
1000th Contest