Introduction: Compressed Air Bulkhead Fitting Outside Wall of House.
Ever since I purchased my house I have been wishing for a compressed air line on the outside of the house. I do all my own automotive repairs, and live in the rust belt, so an impact wrench is a must. My house is 125 years old, and in need of fixing up, as every old home is. I am a hobby woodworker, so pneumatic nailer and stapler use is a common weekend activity. I use a compressed air a lot. So having an air outlet located in the place where you use it most often is a wonderful thing to have. Especially when it would mean not uncoiling and running hoses on ridiculous paths through your house every time you would like to do any project.
This project is all about convenience. My compressor lives in the basement, near my electrical panel, which makes sense as it is a 220 volt compressor, and its big and heavy and hard to move. Dedicated 220 volt outlets are expensive. Air hoses are cheap. So the compressor lives its life in one place.
So the best plan would be to just mount some kind of airline permanently on the outside of my house, with quick connector fitting, to the place where most projects happen. Just power up the compressor in the basement, hook up your airline outside and you are off and working. Sounds great, yes? But his brings up a few issues of its own.
1) Any work you do on a house you own should be well crafted, and designed to last a while and not rust or make a mess.
2) It should be designed with weather in mind, and should not compromise the envelope of your house.
3) If is mounted in a place where you can see it, it should look nice, and not like a large kluged together eyesore
I spent a while trying to figure this project out to make it look good. Every time I would stop at gas station that had a repair garage I would look and see if they had an airline outside and how it was installed. Most of them were horribly done. So the goal was to make this project look nice and get the number of pieces down to a bare minimum. Standard design principle: Less Parts = Better Design. And Make it weather tight. And make it look nice. And get it approved by my wife. This last part is important. This is what I came up with.
This project is all about convenience. My compressor lives in the basement, near my electrical panel, which makes sense as it is a 220 volt compressor, and its big and heavy and hard to move. Dedicated 220 volt outlets are expensive. Air hoses are cheap. So the compressor lives its life in one place.
So the best plan would be to just mount some kind of airline permanently on the outside of my house, with quick connector fitting, to the place where most projects happen. Just power up the compressor in the basement, hook up your airline outside and you are off and working. Sounds great, yes? But his brings up a few issues of its own.
1) Any work you do on a house you own should be well crafted, and designed to last a while and not rust or make a mess.
2) It should be designed with weather in mind, and should not compromise the envelope of your house.
3) If is mounted in a place where you can see it, it should look nice, and not like a large kluged together eyesore
I spent a while trying to figure this project out to make it look good. Every time I would stop at gas station that had a repair garage I would look and see if they had an airline outside and how it was installed. Most of them were horribly done. So the goal was to make this project look nice and get the number of pieces down to a bare minimum. Standard design principle: Less Parts = Better Design. And Make it weather tight. And make it look nice. And get it approved by my wife. This last part is important. This is what I came up with.
Step 1: Why This Needed to Be Done.
Most of the work here gets carried out in the driveway, which is only 20 or so feet away from the compressors location. Sounds simple enough. Right? Its 20 feet A-B.
Not in least, because of the design of the house, it requires running an air hose on the following path. From the compressor, across the furnace room, out the door, through the workshop, past the basement stairs, across the laundry room out through the door at the bottom of the bulkhead (hatchway to some) up the stairs through the door at the top of the bulkhead around the garden, back down the side of the house, and to the driveway. Total length = 100+ feet. Its a pain, it takes time, you have to leave all the doors open, there are lots of places to trip over the hose. And when you are done, you get to pack it all back up again. Its just a bad way if doing things. So bad its almost comical, I sketched up a basic not to scale layout to explain it, Yes its that crazy of a route. Something must be done.
Not in least, because of the design of the house, it requires running an air hose on the following path. From the compressor, across the furnace room, out the door, through the workshop, past the basement stairs, across the laundry room out through the door at the bottom of the bulkhead (hatchway to some) up the stairs through the door at the top of the bulkhead around the garden, back down the side of the house, and to the driveway. Total length = 100+ feet. Its a pain, it takes time, you have to leave all the doors open, there are lots of places to trip over the hose. And when you are done, you get to pack it all back up again. Its just a bad way if doing things. So bad its almost comical, I sketched up a basic not to scale layout to explain it, Yes its that crazy of a route. Something must be done.
Step 2: Gather the Parts.
So here is the list of parts that I came up with:
1 - 1/2" NPT pipe flange
1 - 1/2" NPT Lapp Brand Waterproof Skintop Cable Strain Relief.
1 - 1/4" NPT pipe nipple long enough to get through your wall, plus a few inches, in my case 18"
1 - 1/4" NPT street elbow.
