Introduction: Something for Easter - a Shadow Turned Project - Updated
This instructables aim is to show how to use shadows to help turn consistent shapes to create great decorative objects. To do this you will need a shadow board. This next section goes through what this is and then how to build it. There are also templates available for use with it or any other shadow board design. At the end There is an example of what you can create using this technique, in this case a couple of Easter egg decorations.
I hope you enjoy this guide, if so please consider voting for it in the upcoming contest. Thanks for reading.
If for any reason the links in this guide fail they are all available on my web page at www.handycrafted.jimdo.com
UPDATE
Since writing this guide I have used the shadow board technique to turn a much larger egg, but this time I have hollowed it out to make a box, So now its a true Easter egg, and I intend giving it to my wife on Easter filled with her favourite - chocolate mini eggs see the images - see how to make this egg in my new instructable at the following link https://www.instructables.com/An-Easter-Egg-for-My... and thanks again for reading
Step 1: Shadow Board Idea
What is one
A shadow board is simply a sheet of material placed behind the blank being turned. The material has a shape on it and the wood turner shapes the wood to the design based on the shadow cast from a light in front of the blank. In this case the shadow board is held at 45 degrees to the bed of the lathe. A shape can then be drawn directly onto the board or a sheet of paper clipped to it to make it more reusable.
To use them you draw your shape on the board or paper and then shine a light centrally on the front side of the wood being turned. This makes the shadow on the paper. You then turn the wood, removing the material while observing the shadow on the paper., stopping when the shadow lines up with the design on the shadow board. You can find the sketchup file for this design at:
There are a few more additions to be made, but the majority is there and usable. Sketchup Page. The Shadow board consists of the board itself and two supports, these are clamped onto the lathe using nut and bolt shown in the following images.
You can see in the images that two feet are required and that a cut-out is needed in the board itself - this is to allow for the banjo of the lathe.
Templates
To help use the shadow board (once you have made one) I have created a few templates for shapes, (Oval, Sphere and and Egg shape template) it will be the egg template that's used as part of this guide. If you what to download these they are on my web page (www.handycrafted.jimdo.com)
Construction of the shadow board is detailed in the next section
Step 2: The Shadow Board Supports
The shadow board is an aid to the wood turner, both experienced and beginner and helps to get repeatably accurate results during spindle turning. There are many ways to make a board and it can be as simple as laying a drawing on the bed of the lathe and shining a light down from the top. This is my design and consists of scraps of wood with 45 degree slots cut into them and held onto the lathe using bolts with plates(clamps) under the rails/bed of the lathe
You could just use clamps to hold the upright parts in place, but these would get in the way of you working the wood, which could also result in a hazard should the clamps slip off while working. My design is more suited to general use and can be adapted (with minor changes) to fit just about any lathe.
Materials
Start by gathering the tools and materials required as follows:
- Bolts (8 mm) with nuts and washers
- 12 mm Plywood - off cuts will do
- Wood screws
- 3 mm hardboard
- Band saw or hand saw - a table saw would be really useful
- Square and tape measure
Start by cutting respectable from the 12 mm plywood. The size of these is dependent upon your lath design, but they must be large enough to sit on the bed of the lathe. Leaving sufficient length so they can be moved backwards and forwards without falling off. The must also be taller than the height of the banjo, this is to allow for the 45 degree cut that is needed to hold the shadow board itself.
You will need 4 of these boards, draw a line top to bottom at the middle of each and use a saw to cut a groove along the line. The easiest way to do this is by making a couple of passes with a table saw, but it can also be done using a hand saw, Chisel etc. The grooves need to be large enough to take the 8 mm bolts when two of the boards are sandwiched together.
To sandwich the boards you will only need a screw at each corner, no more. this is important as you will be cutting into these sandwiches, so ensure the screws are as close to the corners as possible while still leaving enough wood to tidy it up at the end.
I then laid out the cutting lines on the face of each sandwich as follows
- Two vertical lines, one on either side of the bolt hole. Initially these where close to the bolt, only allowing space for the nut. But I found that this was difficult to then attach the nut and the washer which was required, so I made another line further back from the bolt.
- Horizontal line across the two bolt lines at approximately 4 cm from the bottom of the face that would sit on the lathe bed.
- Two sets of parallel lines at 45 degrees to the bottom of the sandwich, these where approximately 3 mm apart and terminated 3 cm above the bottom of the sandwich.
The reason for the two sets of lines at 45 degrees was to allow for turning larger blanks on the lathe. The finished clamp would also slide backwards and forwards which too was to allow for blank sizes. The lines where then cut out using a band-saw.
Step 3: The Clamps
Holding the sandwich onto the lathe requires a sliding block the dimensions of which will depend on you lathe. I cut two pieces of plywood. The first was square and just fit between the two faces of the lathe bed. The second was cut to a rectangular shape the width the same as the square part. Its length was just large enough so that it fit under the lath bed without being able to move backwards or forwards, but could move along the length of the lathe. I held this part in place and put the square on top and then carefully removed both parts (still holding them together). Once off the lathe I secured the two parts using four wood screws.
The next step was to make a slot in this part (foot) that would allow the Sandwich section to slide backwards and forwards. This was done by making a line across the middle of the square piece and using a punch to mark drill pints along the line.
I then drilled along the line, using the punch marks to keep the holes in line. Once the holes where made I used the drill press as a mill, moving the wood to smooth out the slot. I then cut the bolt so that the screw thread would not interfere with the shadow board when used in the front slot and set both parts up on the lathe bed so that the bolt was close to the rear of the lathe bed. I then marked the position of the rear bed rail on the sandwich section. The slid it forward and marked the front rail location. I then made 1 cm marks between the two points.
At the time of making I was also cutting some replacement draw bottoms, so for simplicity I made the shadow board the same size. This will probably need cutting down slightly, but that is a simple job for later.
Once I had this part I marked out sections to be removed from two of the sides, this allows the banjo to move freely under the board when in use. The removal of material on two sides allows for the rotation of the board for different lengths of blank being turned. Initial set up needs both sandwich sections in place and the board slotted into them. Set the sandwich block with the graduations on so as the bolt is at the rear of the lathe. Then adjust the other sandwich block until the line visible under the board is horizontal with the lathe bed. Remove the board and mark the second sandwich block at the rear of the lathe bed. Then use a rule and mark the same number of graduations as per the marks on the other block and in the same direction. These graduations allow you to position the shadow board more accurately and later (when I add to this article) will help you allow for the difference in size of the shadow produced to the dimension of the turned item.
Step 4: The Shadow Board
The board itself is just a piece of hardboard (this one came from the back of a kitchen cupboard. You can see from the images that I cut it over sized to a piece of A4 paper and then removed material along two adjacent sides, this will allow for turning the board to portrait or landscape orientations while still letting the banjo move underneath it when in place. Its size along with all other dimensions for the shadow board is up to you - it depends only of the capacity of your lathe.
Step 5: Setting Up and Using the Shadow Board
The shadow board technique is very simple to follow, You start off by turning a blank. The size is not important. For this egg I rounded the wood between centres and then added a spigot at one end to mount it in my chuck. Then I attached the shadow board "jig" to the lathe and inserted the actual board.
With the jig attached I put the blank into the chuck and selected the template to be used (the Egg). This was clipped to the shadow board using an office file clip. I then roughly turned the blank to shape.
Getting an initial shape on the wood allowed for easily centring the template behind the blank relative to where I was standing and importantly to the light that was casting the shadow. Note there are more accurate ways to centre the template, this one was just quicker.
To centre the template I made a mark on the blank and rotated it so to be vertically above the paper (NOT the lathe bed ) . It was then a case of adjusting the paper so that it square to the top of the shadow board and moving it up and down until the horizontal line on the paper coincided with the mark on the wood.
The light casting the shadow must be a single source, I used a cheap LED lamp I got from IKEA that I have mounted on the wall behind the lathe, and extends out and over the lathe. At present its quite close to the lathe and could do with moving higher so as to cast a smaller shadow on the paper.
The distance the light is away from the wood has an effect on the size of the turned piece relative to the size of the shadow on the template. i.e. the further away you can get the light the tighter the shadow will be to the wood and the more closely the finished egg will to the size of the template ring you turn to. That might sound a little confusing, but will become clear with the first time you try this technique. There is also a formula for calculating distance and template sizes which I will add to this page when I can find it.
Step 6: Adding a Design and a Stand
The finished egg was sanded and polished on the lathe prior to parting it off, with the parted end finished with a little sanding and buffing off the lathe.
To decorate the egg I have something called an Egg-Bot. A small C.N.C. drawing machine which can be used to put images into small round oval and egg shaped objects.
The software used for the images is called InkScape and is free to download it also has extensions for controlling the Egg-bot (also free download). Using this you can take virtually any image and apply it to the object in the machine.
The one I used was made up from repeating flowers and vines. It was applied using a pencil, however I found that the polished surface was too smooth for this so I had to sand the egg with 230 grit Abranet, but this still would not work - I found that the pencil was too light to draw on the wood, so I adapted the Eggbot - adding an elastic band between the drawing arm and the securing screw - this held the pencil onto the egg while it was rotating and worked just great. I also had to ensure that the pencil had a sharp point to it, I didn't have a sharpener so I use a little sand paper (Abranet).
Once the image was there I used Pyrography to burn it in place and then coloured it using iridescent paints
Adding a base
The eggs I made were great and very decorative (the second one I did not colour as the grain was fantastic by itself). But the both needed something to sit on to show then off. So I turned a couple of bases using some scrap wood and painted them, giving both a slightly distressed look.
To do this I first painted them with black acrylic paint and when dry applied some of the iridescent paint - Blue for one green for the other. just before this layer dried I buffed them with a tissue - this removed some of the paint leaving a patchy look. The green one I allowed to dry fully and then polished it up, for the blue one and added some gold guilt creme and buffed it - the guilt left a patchy look making it look slight aged this was left to set a little more and then buffed to a shiny / slightly mat finish.
That's it really if you liked this please consider voting for it in the contest, and thanks for reading to the end
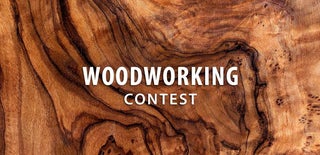
Participated in the
Woodworking Contest