1 - 1/4" Female air line quick connect fitting.
1 - 1/4" Male air line quick connect fitting. (not pictured here)
1 - Teflon thread sealant tape (not pictured here)
1 - Mounting Screws for your pipe flange (sizes vary)
I tried to keep the parts count as low as possible to keep with the clean look. The pipe flange, nipple, and fittings I got from a company online www.pexsupply.com as no local store carried much in the way of black iron pipe in the 1/4" size. The air fittings are from the local home improvement store. The cable strain relief something I had, but can be purchased from an online supplier like Allied Electronics, or you may find something like it at a local electrical supply house. Note of caution: Many of the 1/2" strain releifs I tried did not have a large enough opening for the 1/4" pipe to pass through. You can easily step up to a 3/4" NPT strain relief and pipe flange to make your life easier. The 1/2 version I found just barely fit the 1/4" pipe I was using. I could have gone to a 3/4" pipe flange and strain relief, but smaller flange looked better where it was being mounted.
1 - 1/2" NPT pipe flange
1 - 1/2" NPT Lapp Brand Waterproof Skintop Cable Strain Relief.
1 - 1/4" NPT pipe nipple long enough to get through your wall, plus a few inches, in my case 18"
1 - 1/4" NPT street elbow.
1 - 1/4" Female air line quick connect fitting.
1 - 1/4" Male air line quick connect fitting. (not pictured here)
1 - Teflon thread sealant tape (not pictured here)
1 - Mounting Screws for your pipe flange (sizes vary)
I tried to keep the parts count as low as possible to keep with the clean look. The pipe flange, nipple, and fittings I got from a company online www.pexsupply.com as no local store carried much in the way of black iron pipe in the 1/4" size. The air fittings are from the local home improvement store. The cable strain relief something I had, but can be purchased from an online supplier like Allied Electronics, or you may find something like it at a local electrical supply house. Note of caution: Many of the 1/2" strain releifs I tried did not have a large enough opening for the 1/4" pipe to pass through. You can easily step up to a 3/4" NPT strain relief and pipe flange to make your life easier. The 1/2 version I found just barely fit the 1/4" pipe I was using. I could have gone to a 3/4" pipe flange and strain relief, but smaller flange looked better where it was being mounted.
Step 3: Prep and Paint.
This is going on the outside of your house and will be exposed to weather, steel rusts and makes a mess. So proper painting technique will go a long way. I will not go into detail, but sand, degrease, prime and paint are the order of the day.
Step 4: Begin Assenbly.
To Begin assembly the strain relief gets screwed into the pipe flange. And then the pipe nipple, elbow, and the female quick connect are all assembled together, using Teflon thread sealant tape. Then the pipe nipple and slid through the strain relief and tightened down. To make the assembly shown in the second picture.
Step 5: Paint Again.
Yes, now its time to paint this thing again. Rust is evil and must be prevented. I used a standard grey metal spray can primer, and one of the newer universal (metal, plastic, wood compatible) spray paints on the whole thing once it was assembled.
Step 6: Drill Through the Side of Your House.
Sorry no picures here, I was excited and for forgot to take any. Select your location and make sure it is free of obstructions, other pipes, gas lines, wiring, etc, etc, etc, and drill your hole to get the pipe from the inside to outside.
Step 7: Finishing Up.
Time to finish up this project. Slide the whole assembly through the hole you drilled in the last step add some waterproof caulking behind the flange and secure it to the house with the screws. You will notice in this picture that I had to make a small wooden block to mount the pipe flange to because of the angle of the clapboard siding. The block was stained to match the wood siding of the house, and the pipe flange and screws were touched up with more spray paint. On the inside of the house, add the male quick connect fitting to the other end of the pipe and you are done with the installation.
Step 8: Finished!
Now you are done, no more 100 foot air hoses strung hither and dither, no more tripping, no more coiling. To use compressed air outside just take a short hose and connect from the air compressor to the inside of the bulkhead fitting, and hook your airline up outside, and get to work. And getting to work, that is the fun part.
If you enjoyed this instructable, please take a moment to give me a rating, if you have any questions please feel free to ask in the comments section. Thank you.
If you enjoyed this instructable, please take a moment to give me a rating, if you have any questions please feel free to ask in the comments section. Thank you.
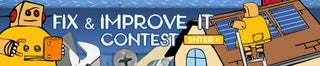
Participated in the
Fix & Improve It Contest
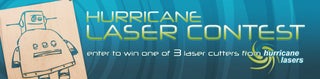
Participated in the
Hurricane Lasers Contest